1. 前言
由于不受中压直流舰船综合电力系统中电频率的限制,直联式高速发电机组可大幅提高转速、功率密度和集成化程度,已成为舰船综合电力系统发电模块的重要趋势。由于受到材料、结构和工艺方面的限制,对于船用高速发电机,提高电机转速所带来的一系列力学、振动噪声等问题逐渐突出 [1]。感应式高速异步电机由于转子结构简单,易于实现高速化、效率高等优点,在国防、航空航天、工农业等领域得到了广泛应用。
高速异步机发电机转子导条由于受到电磁力、热应力、离心力、焊接残余应力等综合作用,容易产生松动甚至断条问题是国内外公认的难题。上世纪90年代,我国发电厂所使用的风机、给水泵等旋转机械的高压电动机,经常发生转子断条事故。
原苏联所产某3.15 MW异步电机由于累计启动停机次数的增多、导条结构缺陷、紧固工艺性差等原因造成转子断条比较严重 [2]。国内仿美国西屋公司设计的某3.2 MW高速异步电机在运行3年后转子出现断条现象,平均每3台转子有2台断条,转子两端分别断裂3至5根,部分在10根以上。分析断条原因为:导条在转子槽中无法有效固紧、护环作用不明显、导条和端环焊接工艺参数不合理 [3] [4]。国内生产的某8.2 MW异步电机存在严重的断条现象,载荷侧断裂68处,端环处于临界甩脱状态。分析认为:导条在槽中存在较大间隙(实测为0.5 mm以上),造成导条在槽中产生振动,并且与导条受热弯曲变形应力共同作用于导条根部,导致应力水平高而发生断条 [5] [6]。
王常春团队发明了“双鼠笼型转子防断条结构”、“重载、频繁起动组合型转子防断条结构”、“深槽高速灯笼型转子防断条结构”等专利 [7] [8] [9] [10]。并提出一种特殊紧固工艺,能使导条经过铁心槽时被拉出明显的凸台(类似过模),从而消除与槽壁的间隙被紧固于铁芯槽中 [3]。该发明得到了广泛应用,目前累计制造及改造700余台,效果较好。分析认为异步电动机转子断条的主因有:导条在转子槽中松动、导条伸出铁心长度不合理、端环尺寸不合理。
除对导条和端环结构优化外,文献 [11] [12] [13] [14] [15] 重点对导条焊接工艺及其残余应力改善进行了研究,主要包括:火焰焊、摩擦焊、感应焊、真空钎焊、电子束焊等。结果表明:在钎料与端环的连接界面处存在一定应力集中,通过优化端环结构可改善应力水平。真空电子束焊相比感应焊的导电性更优,焊缝强度高于母材。
导条紧固于槽内是防止断条或松动的有效途径,其次是通过调整端部结构、焊接工艺来改善应力及强度。导条紧固方式有:墩粗胀紧、挤压成形、双导条楔紧、打斜键等,主要为手工操作。文献 [16] [17] [18] [19] 在传统手工墩粗胀紧的基础上,研究自动楔紧方法及工装,通过导条结构优化、冲涨机设计、转子附加槽衬设计,改善了自动楔紧工艺及适用范围,提高了胀紧量。
本文分析不同导条和端环结构的受力特点,并针对某船用高速异步电机转子导条,提出一种导条超速楔紧改进方法以提高楔紧效率,通过力学分析及实测,验证方法的有效性。
2. 高速异步电机转子结构
高速异步电机转子一般由转轴、铁心及压板,导条、斜键及固定环、导条端环组成,如图1所示。
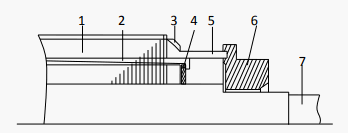
Figure 1. The rotor structure of asynchronous motor. 1. rotor core; 2. Wedge; 3. fix plate; 4. Ring; 5. rotor bar; 6. end plate; 7. Shaft
图1. 异步电机转子结构示意图。1. 铁芯;2. 楔键;3. 压板;4. 固定环;5. 导条;6. 端环;7. 轴
轴采用高强度合金钢锻造,铁芯表面沿圆周方向均匀加工有嵌放导条的槽,固定环与转轴热套并与斜键焊接固定,端环与轴分离,端部导条与端环焊接后构成鼠笼绕组。
