1. 引言
随着我国汽车产销量快速增长,汽车物流行业近年来也取得了迅猛发展。中国汽车物流的发展形成了以整车物流为主,向零部件入厂物流、零部件售后物流以及进出口物流方向延伸的竞争新格局 [1] 。汽车物流企业在物流模式方面进行了诸多探讨,取得了较好的应用效果,学者们也进行了相关研究,陈艳 [2] 探讨了循环取货模式在汽车零部件供应物流中的应用问题,对循环取货的产生和发展、基本原理及其作业流程等理论进行分析探讨,并与传统供货模式进行对比分析,得出循环取货模式的特点及优势;李志权 [3] 探讨了循环取货成本节省的关键因素,建立了循环取货库存成本运输成本的节省模型,最后从企业、供应商、第三方物流企业三个方面分析了循环取货模式的适用范围,并提出循环取货模式的优化方案;林昀 [4] 研究了一个具体公司对于远距离零部件供应商循环取货模式的实证研究,通过对循环取货五个应用环节的详细规划设计,提出一套关于远距离零部件供应商循环取货的解决方案;吕媛媛 [5] 研究分析了基于第三方物流的零部件循环取货入厂物流模式,并对其组织框架和实施条件进行比较分析,设计了基于3PL的循环取货物流方案。基于蚁群算法对循环取货车辆路径优化模式进行了求解分析。本文以安吉零部件物流公司为研究对象,探讨安吉零部件物流公司的供应商选址和物流流程优化,构建循环取货流程优化方案,提高安吉自身的行业竞争力,具有重要的现实意义。
2. 安吉零部件物流循环取货流程问题分析
2.1. 安吉零部件循环取货现状
1) 循环取货特点
循环取货(Milk-run),是一种第三方物流公司用同一运输车辆从多个供应商处装载零配件模式。具体运作方式是在固定时刻,货车从入厂仓库出发,到各个特定供应商处,依照特定的线路,以及装载特定的货量。这样既提高了运输车辆的装载率,又能使物料得到及时补给,同时对于供给量较少的供货商不必等到零部件积满货车再发运,在最大程度上实现JIT供给。图1和图2分别描述了传统直送入厂物流模式和循环取货方式入厂物流模式的差别。
循环取货优化方法的关键就是优化物流配送系统网络,其特点是多频率、小批量,弥补传统直送运输模式配送路程过长的不足,优化配送路径,持续提高产品供货频次,减少运输成本。
2) 循环取货流程
安吉零部件物流负责汽车制造商的全部零部件入厂物流方案设计,依据循环取货运输方式,建立本地入场仓库与外部运输系统对接。其作业流程大致如下图3所示。
计划阶段:安吉零部件物流通过获取制造商的采购订单,通过信息系统平台的线路设计,生成操作调度,并下达具体的指令操作,这是零部件物流循环取货的准备阶段,也称计划阶段。
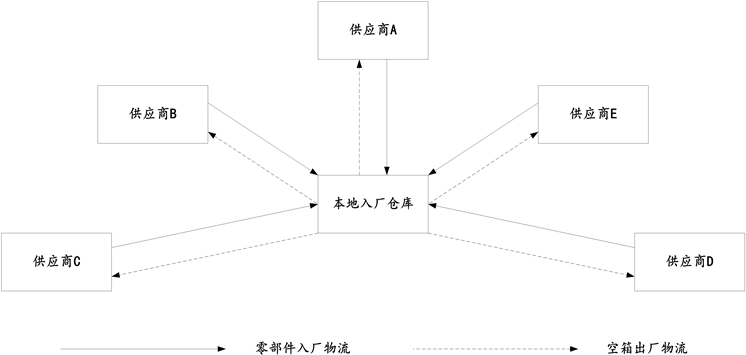
Figure 1. Traditional direct logistics mode
图1. 传统直送入厂物流模式
