1. 引言
近年来,用于环境检测,特别是VOCs的检测中越来越多地用到金属氧化物半导体气体传感器。自1962年日本学者Seiyama首次报道半导体ZnO薄膜电阻变化可判定还原性气体浓度 [1],半导体金属氧化物一直占据着气体传感器的主流发展方向。经过半个多世纪的发展,半导体气体传感器在敏感材料、元件制作和集成工艺等方面均有较大提升 [2] [3] [4] [5],气体传感器在环境监测领域有了广泛的应用,然而,半导体气体传感器的性能评价手段却相对滞后,影响了其在一些低浓度、高危险气体场合的应用 [6]。随着环境检测要求的提高 [7] 及气体传感器性能的进步,亟需建立一种能够满足高灵敏、快速响应传感器的性能评价装置。
目前主要基于静态和动态两种方法对传感器灵敏度(Sensitivity)、响应–恢复时间(Response and recovery time)等关键参数判定 [8] [9] [10]。美国能源部Tobias等 [11] 通过快速移动测试气体出口位置实现传感器周围气体环境的快速置换,测得的响应时间可达毫秒级,但对灵敏度测试的准确性较差;Sawaguchi等 [12] 研究的“diffuse-burst”方法有效地缩短了目标气体在评价系统中扩散时间,减小系统误差,更加真实地表达了传感器固有的响应时间,缺点是该方法不能测量传感器的恢复时间。
本文以微型舱为核心构建了气体传感器性能评价系统,由多组分动态配气单元、微型测试舱和数据采集分析单元三部分组成。舱体及其配件选用聚醚醚酮树脂(Polyetherether ketone, PEEK)材料构建,舱体内部结构为圆柱体,圆柱两端为气体进、出口,上、下端分别设置有吹扫口和传感器安装组件,内腔容积约为31 mL。建立微型测试舱内腔结构三维实体模型,利用FLUENT软件对其内部气体流场模拟分析;采用压差检漏法考察测试舱的气密性;并用甲醛及甲苯等目标组分对气体传感器性能评价系统进行评价。
2. 实验部分
2.1. 微型测试舱及测试系统的设计
基于材料对气体吸附释放特性及传热等性能考虑 [13],测试舱主体及传感器安装组件选用特种工程塑料聚醚醚酮树脂(Polyetherether ketone, PEEK)材料,其长期耐受温度可达250℃,具有低吸收、低释放和自润滑等特性 [14],其它结合部件采用不锈钢304和聚四氟乙烯材料。如图1所示,测试舱外观为长方体结构,传感器安装组件通过外螺纹与测试舱主体相连;测试舱内腔为圆柱体结构,圆柱两端分别设有进气口(A口)和出气口(B口),在内腔上端开设吹扫气口(C口),底部设有传感器安装组件,内腔直径为18 mm,比传感器基座直径略大,内腔容积仅为31 mL;传感器安装组件位于舱体下端连接口(D)内,上端支撑传感器基座,基座与凹槽侧壁间嵌有密封圈,下端孔道通过传感器引线并与测试装置和加热装置相连。传感器安装组件设计了不同尺寸的凹槽及孔道结构(φ19 × 5.5 mm (H)、φ20 × 5.5 mm (H)、φ9.5 × 1.5 mm (H)等),满足不同类型气体传感器的测试需求。
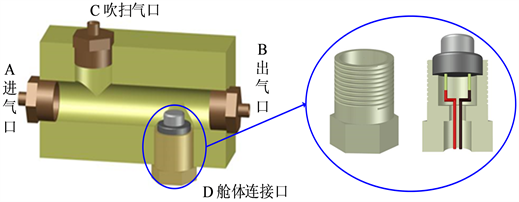
Figure 1. Micro test chamber cross-section and sensor holder structures
图1. 微型测试舱剖面图及传感器安装组件结构图
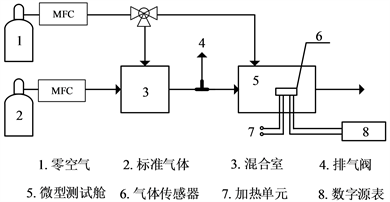
