1. 引言
随着人们对飞机油箱系统污染状态研究监测的不断深入,发现飞机燃油系统中出现的多种问题,如油箱严重腐蚀,与燃油系统中积聚的霉菌、酵母菌、细菌等微生物有密切关系,微生物会破坏飞机油箱密封胶的性能,降低密封效果,导致漏油发生重大事故。另外,随着喷气发动机消耗燃油量的提高及整体油箱结构的复杂,使得微生物更易接触燃油系统,造成燃油系统腐蚀的机会也更高。而硫酸盐还原菌(SRB) [1] 的存在是导致微生物腐蚀的重要原因,它在生长过程中产生硫化氢及硫化物等直接破坏飞机燃油系统。研究飞机油箱密封胶在含SRB的航空煤油中长期浸泡后的性能变化,对于飞机安全具有重大意义。
本实验采用的是目前广泛应用于波音737和空客A320的锰固化聚硫密封胶(PR-1440,B-2型)。通过对硫酸盐还原菌(SRB)进行培养,浸泡实验。测定了有关密封胶硬度、断面伸长率、体积膨胀率等参数,并依据美国材料测试协会标准ASTM D4054 [2] 《新型航空燃料及航空燃料添加剂认证及批准标准规范》对飞机油箱密封胶的相容性进行了评估。
2. 研究与方法
2.1. 实验仪器及材料
锰固化聚硫密封胶、SRB菌种、航空煤油;邵氏硬度计(A型)、万能材料拉伸试验机、电子天平、游标卡尺。生化培养箱、超净工作台、蒸汽灭菌器、微生物计数器、橡胶裁刀;革兰染液,丙酮溶液、无水乙醇。
2.2. 密封胶试片制备
PPG提供的套装Semikit Package已按照密封胶配制混合比例称取基胶和固化剂,实验分四次将固化剂加入基胶并搅拌均匀,然后将混合好的胶注入厚为2 mm的模具中,刮平整后置于25℃,湿度为50%环境中固化14天备用。
用标准橡胶裁刀裁剪出符合ASTM D471要求的25 mm × 50 mm × 2 mm矩形试片和D412标准中要求的Die C标准样片,如图1所示。
2.3. 实验内容
1) 分别取6个哑铃型和4个矩形试片,设两组实验,将哑铃型每三个一组[3] ,矩形试片每两个一组,编号;
2) 浸泡前,测量哑铃形试片的硬度和矩形试片的在空气及蒸馏水中的质量;
3) 分别将每三个相同形状的试片悬挂于含有SRB的航空煤油和不含SRB的航空煤油的大试管中(如图2);
4) 在温度设置为37℃生化培养箱中培养60天;
5) 60天后取出,用丙酮洗净油污,滤纸吸干后,用万能试验拉伸机测量哑铃型试片拉伸应力;
6) 测量哑铃形试片硬度和矩形试片在空气及蒸馏水中的质量。
2.4. 硬度
使用邵氏A型硬度计分别测试出浸泡前后密封胶片的硬度值。在浸泡前后计算硬度的改变:
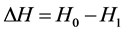
式中:ΔH:浸入前后硬度的改变,单位HA;
H0:浸入前的原本硬度,单位HA;
H1:在浸入后的硬度,单位HA。
2.5. 体积膨胀率
室温下测定,分别称量每个矩形试片在空气及蒸馏水中的重量M1,M2 (精确到1 mg)。在水中称重时,确保试样表面无气泡,为避免测试样本浮起可采用不锈钢作为压载物,使其沉在蒸馏水中。快速地把每个橡胶试片泡在无水乙醇中除水,用滤纸吸干,不可有绒毛或杂物,然后浸入实验装置中。
浸泡60天后,把经过处理的橡胶试片放进已称皮重的烧杯中,记录其在空气中的质量M3和在蒸馏水质量M4。实验过程中,将试片从测试液中移出的时间越短越好。
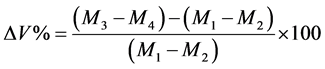
式中:M1:浸泡前试片在空气中的质量,单位/克;
M2:浸泡前试片在蒸馏水中的质量,单位/克;
M3:浸泡后试片在空气中的质量,单位/克;
M4:浸泡后试片在蒸馏水中的质量,单位/克。
2.6. 拉伸强度和断面伸长率
将符合ASTM D412标准中要求的Die C标准样片在150 ml油样中浸泡后,把橡胶试片从试管中取出,迅速把每一个试片浸泡在丙酮溶液中,并用滤纸轻轻吸干不许有绒毛或杂质,保证橡胶试片从处于室温下的航空煤油中移至测试地点的时间介于2 min~3 min。
在万能材料拉伸机上测试出每个胶橡胶试片的最大拉伸强度和断裂伸长率,拉伸速率为50 ± 5 mm/min,最小行程为750 mm,每个浸泡环境下取3个测试样片,求平均值。通过已知的拉伸试片截面积A/mm2,测定施加在两端的拉力F/N,可以得到相应的拉伸强度σ0/Mpa,即

ASTM中拉伸强度单位换算关系式:
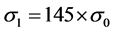
式中:F:施加在两端的拉力,单位/N;
A:拉伸试片截面积,单位/mm2;
:拉伸强度,单位/Mpa;
:拉伸强度,单位/psi。
断面伸长率:

