1. 引言
现代通信、遥感、医疗、航空航天等领域对各种复杂光滑曲面的应用越来越频繁,高精密的光学元件、形状各异的光滑模具、壳体等需求量也与日俱增,这就驱使了相应制造技术必须能适应不断更新的市场要求 [1] [2]。现代先进制造技术结合了计算机控制技术,根据定量数据来确定性去除材料,加工精度和效率非常高 [3],由于工具头的限制,传统的加工方法如单点金刚石车削(Single Point Diamond Turning, SPDT)、数控小工具头加工(Computer Controlled Optical Surfacing, CCOS)、气囊抛光(Bonnet Polishing, BP)等无法满足复杂面型的精密加工需求,尤其是对于非对称凹面零件,加工较为困难且不能保证精度 [4] [5] [6]。
磁射流抛光技术结合了磁流变抛光技术和磨料射流抛光技术,属于完全柔性抛光,能够实现较远距离的精确加工,对于复杂面型的修整和抛光有着传统抛光方式难以比拟的优势。较之于磁流变抛光技术,磁射流技术的抛光工具头较小、磨粒的切削速度和切削压力可调范围大、加工距离较大;较之于磨料射流抛光技术,其去除鲁棒性高、受被加工面型约束小;同时,在磁场的辅助下,液柱能保持较远距离稳定,适应各种形状工件的抛光 [7]。但该技术涉及到流体力学、电磁学等多学科,数学模型复杂,难以建立稳定的射流抛光模型;另外,影响抛光精度的因素较多,例如磁场强度、喷嘴直径、喷射角度、喷射压力、抛光液配比等 [8],从而难以匹配出较优的参数组合。本文将结合实验室自研的磁射流加工中心MJP-150对所选喷头体的磁场进行优化,以获得稳定的射流柱和抛光斑,并验证其应用于复杂曲面的抛光效果。
2. 喷头体结构和磁场优化
作为能量参数加工平台,需要提供能量的系统以及能量的传输媒介,根据磁射流技术的基本原理,为实现较远距离确定性的材料去除,需要具备合理的磁场分布以获得稳定的磁射流抛光液束。
根据磁射流加工机理:为获得高稳定性和准直性的射流液束,需要汇聚在喷射轴向的磁场对出射液体进行塑形 [9],详情如下图1所示。
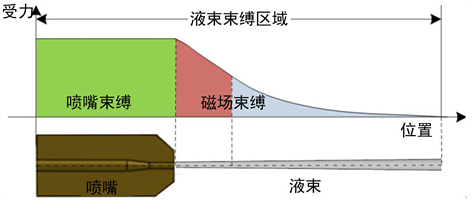
Figure 1. Distribution of binding force of liquid column
图1. 液柱所受束缚力分布
由电磁学相关理论可知,磁荷倾向于聚集在磁极边界上,而且磁力线在空间的走向也是沿着磁阻最小的路径分布。因此采用高磁导率的喷嘴,将诱导磁力线从喷嘴内部穿过,在喷嘴内腔通道的磁场场强将非常弱,以满足磁场塑形的第二个条件。另外,圆柱型磁极表面产生的磁场会向外发散而导致场强较弱,但是锥柱状喷嘴头部锥台形状对锥嘴末端区域的磁场具有聚焦、整形作用 [10]。在从喷嘴末端出来时,由高磁导率材料汇聚的磁力线,在锥状结构的限制下,变得更加汇聚,即喷嘴出口处的磁场强度最强。因此,应用锥柱状的喷嘴,锥角为φ = 13˚,长径比大于等于4,如图2所示。

Figure 2. Schematic diagram of conical cylindrical
图2. 锥柱状喷嘴示意图
空气中
处的磁场强度
是圆柱形部分
和锥状部分
叠加的结果,有 [11] :
(1)
式中R0为锥极末端半径,r为喷嘴台面半径,θ为锥角,J为饱和磁极化强度,锥角面到原点距离
。进一步地,由公式(1)可以推导出原点处的磁感应强度为:
(2)
上式中,令r为常量、θ的二阶微分等于零,则均匀磁场的最佳锥角和台面半径的关系为:
(3)
因此,确定锥角θ和台面半径r就可设计出合理锥状喷嘴。同时由图2所示,磁路主要集中在由喷嘴、隔磁腔和腔体空间构成的回路内,因此磁场的研究可以归结到导体缝隙磁场分布的研究,导体由喷嘴和隔磁腔组成,间隙为喷嘴的出口和隔磁腔出口之间的气隙。根据电磁场和磁阻理论,空气气隙中的电磁场可以表示为:
(4)
式中Ne为线圈匝数,I为线圈的电流强度,
、
和
分别表示间隙、隔磁腔和喷嘴的有效截面,
、
和
分别表示间隙、隔磁腔和喷嘴的相对有效磁导率,
、
和