Figure 2. Schematic diagram of test system
图2. 测试系统示意图
测试系统如图2所示,测试气体经由高浓度标准气体与零空气按照一定流量比稀释后进入混合室内,完全混匀后一定流量的气体经测试舱进气口(A口)进入腔室内部,扩散至腔室下端传感器敏感材料表面,与表面吸附氧发生反应,产生响应信号,再由出气口(B口)排出舱室;传感器信号通过吉时利数字源表(Keithly 2400)采集并输出,待响应信号稳定后,关闭A口进气,同时打开洁净空气(C口)对舱室进行吹扫,使传感器响应恢复至初始状态;尾气经由收集瓶收集后排出室外。气体浓度按照下式计算:
式中:
——进入测试舱内气体浓度;
——高浓度标准气体浓度;
——标准气体的流量;
——载气(零空气)的流量。
2.2. 测试舱内部气流场模拟
测试舱为气体传感器提供测试环境,舱室内气流状态直接影响传感器测试的基线稳定度、响应灵敏度及响应-恢复时间等关键参数。本研究基于SolidWorks软件对测试舱内腔结构建立物理模型,并在ANSYS FLUENT软件中选择标准k-ε方程(k为湍动能,为耗散率ε)对测试舱壁面处湍流流动和腔室内部气体层流状态进行模拟,标准k-ε模型输送方程式如下,两个相互分离的传送公式求解:
(1)
(2)
式中Gk表示由层流速度梯度而产生的湍流能项,Gb是由浮力产生的湍动能项,Ym为在可压缩流动中湍流脉动膨胀到全局流程中对耗散率的贡献项,C1,C2,C3是常量,σk和σε是k方程和ε方程的湍流Prandtl数,Sk和Sε是用户定义的湍流耗散源项。
2.3. 评价装置的构建
以微型测试舱为核心部件,搭建气体传感器性能评价系统。如图3所示,由多组分动态配气单元、微型测试舱和数据采集分析单元三部分组成。本实验采用零空气作为载气,零空气混合前先通过VICI过滤器纯化,再与测试标准气混合,本研究所用标准气体包括1 ppm、10 ppm、100 ppm甲苯,100 ppm甲醛(北京氦普北分气体工业有限公司,BAPB,中国);根据流量比混合法动态配气原理,通过多个Horiba质量流量控制器设定各组分载气和标气的流量,获得精确动态配置的目标检测气体;采用吉时利2400数字源表及其软件(Keithley KickStart)采集并分析数据。
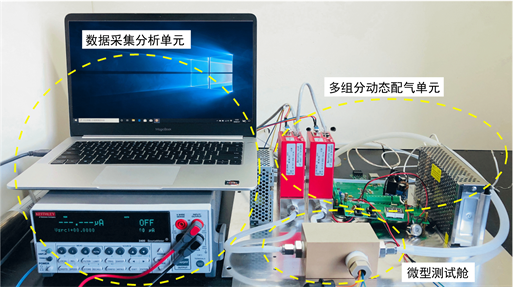
Figure 3. Evaluation device for performances of gas sensor
图3. 传感器性能评价装置图
3. 微型测试舱性能分析
3.1. 测试舱气体流场分析
测试舱为气体传感器提供气体测试环境,稳定的流场是测试准确性必要条件。对微型传感器测试舱内部流场仿真模拟,分析气体在其内部的运动轨迹。以SolidWorks建立的测试舱内腔结构三维实体模型为基础,运用FLUENT软件对气体流场模拟;选择标准k-ε模型,物性参数设置流体材料为空气,粘性系数为1.7894 × 10−5 Pa·s;在绝对参考坐标系中采用分量速度设置,x方向的入口流速为1 mL/min;选则静止壁面(Stationary Wall)类型,无滑移(No Slip)边界条件;采用SIMPLE算法,以速度为基本求解变量,计算测试舱内部流场并分析其特性。气体速度云图及矢量图如图4所示。
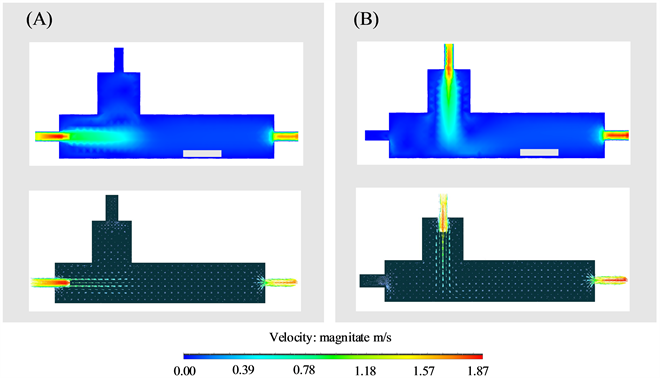
