1. 引言
众所周知,对于任何系统,子系统越多、构成越复杂,则制造、运输、安装、使用、维护等环节的工作量越大、周期越长、成本越高,不损失系统功能及性能前提下,精简子系统非常重要。煤矿综采系统正是一个众多子系统设备协调配合的典型 [1] 。
本文通过系统优化思想简化综采系统,不仅降低制造、运输、安装、使用、维护等环节成本,还提高各环节效率、减轻工人工作量,于实际工程中极具经济效益和人性化 [2] 。
2. 综采系统简介
煤矿综采系统包括采煤机、刮板输送机、液压支架,三种装备构成综合机械化采煤系统(以下简称综采系统),配套使用 [3] 。采煤机负责采煤、装煤;刮板输送机负责运煤;液压支架负责支护工作面保护人员及设备安全,并与刮板输送机配合,互为支点向前移动,实现工作面回退开采,如图1。
3. 综采系统中心距决定系统繁简程度
综采系统中,几十甚至几百节刮板输送机连续铺设、几十甚至几百台液压支架连续铺设,就形成了中心距的概念(即刮板输送机每节中部槽的长度、或两个相邻液压支架的中心之间的距离),如图2。对于一个工作面,因其长度是固定的,采用不同的中心距,会直接决定综采系统内,输送机中部槽数量、液压支架数量,即中心距直接决定综采系统的繁简程度。目前,综采系统中心距有以下四种:1.25 m,1.5 m,1.75 m,2.05 m;最常用的为1.5 m和1.75 m。
实际工程中,综采系统采用哪种数值的中心距,一般由液压支架结构形式和立柱直径共同决定,如图3。以结构形式为掩护式的液压支架为例,立柱直径 ≥ 360 mm时,必须采用1.75 m中心距(1.5 m中心距无法容纳立柱);立柱直径 ≤ 360 mm时,可以采用1.5 m中心距,也可采用1.5 m中心距,行业习惯做法是采用1.5 m中心距(即通常情况下不人为的增大中心距;若遇到三软采煤工作面、板底工作面、大倾角工作面特殊工况时,会考虑人为增大中心距)。
4. 系统繁简与“制–运–装–用–修”关系
实际工程设计中,任何实体产品或系统至少要评估“制造–运输–安装–使用–维修”五大环节。对于综采系统,系统繁简与五大环节关系如下:综采系统越复杂,系统内设备数量越多,则五大环节工作量同比例上升。五大环节简要说明如下:
制造方面,一套综采系统,在设备制造商的生产车间,数百节刮板机中部槽要制造并联接在一起,数百台液压支架要焊接、加工、组装及调试。
运输方面,一套综采系统要历经五次“千吨级”重物搬运。每套综采系统,设备制造商平均要从钢厂采购2000~3000吨钢材,这是第一次物料大搬运(按吨运输);制成商品再发运到煤矿(一般采用货车运
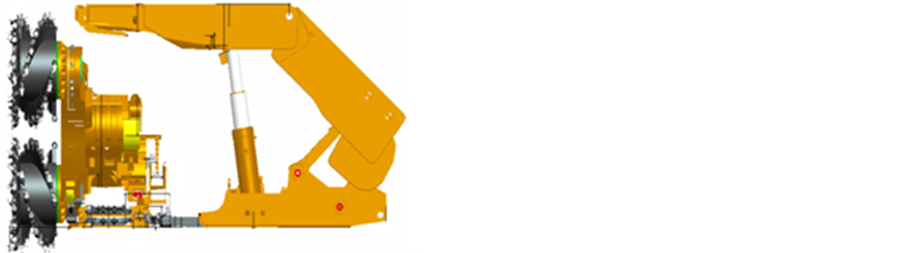
Figure 1. Comprehensive mechanized system section
图1. 综采系统剖面图
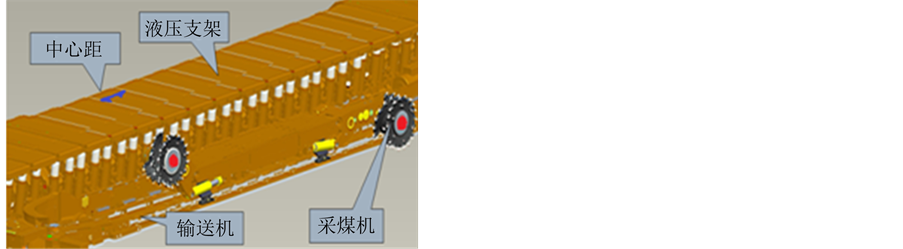
Figure 2. Comprehensive mechanized system layout
图2. 综采系统布局图
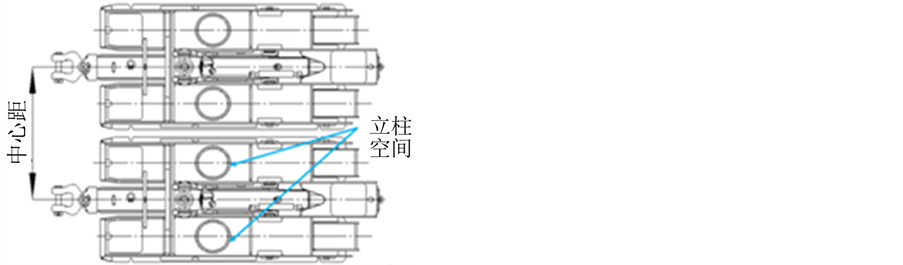
Figure 3. Hydraulic support center distance illustration
图3. 液压支架中心距说明图
输)这是第二次大搬运(按台运输);设备到矿后从地面运到井下这是第三次大搬运(按台运输);从井下设备存放地到综采工作面这是第四次大搬运(按台运输);一个工作面采完后搬移到另外一个工作面(业内称搬家倒面),这是第五次大搬运(按台运输)。
