1. 引言
近几年,我国轨道交通装备制造业进入了高速成长期。轨道交通装备制造企业要想在市场中获得竞争优势,缩短物流时间、降低物流成本是很关键的因素。车间设备布局对生产过程中物料的流动是否流畅,是否能保证生产的顺利进行都起着至关重要的作用。随着生产产品的种类增多和产量增加,轨道交通装备制造企业出现了车间布局不合理等相关问题,影响了企业的生产效益。
1961年,美国缪瑟提出了系统布置设计(SLP)理论,该理论是通过分析设施之间的物流量以及非物流关系来对设施进行布局 [1] 。SLP方法流传很广,我国在1983年引进SLP之后,很多学者将SLP方法广泛运用在了多种情况的设施规划中。张扬 [2] 应用SLP方法分析现有车间布局存在的问题,并根据分析结果提出改善方案。通过Flexsim仿真技术对提出的改善方案进行定量分析,对仿真结果进行分析比较,从而得到最终改善方案,进而指导车间布局调整。王鑫、胡春禄 [3] 运用SLP方法对A医院的门诊部进行设施布局优化设计,设计出了比原有的布局更科学、合理的布局,提高了门诊部就诊效率与患者满意度。刘志海、张丹丹 [4] 对传统的系统布置设计方法进行改进,以顾客流量为主要物流因素,将动线分析与反馈加入布局规划流程,对超市的布局进行优化。有效的了提高超市运作效率。因此,系统布置设计理论可以运用在多种场景。
本文利用SLP理论,对A公司的生产车间内的设备进行重新布局,使车间内物料的运输更加流畅,提高生产效率。
2. A公司生产物流现状分析
A公司是一家为轨道车辆生产相关设备并负责维修的制造企业。该企业生产的产品有三大类共几十种,生产方式主要以装配为主,产品的零件一部分通过外购,一部分自己生产,因此,该车间是集加工和装配于一体的车间。
2.1. A公司当前布局情况
根据A公司生产车间的当前布局情况,并且以维修产品的物料流动路线为例,当前的布局如图1所示。
2.2. A公司生产车间设备布局存在的问题
经过分析后发现,由于车间初建时没有充分考虑与别的作业单元之间的联系,出现了在生产活动中物料流动路线迂回交叉的现象,造成物料搬运距离长。根据当前的生产要求,维修产品的需求增加,需要增加维修相关的配套设备。同时,车间缺少质检区域,因此需要增加相应的功能区。其余的功能区根据生产需要也要进行调整。综上所述,需要将车间的设备进行重新布局,对生产物流的现状进行改善。
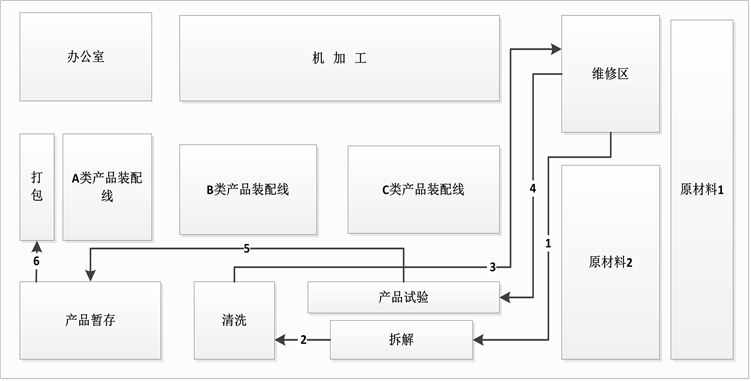
Figure 1. Original layout of Company A workshop
图1. A公司车间原布局
3. SLP理论在A公司车间布局的应用
3.1. 基本要素分析
在进行布局设计之前,根据SLP理论先对车间的基本要素进行分析。
1) 产品P:A企业主要生产维修A、B、C三类产品,所以以A、B、C三类产品作为研究对象。
2) 产量Q:以A、B、C三类产品一个月的产量作为数据依据。
3) 生产路线R:车间生产新产品的流程为:机加工,组装,测试,质检,打包。维修产品的生产流程为:入厂检测,拆解,清洗,维修,组装,测试,打包。
4) 辅助服务部门S:车间办公室。
3.2. 作业单元之间物流与非物流关系分析
根据A公司生产需求,需要增加一个产品维修线,质检区,为了给新增加的功能区提供足够的空间,将原材料2区移出车间外。因此,将整个车间划分为以下14个作业单元:办公区、机加工区、A类产品装配区、B类产品装配区、C类产品装配区、产品试验区、拆解区、清洗区、维修区1、维修区2、原材料存储区、质检区、打包区、产品暂存区。
1) 物流关系分析。根据产品的生产流程,物料运输路线以及运输量等信息,得出各作业单元之间的物流强度,依据物流路线比例和承担的物流量的比例将各物流强度划分为5个等级,从高到低分别为A、E、I、O、U。物流强度等级判断标准如表1所示。根据作业单元间的物流强度绘制出物流相关图。各作业单元之间的物流强度如表2所示。物流相关图如图2所示。
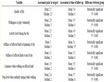
Table 1. Logistics strength level judgment standard
表1. 物流强度等级判断标准
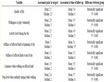
Table 2. Work unit versus logistics intensity