式中:l:试片测量部分原始长度,单位/mm;
L:试片断裂时的最大长度,单位/mm。
3. 结果与分析
3.1. 硬度测试结果(见表1、表2)
从表3可以看出,在37℃条件下,锰固化聚硫密封胶,在无SRB的航空煤油中浸泡60天,浸泡前硬度值为55.0,浸泡后为54.00,硬度减少1.0,符合ASTM D4054的要求。而在含有SRB的航空煤油中,浸泡前硬度值为55.5,浸泡后为49.5,硬度减少6.0,超出标准要求。硬度的减小将直接影响密封胶的强
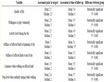
Table 1. The hardness value of PR-1440, B-2 before and after soaking in jet fuel without SRB
表1. PR-1440,B-2在无SRB航空煤油中浸泡前后硬度值
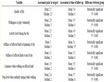
Table 2. The hardness value of PR-1440, B-2 before and after soaking in jet fuel with SRB
表2. PR-1440,B-2在含SRB航空煤油中浸泡前后硬度值
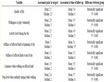
Table 3. ASTM-D4045 for PR-1440, B-2 hardness index requirements
表3. ASTM-D4045对PR-1440,B-2的硬度指标要求
度指标,这将对油箱的安全性造成很大危险。
3.2. 体积膨胀率
从表4中可以看出,PR-1440,B-2在无SRB的航空煤油中浸泡60天,体积发生膨胀,符合要求;在含有SRB的航空煤油中,体积膨胀率为−7.26%,体积出现收缩。究其原因,可以推断SRB的存在改变了密封胶的物理性质。从SRB的代谢机理来看,可能是SRB的生命活动消耗了航空煤油中的烃类组分,并且产生一些硫化物,硫化物的存在影响了密封胶中锰离子的性质,使密封胶的体积收缩减少。
3.3. 拉伸强度和断面伸长率
从表5中可以看出,浸泡前后,在不含有SRB的航空煤油试样中,拉伸强度达到570.9 psi,在含有SRB航空煤油试样中,拉伸强度为537.7 psi,拉伸强度降低了33.2 psi,虽然均符合最低的强度要求。但从表4体积变化来看,在含有SRB的矩形试片中,矩形试片的体积膨胀率为−7.26%,虽然我们肉眼分辨不出来,但通过对比试验可以明显的推断出在含有SRB试样中哑铃形试片的体积也会相应的减少,中间测量部分变细。
表5中,在不含SRB的试样中断面伸长率为209.5%,而在含有SRB的试样中,断面伸长率为189.3%,断面伸长率减小,是因为SRB的存在,破坏了中间测量部分的性质结构,使得强度有所降低。
综上所述,我们可以说明SRB的存在确实破坏了密封胶的部分结构,使得密封胶的强度,伸长率均有所降低。至于深入的破坏机理,目前还不是很清楚,从SRB的代谢过程来看,可能是在SRB生命活
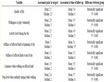
Table 4. The change of the volume expansion ratio of PR-1440, B-2 under different conditions
表4. PR-1440,B-2在不同条件下体积膨胀率的变化
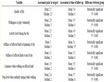
Table 5. The change of mechanical properties of PR-1440, B-2 under different conditions
表5. PR-1440,B-2在不同条件下的力学性能的变化
动过程中消耗了密封胶中硫化物和其他成分,也可能是SRB代谢产生的硫化物和其他成分对密封胶的结构造成破坏。对此,我们还需深入研究。
4. 结论
本实验通过分析实际飞机油箱存在的情况,对航煤中可能存在的微生物进行了研究。研究表明特别是硫酸盐还原菌的存在,大大加剧了油箱密封性能的破坏。我们采用对比实验,分别同时进行了有无SRB的航煤浸泡实验,通过对实验结果进行分析比较,得出了如下结论:
1) 微生物的存在降低了锰固化聚硫密封胶的硬度;
2) SRB的存在使得锰固化聚硫密封胶的体积发生收缩;
3) SRB的存在破坏了密封胶的部分结构,使得密封胶的拉伸强度降低,断面伸长率降低。