分别表示间隙、隔磁腔和喷嘴的相对有效长度,而间隙的有效长度等价于喷嘴相对于隔磁腔的嵌入深度H。
由公式(3)和公式(4)可知,当电磁线圈选定后,喷头内部的磁场强度分布可以通过选取合适的锥角(θ)、台面半径(r)以及嵌入深度(H)来进行优化。基于以上理论分析,选取喷头的材料以及结构形状参数如下表1所示。
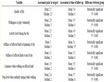
Table 1. Material and structure parameters of nozzle
表1. 喷头材料及结构参数
选定喷头材料及结构后,分别对单一变量对磁场强度的影响进行仿真。当选定锥角分别为30˚、40˚、50˚和60˚时,其电磁分布结果如图3(a)~(d)所示,可以看到,当锥角为30˚时,腔体内的磁场分布变化梯度较大,大于和等于40˚时,磁场分布较均匀。对不同锥角下沿喷射轴线上的磁场分布仿真情况如下图3(e)所示,在喷嘴出口的一定距离处,由于锥角的存在,磁场产生明显的汇聚现象,而且随着距离的增加,磁场逐渐减小,整体呈单峰式分布。对40˚锥角进行细化,在电流为0.4 A,台面半径为3 mm时,磁场强度曲线如图3(f)所示,39˚~40˚附近汇聚磁场最强,因此选取40˚作为最佳锥角。
当确定锥角为40˚后,选取不同的台面半径为研究对象分析电磁场强的分布,台面半径r分别为2 mm、3 mm、4 mm和6 mm,仿真结果如图4所示。图中可以明显看出当台面半径越小磁场强度越强,但是考虑到喷嘴的机械强度在此选取半径为3 mm的台面。
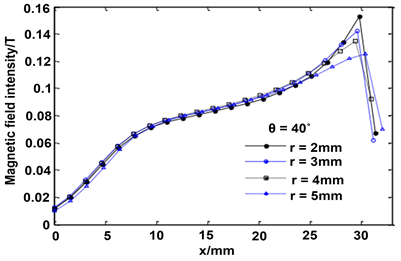
Figure 4. Magnetic field distribution at different mesa radii
图4. 不同台面半径的磁场分布
对于不同嵌入深度(0 mm、10 mm、17 mm和26 mm),锥角θ为40˚,台面半径r为3 mm,研究结果如图5所示。可以看出虽然当嵌入深度为0 mm时磁场分布均匀,但是此时磁场强度较弱,而且在喷嘴末端没有形成汇聚磁场分布;而当嵌入深度增加到10 mm时,磁场在喷嘴末端发生了明显的汇聚现象,喷射路径上的磁场强度也有所增强;当嵌入深度达到35 mm时,磁场的变化梯度过大,且持续距离较短。因此,选取嵌入深度17~26 mm,即线圈高度的1/2时可满足要求。
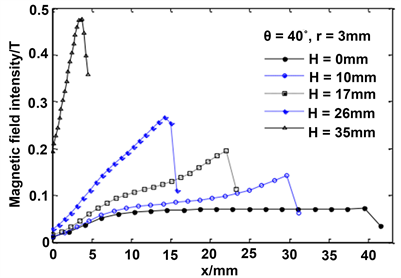
Figure 5. Magnetic field distribution at different embedding depth
图5. 不同嵌入深度的磁场分布
将选定的优化参数进行实验测量,测量工具为高斯测量计、支架以及一维运动平台,用于固定和承载喷头体的运动平台为铝合金材料。支架用于固定高斯测量计的测头(探针),喷头体固定在一维运动平台的运动部件上,通过调节喷头位置来控制测头的探入深度,实验装置与测量结果如下图6所示。从测量出的磁场分布与仿真结果比较,其分布趋势一致,说明所选参数能实现较优的磁场分布。
3. 材料去除稳定性研究
根据前面对磁场的研究,本文采用水基磁流变液混合4 wt.%的CeO2、0.6 wt.%的悬浮剂以及微量硝酸锌作为磁射流加工液,并采用40˚的喷嘴外锥角、3 mm的喷嘴外台面半径以及1/2线圈高度的嵌入深度,0.7 MPa的喷射压力,0.4 A线圈电流作为工艺参数。
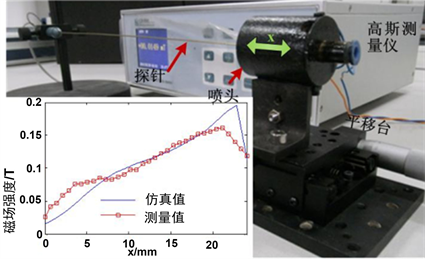
Figure 6. Measurement of magnetic field of nozzle
图6. 喷头体的磁场测量
为验证磁场作用下射流加工的稳定性,采用简单垂直入射喷射加工方式,并选取喷射距离分别为10 mm、56 mm和86 mm,实验过程共持续约3 h,所得的实验结果如图7所示。在喷射距离为10 mm时,磁场对去除的形状并无明显的影响,都呈环状分布;当喷射距离增大到56 mm时,有磁场束缚的加工去除和10 mm的相似,但是对于无磁场时的去除,产生了较明显的变形,包括形状和深度;这一现象将随着加工距离的增加变的更加恶化。