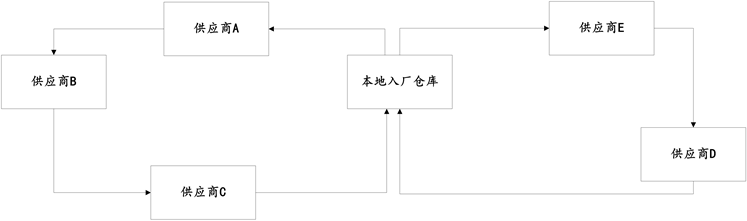
Figure 2. Milk-run Logistics mode
图 2. 循环取货入厂物流模式
实施阶段:在固定的时刻,货车从本地仓库出发,到各个特定供应商处,依照事先特定的线路,装载特定的货量。这样既提高了运输车辆的装载率,又能使物料得到及时补给,同时批量较少的供货商不必等到零部件积满货车再发运,司机和仓库管理员进行运输任务单交接,并填写路线运行记录表,在最大程度上实现JIT供给。具体循环取货流程图4和路线运行表如下表1。
入库阶段:入库扫描人员都可在仓库管理系统中查询零部件入库实绩,并与入库计划核对,还可査询更新后的各零部件库存。在出货前,首先要根据主机厂的物料需求计划制作出相关的备货指示计划,由信息系统生成备货指示书和出货明示卡,指导出货人员完成备货分拣任务。备货人员根据备货指示计划,在相应的工作时间进行对应的备货作业。仓库管理系统按照“先进先出”原则,对已完成备货工作的存放在出货场的零件进行审核,扫描出货明示卡,更新零部件库存。
安吉零部件物流有限公司可以将车辆所取零部件通过循环取货的方式直接送到安吉整车厂所在的本地入厂仓库,其外地取货频次为每六小时一车次,本地配送频次为每两小时一车次。同样安吉零部件物流有限公司的车辆按预先设置好的线路依次从供应商处取货,同时依次返还空料箱,供应商根据生产计划备每日发货量,安吉物流公司负责取货,如下图5所示。
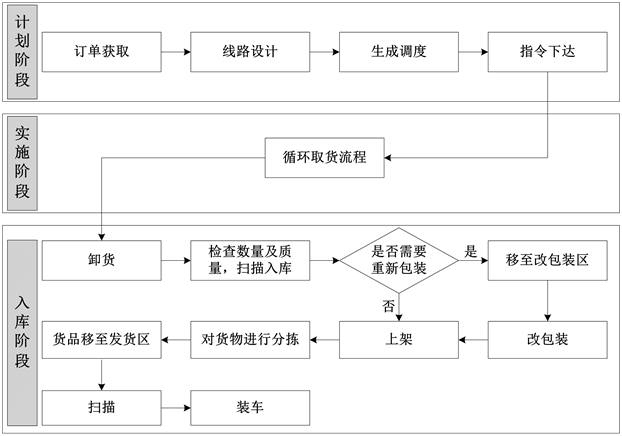
Figure 3. Operation flow of parts inbound logistics in Anji
图3. 安吉零部件入厂物流作业流程图
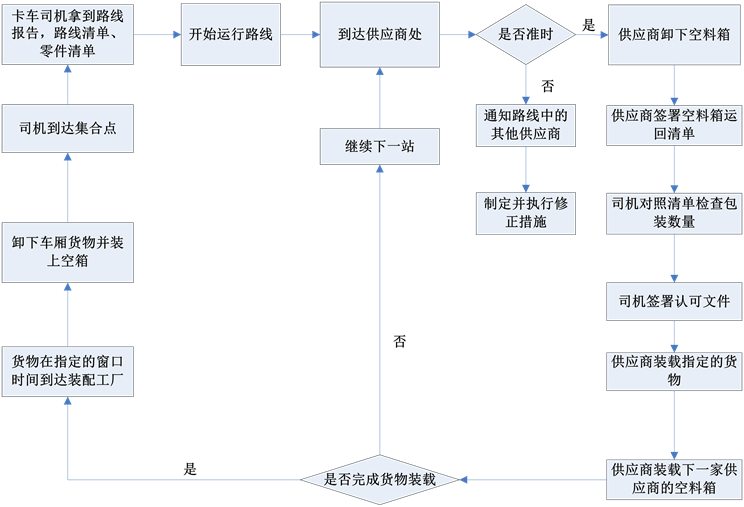
Figure 4. Operation flow of parts milk-run logistics in Anji
图4. 安吉零部件循环取货流程流程图
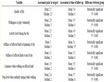
Table 1. Record list of operation of parts milk-run logistics route in Anji
表1. 安吉零部件循环取货线路运行问题记录表
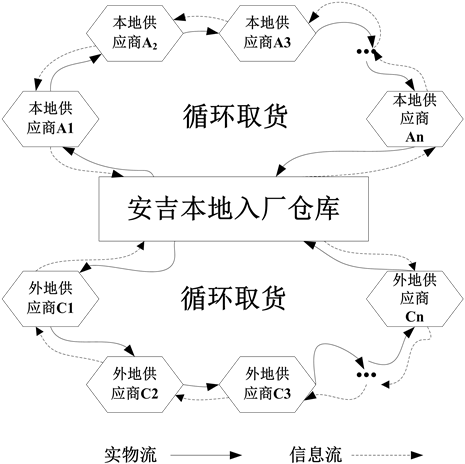
Figure 5. Logistics mode of parts inbound logistics in Anji
图5. 安吉零部件入厂物流模式
2.2. 安吉零部件循环取货问题分析
通过对安吉物流流程各个环节的分析,发现在循环取货的过程中存在如下问题:
1) 配送成本过高