2.1. 转子端部受力分析
1) 电磁力
转子漏磁通产生的电磁力指向槽底,其频率为2倍转子电流频率,若导条与槽内为间隙配合,则在电磁力的作用下产生振动,并传递到导条焊接处。
2) 热应力
热应力主要包括:导条自身“挤流效应”热弯曲、导条与铁芯线胀系数差异的热应力、导条与端环热变形差异的热应力三部分。第一部分与导条尺寸及槽高方向的漏抗梯度有关,由于电热损耗造成导条上、下侧温差大,膨胀不均匀引起热弯曲。第二部分为导条与铁心的变形量差异,径向变形差有利于导条在槽内胀紧,但轴向变形差容易导致导条轴向受拉,与铁芯槽产生相对滑动;第三部分受端环的径向热变形差异较大,导条被端环往外弯折。
3) 离心力及扭转力
离心力与转速的二次方呈正比,高速下导条离心力较大,传递给铁芯使得槽口弹性变形增大,从而导条进一步往外移动。导条伸出端部分较槽内部的离心力更大。端环的离心力变形若大于导条时,进一步将导条往外径方向弯折。导条外圆通过护套对抑制部分径向变形,并保护定子线圈。由于电机启动或突然短路下转子产生较大的扭转力矩,此时端环相对铁心扭转,对导条产生较大的切向力。
4) 焊接残余应力
以钎焊为例,转子加热结束后端环从钎焊温度下逐渐冷却,端环因受热产生的弹性变形开始恢复。当温度降至钎料固相线以下后,端环因受到固态钎料的阻碍作用而产生收缩应力。若端环与导条采用环形凹槽连接结构,端环凹槽内、外坡口分别受到拉应力和压应力,凹槽底则受剪力。
2.2. 转子端部结构分析
1) 导条结构
导条中部与铁心槽配合,导条形状有:梯形、倒梯形或矩形等。端部形状与端环的槽配合,形状有平行四边形、矩形、圆形等。当端环槽型与导条不一致,如平行四边形槽与梯形导条配合,则加铜楔焊牢。
导条尺寸优化的参数主要有:导条伸出铁芯量及出铁心端面的导条截面高度。伸出量太小,则护环及端环体积增大,不但对导条没有保护作用,反而增加了惯性力。伸出量太大,其悬臂梁在离心力作用下的反力越大。导条截面高度减小,使得断面系数成平方减少,将引起导条根部这一危险断面的应力增加。截面高度太高,增加了焊接量及工艺难度,并增大了导条及端环的离心力。
此外,采用灯笼型转子可改善应力水平,即将导条压弯嵌入端环的槽中,使护环探入并超过导条的根部,直接对导条的危险断面实施保护,而且导条预制弯曲结构能分散在危险断面作用的应力。
2) 端环等结构
对于双鼠笼转子,导条端部与铁心端面平齐,上、下层导条共用同一端环,此时电流不均匀导致上、层导条的伸长量差异,具体为下层导条受拉伸,上层导条受压缩,容易引起断条。对此采用上、下端环结构能有效降低上下层导条弯曲应力,但增加了导条端部长度,其离心力相应增加,且双环结构的焊接工艺性较差。转子结构如图2所示。
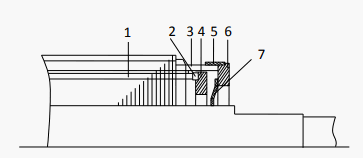
Figure 2. Rotor optimized structure. 1. lower bar; 2. Bushing; 3. upper guide bar; 4. lower end plate; 5. rotor sheath; 6. upper end plate; 7. Bracket
图2. 转子结构优化。1. 下导条;2. 衬套;3. 上导条;4. 下端环;5. 护套;6. 上端环;7. 支架
为减小导条端部离心力下的径向变形,通过加护环或绑扎复合材料加强,同时保护定子线圈。其中,护环的过盈量以及绑扎力需优化设计。
为增加导条端部强度,可在导条根部加衬套,连同导条一并焊入端环孔内,但衬套需要一定的厚度才能起到足够的加强效果,需根据端部空间合理设计。
为防止导条受热伸长,端环与转轴之间的撑环与轴的接触面上配以导键,以保证撑环在轴上自由滑动。若取消撑环结构,将端环与转轴分离,但该结构不能抑制端环相对铁心的扭转力。若在端环与轴之间加支撑环或支架减小扭转变形,该支撑环或支架径向和轴向刚度需合理设计,不能影响导条轴向伸缩变形。