表2. 作业单元对物流强度
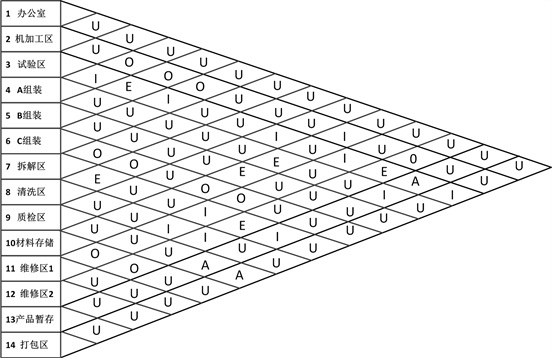
Figure 2. Work unit logistics related diagram
图2. 作业单元物流相关图
2) 非物流关系分析。判断车间设备布局是否合理,不止要考虑各作业单位之间的物流强度,还要考虑各作业单位之间的特殊要求,比如生产流程是否顺畅,人员的沟通是否方便等非物流因素。对各作业单元之间的非物流因素进行评价,得出作业单位接近程度,并按照从高到低的顺序划分为A、E、I、O、U、X这6个等级,X表示两个作业单元尽量不能靠近。根据实际情况,依据① 工作的连续性;② 方便监督管理;③ 工作噪音;④ 物品搬运安全;⑤ 人员联系五个非物流相关性因素对所有单元之间的接近程度进行评价。绘制非物流相关图如图3所示。
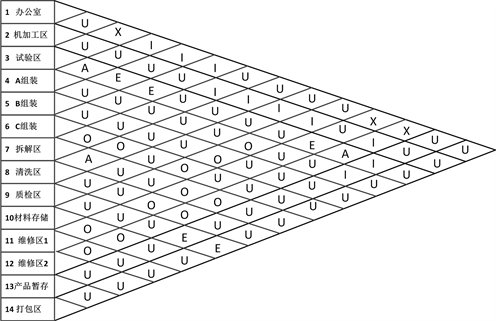
Figure 3. Work unit non-logistics related diagram
图3. 作业单元非物流相关图
3) 综合关系分析。在布局时要将物流与非物流关系综合考虑。根据A公司的生产情况,需要人员之间的沟通以及信息的传递,但是各作业单位之间的物流关系在生产中要更重要。因此在分析作业单位之间的综合关系时,确定物流关系与非物流关系之间的比值为2:1比较合理。各等级代表分值A:4,E:3,I:2,O:1,U:0,X:−1。根据得出的综合关系分值绘制综合关系相关图如图4所示。
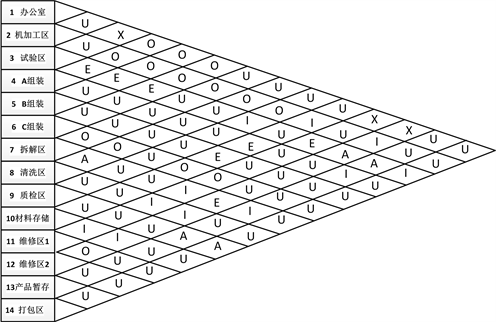
Figure 4. Work unit comprehensive correlation diagram
图4. 作业单元综合相关图
3.3. 绘制作业单位位置相关图
根据得出的各作业单元之间的综合物流关系,按照各作业单位综合关系从高到低的顺序依次插入,绘制作业单位位置相关图如图5所示。
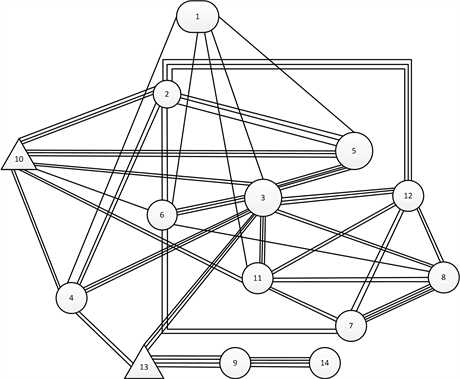
Figure 5. Work unit position correlation diagram
图5. 作业单元位置相关图
4. 方案选择
作业单元位置相关图是一个原始布置图,根据车间内的条件以及成本物料搬运方式等因素进行修正,做出以下两个方案,如图6、图7所示。
为了从候选的两个方案里选出最适合的方案,需要从多方面对方案进行分析,我们采用加权因素分析法,选择影响车间设备布局的相关因素并赋予不同的权重(1~10),通过公司的专家们和负责人对两个方案进行评价,评价得分从高到低分为A、E、I、O、U五个等级,等级对应一定的分数(A-4、E-3、I-2、O-1、U-0),将各因素的得分与权重相乘并相加所得的和为各方案最后的得分。最后将根据车间的情况,选择以下五个因素进行评分。
1) 生产流程顺畅度
2) 物料搬运效率
3) 空间利用率
4) 工作环境安全及舒适
5) 设备的特殊要求
通过专家和负责人打分,两种方案的评价结果如表3所示。
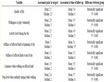
Table 3. Weighted factor analysis result
表3. 加权因素分析结果
根据评价的结果,方案一的得分高于方案二,方案一中设备间的通道较宽有利于叉车等搬运工具作业,也有利于车间出入口的设置,与车间本身的条件更加适合,因此选择方案一作为车间新的布局是合理的。新的布局将清洗和拆解作业区与维修区相邻,使原来物料搬运路线交叉迂回的现象得到改善,同时将各装配线放置在检测室周围,减少搬运距离,降低搬运成本。
5. 总结
公司为了适应市场的变化,要不断的调整产品的品种和产量来满足市场的需求。当生产车间原有的设备布置方案导致生产物流不顺畅或者不能满足生产需求时,为了提高生产效率,物流效率、空间利用率等指标。就需要对生产车间设备的布局进行重新设计。
本文通过用SLP方法,对A公司生产车间进行分析,设计出可行方案,并用因素分析法对方案进行评价,从中选择出合适的布局方案。新的布局添加了新的功能区,满足了车间的需求,同时也让车间内设备的布局更符合生产流程,让原布局中物料搬运路线交叉迂回的现象得到了改善,使得生产物流更加顺畅,物流效率提高,降低物流成本。同时,作业环境也得到了改善。