1. 引言
输送油、气的管道大多处于复杂的土壤环境中,所输送的介质也多有腐蚀性,管道内壁和外壁都可能遭到腐蚀。一旦管道被腐蚀穿孔,即造成油、气泄露,不仅使运输中断,而且会污染环境,甚至可能引起火灾,造成危害。3PE管防腐管道采用的环氧底漆、中间聚乙烯粘结层和外层聚乙烯保护层3层结构,具有良好的抗腐蚀性、抗水气渗透性以及力学性能 [1] 。
针对国内外发现的3PE管道防腐层投产后短期内粘结失效案例,研究认为防腐层剥离与防腐材料和钢管底材之间加热过程不协调所产生的热残余应力有关 [2] 。防腐层涂覆过程中,由于管体、环氧底漆、粘结剂和外保护层的使用材料并不相同,热膨胀系数存在较大差异,防腐层系统产生比较高的热残余应力。当局部残余应力超过了因为水渗透而降低的防腐层剩余粘结强度时,就会发生防腐层剥离 [3] 。
2. 有限元分析理论
基于3PE管涂覆结束后水冷却阶段因温变产生的热残余应力案例,分析研究利用ABAQUS在热辐射、热对流模拟方式上的解决方案。预制3PE钢管工艺流程中,管体在缠绕聚乙烯保护层后通过水冷进行冷却,冷却过程中并未经历快速、剧烈的形变,不存在机械能转化为热能,温度场对应力场无依赖关系,故适合采用顺序热应力耦合进行求解。聚乙烯和环氧底漆可以近似认为是一种超弹性橡胶材料。对于橡胶材料,在一定变形范围内采用Von Mises等效应力来确定模型中的应力分布。它可以清晰描述出结构内部的应力分布,从而可以快速确定模型中的最危险区域。
3. 模型建立
3PE管的管壁厚度与直径相比较小,是一种典型的薄壁结构。建立管体的轴对称模型即可进行精确的分析。工程中采用的3PE管外保护层是缠绕上去的,且有一定宽度,所以取包含一个或几个典型宽度的管长进行研究即可。综合考虑实际情况与数值仿真的可行性,所模拟管体的参数见表1。模拟中假设各材料参数与温度无关,各材料参数见表2。
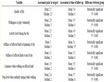
Table 1. The geometric parameters of analog pipe body
表1. 模拟管体的几何参数
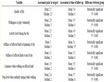
Table 2. The material parameter of 3PE anticorrosion pipe
表2. 3PE防腐管材料参数
初始条件设置:实际制管工艺中,管体首先被预热到250℃ (最高不超过275℃),然后再进行其他工艺。因此,计算模型的初始时刻整个管体的初始温度为250℃。
边界条件设置:水冷边界可以通过热对流边界条件进行模拟。管壁内侧与空气接触,空气实际的温度也会比较高,而且空气流动不大,所以热对流现象不明显,主要是热辐射效应,热辐射系数采用0.8。在计算应力的分析步中,还需定义位移边界条件和管体尾端在轴向的位移约束。
接触设置:在管体—环氧底漆,环氧底漆—粘结剂,粘结剂—聚乙烯保护层之间通过Tie约束建立接触面两侧结构的完全刚性连接约束。
根据几何模型建立有限元模型。热传导模拟中采用热传导CAX4单元(4节点双线性轴对称单元),模型和材料的参考温度设置为室温20℃,物理时间设置为60 s。
4. 仿真结果分析
1) 温度场分布。由于防腐层外侧采用水冷边界,所以温度变化较大,防腐层大部分区域温度降到50℃以下。管体内壁采用的是辐射散热,热辐射效应不明显,所以管体温度仍然较高,环氧底漆的温度介于管体和聚乙烯保护层之间。
2) 变形场分布。3PE管防腐层涂覆区域内变形场分布如图1所示,可以看出,最大变形发生在管端截短防腐层补口预留处。其中补口预留处的PE外防护层的形变量大于中间粘结剂层,熔接环氧(FBE)底漆层的变形量最小,这是由于环氧底漆的热膨胀系数远小于粘结层(大约是粘结层的1/10)。从形态上看,环氧底漆因温度降低导致的变形要小于粘结层。
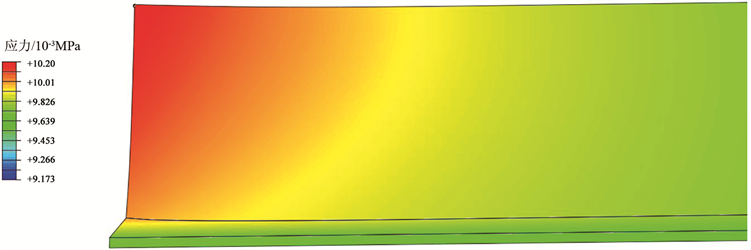
Figure 1. The distribution of deformation field of 3 PE pipe coatings
图1. 3PE管防腐层变形场分布
3) 应力场分布。3PE管防腐层涂覆区域内应力场分布如图2所示,可以看出,热残余应力集中现象同样出现在管端截短防腐层补口预留处。在FBE底漆层最为明显,其热残余应力比邻近的粘结剂层高320%。虽然FBE底漆层其产生的形变较小,但是由于其弹性模量要远大于粘结层的弹性模量(约80倍),所以FBE底漆的应力反而要大于粘结层。
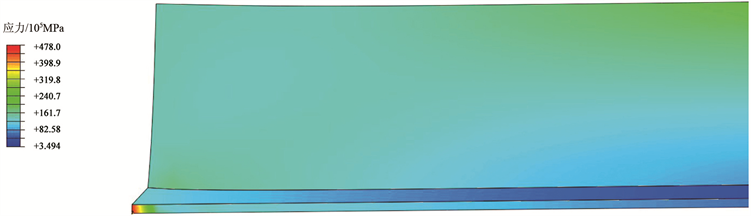
Figure 2. The distribution of stress field of 3 PE pipe coatings