安吉零部件物流在入厂场物流具体实施过程中,无论本地供应商还是外地供应商,均是直接将车辆所取零部件通过循环取货的方式直接送到安吉整车厂所在的本地入厂仓库,而对于外地供应商将零件送往本地入入厂仓库的费用问题却没有进行有效预估,尤其对于极少批量的货物动辄就直接运往本地入厂仓库的费用更是增加了公司配送成本,造成了人力、财力和时间成本的浪费。
2) 运输责任不明确
在循环取货过程中,由于涉及到安吉零部件物流、供应商和制造商三方如果出现意外运输事故时,不及时明确责任,三方会相互推脱责任,因此必须制定好职责分配,这样才能保证循环取货项目正常运行。而由安吉零部件现有循环取货线路运行问题记录表,发现根本就没有涉及到责任确认问题,司机并无须对货物的安全送达负责,供应商也没对其进行记录,在整个配送过程中,供应商、安吉零部件、制造商三方分工不明确,导致运输责任不清晰。
3) 货物质量无保障
在循环取货过程,由于这个过程是多方参与,供应商不可能派工作人员随车进行货物交付,制造商也不可能跟踪检测,安吉零部件物流公司也不会进行质量检测,所以在循环取货过程中货物质量并无有效保障。
3. 安吉零部件供应商选址与循环取货模式设计
3.1. 零部件供应商选址优化
本文SCC (Supplier Consolidation Center)供应商集货中心采用重心法选址,重心法理论模型完成SCC的选址之后,选取距离最近的供应商企业仓库作为SCC。
1) 供应商SCC选址方式
a) 在SCC选址的建模假设
安吉零部件循环取货的物流成本以运输费用的形式表现,而且产品的运输费用仅仅和供应商集货中心(SCC)、供应点之间的直线距离成正比例关系,而不考虑其他因素;
不考虑集货中心(SCC)所处地理位置不同所引起的成本差异,如土地使用费、建设费、劳动力成本、库存成本等。
记SCC到安吉零部件供应商点j的运费为
,总运费为H,则有:
(3-1)
(3-2)
式中
——SCC到安吉零部件供应商j的运费费率,即每吨公里的运输费用:
——安吉零部件供应商j到SCC的物流量;
——SCC到安吉零部件供应商j的距离,即
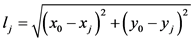
因此,可以将重心法选址模型最优评价函数模型表示为:
(3-3)
为求得总运费最小的安吉零部件SCC的位置,对x0, y0求偏导数,并令其为0,有:
(3-4)
(3-5)
由式(3-4)和式(3-5)可得SCC最适合的坐标为:
(3-6)
(3-7)
但是由于式(3-6)和式(3-7)中含有lj, 即含有x0, y0,不能直接求出SCC的坐标,因此采用迭代计算的方法进行SCC的选址。
b) 具体步骤如下:
选取SCC规划位置点的初始解,记为
。可以利用公式(3-8)和(3-9)计算各供应商位置之间的几个重心点
,并将几何重心点作为初始SCC规划的地点。
(3-8)
(3-9)
计算与
对应的总费用
;
把
带入式和式(3-7),计算SCC的改善点