3) 端部楔紧结构
为改善导条应力及转子振动,关键是将导条紧固在铁芯槽内,其次是优化调整导条的伸长量、护环的位置和紧量、端环的截面积等。紧固结构主要分为导条高度和宽度方向紧固。
对于高度方向紧固,一种为楔形导条结构,即将现有导条按高度方向分解成具有斜键效果的两个部分,通过对打实现紧固。另一种为斜键结构,即在导条下部打进一对斜键,从高度方向顶紧导条,然后将斜键紧固在转轴上。高度方向紧固的机理是使得导条通过弹性变形与槽贴紧,但工艺性受部件尺寸及形位公差影响较大,尤其是对于细长形导条,难以保证导条处处紧固,且检验困难。
对于宽度方向紧固,一种为墩粗胀紧,通过专用工装从外部径向冲压导条,使其涨紧在铁芯中,或者打洋冲,在导条上每隔一定轴向间距冲击深约1~2 mm凹坑。另一种为采用圆盘滚子挤压转子铁芯槽口使其收缩变形从而压导条。宽度方向紧固的机理是从径向施加外力使导条或槽口产生塑性变形后贴紧。该方法便于自动化施工,例如某数控导条冲涨机 [16] 实现了导条高效胀紧,如图3所示。但该方法存在工艺参数复杂,质量检验困难等不足。
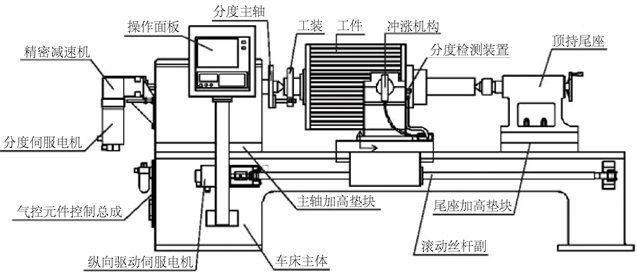
Figure 3. CNC rotor bar expansion machine
图3. 数控导条冲涨机
3. 导条楔紧过程分析
以某船用高速异步电机转子 [20] 为例分析导条紧固过程。转轴和铁心采用高强度合金钢整体锻造,导条槽截面为梯形状,下方为矩形状,转子导条放入梯形槽内,通过槽两侧限位,底部通过斜楔对打施加预紧力。转子截面周向1/28模型如图4所示。
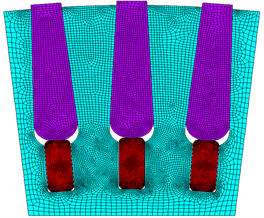
Figure 4. Circumferential 1/28 rotor mode
图4. 转子截面周向1/28模型
其中,斜键截面为矩形,锥度1:200。斜键对打过程中,导条与斜楔单边过盈δ、导条突出槽口量H计算结果如表1所示。各部件之间的接触压力、Mises等效应力曲线如图5和图6所示。
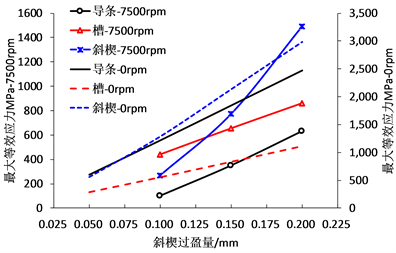
Figure 6. Maximum mises equivalent stress curve
图6. 最大等效应力曲线
计算结果表明:① 楔紧存在空行程(L0 = 10.8 mm,H0 = 0.954),这是由于装配间隙及加工公差所致;② 弹性变形下的斜楔过盈量与导条凸出量呈较好的线性关系,因此可通过测量L和H的值来检验楔紧量;③ 保证高速下斜楔与导条不分离,最小楔紧量约为L = 30.8 mm,H = 1.014 mm;为防止导条屈服,最大楔紧量约为L = 50.8 mm,H = 1.075 mm。
4. 导条超速楔紧方法
导条静态楔紧与实际情况存一定差距,主要原因有:① 加工误差对楔紧一致性影响较大;② 斜键为细长结构,径向接触沿状态沿轴存在梯度,越往铁芯槽中处楔紧效果越差;③ 动态下导条受离心力和热应力进一步产生径向变形。
针对第三点,分析认为随着转速的增加导条凸出槽口量逐渐增加,导条与槽侧壁接触压力增大,导条超速后再打紧斜键能提高预紧效果。
4.1. 冷态超速
冷态下,超速7800 rpm时的导条与槽楔接触压力和变形如图7和表2所示。
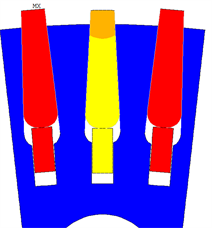
Figure 7. Cloud diagram of contact pressure and deformation under over-speed (7800 rpm)
图7. 超速下接触压力及变形云图(7800 rpm)