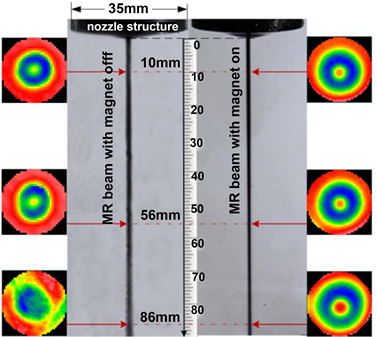
Figure 7. Distance stability of material removal with or without magnetic field
图7. 有无磁场时材料去除的距离稳定性
提取有磁喷射时抛光斑剖面作为研究对象,如图8所示。图8(a)中展示了加工斑的中轴剖面曲线,为了准确的分析加工形状,分别作了以下定义:DR为去除斑的直径,dR为去除斑谷值的直径,hR为中间凸起的高度,HR为谷的深度。由图8(b)可以看出加工斑的直径和谷值直径随喷射距离几乎不变,这种稳定性延续表现在中间凸起高度和谷深,如图8(c)所示。由此实验说明了磁射流加工材料去除的距离稳定性和时间稳定性,同时证明了磁场优化工艺参数的合理性。
(a) 抛光斑剖面
(b) 抛光斑上下直径对比
(c) 抛光斑深度和中间凸起对比
Figure 8. Material removal contrast of different spray distance
图8. 不同喷射距离材料去除对比
4. 对复杂光滑曲面加工实验
通过对喷头体磁场进行优化,使磁射流在材料去除上具有良好的距离稳定性和时间稳定性,因此磁射流抛光技术不仅可以应用在规则平面、曲面的加工中,在一些复杂凹面的抛光甚至微结构加工方面也有着巨大潜力。
如图9(a)是对一块非连续透镜的抛光,传统刚性接触式工具头加工所留下的加工盲区,磁射流抛光技术就能很好的运用其加工距离和灵活性上的优势,将该盲区的粗糙度大幅降低,由原来的粗糙度Ra值为91.07 nm降至4.86 nm;图9(b)是采用间距为1.4 mm的之字栅线路径,工具头以离散形式运动,各驻留点时间相同(30 s),在光滑K9玻璃上加工出超光滑的微阵列凸透镜,对玻璃表面的检测结果,各子凸透镜的高度为0.03 λ (光波长)。由此可见,磁射流抛光技术在光学制造的灵活性和精度上不仅优于传统加工技术,而且由于其特殊的W形去除函数和高加工精度,在微透镜阵列甚至复杂面型光学元件的制造上有着巨大应用前景。
除加工玻璃元件外,磁射流抛光技术还可应用在金属、陶瓷等材料加工上。如图10(a)是一套不锈钢牙齿模具,图10(b)~(e)分别是对其进行多次抛光的效果。可以看到,采用磁射流对存在麻点、表面氧化的不锈钢模具进行多次抛光,模具光泽度明显增加,表面纹路和麻点全部消失,不破坏模具轮廓,一些微小的深凹区域也能很好的抛光,说明磁射流抛光技术对异形表面也具有良好的抛光效果。
(a) 非连续双曲面镜抛光
(b) 微透镜阵列
Figure 9. Glass device polished by magnetorheological jetting
图9. 磁射流抛光玻璃器件
5. 结语
磁射流抛光技术是现代先进流体辅助柔性加工技术的重要组成部分,具有独特的技术优点,如无亚表面损伤、边缘效应弱、加工中热效应小以及较低的加工应力形变等,结合自由度较高的数控机床,配置合理的磁场分布,辅以合适的抛光液,能够实现多种材料的远距离精确抛光,使得该技术适于加工任何表面,尤其是在较大陡度的复杂表面加工上,磁射流抛光技术有着传统抛光方式难以比拟的优势。本文结合电磁学相关理论,在选定喷头体材料和部分结构参数下,对影响射流束的喷头体磁场进行仿真和优化,确定了当喷头体锥角为40˚、喷嘴台面半径3 mm和喷头嵌入深度为线圈高度1/2时,可以得到最优磁场分布,并对该磁场下的液束分布和抛光斑情况进行了研究,证明了磁射流在材料去除上的距离稳定性和时间稳定性。同时,将优化后的磁射流应用于复杂光学表面抛光、微透镜阵列加工和不锈钢牙齿模具抛光,说明了对磁场的优化可以很好地提高磁射流在确定性加工上的稳定性。
基金项目
深圳市科技创新计划资助项目(No. JCYJ20170817115139963, JCYJ20170817115017509)。
NOTES
*通讯作者。