1. 引言
作为重要旋转类零件,通过齿轮副间的啮合传递动力,齿轮在当今的机械设备中应用广泛;啮合效率越高,机械设备的工作效率越高,反之亦然。汽车变速器作为最精密最复杂的综合机械产品之一,其效率的高低与齿轮的性能具有较大关系。在经典齿轮设计方法中,齿轮的润滑特性,尤其是弹流润滑,并不在考虑范围之内,但实际上其对齿轮的工作特性有着重要的影响,润滑特性越好,齿轮啮合效率越高。因此,研究弹流润滑下齿轮的润滑特性,计算齿轮啮合效率是目前高效率齿轮设计的重要研究内容之一。
在弹流润滑和齿轮啮合效率研究方面,国内外学者做了大量的研究工作。周哲波 [1] 假设接触齿面间载荷均等,提出了计算渐开线直齿轮传递损失的计算方法。Li和Kahraman [2] 建立了直齿轮的弹流润滑模型,研究了当润滑介质为非牛顿流体、齿廓存在修形、齿面存在粗糙度的情况下的弹流润滑特性,并与未修形、牛顿流体润滑介质状况下的润滑特性进行了对比。王文中、操鸿、胡纪滨 [3] 将斜齿圆柱齿轮啮合的齿面接触等效为有限长线接触的弹流润滑问题,建立了渐开线斜齿轮啮合的弹流润滑计算模型。Li等 [2] 和Kolivand等 [4] 提出了适合于直齿轮和斜齿轮的混合弹流润滑模型,可用于计算滑动摩擦损失的摩擦系数。王斌和陈辛波 [5] 结合弹流润滑和边界润滑两种摩擦系数,建立了以瞬时压力角为变量的直齿轮啮合效率分析模型。畅通和王优强 [6] 建立渐开线直齿圆柱齿轮线接触混合润滑模型,求解其热瞬态混合润滑问题。
本文以渐开线直齿轮为研究对象,首先建立牛顿流体弹流润滑模型,采用多重网格法进行数值求解;然后,将直齿轮啮合效率计算理论与弹流润滑模型结合,研究齿轮啮合效率在不同输入转矩、转速以及不同压力角下的特征及其变化规律,为设计高效率齿轮提供更为有效的参考依据。
2. 渐开线直齿轮瞬态弹流润滑模型
2.1. 直齿轮啮合模型
图1为一对直齿啮合的几何模型,其中,φ为压力角,za为小齿轮的齿数,zb为大齿轮的齿数;ωa为小齿轮的转速,ωb为大齿轮的转速;P为节点,NaNb为理想的啮合线,K为某刻齿轮啮合位置,A为齿轮进入啮合的位置;Oa为小齿轮的几何圆心,Ob为大齿轮的几何圆心;坐标轴x为齿廓渐开线的切向方向,y为啮合线作用的方向。定义线段p = AK,s = PK,约定s在P点左侧为负值,s在P点右侧为正值。啮合过程中,所有的啮合点都在啮合线NaNb上,因此直齿轮正确啮合的条件为啮合线上各轮齿同时啮合。
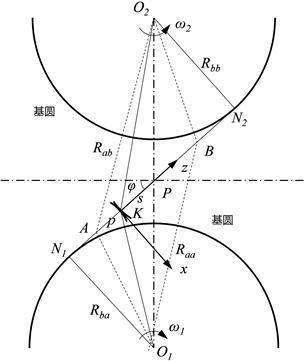
Figure 1. Geometric contact model of spur gear
图1. 直齿轮接触几何模型
根据几何关系,可得接触点K处的曲率半径为:
(1)
式中:Ra——齿轮的曲率半径;Rb——大齿轮的曲率半径;
Rba——小齿轮的基圆半径;Rbb——大齿轮的基圆半径。
进而可以得到小齿轮和大齿轮齿面沿x方向的速度为(沿y方向速度为0):
(2)
滚动速度为:
(3)
滑动速度为:
(4)
上述公式可以描述直齿轮的啮合过程,为了验证上述模型,选取一对在实际工程中有所应用的渐开线直齿轮副进行分析,其基本参数如表1所示。
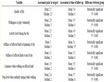
Table 1. Basic parameters of spur gears
表1. 直齿轮的基本参数
