1. 引言
C/C复合材料因其具有密度低、热膨胀系数低、摩擦系数稳定、耐烧蚀等优良性能,特别是随温度升高其力学性能不降反升的特性,是理想的航天航空高温结构材料 [1] 。但是在
450 ℃
以上的氧化气氛中C/C复合材料会迅速氧化,物理及力学性能急剧下降,使其在高温有氧气氛中的应用受到一定的限制 [2] [3] 。因此,利用各种涂层技术,在C/C复合材料表面制备高温陶瓷涂层进行氧化保护是切实有效解决C/C复合材料的高温氧化问题的方法。
目前,常见的高温抗氧化涂层有各种硅化物、硼化物、碳化物或氧化物等,但由于这些涂层膨胀系数较大,制备温度较高,在冷却过程中涂层会产生裂纹;另外,在经历多次热循环后,涂层同样会因热膨胀差异问题而产生裂纹,进而导致涂层失效。SiC具有良好的抗氧化性能,与C/C复合材料有较好的化学物理相容性和相近的线膨胀系数(4.3~5.4 × 10−6/℃),是C/C复合材料和外层涂层之间理想的过渡涂层材料 [4] [5] [6] 。
目前,SiC涂层的制备技术常见的有包埋法、化学气相沉积法、刷涂法 [6] [7] 等,包埋法是常见的C/C复合材料涂层制备方法,利用这种方法制备的涂层与基体有较强的界面结合力,但其制备温度较高,一般需要在1800℃~2100℃保温2~4 h [8] ;化学气相沉积法可以在较低的温度(1200℃左右)实现涂层的制备,但制备时间往往需要20 h左右 [9] ;刷涂法由于需要多次涂刷干燥,需要的制备周期更长 [10] 。放电等离子体烧结技术(Spark Plasma Sintering, SPS)是新近发展起来的一种致密化技术,已成功用于梯度功能材料、金属基复合材料、纳米材料以及多孔材料等多种材料的制备。相比于热压反应烧结,SPS技术具有以下无可比拟的优点 [11] :① 烧结温度低,比热压烧结低200℃~300℃;② 烧结时间短,只需3~10 min,而热压烧结需要120~300 min;③ 烧结机理特殊,赋予材料新的结构与性能;④ 烧结体密度高,晶粒细小,是一种近净成形技术;⑤ 单件能耗低。因此,利用SPS技术制备的SiC涂层在理论上应比热压反应烧结技术制备的涂层更具有优越的结构和性能,但目前采用SPS制备C/C复合材料涂层的研究还很少见报道。
本研究采用放电等离子体烧结技术,进行C/C复合材料表面SiC涂层的制备。SPS具有特殊的烧结机理,有望制得无裂纹,与基体结合紧密,烧结温度低的SiC涂层。
2. 实验过程
C/C复合材料试样为湖南省江南石墨制品有限公司产品,密度1.75 g/cm3,尺寸为φ20 mm × 6 mm。C/C复合材料基体先用400#砂纸,再用600#砂纸打磨,之后用无水酒精进行超声波清洗。
