1. 引言
液压驱动是高端、重型装备的主要动力型式,主要通过比例阀(或伺服阀)进行流量调节来实现加载控制。传统电液比例阀响应速度快、控制精确,是液压系统的主要控制部件,然而其结构复杂、价格高、易堵塞、控制困难,限制了其应用范围,在液压试验机、硫化机等工作环境较差、成本要求较高的液驱装备应用中存在不适应性。阮健 [1] [2] [3] 等人提出了一种有高稳定性和较快响应速度的2D电液数字换向阀,并通过建模与Matlab仿真研究了该阀的关键结构和动态特性,但是该阀仍存在精度要求高,不易加工,仅具备导控阀功能的缺陷。李军霞 [4] 等人利用功率键合图理论和Matlab对电液比例溢流阀调压系统的动态特性进行了仿真分析,并采用Fluent对其内部流场进行了数值仿真,得到了阀内流体的压力和速度变化情况。权龙 [5] [6] 等人提出了一种具有较高的闭环响应带宽和能量效率的新型先导控制比例方向阀,在时域和频域中对阀的动态阶跃响应和频率响应特性进行分析,对比仿真了不同阀芯面积比和节流槽面积增益对动态特性的影响。魏超 [7] 等人介绍了一种具有较快开关响应速度和较强通流能力的三级高速脉冲阀结构并进行了仿真和实验,结果发现高速脉冲阀的先导阀和次阀先后控制主阀芯动作的模式的特点,高速脉冲阀开阀瞬间阀芯开度大,响应时间在10 ms以内。
多个学者针对传统电液比例阀提出了优化,但仍存在加工困难,控制困难以及响应不够快等问题。故本文在分析比例阀控、以及数字阀结构及其流量控制特性的基础上,提出了一种螺纹导向型带初始位置感应的三段式数字阀结构,其具有较高的比例控制精度和良好的动态响应特性,同时建立其流量控制模型并进行了试验验证。
2. 三段式数字阀结构原理
数字阀的结构如图1所示,包括齿轮箱1、阀体2、螺纹箱3、阀芯4、步进电机11及传动机构。齿轮箱、阀体、螺纹箱采用三段式连接而成,阀芯位于阀体内部的阀腔内;传动机构由主动齿轮9和从动齿轮8组成,步进电机的输出轴与主动齿轮相接,主动齿轮与从动齿轮啮合,组成一对齿轮副,从动齿轮与阀芯一端相接,阀芯另一端制成螺杆,螺杆与螺纹箱上的内螺纹相配合组成一对螺旋副,阀芯的左
1.齿轮箱;2.阀体;3.螺纹箱;4.阀芯;5.箱盖;6.齿轮箱定位销;7.从动轮定位销;8.从动齿轮;9.主动齿轮;10.限位板;11.步进电机
Figure 1. Principle diagram of digital valve structure
图1. 数字阀结构原理图
端通过螺旋副将步进电机的旋转运动转化为直线运动。
具体工作原理:当数字阀驱动电路发出脉冲信号后,步进电机转动对应角度,在齿轮机构的带动下,驱动阀芯转动,由于阀芯左侧螺纹机构的导向作用,阀芯每转动一圈的同时横移一个螺距,从而控制阀芯开度,起到换向和节流的作用。齿轮箱顶端装有限位板10,限位板上配备了光电传感器,在控制器上电启动时,传感器检测阀芯是否处于零位,如果不处于零位,则输出控制信号给步进电机,便于控制阀芯回到零位,以消除累积误差,提高阀芯位置的重复精度。
3. 数字阀流量控制模型及仿真分析
数字阀的输入信号为步进电机的控制脉冲,输出为阀的出口流量,为此建立控制系统各环节的模型如下:
3.1. 步进电机数学模型
步进电机选用两相混合式电机,在不计定子极间和端部的漏磁、不计永磁体回路的漏磁、忽略磁滞和涡流的影响、忽略饱和的影响、忽略定子线圈自感的谐波分量。
不失步时,步进电机每接受一个脉冲信号转过一个步距角,即:
,而转子实际转过的角度
围绕一个新的平衡点振荡,根据小振荡理论,可推导出传递函数为:
(1)
两相混合式步进电机的电压平衡方程为:
(2)
(3)
式中:R:绕组电阻;
:电感系数;
:电枢绕组的反电动势系数;
:电动机的齿数;
:电动机转子角位移;
:电机转速;
、
:绕组A、B的电流;
、
:绕组A、B的电压。
步进电动机的力矩平衡方程为:
(4)
式中:Te:电磁转矩;J:转动惯量;B:粘滞摩擦系数;TL:负载转矩。
按单相励磁方式,由式4可得步进电机运动方程为 [8] :
(5)
设
,
,转子达到平衡位置。此时仅有一相电源接通,无其他电流通路,振荡过程中
不变,则增量运动方程为:
(6)
因 很小,方程线性化为:
(7)
对式(7)进行拉氏变换,将初值0代入可得:
(8)
则步进电机的模型为:
(9)
3.2. 传动机构模型
数字阀传动机构由齿轮副和螺纹传动副构成(图2),推导出所需的传递函数为:
(10)
式中:x:阀芯位移。
对于数字阀而言,螺杆螺母机构的功能是将旋转运动转变成直线运动,忽略齿轮啮合齿隙、螺纹间隙则:
(11)
式中:
:主动轮齿数;
:从动轮齿数;P:螺距。
3.3. 换向阀的数学模型
数字阀阀芯位移和流经数字阀的流量的数学模型为:
(12)
(13)
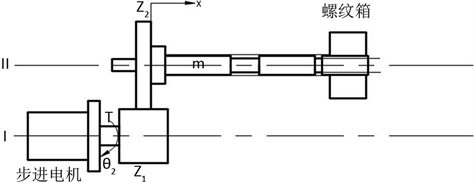