;
利用(3-1)计算与
对应的总费用
;
如果
,说明
是最优解;如果
,说明结果得到改进,有待进一步优化,返回到第5步,计算再次改善的新位置;如此反复迭代,直到第
,使得
,求出最优解
。此时的
即为SCC最佳选址的位置,
即为最小的总运输费用。
2) 供应商SCC选址运算
通过对安吉零部件物流公司17家循环取货供应商分析,根据离安吉零部件入厂仓库的距离,可以将其分为:本地供应商、近距离外地供应商、远距离外地供应商三类,以下分别对这三类供应商进行路径优化。
a) 本地供应商SCC选址
根据安吉零部件精益生产需求,对上海市零部件供应商循环取货的频次设为每天一次,取货车辆长度为7.2 m,单车最大载重量8 T,装车容量设为24.4 m3,运输费率为10元/km,运输速度为25 km/h。安吉零部件本地供应商分布如下表2。
采用重心法对这8家零部件供应商SCC进行选址分析,首先用几何重心法确定初始SCC选址位置为:
。
将初始解
进行迭代运算得到最优解,则SCC选址的最优点位置为(121.39776, 31.11409),经比较分析,F公司离最优点最近。
b) 外地供应商SCC选址
便于计算,将外地供应商的相关参数设置同本地供应商。将表3外地供应商供货情况也用重心法计算。安吉零部件外本地供应商分布如下表3。
通过计算可得到,近距离外地供应商SCC选址的最优点位置为(121.3229758, 31.1562122),通过比较分析发现与本地B公司(121.3629758, 31.2572222)最接近,主要从经济效益方面考虑,可以租用地B公司仓库作为SCC。同样,通过重心法可以求得远距离外地供应商SCC选址的最优地点,通过比较发现距离其最优点的远距离供应商最近的是F1公司,所以可以租用F1公司仓库作为SCC。
3) 优化效果分析
通过上节SCC的选取,重新对循环取货路线进行规划,并测量出其距离,并且通过SCC的选取,安吉零部件物流公司的循环取货路线可以不从本地出发,而可以从SCC出发,将各个地方的货物取完后再送往安吉零部件物流本地入厂仓库。
a) 本地供应商SCC选址前后比较分析
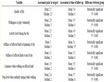
Table 2. Distribution and supply of local parts suppliers of Anji
表2. 安吉零部件本地供应商分布及供货情况
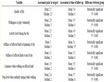
Table 3. Distribution and supply of non-local parts suppliers of Anji
表3. 安吉零部件外地供应商分布及供货情况
通过本地供应商SCC选定后,可以先从F点出发循环取货,将其他供应商的货物全收集于F点,再从F点直接将货物送往到A点。具体本地供应商运输路线优化后分布图如下图6。
