1. 引言
一般的,轮对弹性振动模态阶数对车辆动力学影响是不同的。轮对弯曲模态会降低车辆临界速度,而轮对垂弯曲、横弯曲模态对临界速度的影响不大 [1]。轮对的一、二阶弯曲和一阶扭转模态变形会引起较大的轮轨蠕滑力,加快车轮不圆的形成,加重轮轨磨耗 [2]。所以对于重载货车轮对不同模态对车辆动力学影响的研究十分必要。
通过国内外学者研究可知,文献 [3] 认为在轮对一阶弯曲固有频率内,轮轨垂向力的较小波动会引起较大的横向蠕滑,加重轮轨磨耗;文献 [4] 研究发现,轮对的扭转模态和弯曲振动将会造成车轮的多边形磨耗;文献 [5] 等人通过现场测试和数值计算,认为车辆运行时,轮轨间的不平顺会激发轮对一阶弯曲共振,进而导致车轮的多边形磨损,将车轴加粗改造后,轮对弯曲频率提高,并经过线路运营试验和测试分析,发现车轴加粗可以缓解轮对弯曲共振产生的车轮多边形磨损。此外,文献 [6] [7] 也将轮对弹性化处理后,研究了各阶模态与车轮多边形磨损之间的关系。文献 [8] 建立了车辆轨道系统动力学模型和车轮圆周磨耗预测模型,动力学模型中考虑了轮对的第一阶弯曲和扭转模态变形,得出结论,随运行距离的增大,弹性车轮会造成磨耗增加以及恶化车轮非圆化现象。
由上述可知,轮对考虑成柔性体后探究轮对的轮对弹性振动模态阶数对车辆动力学性能的影响是十分必要的,轮对弹性振动模态阶数不仅对轮轨之间有一定的影响,而且与踏面的磨损程度以及车轮非圆化有很大的关系。针对于考虑轮对弹性的重载货车刚柔耦合动力学建模的研究比较少,重载货车在实际运营的过程中,轮对承载较大的载荷,必然会产生弹性变形,所以在研究弹性轮对的基础上,深入挖掘轮对弹性振动模态阶数对轮轨动态作用的影响,确定真实的运行动态性能响应,为货车的日常维护以及检修提供理论依据。
2. 柔性轮对的动力学建模方法
2.1. 柔性体的运动学描述
图1所示为某重载货车轮对模型,建立其绝对参考系为X0Y0Z0。在此基础上,引入相对参考系X1Y1Z1,该坐标系与车轮的运动状态相同,但与绝对坐标系(地面坐标系)始终保持平行。由于柔性体拥有无限多的自由度,所以无法利用连续力学方法求其解析解,故将其离散化,离散成有限个节点,通过节点的自由度来描述柔性体的变形,具体表现形式如下图。
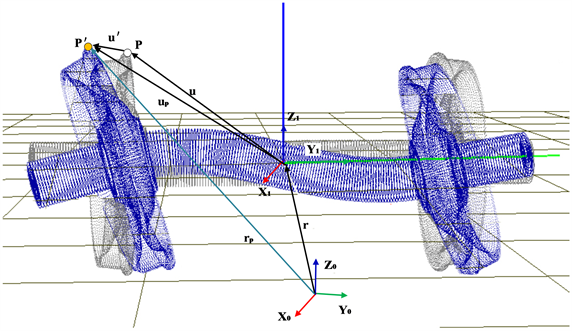
Figure 1. Description of elastomer space
图1. 柔性体空间描述
如图1所示弹性轮对,若两参考系原点的相对位置为r,弹性体上任一点P在绝对坐标系X0Y0Z0和相对坐标系X1Y1Z1位置向量分别为
和
,则他们的关系可表示为:
(1)
式中u为未变形状态下P点的恒定半径矢量;
为P点变形后位移矢量;
为相对参考系发生转动而产生的坐标变换矩阵。
用模态振型叠加表示P点微小的弹性位移
(2)
式中,
为在模态集中提取出与P点相关的模态矩阵;
为模态坐标;N为有限元模型自由度的个数;H为所选模态阶数。
2.2. 轮对柔性体的有限元建模