将齿轮啮合的时间计算域按照等步长划分,根据上述模型可得到如图2和图3所示的啮合过程中的曲率半径与相关速度。由图2可以看出,主动齿轮啮合点处曲率半径逐渐增大,从动齿轮啮合点处曲率半径逐渐减小,综合曲率半径以节点位置为分界点,呈先增大后减小的趋势。由图3可以看出,主动齿轮啮合点处瞬时速度逐渐增大;从动齿轮啮合点处速度逐渐减小;啮合点处滑动速度以节点为分界点先减小后增大,节点处滑动速度为0;啮合点处滚动速度逐渐增大。
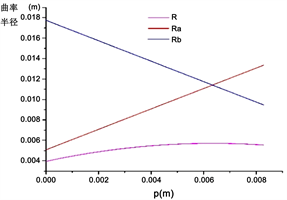
Figure 2. Curvature radius of spur gear in meshing process
图2. 直齿轮啮合过程中的曲率半径
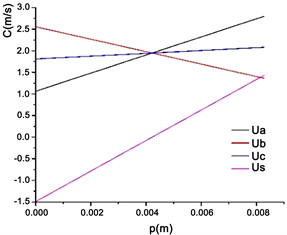
Figure 3. Relevant speed parameters in spur gear meshing process
图3. 直齿轮啮合过程中相关速度参数
2.2. 瞬态润滑控制方程
为揭示油膜压力及油膜厚度的分布规律,直齿轮啮合接触弹流润滑模型的核心是建立Reynolds方程与膜厚方程并进行数值求解。相对于稳态弹流润滑模型而言,瞬态弹流润滑模型的控制方程基本相同,只是采用与时间相关的时变参数。
设润滑介质为牛顿流体,则关于油膜压力的Reynolds方程的无量纲形式为:
(5)
式中:
p——油膜压力
t——时间
b——一半接触面长度
ρ——流体密度
η——流体粘度
uep——节点处的滚动速度
R0——节点处等效曲率半径
膜厚方程的无量纲形式为:
(6)
式中:
CR(t)——综合曲率半径
Xin——润滑介质的入口坐标
Xout——润滑介质的出口坐标
载荷方程的无量纲形式为:
(7)
式中:
w0——节点处的单位载荷
式(5)-(7)构成了基本的直齿轮弹流润滑控制方程组。为了求解,还需要给定边界条件:
显然,上述方程组的非线性较强,需要首先在计算域上进行离散,然后采用合适的数值方法对离散方程组进行求解。本文采用计算效率较高的多重网格中的全近似格式(FAS, Full Approximation Scheme)进行直齿轮表面的压力分布和油膜厚度的数值求解。
2.3. 润滑特性分析
以表1所列的齿轮副为应用对象,定义T = 100 Nm,E1 = E 2 = 2.06 × 1011 Pa,η0 = 0.08 Pa∙s,Z = 0.68。考虑到单双齿啮合区域的变化,动态载荷如图4所示。
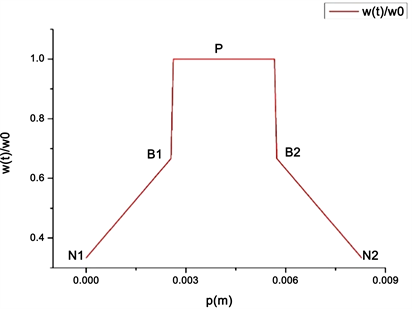
Figure 4. Dimensionless load distribution map
图4. 无量纲载荷分布图
图5和图6为计算得到的直齿轮啮合过程中啮合点处的油膜厚度与齿面的压力分布。图5为计算得到的齿轮啮合过程中的油膜压力分布,可以看出,油膜压力最大值出现在双齿啮合转变为单齿啮合点附近,约1.335 GPa左右,整个啮合过程均存在第二压力峰,此特性与Hertz接触理论所得齿面压力不同,且压力随着啮合过程的进行先变宽后变窄。图6为计算得到的油膜厚度,可以看出,油膜厚度在进入单齿啮合阶段后整体减小,最小值约为0.3 μm,且整个过程存在油膜颈缩现象。
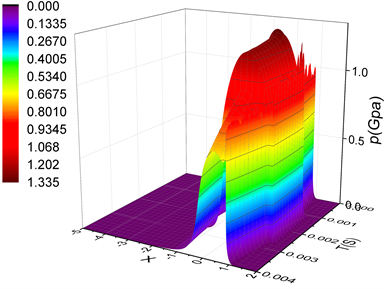
Figure 5. Oil film pressure distribution map
