1. 引言
土压平衡盾构机中心回转组件位于盾构机前盾的中心位置,其前端与刀盘通过螺钉连接。中心回转组件的内部设有数个流体通道,中心回转组件与刀盘连接后,该流体通道与刀盘上的管路连接,其作用是向刀盘的面板上输送泡沫或膨润土以及向仿行刀液压油缸输送液压油 [1] 。通过对某土压平衡盾构机中心回转组件旋转接头安装法兰连接螺钉断裂、轴线偏摆,回转组件整体后移等现象进行原因分析和故障排查,并提出中心回转组件的受力计算方法和结构改进方案,为盾构机设计人员、广大盾构机施工人员提供一些参考和建议。
2. 故障概况
某土压平衡盾构机在投入使用初期,中心回转组件出现了旋转接头安装法兰连接螺钉断裂故障,在对断裂螺钉更换后继续施工,随后出现了中心回转组件轴线偏摆的问题,在之后3个月的施工中中心回转组件一直在轴线偏摆的状态下运转,直至发现中心回转组件整体后移的故障,停止施工。经测量,中心回转组件整体向后移动了约70 mm距离。
3. 故障原因分析和排查
3.1. 中心回转组件工作原理和受力情况
中心回转组件包括中心集成块、管路保护罩、中心轴1、中心轴2、中心轴法兰、中心回转密封、旋转接头安装法兰、旋转接头、连接销以及O型圈等(图1)。鱼尾刀从后往前安装在刀盘的中心位置,鱼尾刀安装座位于鱼尾刀后方,并与鱼尾刀通过螺钉连接。中心集成块位于鱼尾刀安装座后方,与刀盘通过16根M20螺钉连接,用以承受施工中鱼尾刀产生的轴向力F1 [2] ,并克服施工中土仓中的渣土对中心集成块、管路保护罩、中心轴1、中心轴2产生的摩擦力矩Tz1,渣土对中心轴法兰产生的摩擦力矩Tz2,切口环封头对中心回转密封产生的摩擦力矩Tr,以及旋转接头内部的摩擦力矩TR。克服Tr所需的驱动扭矩经中心集成块、中心轴1、中心轴2、转接头安装法兰及其之间的连接螺钉、连接销传递至中心回转密封上;克服Tz2所需的驱动扭矩再经中心回转密封传递至中心轴法兰上,克服TR所需的驱动扭矩经旋转接头安装法兰传递至旋转接头上。可见,克服Tz2、Tr和TR三者的驱动扭矩均通过C-C截面上的连接螺钉和连接销进行传递。
其中切口环封头对中心回转密封产生的摩擦力矩Tr以及旋转接头内部的摩擦力矩TR为盾构机设备自身特性,为一恒定值。渣土对中心轴法兰产生的摩擦力矩Tz2可使用如下公式计算 [3] :
(1)
1-中心集成块,2-中心轴1,3-中心轴2,4-旋转接头安装法兰,5-中心回转密封,6-中心轴法兰,7--旋转接头,8-连接销,9-螺钉M16,10-螺钉M20,11-管路保护罩,12-鱼尾刀,13-鱼尾刀安装座,14-刀盘
Figure 1. Principle of centre rotation component
图1. 中心回转组件结构图
式(1)中各符号意义如下:
μ—渣土与中心轴法兰摩擦系数;
Pz—土仓内土压(由于地下水产生的摩擦力较小故在计算时不考虑地下水压),MPa;
DF—中心轴法兰外径,mm;
dF—中心轴法兰内径,mm。
Tz1包含渣土对管路保护罩的摩擦阻力矩T1和中心轴1和中心轴2的摩擦阻力矩T2,即:
(2)
T1、T2可使用如下公式计算:
(3)
(4)
式(3) (4)中各符号意义如下:
Abh—管路保护罩前面和背面与渣土的有效摩擦面积mm²;
Lbh—管路保护罩半径,mm;
Dzx—中心轴外径,mm;
L1—中心轴1长度,mm;
L2—中心轴2与渣土摩擦面长度,mm。
3.2. 中心回转组件故障排查和分析过程
