1. 前言
经国土资源部矿产资源储量评审中心专家确认,位于四川东北部的普光气田成为四川盆地已发现的最大天然气田,跻身我国特大天然气田之列。普光气田位于四川省宣汉县,天然气中硫化氢平均含量为15.16%,二氧化碳含量为8.64%[1] 。集气站采用全湿气加热保温混输的生产工艺,井口天然气在井场经加热、节流、分离、计量后进入外输系统。站场集输设备中,分离器是主要设备之一,包含有分酸分离器、计量分离器、生产分离器、火炬分液灌等。
井站分离器的设置是为了有效分离天然气中的杂质,保证计量装置的计量精度。另外,通过分离器将天然气中的气相、液相分开以便于对气井生产的物流分别计量。
集气站的流程如图1所示[2] 。我们所计算的分离器,在流程属于一级分离器,设备属于高压设备,并且从原来工艺中的卧式分离器改为立式分离器。为了了解设备在正常运行工况下内部的压力、速度、成份分布等情况,我们采用流体分析软件,对高压分离器内部的流场进行了分析。
现有CFD软件包比较多,如phoneics、CFX、fluent、start-cd等,而fluent是目前国际上比较流行的商用CFD软件包,在美国的市场占有率为60%。它具有丰富的物理模型、先进的数值方法以及强大的前后处理功能,在航空航天、汽车设计、石油天然气、涡轮机设计等方面都有着广泛的应用,其在石油天然气工业上的应用包括燃烧、井下分析、喷射控制、环境分析、油气消散/聚积、多相流、管道流动等。Fluent的软件设计基于CFD软件群的思想,从用户需求角度出发,针对各种复杂流动的物理现象,Fluent软件采用不同的离散格式和数值方法,以期在特定的领域内使计算速度、稳定性和精度等方面达到最佳组合,从而高效率地解决各个的复杂流动计算问题。本文计算分析分离器内部的流场采用的是Fluent软件。
2. 计算模型
2.1. 几何模型
高压分离器的模型见图2。模型的尺寸完全按照所提供的图纸进行三维建模。模型建模是在CATIA软件内进行的。先根据分离器图纸建立设备的模型,然后采用软件中的逻辑算法,用外包络模型减去设备模型,最终获得分离器内部用于流体计算的空间模型。具体的方法可以参见参考文献[3] 。在流体计算分析中,分离器内部,只考虑了伞形罩帽的零件模型。但是,容器上接管法兰在流体计算中未予考虑,因

Figure 1. Flow diagram of gas gathering station
图1. 集气站场流程示意图

Figure 2. Pressure separator model for fluid calculation
图2. 用于流体计算的高压分离器模型
为这些法兰均是测量用的法兰,其内部的流体是不流动的,或者说流动非常小,可以不考虑流体在这些接管内的速度变化对压力容器内部流场的影响。在几何模型中,只包含了分离器的主体部分,入口、出口、内部的伞形罩帽。因为伞形罩帽对流场有比较大的影响,起到使出口压力分布均匀的作用。
2.2. 流体计算的边界条件
入口边界条件设置:质量入口,流量3.2 kg/s,温度313 K,组分如表1所示。实际计算中,只考虑CO2、H2S、CH4三种成分。
出口边界条件设置:压力出口,压力为10 MPa。
计算时根据介质组分和含量,把混合气体作为一种单一性质的介质,根据理想气体混合律计算出混合物的物性参数。
2.3. 模型设置
方程:流动方程、能量方程、标准k-ε湍流模型、标准壁面函数。
算法:SIMPLE。
空间离散:QUICK/二阶迎风。
时间离散:二阶隐式。
2.4. 有限元网格
网格整体平均尺寸:0.04 m,最大网格尺寸:0.07 m,网格数量:1,341,389。
对于结构进口、出口、伞形罩帽等位置,进行了网格加密处理。所划分的有限元网格如图3所示。
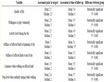
Table 1. Fluid gas components in the calculation
表1. 流体计算中的气体组分

Figure 3. Finite element mesh model. (a) Longitudinal sectional; (b) Outlet; (c) Inlet
图3. 有限元网格模型。(a) 纵截面;(b) 出口;(c) 入口
3. 分析结果
3.1. 速度分布
图4是分离器内部流速的分布结果,从图中可以看到,分离器内部流速分布是很均匀的,除出口位置和入口位置速度变化比较大,容器内的流速大部分都在3.59 m/s,比较低,但是在出口位置速度很高,出口速度最大为71.7 m/s,入口速度约为61 m/s。
(a)
(b)
(c)
Figure 4. Internal velocity distribution calculations result of splitter. (a) Velocity distribution at outlet; (b) Velocity distribution at inlet; (c) Overall velocity distribution within the separator
图4. 分离器内部流速分布计算结果。(a) 出口速度分布;(b) 入口速度分布;(c) 分离器内部整体流速分布
3.2. 压力分布
图5是分离器内部压力的分布计算结果,从图中可以看到,分离器内部压力分布也是很均匀的,压力为10.3 MPa。在出口位置,由于流速增加,导致压力的下降,出口位置压力为10 MPa。入口位置的压力
(a)
(b)
(c)
Figure 5. Internal pressure distributed results within separator. (a) Outlet pressure; (b) Inlet pressure; (c) Overall pressure distribution within the separator
图5. 分离器内部压力的分布计算结果。(a) 出口压力;(b) 进口压力;(c) 分离器内部整体压力分布
和分离器内部压力相同。最特殊的位置是正对着入口位置的压力容器底部,由于进入分离器的天然气初速度方向是向下的,在向下运动到分离器边界上,才会折返向上运动,在折返点,天然气对容器的冲击很大,此处是压力最高的位置,压力大于10.3 MPa。从计算结果看,分离器入口和出口之间的压力差并不大。
4. 结论与讨论
通过对分离器内部的流场进行分析,发现在容器内部伞型罩帽上侧和下侧之间的速度场、压力场都没有变化,换句话说,伞型罩帽在分离器内部不会对流场产生影响。若是为了调整分离器内部的流场,才增加的伞型罩帽,则证明结构没有起到作用。若是为了过滤天然气中的杂质,则伞型罩帽可以保留,若是为了调节分离器内部的流场而设置的该设备,则设备完全可以取消。
从分离器内部的压力场计算看,在分离器下部,与进口管正对的位置,压力比较高。从压力容器设计的角度看,在容器内部该位置,可以把堆焊层的厚度增大,以提高容器的抗压能力。
同时,在分离器设计中,下部有开孔,是为了把分离器内部分离的天然气中的杂质放出。但是从流体分析看,目前的设计结构并不利于杂质沉淀到分离器底部。通过入口进入分离器的流体,会沿分离器底部的内壁流动,然后改变方向向上流动。这样的流动会把分离器底部沉淀的杂质冲刷到上部区域。从利于杂质沉淀的角度看,在分离器内部天然气入口位置,应该增加一个遮挡板,使天然气能够在遮挡板位置流动方向改变为向上。在遮挡板下部,天然气相对静止,方便杂质沉淀下来。