图5. 油膜压力分布图
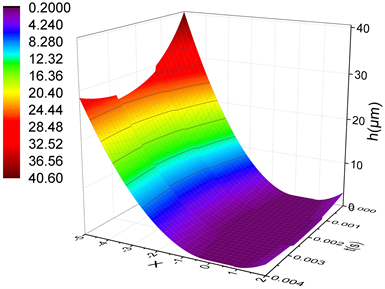
Figure 6. Oil film thickness distribution map
图6. 油膜厚度分布图
选取图4中的啮入点N1、双齿变单齿点B1、节点P、单齿变双齿点B2和啮出点N2点作为基本啮合点。图7为计算得到的这些基本啮合点处的油膜压力和厚度。可以看出,每个啮合点的油膜压力分布均存在第二压力峰,且均在第二压力峰处出现最小膜厚;不同啮合点处的油膜压力的区域宽度不同,节点P处最宽,啮入点N1和啮出点N2的最窄;不同基本啮合点最大压力不同,节点P处最大近1.3 GPa,啮出点N2最小近0.8 GPa。
图8为中心位置处(x = 0)的最小油膜厚度、中心油膜厚度和油膜压力。可以看出,最小油膜厚度随着啮合过程呈上升趋势,在单双齿啮合的变化区域出现较大的上升脉冲,在本文工况中,最小油膜厚度在0.3 μm至0.38 μm区间之内,在两个单双齿啮合变化位置处约为0.35 μm。中心油膜厚度随着啮合过程总体也呈上升趋势,在0.35 μm至0.45 μm区域之内变化,在双齿变单齿啮合位置处,中心油膜厚度突然出现较大的上升脉冲,最高可达0.42 μm,在单齿变双齿啮合位置处,中心油膜厚度出现一定的下降脉冲,最低约为0.37 μm。中心油膜压力随着啮合过程可分为三个区域,在0.7 GPa至1.3 GPa之间变化,在啮入点至双齿啮合结束区间,压力呈上升趋势,在进入单齿啮合区间的初始,压力发生阶跃至最大值,之后在整个区间内基本保持不变,在重新进入双齿啮合区间的瞬间,压力又会突然下降至某点,然后在整个区间内呈下降趋势。
(a) 最小油膜厚度
(b) 中心油膜厚度
(c) 油膜压力
Figure 8. Variation of oil film thickness and pressure with meshing line at central position
图8. 中心位置处的油膜厚度和压力随啮合线的变化
3. 直齿轮啮合效率预测模型
由于直齿轮的啮合过程中同时存在滑动与滚动,因此其功率损失主要分为两个部分:滑动摩擦功率损失、滚动摩擦功率损失。为了提高计算效率,作如下假设:
1) 摩擦因数取为平均值,由上述的热弹流润滑模型计算得出的平均速度来计算 [7] 。
2) 啮合过程中,齿轮表面受均等载荷。
滑动摩擦功率损失主要由啮合点处两接触齿面的速度差导致,计算公式为 [1] :
(8)
式中:
f——啮合点处的摩擦系数;
Fn——法向齿面载荷;
us——瞬时滑动速度。
根据上一小节分析发现,两齿面间的油膜厚度与油膜压力分布是不均匀的,因此必然产生滚动摩擦损失,计算公式为 [8] :
(9)
式中:
hmin——瞬时啮合点的最小油膜厚度;
ur——瞬时滚动速度;
l——齿宽;
φ——齿轮压力角。
总功率P为:
(10)
式中:
T——齿轮组输入扭矩;
n——主动轮转速。
因此,可得直齿轮的啮合效率为:
(11)
4. 啮合效率和机械效率损失分析
4.1. 不同转矩输入工况
保持其他参数不变,改变输入转矩如表2所示,研究齿轮的啮合效率情况及其变化规律。
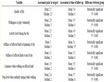
Table 2. Change range of input torque
表2. 输入转矩的变化范围设定