3.2.1. 首次故障即C-C截面连接螺钉和连接销断裂故障分析及处理措施
(1) 故障现象
在初始施工阶段例行检查时发现刀盘转动时旋转接头及其安装法兰并未随之转动。发现上述情况后,遂组织对该故障进一步检查确认。往刀盘上注入泡沫检查,发现中心回转组件上排气管螺塞处有泡沫泄露;随后拆除旋转接头进一步检查,观察到C-C截面上螺钉和连接销全部断裂,中心轴2也严重磨损,如图2所示;继续对中心回转密封中的油脂填充情况进行检查,发现密封舱内油脂填充充分,满足密封和润滑要求。
(2) 故障分析过程
根据前面故障现象及所掌握的已知信息,结合图1结构,初步判断C-C截面螺钉和连接销断裂的原因有三点:
① 旋转接头出现故障不能转动。
② 螺钉M16预紧力不够使中心轴2和旋转接头安装法兰之间摩擦力矩不够或连接销剪切强度不够;
③ 中心回转密封转动时阻力矩过大;
对于序①:施工现场将旋转接头拆下后进行手动盘车,转动灵活,故该原因可以排除。
对于序②:查看图纸发现,旋转接头安装法兰与中心轴2连接面C-C截面与其它连接面上连接螺钉数量和规格相比,C-C截面螺钉数量最少,只有9件,规格M16;而其它联接面的螺钉数量为16或18件,规格为M16或M20,因此可以判断C-C截面为危险截面,故需要对C-C截面强度重新进行校核。
由于连接销与销孔之间存在0.25 mm间隙,扭矩只能通过9件M16螺钉在中心轴1和中心轴2之间
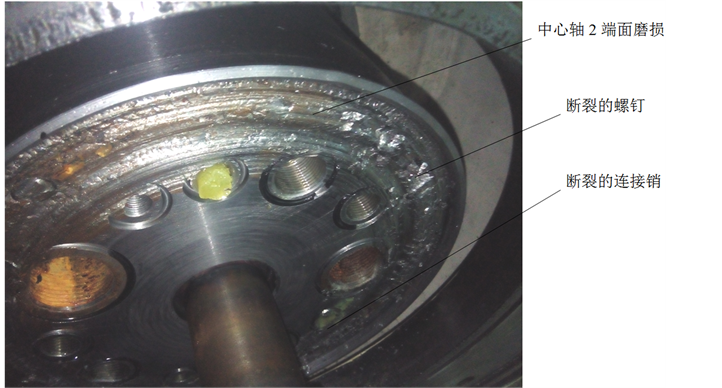
Figure 2. Fracture of bolt and pin in C-C section
图2. C-C截面连接螺钉和连接销断裂情况
的法兰面上的预紧力产生的摩擦力进行传递,或者通过连接销承受的剪切力进行传递。因此在对螺钉或连接销进行强度校核时,要单独进行计算,而不能视为连接销和螺钉同时作用来传递扭矩 [4] 。
(一) 通过连接销传递扭矩时,连接销上产生的剪切应力可以使用如下公式计算:
(5)
式(5)中各符号意义如下:
F—连接销所受剪力,N;
A—连接销截面积,mm2;
d—连接销直径,mm;
L—连接销安装半径,mm;
Tr—切口环封头对中心回转密封产生的摩擦力矩,N×m;
TR—旋转接头内部的摩擦力矩,N×m;
Tz2—渣土对中心轴法兰产生的摩擦力矩,N×m。
经计算,连接销剪切应力为287 MPa,连接销由45优质碳素钢材料制成,许用剪切应力328 MPa,安全系数为1.14。
(二) 通过连接面摩擦力传递扭矩时,螺钉达到手册规定的预紧力时在连接面产生的摩擦力能传递的扭矩可以使用如下公式计算:
(6)
式(6)中各符号意义如下:
μ—摩擦系数;
nls—螺钉个数;
Fy—螺钉预紧力,kN;
rls—螺钉安装半径,mm;
Kf—可靠性安全系数。
9根8.8级螺钉达到手册规定的预紧力时,能传递的扭矩连计算结果为3.6 kN×m,而
为9.7 kN×m,故螺钉预紧力不能传递足够的扭矩来克服摩擦阻力。
根据上述(一) (二)可以得出,C-C截面上扭矩由连接销进行传递,且连接销设计安全系数偏小(安全系数值为1.14)。
对于序③:如中心轴法兰及土仓壁板上发生结泥饼现象,则会导致中心轴法兰转动时阻力矩超过设计值。遂开仓检查,证实了土仓内中心轴法兰及土仓壁板上确实有大量泥饼存在。
因此结合上述对序②、序③分析,判定连接销设计安全系数偏小且施工中未及时对渣土进行有效的改良导致土仓内有大量泥饼产生,是此次故障发生的主要原因。