基于上述理论,本文以某30t轴重重载货车轮对为分析对象,在有限元软件 ANSYS 中建立轮对的柔性体模型。图2为轮对三维模型结构图,图3给出了柔性轮对通过solidworks、HyperMesh、ANSYS等软件进行建模的总体流程。
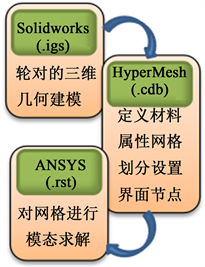
Figure 3. Modeling process of flexible wheelset
图3. 柔性体轮对的建模流程
由于轮对形状的不规则性,应用solidworks绘制出轮对的三维实体模型,导入HyperMesh对其进行网格划分,共有312,845个节点,299,376个单元,轮对采用Solid185三维实体单元,材料的泊松比为0.3,弹性模量为210 Gpa,密度7800 kg/m3。导入到有限元分析软件ANSYS中做柔性化处理(图4) [9]。
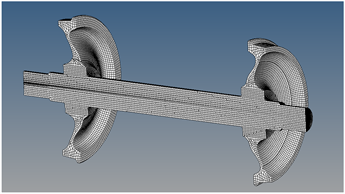
Figure 4. Finite element model of wheelset
图4. 轮对有限元模型
采用Craig-Bampton法求解轮对的本征模态和静模态。对该柔性体模型进行模态综合计算后得到前20阶自由振动模态 [10],由于受到速度的限制,对于高频模型这里就不做过多的研究,而车辆宏观动力学行为的主要能量也集中在低中频,所以这里同样选取300 Hz以下的轮对弹性振动模态阶数模型做研究分析。然后去除前6阶刚性结构,对每一阶模态进行单独求解,完成轮对弹性振动单一模态阶数的建模,进行仿真分析,得到各阶模态模型对应的车辆动力学指标。下图5为单独模态模型及相应的频率。
通过分析可知,图5(a)、图5(c)、图5(f)分别为轮对弹性振动模态阶数沿轨道方向振动模型,对应的自振频率分别为98.84 Hz、172.21 Hz以及274.75 Hz,图5(b)、图5(d)、图5(e)为弹性轮对垂直轨道方向振动模型,对应的自振频率为172.21 Hz、246.94 Hz以及274.75 Hz。通过对比轮对弹性振动单一模态阶数的模型能够了解不同模态阶数的弹性结构对车轮磨耗、车辆动力学以及车辆振动的影响。
2.3. 刚柔耦合动力学模型的集成
将软件ANSYS建好的柔性体模型.rst文件,通过ANSYS _UM接口程序计算轮对的质量矩阵和刚度矩阵生成.fum文件,去除刚体模态后在Wizard of flexible subsystem中生成.fss文件,完成UM柔性轮对的建模,重复此操作即可得到轮对弹性振动单一模态阶数模型,再将求解的模型导入到UM Input中 [10]。建立柔性体步骤如图6所示。
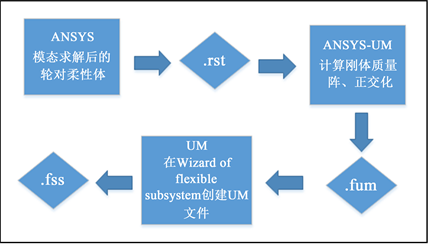
Figure 6. UM wheelset handling process
图6. UM轮对处理过程