安装方面,一套综采系统安装在井下工作面,要将数百节刮板机中部槽联接在一起,数百台液压支架整齐排列在一起。
使用方面,一套综采系统采每一刀煤(平均一个工作面要采1000余刀),支架操作工人要逐台操作支架,完成“降架–移架–升架–推溜”等一系列动作。
维修方面,一套综采系统,一般分为日常检修和大修。日常检修在检修班时间段完成,逐台查看检修;大修则需要逐台拆除、从工作面运到地面。
综上,“逐台”这个模式,贯穿于综采系统的“制造–运输–安装–使用–维修”全部环节。
5. 综采系统优化的方向
经过前文分析,综采系统中心距直接决定系统的繁简(系统内设备数量多少),“逐台”模式贯穿于综采系统“制造–运输–安装–使用–维修”全部环节,那么,我们就必须重视一套综采系统包含多少台设备,即论证合理的综采系统中心距数值,因为他代表经济效益、代表工作量、代表效率、代表工人劳动强度。
对于任何一个煤矿井下综采工作面,要铺设的综采系统长度是个定值(如300 m),那么这套综采系统含有多少台设备完全取决于中心距。若用1.5 m中心距则200台支架和200节刮板输送机中部槽,机头机尾和过渡槽都忽略;若用1.75 m中心距则172台支架和172节刮板输送机中部槽,中心距由1.5 m增大到1.75 m后,综采系统设备数量减少14.3%,可视为系统简化14.3%,所以,“中心距”决定综采系统的“繁简”,中心距大,则系统简单,反之系统复杂。
6. 综采系统优化的限制条件
按照前文的分析,最理想的综采系统应该是一台采煤机、一节输送机、一台液压支架,但就目前科技水平而言,这只能是理想,无法变为现实,会存在运输能力、设备性能、经济性、行业历史等限制条件。
6.1. 运输能力限制
对于综采系统,增大中心距,意味着设备数量减少,单台设备体积和重量增大。就只有一台液压支架的最理想的综采系统而言,即使不考虑采煤工艺的可行性,我们也将面对2000~3000吨级的巨无霸设备,无论地面运输还是井下运输、安装都没有可行性。所以,运输(地面运输、设备下井、井下运输)制约综采系统中心距增大。目前常用的1.5 m中心距人为增大到1.75 m,大多数现代化矿井运输能力(巷道尺寸和提升重量等)都可满足。
6.2. 设备性能不降低
对于综采系统,适当增大中心距,对采煤机没有影响;对刮板输送机弯曲性能没有影响;对液压支架有支护强度的影响,具体为:单台支架宽度增大,阻力不变,支护强度下降(涉及到立柱、平衡千斤顶、护帮千斤顶、前梁千斤顶、尾梁千斤顶等,用于支护工作面顶板、顶煤、煤壁,具有支护功能的液压千斤顶,如图4)。
这个影响,通过设计即可解决,具体方法是:设计上增大中心距的同时,要增大此类油缸直径以保证液压支架支护强度不下降 [4] 。
6.3. 综合成本的经济性
通过实际工程验证,人为适当增大综采系统中心距,具有设备供应商和用户双赢的经济收益。
以1.5 m增大到1.75 m为例,综采系统总吨位不增加,反而会略有降低,且刮板输送机中部槽数量和液压支架总台数同时减少14.3%,综采系统得到较大幅度的简化,设备供应商的生产和运输成本会下降(尤其液压支架的成本会有可观的下降,原因是综采系统内,因成本高昂的液压系统、立柱千斤顶、电液控制系统减少而产生的收益,远大于单台支架立柱千斤顶重量增加而产生的损失),效率会提升、并且,设备故障率会相应减少(连接点少则故障点少)。.