另外在判定故障原因时,有一个主观因素不可忽视,即:相同的机型以往曾经发生过中心轴法兰因与其他物体接触使其旋转阻力过大而导致C-C截面连接螺钉和连接销被剪断的故障,所以此次故障发生时大家普遍认为该此次故障发生原因与上次故障原因类似。
(3) 处理措施
在经过以上分析后,故障处理措施为:更换中心轴2、旋转接头安装法兰、9件M16 × 85连接螺钉、连接销及相应的密封圈;并在中心集成块和中心轴1、中心轴1和中心轴2、中心轴2和中心轴法兰之间分别增加4处长150 mm焊高8 mm或5 mm焊缝。
原结构中,驱动中心轴法兰旋转的力矩通过中心轴2、C-C截面、旋转结构安装法兰及中心回转密封传递至中心轴法兰上,在中心轴2和中心轴法兰之间增加焊缝后,驱动中心轴法兰旋转的力矩通过中心轴2以及中心轴2与中心轴法兰间的焊缝直接传递到中心轴法兰上,受力情况得到有效改善。
但是,更换并复装中心轴2等零件过程中,维修人员发现中心轴法兰与切口环封头之间的间隙比图纸小了3 mm,这一关键细节信息未引起维修人员的警觉,维修人员也未对这一信息进行有效传递。而正因为忽视了这一个小细节,错过了发现故障的根本原因以及解决该故障的最后一次机会(后续施工中已脱离了加固区的保护,不再具备开仓维修条件),从而导致后续一系列更严重问题的发生。
2.2.2. 中心回转组件轴线偏摆的问题分析及处理措施
在对中心轴2、旋转接头安装法兰、C-C截面连接螺钉和连接销进行更换后盾构机继续施工,运行约1周后发现中心回转组件存在轴线偏摆现象,停机检查未发现异常。分析后认为可能是中心轴2复装过程中与中心轴1轴线不重合导致。在此过程中未注意中心回转组件是否存在后移现象,对该偏摆故障也一直未进行处理,于是在之后施工中中心回转组件一直在轴线偏摆的状态下运转,直至发现新的故障,方才停止施工。
2.2.3. 中心回转组件整体后移的故障分析及处理措施
(1) 故障现象
继发现中心回转组件存在轴线偏摆现象后,盾构机继续施工了约3个月的时间,在对中心回转组件进行例行检查时发现中心回转组件在轴向向后移动了约70 mm。发现此故障时,旋转接头、中心回转密封、旋转接头安装法兰均可以随刀盘转动。由于此时盾构机处于富水地层,无法开仓检查。为进一步确认故障,对中心回转组件上的仿行刀液压油管进行压力测试,发现仿行刀液压系统压力无法升高。
(2) 故障分析过程
根据前面故障现象及所掌握的已知信息,结合图1结构,初步判断旋转接头后移70 mm的原因有四点:
① A-A截面螺钉断裂;
② B-B截面螺钉断裂;
③ 中心集成块与刀盘连接螺钉断裂;
④ 中心轴法兰或驱动部中心封头损坏;
对于序①和序②:在刀盘转动时,旋转接头、中心回转密封、旋转接头安装法兰均可以转动。而如果序1和序2发生,则旋转接头、中心回转密封、旋转接头安装法兰无法转动。故序1和序2可以排除。
对于序③:在盾构机正常施工时,刀盘所承受的轴向推力有一部分由鱼尾刀承受。鱼尾刀所受的轴向力通过鱼尾刀座传递到中心集成块上,然后通过中心集成块与刀盘之间的16根连接螺钉传递到刀盘背面的法兰上。盾构机始发过加固层过程中,如果未按照《操作说明书》的要求在鱼尾刀前方的加固层上预先开挖出一个缺口,则会在刀盘面接触到掌子面之前鱼尾刀先接触到了掌子面,那么本应该由刀盘面承受的盾构机前进的推力将完全作用在鱼尾刀上,当鱼尾刀所受的轴向力超过连接螺钉的破断载荷时,螺钉就会被拉断。因此初步判断中心集成块与刀盘连接螺钉断裂。需要对连接螺钉能承受的载荷进行校核计算。