涂层组成材料Si粉和石墨粉,考虑到Si的高温挥发性,Si/C摩尔比取1.11,另还加入了5% Al2O3烧结助剂,所有样品粒度均为300目,均为中国试剂网产品。将涂层材料在烘箱中150℃温度条件下保温1 h,然后入球磨机球磨24 h、过筛、装模,装模如图1所示。然后放入SPS-3.20MK-Ⅳ型放电等离子体烧结机上进行烧结,烧结温度1100℃~1400℃,保温时间1 min,压力为30 MPa,真空度小于6 × 10−3 Pa。
将涂覆后的C/C复合材料分别进行XRD物相鉴定和SEM表面和断面形貌分析,另外,为表征涂层的抗氧化效果,最后将涂覆的C/C复合材料在1400℃空气气氛下的高温炉中进行了抗氧化性能实验。
3. 实验结果及讨论
在SPS烧结过程中发现:当烧结温度为1100℃时,SiC涂层与C/C复合材料基体不结合,处于分离状态,说明SiC涂层与基体没有产生化学键结合;烧结温度高于1400℃时,由于Si粉气化挥发,在冷却的过程中会在模具隙缝中凝固,导致无法脱模,因此,本研究的烧结温度范围确定为1100℃~1400℃。
图2为不同烧结温度下制得的SiC涂层的表面形貌和XRD图谱。由图2(a)可知,烧结温度为1100℃时,涂层组成为Si和C,没有SiC生成,意味着在此烧结温度下Si与C不能发生反应,故涂层与基体也不会产生任何化学键合作用,因此,涂层与基体的几乎没有结合强度;由图2(b)可见,烧结温度1200℃时,涂层主要由b-SiC和Al2O3,说明Si与C已发生化学反应并完全生成了SiC,但此时的SiC晶粒尺寸不均匀,在5 mm以下;烧结温度升高至1300℃,涂层组分仍然是b-SiC和Al2O3,但由于Si与C之间的反应充分进行,生成的SiC晶粒大小均齐,颗粒进一步长大到5~10 mm左右,镀层内的SiC晶粒堆积紧密,且没有裂纹出现,是理想的致密SiC涂层;当烧结温度继续升高至1400℃时,由于Si粉气化挥发,在冷却的过程中在镀层表面凝固下来,因此,镀层组分除了b-SiC和Al2O3,还有Si和C出现。综上分析可知,1300℃是理想的烧结温度,在该温度下可以制得致密的、表面无裂纹的SiC涂层。
图3为1300℃制备的SiC涂层与C/C复合材料基体界面的线成分分析,由图可见,涂层与C/C复合材料基体之间存在宽约5 mm左右的过渡区域,在该过渡区域内的主要元素是C和Si,从涂层至基体,基体的成分C逐渐增多,涂层的主要成分Si逐渐减少,并且向C/C复合材料基体产生了扩散,说明SiC涂层与C/C复合材料基体界面结合为化学冶金结合,而不是简单的机械结合,故生成的SiC膜层与基体结合紧密。
