1. 引言
在立式电动机、采油钻杆、螺旋传动轴等工程设备上,推力轴承的应用是非常广泛的[1] -[4] 。但由于这些场合中大多伴随有非均布振动、载荷冲击与长期重载运行,轴承摩擦副间的受压润滑膜的流体动力学特性对提高轴承的承载能力、工作可靠性与抗疲劳寿命有着重要的影响。特别是在重载或长期工作下轴承摩擦副间的摩擦性能会变得恶劣,提高润滑膜的承载能力并延长轴承的使用寿命就需要进行润滑补偿。但大多数轴承的密封结构要求与长期工作需要使得润滑剂的补偿难以实现。目前的有润滑轴承采用浸油法或油液外输入法,润滑油在摩擦过程中难以实现内循环,且油膜承载能力取决于润滑油的粘度及润滑液中的极压添加剂,因而限制了轴承的寿命和承载能力。如何提高润滑膜对冲击振动的自适应能力与吸振能力,能否根据外界载荷的变化对界面润滑膜的厚度与组分进行实时调节,成为摩擦领域新的研究课题之一。
近年来有些学者提出将磁流体这一传统上用于密封与阻尼控制的多相混合胶体作为智能润滑剂的设想,并进行了一些工程实践[5] -[7] 。通过对外磁场的调节,改变磁流体的粘度与内纤维结构,从而提高磁流润滑膜的承载能力与抗振吸振性是可行的,也为众多的实验所证明。但由于大部分的轴承类摩擦副的基体材料基本上都是导磁的且一旦在磁场中被磁化后将具有残磁效应,这一问题的出现将加剧磁流体膜的损耗且补充困难[8] 。
正是基于以上考虑,如果能采用多孔材料来制备轴承支撑块,并在轴承座中事先储存一定量的磁流体,通过恰当的结构与控制机构设计,使磁流体能够通过彼此互通的有序贯通孔对摩擦界面间的磁流润滑膜进行连续补充并形成微循环,则可有效解决问题。
2. 实验设计
该实验机采用杠杆平衡原理进行加载,转速在0~200 r/min之间无级变速可调。通过压力传感器、力矩传感器和数据接口,可对过程参数实时显示,且数据采集的频率与采样时间可自行设置。
轴承的外磁场由圆周向均布的6个电磁铁产生,磁场强度可通过对外接直流电源输入电大小调节,实验中所设计电磁铁的输入电流许可范围为0~2 A。
为了后续研究中进行磁场波动和磁场耦合空间分布对轴承摩擦学性能影响分析的需要,输入电源设计为波动直流电源,基本设计要求为:三相输出,相位角相差120度;输出波形为交直流耦合且最低点过零;波形为正弦波且没有失真;输出电流大小可调;波形频率可调。为了剔除导磁材料感生磁场对实验结果的影响,轴承组件中除了多孔轴承块外全部采用硬铝材料制备,如图1。
在影响因素的选择设计上:
外加载荷分别取19.6 N、39.2 N、73.5 N、98 N和147 N;
主轴转速分别取50 r/min、100 r/min、150 r/min和200 r/min;
输入电流分别取0 A、0.4 A、0.8 A、1.2 A、1.6 A和2 A。
实验中,为了尽可能精确记录不同载荷、转速及外加磁场强度下轴承副间摩擦学性能的变化,对摩擦系数每秒采集一次,并以连续的300秒作为一次采集周期。
因此该磁流润滑微循环推力轴承的实现将具有如下优点:
(a) (b)
Figure 1. The structure of inverted cone friction-disc and porous bearing-block
图1. 倒锥摩擦盘和多孔轴承块结构图
1) 可以对轴承摩擦副间润滑膜进行不间断补偿,提高了界间摩擦性能的稳定性,特别适合于需要长期连续作业的工况。