(7)
式(7)中各符号意义如下:
n—螺钉数量;
σb—螺钉材料抗拉强度,MPa;
As—螺钉小径公称应力截面积,mm²。
经计算,16根8.8级M20螺钉破断载荷为3136 kN,即使在始发过程中,盾构机推力也高达10,000 kN以上,该推力足以使连接螺钉受力断裂。连接螺钉断裂后,鱼尾刀及中心回转组件在掌子面轴向力的作用下后移。由于中心轴法兰驱动部封头之间只有5 mm间隙,当中心回转组件后移量达到5 mm时,驱动部中心封头就会与中心轴法兰发生接触,阻挡中心回转组件继续后退。
当序④也发生时,即中心轴法兰或驱动部中心封头损坏时,中心回转组件才能继续后退。因此,只有序③、序④必须同时存在才能出现旋转接头向后移动70 mm的现象。从工作原理和结构分析,只有长期的挤压和磨损才能导致中心轴法兰或驱动部中心封头发生损坏。但在中心集成块与刀盘连接螺钉未断裂的情况下,并不会产生挤压和磨损的情况,因此可以得出“序③中心集成块与刀盘连接螺钉断裂”已经发生了相当长的一段时间。序③发生后长时间的挤压和磨损导致了序④的发生,从而出现了旋转接头向后移动70 mm的现象。
但,仍有一个问题需要进行说明,即:中心集成块与刀盘连接螺钉断裂后,刀盘已不能通过连接螺钉带动中心回转组件旋转,但直到故障被发现时中心回转组件仍在跟随刀盘旋转。根据中心回转组件结构,初步判断如下:中心集成块与刀盘之间的连接管路未全部断裂,起到了带动中心回转组件跟随刀盘一起旋转的作用。故需要校核中心集成块与刀盘之间的钢管的强度能否带动中心回转组件旋转。
中心回转组件所受到的旋转阻力矩Tz为土仓中的渣土对中心集成块、管路保护罩、中心轴1、中心轴2产生的摩擦力矩Tz1,渣土对中心轴法兰产生的摩擦力矩Tz2,切口环封头对中心回转密封产生的摩擦力矩Tr以及旋转接头内部的摩擦力矩TR之和 [5] ,即:
(8)
经计算,中心回转组件旋转阻力矩Tz值约为50 kN×m。
中心集成块与刀盘连接的管路共有11根,材料为20号钢,规格如下表1。
对中心集成块及刀盘连接管路进行有限元计算,在11根管路与刀盘连接面施加约束,给中心回转组件施加50 kN×m的旋转载荷,分析结果显示:11根管路均发生塑性变形,如下图3所示。管路发生变形后,中心集成块与管路发生接触,对管路产生剪切应力。
1根泡沫管能承受的扭矩为通过下式计算:
(9)
式(9)中各符号意义如下:
Rg—泡沫管与刀盘连接处到刀盘轴线的距离,m;
Fg—泡沫管能承受的最大剪切力;
τ—泡沫管材料剪切强度,MPa;
Ag—泡沫管材料截面积,mm²。
通过计算,Tg为37 kN×m,中心回转组件旋转阻力矩Tz值约为50 kN×m,可见2根泡沫管即可以将中心回转组件带动,使其跟随刀盘旋转。
(3) 处理措施
根据上述对故障现象的分析,确定了故障产生的原因及过程。由于盾构机早已脱离加固区进入富水地层,已不具备开仓处理的条件。经过分析,认为在中心回转密封未失效、并且在采取适当措施防止中心回转组件继续后移的情况下,可以继续施工,待盾构机到达接收井后再对盾构机中心回转部位进行修复。
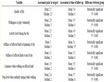
Table 1. Pipe between Cutter and Central integration block