为研究镀覆基体的抗氧化性能,将1300℃制备的镀覆SiC的C/C复合材料放入高温炉中于1400℃的大气气氛条件下进行抗氧化性能实验,结果见图4。由图可见,未镀覆C/C复合材料在高温大气气氛下发生了严重氧化,质量百分数急剧下降;通过SPS技术,镀覆一层SiC后,基体的抗氧化性能得到大幅度的提高,在1400℃氧化180 min后的质量损失为10%左右,氧化300 min后的质量损失为25%左右。
4. 结论
1) 利用放电等离子体烧结技术,在1200℃~1300℃范围内均可制得主要成分为b-SiC的涂层。
2) 在1300℃保温烧结1 min,能得到无裂纹,晶粒大小均齐、与基体结合紧密的b-SiC涂层。
3) 镀覆SiC涂层的C/C复合材料的抗氧化性能得到大幅度的提高。
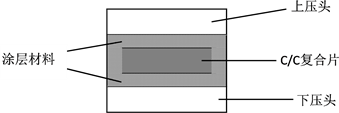
Figure 1. Schematic diagram of SPS for SiC coated C/C composites
图1. C/C复合材料Si涂层的SPS烧结示意图
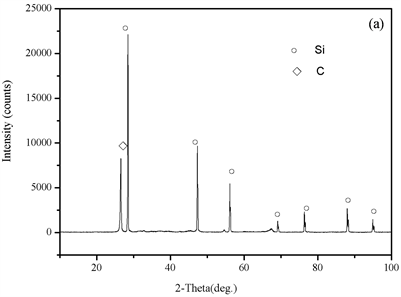
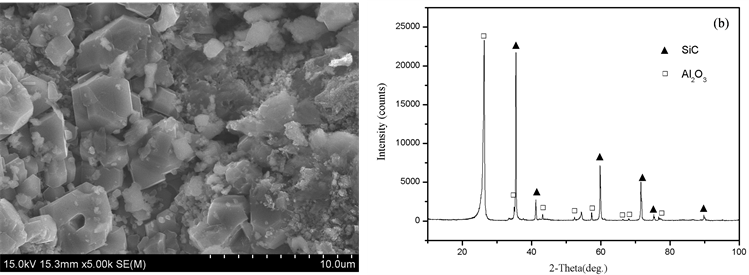
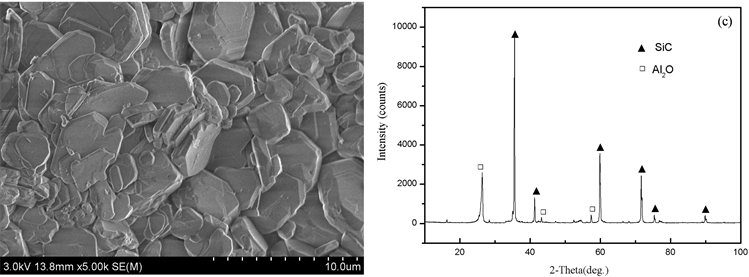
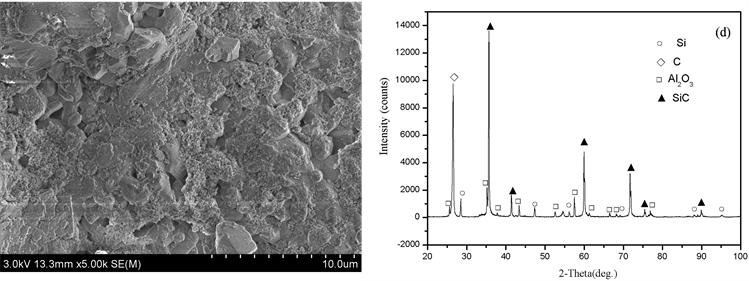
Figure 2. SEM images and XRD patterns of SiC bonding layer prepared at: (a) 1100˚C; (b) 1200˚C; (c) 1300˚C; (d) 1400˚C
图2. 不同烧结温度下的SiC涂层表面扫描图片和XRD图谱:(a)
1100 ℃ ;
(b)
1200 ℃ ;
(c)
1300 ℃
;(d)
1400 ℃
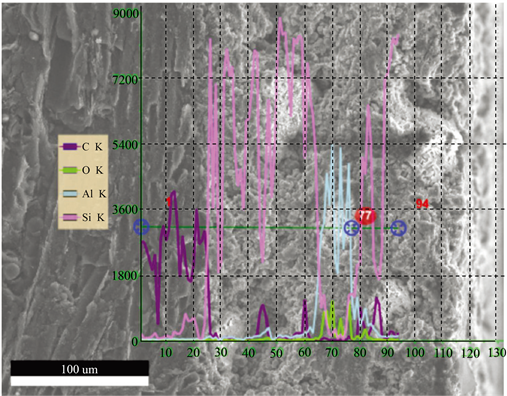
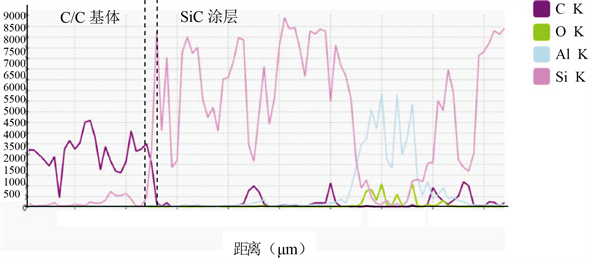
Figure 3. Linear scanning analysis of the interface of SiC coated C/C composite
图3. SiC涂层与C/C复合材料基体界面线扫描分析
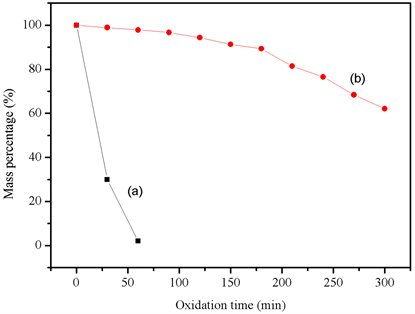
Figure 4. Oxidation curves of C/C composite at 1400˚C in air: (a) uncoated; (b) SiC coated
图4. 1400℃空气气氛下C/C复合材料的氧化曲线:(a) 未镀基体;(b) 镀覆基体
基金项目
中国科学院特种无机涂层重点实验室开放课题资助项目(KLICM-2014-06)。
河北省教育厅高等学校科技计划重点项目(ZD2017073)。