通过比较可知:
原来本地总路程 = 11.2 + 8.8 + 8 + 11.4 + 25.3 + 10.3 + 17.4 + 13.2 + 13.6 = 111.2 km
优化后本地总路程 = 15.5 + 11.2 + 8.8 + 8 + 14.1 + 10.3 + 17.4 + 16 + 5.9 = 99.2 km
所以优化后,安吉零部件本地供应商总运输路线缩短了12 km。
b) 外地供应商SCC选址前后比较分析
通过近距离外地供应商SCC选定后,可以先从B点出发循环取货,将其他供应商的货物全收集于B点,再从B点直接将货物送往到A点。具体近距离外地供应商运输路线优化后分布图如下图7。
通过远距离外地供应商SCC选定后,可以先从F1点出发循环取货,将其他供应商的货物全收集于F1点,再从F1点直接将货物送往到A点。具体远距离外地供应商运输路线优化后分布图如下图8。
比较图6、图7和图8可知:
原来外地总路程L = 30 + 113 + 82.7 + 98.5 + 71.3 + 60.4 + 7.5 + 46.8 = 510.2 km
优化后近距离外地路程L1 = 15.3 + 29.9 + 7.5 + 21.5 + 6 = 80.2 km
优化后远距离外地路程L2 = 70 + 74.2 + 95.8 + 41.3 + 117 = 398.3 km
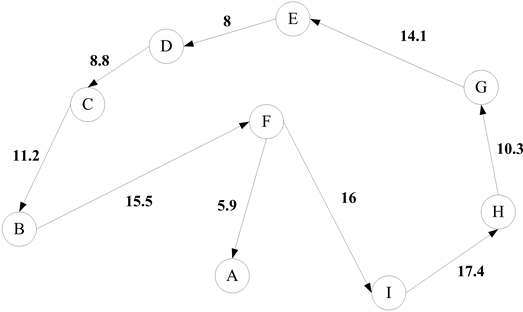
Figure 6. Transportation route map of local supplier after optimization
图6. 本地供应商运输路线优化后分布图
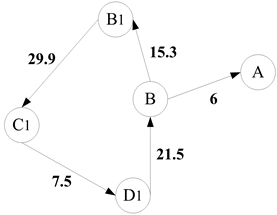
Figure 7. Transportation route map of close-range non-local supplier after optimization
图7. 近距离外地供应商运输路线优化后分布图
优化后外地总路程 = L1 + L2 = 478.5 km
所以优化后,安吉零部件外地供应商总运输路线缩短了31.7 km。
3.2. 循环取货物流配送模式设计
通过以上分析,可以将本地供应商循环取货将货物运往安吉零部件本地集货中心和近距离外地供应商循环取货将货物运往安吉零部件本地集货中心归为一类入厂物流模式,即第一类入厂物流模式,本模式较适合于小批量的,距离本地入厂仓库距离较远的本地供应商和外地供应商,如下图9所示。
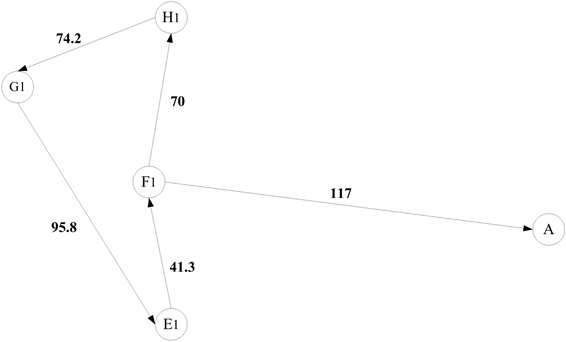
Figure 8. Transportation route map of long-range non-local supplier after optimization