图2. 3PE管防腐层应力场分布
通过观测和分析Mises应力分布云图,可以发现在3PE管防腐层涂覆后,经过水冷却,3PE防腐层在60 s内温度由250℃急剧减少到50℃左右,热残余应力集中现象出现在管端截短防腐层的角上,在基材与FBE底漆层热残余应力最大,同时在补口预留处的PE外防护层出现明显形变。若基材与FBE底漆层在外界环境影响下导致层间粘合力小于热残余应力,就会产生管端防腐层翘边剥离现象。
5. 管端截短防腐层区域热残余应力分析
分析了FBE底漆层膜厚度、粘结剂膜厚度、聚乙烯保护层厚度以及聚乙烯保护层在预留段的收尾形状等参数对残余应力的影响,对3PE防腐钢管管端截短防腐层区域的热残余应力进行重点研究,利用有限元分析软件观测各工况条件下热残余应力的分布情况。
5.1. FBE底漆层膜厚度的影响
通过分析不同FBE底漆层膜厚度下最大热残余应力值(见表3),可以看出,随着FBE底漆层膜厚度的增加,最大轴向热残余应力和最大环向热残余应力均缓慢变小,径向热残余应力变大。Mises等效应力值随着FBE底漆层膜厚度的增加而缓慢增加,当底漆层膜厚度增加43%时,Mises等效应力仅增加4%。说明FBE底漆层膜厚度对Mises等效应力的影响比较小。
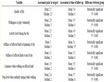
Table 3. The max thermal residual stress under different thickness of FBE primer film
表3. 不同FBE底漆层膜厚度工况下最大热残余应力值
5.2. 中间粘结剂层膜厚度的影响
通过分析不同中间粘结剂层膜厚度下最大残余应力(见表4),可以看出,随着中间粘结剂层膜厚度的增加,各个应力分量缓慢减小,Mises等效应力变大,粘结剂层膜厚度的增加对热残余应力几乎没有影响。
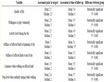
Table 4. The max thermal residual stress under different thickness of intermediate adhesive layer film
表4. 不同中间粘结剂层膜厚度工况下最大热残余应力值
5.3. PE外防护层膜厚度的影响
通过分析不同PE外防护层膜厚度下最大残余应力(见表5),可以看出,随着PE外防护层膜厚度的增加,所有应力分量都随之增加,尤其是径向热残余应力增大显著。说明PE外防护层膜厚度的增加不利于降低管道预制工艺产生的残余应力。
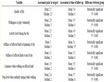
Table 5. The max thermal residual stress under different thickness of external PE coating layer film
表5. 不同PE外防护层膜厚度工况下最大热残余应力值
5.4. 管端截短防腐层收尾形状的影响
图3是当坡度为30˚,Mises等效应力为15.46 MPa时的等效应力图,可以发现,3个应力分量都降低,但是降低的幅度不相同,环向热残余应力变化幅度较小,径向热残余应力变化非常明显,此时的管端截短防腐层收尾形状比垂直形状时径向热残余应力减小85%左右。所以,相比较垂直收尾形状,有一定角度的收尾形状能够有效降低热残余应力。表6为不同收尾坡度下的最大热残余应力,对比发现,当角度为30˚时,最大热残余应力最小,因此该角度为最佳收尾角度。
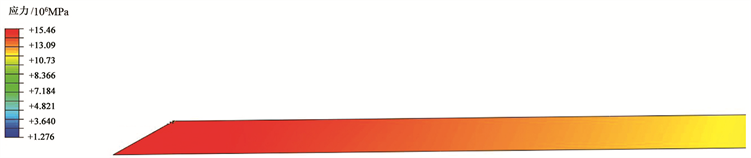
Figure 3. Mises equivalent stress diagram (30˚ tail shape)
图3. Mises等效应力图(30˚收尾形状)
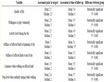
Table 6. The max thermal residual stress under different tail slopes
表6. 不同坡口收尾坡度下最大热残余应力
6. 结论
1) FBE底漆膜厚度的增加会相应增加3PE管的热残余应力,但其影响可以忽略。防腐钢管在破损风险大的环境下,可以适当增加FBE底漆膜厚度。
2) 中间粘结剂层膜厚度的增加对热残余应力几乎没有影响。
3) PE外防护层膜厚度是影响FBE底漆与基材间的热残余应力的主要因素。随着聚乙烯保护层厚度的增加,管道预制工艺产生的热残余应力相应增加。
4) 相比较垂直收尾的情况,有一定角度的收尾能够有效降低热残余应力,采用30˚的收尾坡度时最大热残余应力最小。