1. 引言
聚丙烯(PP)因其优良的综合力学性能、化学稳定性、耐热性以及较好的成型加工性能和相对低廉的价格而在日常生产生活中扮演着及其重要的角色。但由于PP在低温脆性、抗冲击性和耐候性差等方面的缺陷,在许多领域上的使用受到限制[1] ,需要对PP进行增韧改性,通常的方法[2] [3] 包括:动态硫化、增大体系中β-PP晶含量、刚性粒子增韧等。
本文采用动态硫化条件下橡塑原位复合及添加无机刚性粒子二氧化硅对PP进行改性,并选择过氧化二异丙苯(DCP)和硫磺复合硫化体系。三元乙丙橡胶(EPDM)颗粒表面活性较高,且与PP相界面粘接性良好,同时在PP基体冷却降温过程可充当成核剂,促进PP异相成核,形成尺寸较小并且均匀的晶体,提高了PP材料的冲击性能[4] [5] 。本文主要探讨了不同EPDM含量对于PP/EPDM共混体系固化行为、结晶动力学的影响,对于PP/EPDM共混体系的配方设计与工艺条件优化具有现实意义。
2. 实验部分
2.1. 实验原料
聚丙烯(PP),T30S,辽宁华锦通达化工股份有限公司;三元乙丙橡胶(EPDM),4785HM,美国DOW Chemical公司;二氧化硅(SiO2),CYDZ 255-2006,国药集团化学试剂有限公司;硫磺,HG 3384-84,天津市红岩化学试剂厂;过氧化二异丙苯(DCP),烟台恒诺化工有限责任公司;抗氧剂1010(AT-10),东莞市圣诺塑胶材料有限公司;氧化锌,HG 3623-99,天津市红岩化学试剂厂;KH-570、CG-A174:上海市名祺胶粘材料有限公司。
2.2. 实验设备
平板硫化机,QLB-350,上海双翼橡胶机械有限公司;
摆锤冲击试验机,ZCJ-300A,深圳市新三思材料检测有限公司;
缺口制样机,QYJ-1251,深圳市新三思材料检测有限公司;
哈克转矩流变仪,Polylab OS,赛默飞世尔公司;
开放式炼胶机,XK-160,广东湛江机械厂;
邵氏硬度计,HLX-AC,扬州中科计量仪器有限公司;
导热系数测定仪,YBF-3,杭州大华仪器制造有限公司;
橡胶加工分析仪,RPA-8000,台湾高铁科技股份有限公司;
微电脑加热板,YOUYUE-946A,深圳市优越精工有限公司;
万能制样机,TWZY-24,吉林省泰和试验机有限公司。
2.3. 制样与性能测试
1) 最佳硫化温度测定:先将PP、EPDM以及各种助剂在开放式炼胶机上进行熔融混炼,温度167℃,制备未硫化胶料,然后取适量混合胶在橡胶加工分析仪进行硫化温度扫描,测试最佳硫化温度。
2) 胶料制备及动态硫化:将PP、EPDM以及各种助剂在哈克转矩流变仪进行混炼,制得胶料(主机转速60 r/min,温度180℃,操作时间7 min),然后将胶料在开放式炼胶机上进行二次混炼(温度170℃,辊距2 mm,操作时间15 min),最后在平板硫化机上进行模压成型(温度180℃,模压15 min),制成直径为10 cm的圆片试样。
3) 硬度测量:依据GB-T 2411-2008,在同一圆形试样5处不同位置采用邵氏硬度计分别测量硬度,并取平均值。
4) 冲击强度测试:利用万能制样机从圆形试样上切取宽度10 mm、厚度2 mm、长度8 cm的标准样条,经缺口制样机在宽度方向铣制2 mm缺口,采用摆锤冲击试验机进行测试,每个配方测试5~7根样条,取其平均值。
5) 导热性能测试:热导率的测试按照ASTM E1530标准进行,采用“稳态法”原理对不同材料的导热系数进行测定。
6) 材料固化行为测试:先在程序控温热台上加热粒料至210℃,保温15分钟,然后快速将样品转移至冷却水槽中(水温20℃),采用LU-R2100型数显温度测试仪(配铜–康铜T型热电偶)测量,并记录样品整个冷却过程的温度变化,绘制降温曲线。
3. 结果与讨论
3.1. 硫化温度测定
图1是通过橡胶加工分析仪(RPA)测得的EPDM橡胶温度扫描曲线,可以看出,在温度较低时胶料处于玻璃态,模量较高,随着温度的升高(直至接近粘流温度时),胶料的模量急剧降低。当温度继续升高