图9为计算得到的不同输入转矩下整个啮合过程的机械功率损失及啮合效率的变化情况。由图9(a)可以看出,啮合效率基本范围约为[93.8%, 99.8%],与实际工程测试数据基本一致 [9] [10] [11] ,从啮合方向来看,无论输入转矩如何变化,啮合效率在开始的啮合阶段都存在低效率区域,节点附近区域的效率最高。由图9(b)可以看出,无论是最大还是最小啮合效率,均随着输入扭矩的增大而增大,其中最小啮合效率的上升非常显著,有利于提高平均效率(取为最大啮合效率和最小啮合效率的均值)。由图9(c)可以看出,最大滑动摩擦损失随着输入扭矩的增大而增大;从啮合方向来看,无论输入转矩如何变化,滑动摩擦损失先小幅增大,之后减小至节点后再增大,节点附近区域的滑动摩擦损失最小。由图9(d)可以看出,最大滚动摩擦损失处在啮入点附近,且随着输入扭矩的增大而增大,在单齿啮合区域和双齿啮合的转变区域出现波动。
(a) 啮合效率
(b) 啮合效率极值
(c) 滑动摩擦损失
(d) 滚动摩擦损失
Figure 9. Change of mechanical power loss and meshing efficiency of spur gears in meshing process under different input torques
图9. 不同输入扭矩下直齿轮啮合过程中的机械功率损失和啮合效率的变化情况
从数量级上比较发现,机械功率损失以滑动摩擦损失为主。小扭矩工况下的平均效率要低于大扭矩工况的。由于最大啮合效率受扭矩的影响不大,因此最小啮合效率的高低是决定平均效率是否高低的直接因素,其最低值是由发生在啮入点附近存在的较大的滑动摩擦损失造成的。
4.2. 不同转速输入工况
保持其他参数不变,改变输入转速如表3所示,研究齿轮的啮合效率情况及其变化规律。
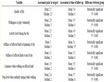
Table 3. Change range of input speed
表3. 输入转速的变化范围设定
图10为计算得到的不同输入转速下整个啮合过程的机械功率损失及啮合效率的变化情况。由图10(a)可以看出,啮合效率基本范围约为[93.8%,99.7%],与实际工程测试数据基本一致,从啮合方向来看,无论输入转速如何变化,在开始的啮合阶段都存在低效率区域,节点附近区域的效率最高。由图10(b)可以看出,最大啮合效率随着输入转速的增大而轻微减小,而最小啮合效率随着输入转速的增大而显著增大,有利于提升平均效率。由图10(c)可以看出,最大滑动摩擦损失随着输入转速的增大而增大;从啮合方向来看,无论输入转速如何变化,滑动摩擦损失先小幅增大,之后减小至节点附近后再增大,节点附近区域的滑动摩擦损失最小。由图10(d)可以看出,最大滚动摩擦损失处在啮入点附近,且随着输入转速的增大而增大,在单双齿啮合转变区域出现波动。
(a) 啮合效率
(b) 啮合效率极值
(c) 滑动摩擦损失
(d) 滚动摩擦损失
Figure 10. Change of mechanical power loss and meshing efficiency of spur gears in meshing process at different input speed
图10. 不同输入转速下直齿轮啮合过程中的机械功率损失和啮合效率的变化情况