Figure 4. The gas velocity cloud and vector diagrams for (A) Inlet and (B) Purge inletof the internal test chamber
图4. 测试舱内部(A)进气口及(B)吹扫气口进气的气体速度云图及矢量图
如图4所示,测试气体以较高流速进入到测试舱内部,随着壁面压力减小,气体流速逐渐衰减呈均匀分布,并以稳定流速通过被测试传感器表面;速度矢量图显示舱内涡流、湍流仅分布于气体入口、出口部位,传感器表面气流平稳。仿真模拟结果表明,本研究设计的微型气体传感器测试舱内部气体流场分布均匀,内部死体积较少,能够均匀分散的气体浓度,同时获得较低的传感器表面气体流速,满足设计要求。
3.2. 测试舱气密性检验
传感器测试舱在使用过程中,为尽量避免内部气体与外界空气发生交换,应满足一定气密性要求 [15] [16] [17]。本研究设计的微型传感器测试舱存在多个进气口及传感器支撑体接口,以压差检漏法 [18] 对其进行气密性检验。实验装置如图5所示,测试该传感器测试舱在常规使用条件下的气密性,质量流量计(SEC(F)-N112MGM(R)W)设置流量,打开开关阀A,关闭开关阀B,记录流量计A(DCal 5000,北京科安公司)示数(X)待测试舱内部压力稳定后,记录流量计B此时示数(Y);关闭开关阀A,打开开关阀B,待测试舱内部压力稳定后,再次记录流量计B示数(Z);质量流量计流量设置为不同值,依次测试。
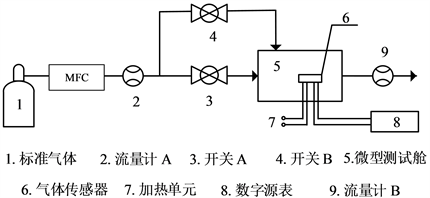
Figure 5. Schematic diagram of test chamber air tightness test
图5. 测试舱气密性测试示意图
如图6所示,质量流量计预设100 mL/min~2000 mL/min的不同流量,流量计所记录数据X、Y、Z标准差(σ)小于0.84,泄漏率远小于0.1%。测试舱气密性在使用空气泄露率 [19] 评价时,1 kPa正压条件下,舱内气体
表明在常规条件下,舱室及其配件接口处无明显漏气现象,满足本试验气密性设计要求。
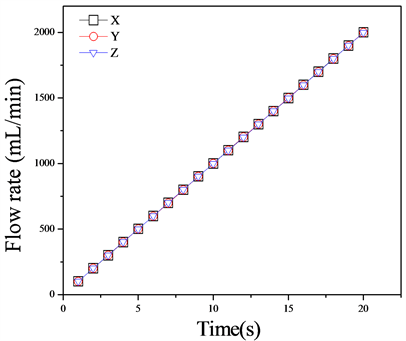
Figure 6. Comparison of test chamber air inlet flow with air outlet flow
图6. 测试舱进气口及吹扫气体口与出气口流量对比
3.3. 测试舱应用效果分析
以甲醛、甲苯为目标组分,考察装置对传感器的系统评价能力。
3.3.1. 入口气流对传感器基线影响
将购买市场上两款具有代表性的电阻型气体传感器和自制半导体气体传感器,分别标记为Sensor W、Sensor F和Sensor Z,分别安装于测试舱内,测试入口气体流速对响应信号基线的影响。如图7所示,测试舱进气口通入零空气,每种流速观测时间为200 s,以200 mL/min为初始流速并逐渐增大流速,200 mL/min~1200 mL/min流速下三款传感器基线相对平稳,响应阻值随流速增大而升高,当入口气体流速大于1200 mL/min后三款气体传感器基线均出现不同程度的波动,其中Sensor Z基线波动巨大,对气流扰动最敏感。三款传感器性能虽有所差异,但响应趋势基本相同,间接反应了不同入口流速下测试舱内传感器上方的气体流动状态,表明微型传感器测试舱在入口气体流速不大于1200 mL/min时内部流场平稳,可为敏感元件提供稳定的外部气体环境。