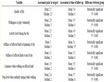
Table 2. Calculation results of over-speed without temperature rise
表2. 冷态超速结果
4.2. 热态超速
热应力分析表明导条与槽的温差或材质线胀系数差越小,则导条与槽的楔紧量越小。热态超速计算结果如表3所示。
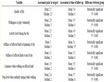
Table 3. Calculation results of over-speed with temperature rise (no temperature gradient)
表3. 热态超速结果(无温度梯度)
结果表明:① 随着温度的增加,ΔH逐渐减小,当温度为140℃时,ΔH = 0.274 mm,相比无温升时的0.328 mm小0.054 mm。② 当导条与槽通风孔的温度不均匀时ΔH进一步减小。③ 理想冷态(0/0℃)超速下的ΔH = 0.328 mm,是理论最大值。实际热态超速不是最恶劣工况,实际冷态(40/40℃)超速下的ΔH = 0.313 mm,该方法比热态超速的楔紧量增加0.039 mm。对此提出冷态超速的楔紧方法。
5. 实验验证及分析
热态超速楔紧试验中,转子无端环,支撑在轴承座上,通过原动机拖动至7800 rpm。期间转子通过风摩损耗受热,安全罩同时起保温作用,超速动成型方案如图8所示。
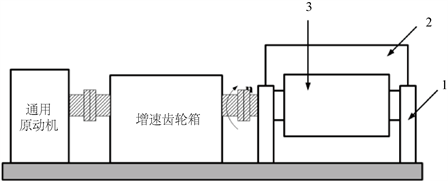
Figure 8. Over-speed scheme. 1. Bearing; 2. Safety cover; 3. High-speed asynchronous rotor
图8. 超速动成型方案。1. 轴承;2. 安全罩;3.高速异步电机转子
冷态超速方法为:拖动转子升速至7800 rpm,中间不做停留以减小转子温升。超速完成后测量转子温度,对打两端斜键,记录导条突出槽口量与前一次斜紧的差值,直至差值趋于0。为对比分析,前第四次均采用热态超速楔紧,至导条突出量稳定在0.05 mm以内(平均0.01 mm),在此基础上,进行第五次楔紧,改为冷态方法。实测导条凸出槽口量明显增加,如图9所示和表4所示。
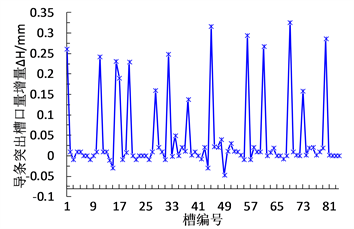
Figure 9. Curve of the difference in the rotor bar protrusion in over-speed without temperature rise
图9. 冷热态超速时导条突出量差值曲线
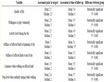
Table 4. Results of over-speed test
表4. 超速试验结果
理论计算第五次相比第四次导条的突出量差值平均为0.039 mm,与实测结果0.033 mm较吻合。
6. 结论
1) 为改善导条应力及转子振动,关键是将导条紧固在铁芯槽内,其次是优化调整导条的伸长量、护环的位置和紧量、端环的截面积、焊接工艺等。导条楔紧工艺受加工误差、斜键结构、导条离心力和热应力的影响较大,需严格控制。
2) 针对动态下导条受离心力和热应力特点,提出冷态超速楔紧方法,仿真结果表明:冷态超速比热态超速的楔紧量增加0.039 mm,与实测结果0.033 mm较吻合,说明该方法能提高楔紧效果,进而有利于降低转子振动噪声。
上述结果为船用高速异步电机转子导条楔紧结构设计提供了有效依据和参考,后续研究将围绕转子精细建模和导条振动分析开展。
NOTES
*作者简介:孙良友(1977-),男,工程师。研究方向:船用高速电机、电力电子技术。邮箱slylk@sohu.com。