综采系统内的设备数量减少,用户(煤矿)的运输、安装、日常使用、维护、搬家倒面等工作都得以同等比例的简化,成本大幅降低、效率大幅提高。
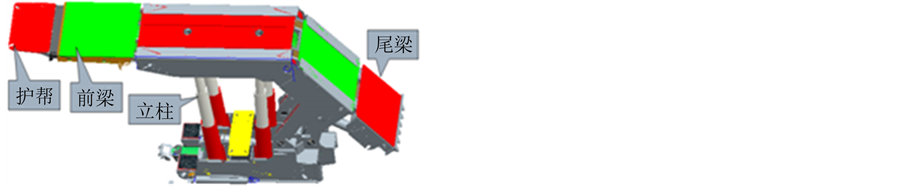
Figure 4. Hydraulic support center distance illustration
图4. 液压支架中心距说明图
经笔者实际工程测算,若1.5 m增大到2.05 m (及1.75 m增大到2.05 m),则因系统中支架产品的立柱千斤顶增重明显(2.05 m中心距时,立柱重量大幅增加),综采系统内支架综合生产成本不降反升,这是设备供应商无法接受的(原因是,支架产品是低毛利商品,按吨售卖,而立柱千斤顶吨成本约是支架市价的2倍,所以,单台支架中,立柱千斤顶重量比例过大,支架成本越高)。
6.4. 行业历史
用于煤矿井工开采的综采系统,其中心距数值在国内乃至全球是统一的(起源于西方发达国家),前文已经提到过,综采系统中心距有以下四种:1.25 m,1.5 m,1.75 m,2.05 m;最常用的为1.5 m和1.75 m。优化综采系统中心距不能超出这个范围(不可以是1.6 m、1.9 m或其他数值),否则会存在支架与刮板输送机不配套,不同厂家之间无法配套、国内与国外不配套、新购设备与原有设备不配套,乱成一片,这是设备供应商和煤矿用户都无法接受的。
6.5. 小结
综上,综采系统优化,必须结合运输能力、设备性能、综合成本、行业历史,以不扰乱行业、不增加设备供应商和煤矿用户负担为前提,实现降本增效 [5] 。就目前4种中心距数值而言,1.25 m的综采系统已基本淡出市场,2.05 m是最大值没有人为增大的优化空间,1.5 m (1.75 m)向2.05 m优化又会造成设备供应商制造成本增加,唯一符合条件的就是1.5 m向1.75 m优化,最重要的是,1.5 m中心距是国内最主流数值,实际工程效益巨大。
7. 综采系统优化的意义
以综采工作面长180 m为例,需要1.5 m中心距液压支架120架,若优化为1.75 m中心距,则减少17个支架,系统得到简化。
一套支架一般要用8年左右,即使1年采1个工作面,那么这套支架要经历8次安装、搬家倒面。若优化为1.75 m中心距,可减少累计136架次的安装、回撤、搬家工作。支架大修1次就要经历升井–拆解–清理维修–组装–再下井,优化后大修工作量减少14%。对于支架日常操作,采每一刀煤,支架工可少操作支架17架次。每刀煤,支架都要经历“降架–移架–升架–推溜”,若一架支架有7种油缸(带伸缩梁和护帮),支架工少操作手柄204次。对于日常检修,主要是液压支架的液压系统和油缸、输送机中部槽互相连接及输送机与液压支架连接,工作量减少14%。
综上,综采系统优化对用户(煤矿)的影响是持续的,我国又是产煤大国(资源结构也是富煤贫油少气),优化意义尤为重大。
8. 结论
设计上,将综采系统中心距从1.5 m人为增大到1.75 m,同时增大工作阻力确保支护强度不降低,
表1. 优化收益
使综采系统化繁为简,技术可行、经济双赢(设备供应商和煤矿用户)、效率提升、井下工人劳动强度降低,收益如表1。
以“设计上人为增大中心距”的方法简化综采系统“一举多得”,是行业趋势,应被考虑纳入行业标准,惠及全行业。
通过设计手段优化(简化)工业系统的思想,应深置于广大技术人员思维中,共同推动我国工业系统科学持续发展,实现高效、低耗运转。