2) 可以通过外磁场控制磁流体的粘度,提高轴承的承载能力。
3) 可以事先储存一定量的磁流润滑胶体于轴承座中,并进行自动补充,延长了轴承的单次维护时长。
4) 如果轴承失效,只需对多孔轴承块进行更换即可且更换方便,极大地降低了维护安装难度。
3. 实验结果分析
在剪切速度较低的情况下,外磁场强度的增加会引起界面摩擦系数的增大,且外磁场强度越大,引起的磁流变剪切阻尼越大;当剪切速度较高时,外磁场的存在会有效降低界面摩擦系数,虽然随着外磁场强度的增加减摩效果有所减弱,但减摩的作用依然大过磁流变阻尼作用。同时在轻载时外加磁场引起的磁流变性会加大界面间的摩擦系数,只有在载荷较大时,磁流微循环推力轴承的减摩作用才得到体现,且载荷越大减摩效果越明显。另外转速越高,磁流润滑的减摩效果越明显。由表中还可看出,由于磁流体在外磁场作用下同时还具有阻尼器的作用,在相同剪切速度下,外磁场强度的增加也将引起摩擦系数的增加,如图2所示。
图中对比可知:在同样的外载荷下,硅油润滑时界面间摩擦系数随转速的增加而增大,而磁流润滑时则随转速的增加而减小。以外载荷W = 147 N时为例,取分别取n = 50 (r/min)和n = 200 (r/min)时的摩擦系数进行对比,硅油润滑时,界面间摩擦系数增大为1.47倍(0.537/0.366),而磁流润滑时,则减小为79.8% (0.323/0.405),减小了20.2%。
同样还可以作出不同外磁场强度下,磁流润滑时界面摩擦系数在不同外载荷下的摩擦系数变化曲线,如图3、图4分别对应于当输入电流I = 1.2 A,1.6 A时摩擦系数变化曲线。
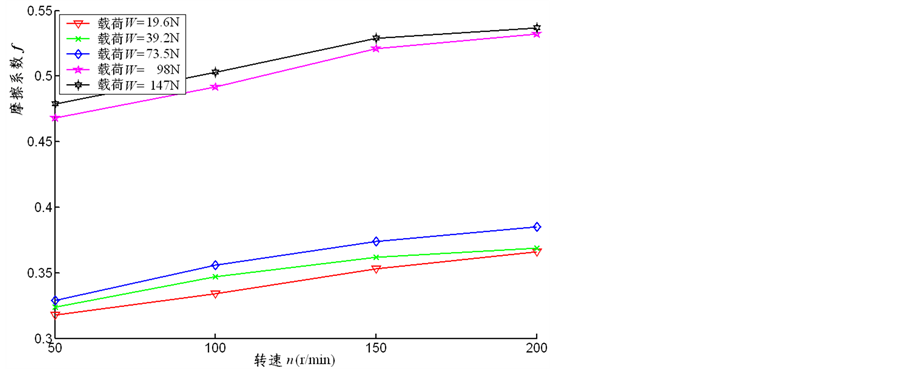
Figure 2. Curves of friction coefficient versus rotating speed in different loadings (silicon oil)
图2. 不同载荷下摩擦系数关于转速的变化曲线(硅油润滑)
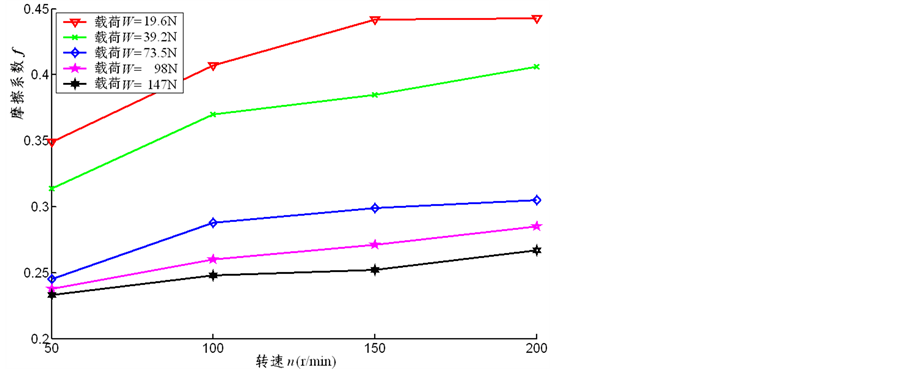
Figure 3. Curves of friction coefficient versus rotating speed in different loadings (ferrofluid, I = 1.2 A)
图3. 不同载荷下的摩擦系数关于转速的变化曲线(磁流润滑,I = 1.2 A)
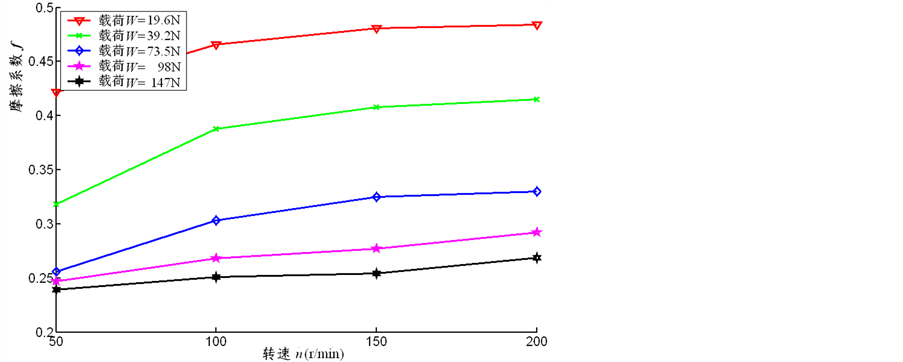
Figure 4. Curves of friction coefficient versus rotating speed in different loadings (ferrofluid, I =1.6 A)
图4. 不同载荷下的摩擦系数关于转速的变化曲线(磁流润滑,I = 1.6 A)
明显得到,转速越高,磁流润滑的减摩效果越明显。由表中还可看出,由于磁流体在外磁场作用下同时还具有阻尼器的作用,在相同剪切速度下,外磁场强度的增加也将引起摩擦系数的增加。
4. 本章小结
本章首先介绍了磁流润滑多孔推力轴承计,开展了相关摩擦学试验并对实验结果进行了分析,得到:界面摩擦系数在非磁流润滑时随转速的增大而增大,而采用磁流润滑时则随转速的增大而减小。