Figure 1. Temperature scan curve of EPDM via RPA
图1. EPDM橡胶的温度扫描曲线(RPA)
到硫化温度时,胶料进入硫化阶段,内部开始交联,体系模量有所增加,当硫化过程彻底结束后,聚合物出现热老化,导致模量又有下降。由图1不难看出,当温度达到170℃时,体系开始硫化,200℃左右硫化过程基本完成,综合考虑本研究选取180℃作为EPDM的硫化温度。
3.2. PP/EPDM动态硫化共混改性后导热及力学性能分析
20世纪70年代,Bucknall首先提出了聚合物的银纹–剪切带理论,该理论[6] 认为:橡胶颗粒在增韧体系中作为应力集中点可以诱发大量银纹,银纹尖端的应力场又可继续诱发大量的剪切带,这些银纹和剪切带在外力作用下可以耗散部分能量,从而有利于共混物冲击强度的提高。表1为不同共混物的导热系数、冲击强度和邵氏硬度值,不难看出,随着EPDM含量的增加,共混体系的冲击强度逐渐提高。通常情况下,塑料的硬度高于橡胶,因此随着橡塑比的增高,共混物的邵氏硬度有所下降。从导热系数来看,当EPDM含量达到40%时,导热系数达到最大值,这可能是当EPDM含量很少时,由于橡胶的导热性能比塑料差,共混物整体导热性能降低;而当橡胶含量为40%时,EPDM作为分散相粒子能较好地分布在PP基体中,形成双连续相结构,从而有利于导热通路的形成。
3.3. 填料对聚丙烯固化行为的影响
随着橡胶相含量的提高,冷却速率越来越高。这可能是与橡胶加入以后,可部分填充PP分子链间的空穴有关[7] 。图2(a)还可以看出,在曲线初始阶段,不同配比的共混物温度值相互重合,大约在降温至
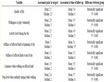
Table 1. Thermal conductivities, impact strength and shore hardness of various blends
表1. 不同共混物的导热系数、冲击强度和邵氏硬度

Figure 2. (a) Temperature decay curves; (b) q-ln t curves of various blends
图2. (a) 不同共混物的降温曲线;(b) 不同共混物的q-ln t曲线
110℃时曲线发生分离,而PP的最佳结晶温度区间位于110℃~120℃,因此固化曲线分离就与EPDM加入对PP结晶动力学的影响有关。EPDM加入之后,导致PP结晶度降低和结晶潜热释放量下降,因此共混组分较纯PP的冷却速率更高。图2(b)是对图2(a)做无因次处理的结果,无因次温度q = (T − Tc)/(T0 − Tc),其中Tc为冷却介质温度,T0为起始聚合物熔体温度,由图2(b)也可以看出,随着EPDM含量增加,共混物冷却速率显著提高。
3.4. 填料对聚丙烯结晶动力学的影响
根据文献报道[8] ,通过2d-Tait方程和聚乳酸的P-V-T关系,可以获得不同复合材料的结晶度数据,其计算公式如下:

其中,ρc = 0.936 g/cm3,ρa = 0.852g/cm3 (ρc和ρa分别为聚丙烯晶区和非晶区的密度)。
由图3可以计算不同EPDM含量共混复合材料半晶时间(t1/2),如表2所示。在PP/EPDM共混物中,一方面细小的EPDM分散相可以起到成核剂的作用,有助于PP的结晶过程;另一方面,EPDM的分子链含支链较多,在空间上无规排列,易发生缠结,导致PP分子链运动及其在晶格上的正常排入,从而降低了PP结晶能力。另一种理论认为[9] ,晶核的生长结晶需要跨越一定的能垒,能垒的大小与聚合物界面自由能存在很大的联系,而共混物内部两相良好的相容性可以在一定程度上降低界面自由能,进而影响结晶过程。由表2不难看出,随着EPDM的加入,PP的半晶时间缩短,说明本研究中EPDM的添加

Figure 3. The melt crystallization kinetic curves of neat PP (a), PP/EPDM (90/10) (b) and PP/ EPDM (80/20) (c)
图3. 不同材料冷却结晶曲线 (a) 纯PP;(b) PP/EPDM (90/10);(c) PP/EPDM (80/20)
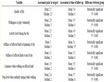
Table 2. Effect of EPDM content on crystallization half-time (t1/2) of PP
表2. 不同EPDM含量对橡塑共混体系结晶速率(1/t1/2)的影响
对PP的结晶起促进作用,表明EPDM在共混体系的冷却结晶过程中对PP具有良好的成核促进作用。
4. 结论
1) 随着EPDM含量增加,共混物冷却速率较纯PP有显著提高。当橡胶含量为40%时,导热系数达到最佳值0.420 W/m×K。
2) EPDM加入之后,导致PP结晶度降低和结晶潜热释放量下降,因此共混组分较纯PP的冷却速率更高。
3) 随着EPDM的加入,使得PP半晶时间t1/2显著缩短,EPDM在共混体系的冷却结晶过程中对PP具有良好的成核促进作用。
致 谢
安徽省教育厅重点研究(KJ2012A011)及安徽大学“211工程”(02303319-0128)联合资助项目。

NOTES
*通讯作者。