表1. 中心集成块与刀盘连接的管路

Figure 3. Displacement nephogram of Pipe between Cutter and Central integration block
图3. 中心集成块及刀盘连接管路受扭力位移云图
为防止中心回转组件继续后移,制作了一套工装,并通过该工装将已经后移了70 mm的中心回转组件往前顶推,并阻止中心回转组件后移。之后,盾构机继续施工,最终顺利到达接收井。
3.2.4. 故障发生过程与总结
通过上述3.2.3的分析可知,故障发生的真正原因与3.2.1和3.2.2的分析存在本质的区别。一系列故障发生的真实过程可还原为:盾构机始发过加固层时,由于未按照《操作说明书》的要求在鱼尾刀前方的加固层上预先开挖出一个缺口,在刀盘面接触到掌子面之前鱼尾刀先接触到了掌子面,盾构机前进的推力完全作用在了鱼尾刀上,使鱼尾刀所受的轴向力超过了设计值,中心集成块与刀盘连接螺钉被拉断。此时由于中心集成块与刀盘之间有11根材料(20钢)延展性较好的连接管路未被全部拉断,仍在带动中心回转组件跟随刀盘一起旋转。然后,鱼尾刀与中心回转组件整体后移,当后移距离达到5 mm时,中心轴法兰与驱动部中心封头接触并在两者之间产生挤压,导致中心轴法兰旋转阻力矩急剧增大,超过了C-C截面连接螺钉和连接销的设计值,导致了C-C截面连接螺钉和连接销断裂。而在对首次故障C-C截面连接螺钉和连接销断裂故障分析时,由于未掌握“中心轴法兰与切口环封头之间的间隙比图纸小了3 mm”这一关键信息,误认为C-C截面连接螺钉和连接销断裂故障是因为连接销设计安全系数偏小和渣土未有效改良而导致,而未找到故障发生的根本原因。虽然在处理故障时采用增加焊缝的方式改善了C-C截面的受力情况,避免了C-C截面连接螺钉和连接销断裂故障的重复发生,但未从根本上解决问题。在后续施工过程中,中心轴法兰与驱动部中心封头长期的挤压磨损,导致中心轴法兰或驱动部中心封头发生损坏,然后中心回转组件继续后移,直至后移距离达70 mm时被发现。在采取顶固工装防止中心回转组件继续后移后,盾构机继续施工,最终到达接收井。
盾构机到达接收井后,检查中心回转组件和鱼尾刀,发现中心轴法兰与驱动部中心封头均发生了不同程度的损坏、中心集成块与刀盘连接螺钉断裂,仅通过钢管连接。上述现象均与3.2.3和3.2.4的分析一致。
4. 优化与改进措施
通过上述分析,故障发生的根本原因为:盾构机始发过加固层时未按照要求在鱼尾刀前方的加固层上预先开挖出一个缺口,导致使鱼尾刀所受的轴向力超过了设计值,使中心集成块与刀盘连接螺钉被拉断。
4.1. 施工过程改进措施
在盾构机始发过加固层前,施工方必须严格按照《操作说明书》的要求:在鱼尾刀前方的加固层上预先开挖出一个坑口、且施工中推进速度小于10 mm/min,从而保证通过鱼尾刀传递到中心集成块上的轴向力在设计许可范围内,避免通过鱼尾刀传递到中心集成块上的轴向力过大。
4.2. 鱼尾刀结构优化与改进
将鱼尾刀直接焊接到刀盘面板上,不与中心集成块发生接触相连。使鱼尾刀所受轴向力传递在刀盘上,而不再通过鱼尾刀安装座传递到中心集成块上。即使鱼尾刀所受的轴向力超过了设计值,也不会导致严重故障发生。
5. 结语
(1) 提出了中心回转组件的故障分析方法。
(2) 提出了中心回转组件在渣土中受力计算方法。
(3) 提出了鱼尾刀结构优化设计及改进措施。