从数量级上比较发现,在该工况下机械功率损失仍然以滑动摩擦损失为主。低转速工况下的平均效率要低于高转速工况的。由于最大啮合效率受转速的影响不大,因此最小啮合效率的高低是决定平均效率是否高低的直接因素,其最低值是由发生在啮入点附近存在的较大的滑动摩擦损失造成的。
4.3. 不同压力角对啮合效率的影响
压力角是关键设计参数之一,保持其他参数不变,改变压力角如表4所示,研究齿轮的啮合效率情况及其变化规律。
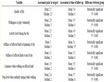
Table 4. Change range of pressure angle
表4. 压力角的变化范围设定
图11为计算得到的不同压力角下整个啮合过程的机械功率损失及啮合效率的变化情况。由图11(a)可以看出,啮合效率基本范围约为[93.7%,99.7%],与实际工程测试数据基本一致,从啮合方向来看,无论压力角如何变化,在开始啮合阶段都存在低效率区域,节点附近区域的效率最高。由图11(b)可以看出,无论最大啮合效率还是最小啮合效率均随压力角的增大而轻微减小,整体平均效率呈下降趋势。由图11(c)可以看出,最大滑动摩擦损失随压力角的增大而增大;从啮合方向来看,无论压力角如何变化,滑动摩擦损失都是先小幅增大,之后减小至节点附近后再增大,节点附近区域的滑动摩擦损失最小。由图11(d)可以看出,最大滚动摩擦损失出现在啮入点附近,且随压力角的增大而增大,在单双齿啮合转变区域出现波动。
(a) 啮合效率
(b) 啮合效率极值
(c) 滑动摩擦损失
(d) 滚动摩擦损失
Figure 11. Change of mechanical power loss and meshing efficiency of spur gears in meshing process at different pressure angles
图11. 不同压力角下直齿轮啮合过程中的机械功率损失和啮合效率的变化情况
从数量级上比较发现,机械功率损失以滑动摩擦损失为主。小压力角下的平均效率要高于大压力角的。最大啮合效率受压力角的影响偏小,其最低值是由发生在啮入点附近存在的较大的滚动摩擦损失造成的,最小啮合效率受压力角的影响相对大点,其最低值是由发生在啮入点附近存在的较大的滑动摩擦损失造成的。
5. 结论
本论文将直齿轮弹流润滑问题等效为一维线接触问题,研究直齿轮啮合过程中的机械功率损失和啮合效率的变化及其受关键参数的影响规律。
1) 基于直齿轮啮合的几何特征建立了直齿轮啮合接触模型,可以计算任意啮合点处的曲率和速度;基于牛顿流体和润滑理论,建立了直齿轮瞬态弹流润滑模型,可以计算任意啮合点处的油膜压力和油膜厚度,与Hertz接触理论所得齿面压力不同,在润滑介质出口处存在第二压力峰,且同时存在油膜颈缩现象,揭示了直齿轮啮合中的弹流润滑状态。
2) 建立了直齿轮啮合效率模型,可以预测不同工况下的啮合效率及其变化规律,仿真结果发现有:低转矩、低转速和大压力角都会造成啮合平均效率偏低;单齿啮合区的最大啮合效率水平普遍较高的情况下,啮合过程中的最小啮合效率的大小是决定平均啮合效率高低的关键因素,其以滑动摩擦损失为主,且效率最低点往往发生在啮合过程中的啮入点等,为设计高效率直齿轮提供有效的参考依据。
上述分析数据虽然在总体效率范围得到了工程验证,但是仍然没有覆盖更宽的转矩、转速和压力角等工程实际应用范围,还需要细化研究做进一步验证,将在后续论文工作中展示。