图8. 远距离外地供应商运输路线优化后分布图
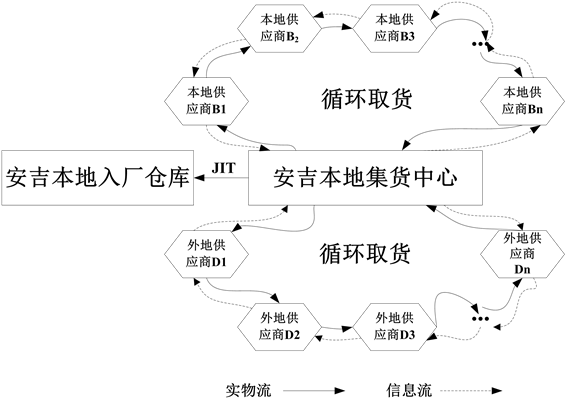
Figure 9. First kind of logistics mode of parts inbound logistics in Anji
图9. 第一类入厂物流模式
而将远距离外地供应商循环取货将货物运往安吉零部件外地集货中心,再送往安吉零部件本地入厂仓库归为第二类物流模式,对于第二类入厂物流模式,本模式较适合于小批量的,距离本地入厂仓库距离很远的外地供应商,如下图10 所示。
并通过以上分析,安吉零部件物流循环取货模式可以分为循环取货1、2、3三种,如图11所示。
3.3. 两种模式对比分析
从实施对象、实施范围、零部件需求计划提前期、运行总路程、配送总成本和卸货地点六个方面对安吉零部件物流循环入厂配送模式对比分析。如表4所示。

Figure 10. Second kind of logistics mode of parts inbound logistics in Anji
图10. 第二类入厂物流模式
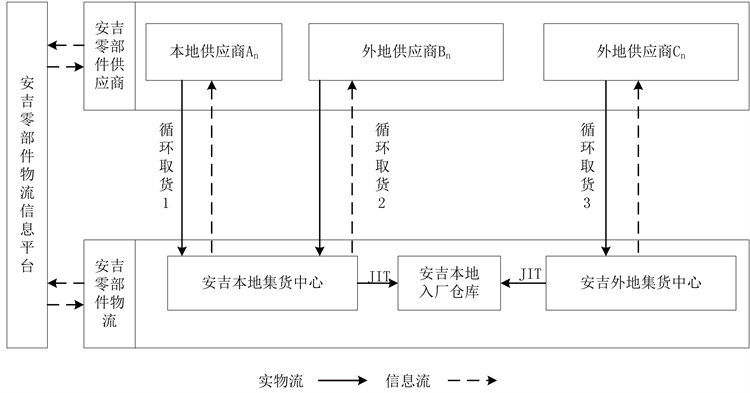
Figure 11. Milk-run mode of parts inbound logistics in Anji
图11. 安吉零部件入厂物流循环取货模式图
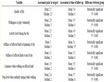
Table 4. Comparison of parts milk-run inbound logistics in Anji
表4. 安吉零部件循环取货入厂物流模式对比表
通过循环取货模式的改进,节约了配送成本、优化了循环取货的路线,达到路径优化的效果,从而缩短运输路程,降低运输成本。在流程中更是加设了信息核对以及应急措施的制定环节,便于能在最短时间完成循环取货任务,保证了运输过程中产品质量的安全性,减少了残次品概率。
4. 结论
从安吉零部件物流公司存在的循环取货问题入手,运用定性和定量的分析方法,指出了安吉零部件物流配送运输成本高、运输责任不明确和质量无保障方面的问题;运用重心法对集货中心进行目标选址,设计了两类新的入厂模式,优化了流程设计,安吉零部件本地供应商总运输路程线缩短了12公里/次,需求计划提前期时间缩短了0.48小时/次,运输成本节省了120元/次。安吉零部件外地供应商总运输路程缩短了31.7公里/次,需求计划提前期时间缩短了1.268小时/次,运输成本节省了317元/次。取得了明显的效果,提高了安吉零部件物流循环取货的效率,增强了企业的核心竞争力。
基金项目
国家社科基金项目资助,低碳制造下陶瓷供应链碳排放测度与控制研究,项目编号:2017BJY008。