Figure 2. Principle diagram of digital valve transmission structure
图2. 数字阀传动原理图
式中
:流量系数;W:面积梯度;
:数字阀出油口压力;
:数字阀进油口压力;
:液压的密度。
因此,数字阀流量控制系统传递函数为:
(14)
3.4. 流量控制特性仿真结果分析
将式(14)化成二阶系统的标准形式:
(15)
由上式可知:二阶系统的阻尼比
二阶系统的固有频率
二阶系统的增益
通过研究二阶系统性能指标来研究步进电机不同结构参数、面积梯度变化、传动比变化以及负载压力变化对流量控制特性的影响。
3.5. 步进电机参数对流量控制特性的影响
步进电机是数字阀最重要的组成部分之一,其内部系数影响数字阀的流量控制特性,在本模型中步进电机的内部参数包括电机转动惯量J、电机阻尼系数B、电感
、相电流
。
图3(a)为了获得很好的流量控制特性,则需保证超调量小、响应时间短、振荡次数少。由于超调量只与二阶系统的阻尼比有关,阻尼比越大超调越小,即B越大超调越小,一般选择在0.4~0.8之间。然后调整固有频率
。当阻尼比一定时固有频率越大,系统响应的快速性越好。
从图3(a)~图3(d)仿真图形中不难看出,在0.3s时间后,无论步进电机参数取何值,流量都趋于稳定,即响应时间在0.3s左右,当电机转动惯量越小或电机阻尼系数越大时,其超调量越小,响应速度越快;电机相电流或电感越小时,超调量越小,但其响应时间长。因此合理选用电机结构参数可以改善流量的控制特性。
3.6. 结构参数与压力对流量控制特性的影响
图4(a)所设计的新型数字阀为孔口全周边的圆周滑阀,对于孔口为全周边的圆周滑阀,
,其中d为阀芯直径。可以改变阀芯直径来改变面积梯度间接地改变数字阀的流量控制特性,阀芯直径分别取6 mm,8 mm,10 mm进行流量控制特性仿真分析。从图中可以看出面积梯度越大,输出的流量越大。
(a) 电机转动惯量J
(b) 电机粘性系数B
(c) 相电流ia
(d) 电感Ld
Figure 3. Influence of different stepper motor parameters on flow control characteristics
图3. 步进电机参数对对流量控制特性的影响
(a) 面积梯度 w=πd
(b) 齿轮传动比i
(c) 负载压力PC
Figure 4. Influence of different structural parameters and pressure on flow control characteristics
图4. 结构参数与压力对对流量控制特性的影响
图4(b)研究不同传动比对流量特性的影响,分别取传动比为0.5、0.6、0.7。从图中可以看出传动比越大,输出的流量越大。
图4(c)负载压力分别取5 MPa、15 MPa、25 MPa,研究不同负载压力对流量控制特性的影响,从图中可以看出负载压力越大,输出的流量越小。
从图4(a)~图4(d)仿真图形中不难看出,在0.3 s时间后,无论结构参数取何值,流量都趋于稳定,即响应时间在0.3 s左右。
4. 误差分析
4.1. 步进电机定位精度对数字阀精度的影响
步进电机转动1000步,换向阀阀芯轴向位移4 mm。步进电机多次转动时到达同一位置的误差小于±0.5步,换算为轴向位移小于0.002 mm。通过计算,可以得到输出流量为130.33 L/min,误差为(130.33 −130.07)/130.07 = 0.20%。
4.2. 间隙对数字阀精度的影响
根据图纸尺寸,步进电机的输出轴与平键之间的最大间隙为0.039 mm,齿轮传动的齿隙为0.1 mm,螺纹副的回程间隙为0.03 mm。将这些间隙折合成步进电机转动的角度,计算可得α = 0.33˚,换算成换向阀阀芯轴向位移,为0.031 mm。经仿真,数字阀的输出流量可以达到134.10 L/min,最大相对误差为 3.1%。
5. 结论
本文提出了一种螺纹导向型带初始位置感应的三段式数字阀,建立了数字阀数学模型并进行仿真,结果表明数字阀具有良好的动态响应特性,响应时间在0.3 s左右。此外,分析了数字阀电机内部参数、结构参数以及压力对流量特性的影响,结果发现电机转动惯量越小或电机阻尼系数越大时,其流量的阶跃响应超调量越小,响应速度越快;电机相电流或电感越小时,其流量的阶跃响应超调量越小,但其响应时间长,当阀芯半径与传动比增大时,其流经阀的流量也同比例的增大,当阀口负载压力增大时,其流经阀的流量以开方的趋势减少。
基金项目
本论文有以下项目的支持:国家自然科学基金[51205368],浙江省自然科学基金[LY17E050001]和2017年地方高校国家级大学生创新创业训练计划项目[201710345035]。
NOTES
*通讯作者。