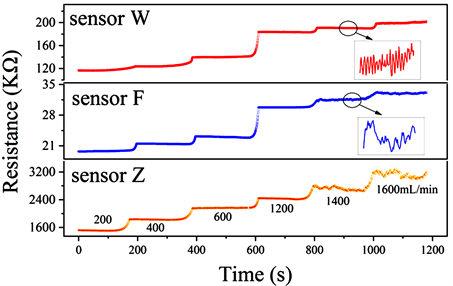
Figure 7. Response base line under different inlet gas flow rates
图7. 不同入口气体流速条件下的传感器基线图
3.3.2. 测试舱对传感器性能评价
Sensor W对甲苯的标称检测下限为10 ppm,灵敏度(Rg/Ra)为0.52,本研究构建的评价系统对Sensor W性能评价结果如图8所示,甲苯检测下限为0.1 ppm,灵敏度(Rg/Ra)为0.926,检测范围为0.1 ppm~100 ppm测试范围,与标称值相比,本次测试Sensor W的性能指标,包括灵敏度、检测限及检测范围,均有所提高。
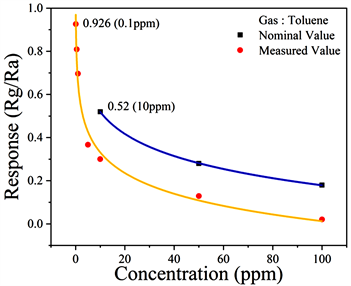
Figure 8. Comparison of mearsured value with nominal value for sensor W sensitivity
图8. Sensor W灵敏度标称值与实测值对比
Sensor Z在系统中的性能评价结果,在最佳工作温度下,Sensor Z对不同浓度的甲苯和甲醛的灵敏度响应如图9(A)所示,在500 ppb~10 ppm范围内,随着甲醛浓度的阶跃式增加,Sensor Z的响应稳步上升;同样,在5 ppb~300 ppb范围内,Sensor Z的灵敏度随着甲苯浓度增加而上升。图9(B)为Sensor Z对500 ppb甲醛和5 ppb甲苯的动态响应恢复曲线,对甲醛和甲苯的响应时间(T90)分别为11 s和36 s,恢复时间(T10)分别为2 s和9 s。Sensor Z本身对多种还原性气体具有良好的灵敏度和响应恢复特性,该系统能够满足其低浓度动态条件下的气敏特性分析。
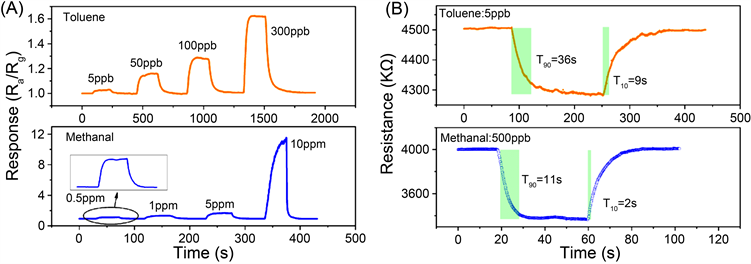
Figure 9. (A) Sensor Z对不同浓度甲醛和甲苯的灵敏度响应曲线;(B) Sensor Z对500 ppb甲醛和5 ppb甲苯的动态响应恢复曲线
图9. (A) Sensitivity of sensor Z to different methanal and toluene concentrations; (B) enlarged response curves of sensor Z exponse to 500 ppb methanal and 5 ppb tolene
4. 结论
本研究设计开发了一款用于高灵敏、快速响应半导体气体传感器的微型测试舱,并以微型测试舱为核心部件,搭建动态气体传感器性能评价系统;对微型测试舱内部气流进行仿真并利用三款气体传感器进行验证,同时基于微型测试舱搭建的系统对两种气体传感器(Sensor W、sensor Z)测试,结果显示,该系统可同时对传感器进行灵敏度、检测限、响应–恢复时间及检测范围评价。本文构建的气体传感器性能评价系统具有内部流场稳定、浓度分布均匀、气密性好等特点,尤其适用于高灵敏气体传感器的低浓度响应能力测定及响应恢复时间的评价。
基金项目
国家重点研发计划项目(NO. 2016YFC0700604),北京市科学技术研究院萌芽计划(NO.BGS201910)。
NOTES
*第一作者。
#通讯作者。