将上述完成的UM柔性轮对的有限元模型导入UM Input后,遵循体、铰、力元的规则。柔性体轮对用等效力元模拟轮对与轴箱的连接,其次建立两个6自由度侧架,侧架与轮对之间采用可以模拟具有线性和非线性特性的柔性铰Bushing力元建立连接 [11] [12]。明确各构件的运动、受力及传力状态构成动力学系统。确定车辆的拓扑关系如图7所示,图8为在UM中建立的整车动力学模型。需要指出的是对于轮轨高频振动,轨道的弹性作用不容忽视,因此在模型中将轨道简化为支撑在弹性基础上的梁结构,以此模拟轮轨高频相互作用 [13]。
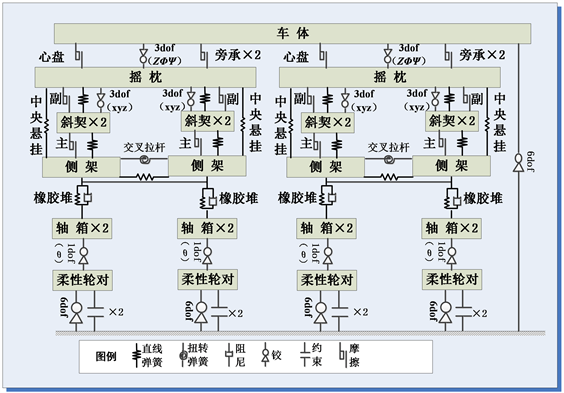
Figure 7. Heavy-haul freight wagon topological relationship
图7. 整车拓扑关系
2.4. 轨道不平顺
事实上由于作业条件、地理环境和技术水平的限制,实际铺设的轨道很难保证完全平直,所有铁路轨道普遍存在不平顺现象 [14]。不平顺是激发轮轨界面接触振动的主要激扰源。在本文研究中,需要激发轮对的中高频弹性振动模态,故需要考虑轨道不平顺中的短波成分,所以在传统的三大干线轨道不平顺的基础上进一步叠加了0.1~1 m波长的短波不平顺成分,以此代表干线及重载专线的轨道随机不平顺状态,各向不平顺如图9所示。
(a) 垂向不平顺
(b) 横向不平顺
Figure 9. Track irregularity
图9. 轨道不平顺
3. 模态阶数间的车辆动力学的影响分析
本节完成轮对弹性振动单独模态阶数对车辆动力学影响的研究。分别对单独模态阶数的轮轨横向力,轮对纵蠕滑力的特性响应作对比,确定轮对弹性振动不同模态阶数间的差异。仿真条件:名义运行速度90 km/h,无坡道、直线轨道,采用LM型踏面和CN75轨。
3.1. 模态阶数模型间的动力学响应对比分析
图10给出了轮对刚性化和轮对弹性振动模态阶数的一位轮对处踏面接触点位置对比图,从图中可以看出,0~5 s时不同模态阶数模型相比较刚性结构的接触点位置呈现较大的跳跃,5 s后车辆进入稳定状态,由于轮对的弹性结构被激发,一阶、二阶模态的踏面接触点带宽总体由−8~23 mm变窄到−5~12 mm,与刚性轮对模型相差大约1/3左右。各阶模态踏面接触点位置对比可知,一阶模态的踏面接触点位置波动范围要比二阶的略大一些,说明不同模态阶数振动变形都可能会对轮轨接触点位置产生很大的影响,但弹性体不同模态阶数间的踏面接触点位置相差无异。总体来看,弹性体不同模态阶数模型的踏面接触点带宽都变窄,会加重车轮与钢轨的磨耗,造成车轮多边形的形成。说明车轮的磨损和车轮多边形的形成与轮对弹性化后的一阶、二阶模态振型可能有较大关系。
(a) 横向振型时域响应
(b) 垂向振型时域响应
(c) 横向振型频谱特性
(d) 垂向振型频谱特性
Figure 10. Time-domain response and spectrum characteristics of wheel-rail lateral forces in different modes
图10. 不同模态的轮轨横向力时域响应和频谱特性
研究发现轮对一、二阶弯曲模态会使轮轨接触点处产生不同程度的蠕滑,而产生较大的蠕滑力,可能会加重轮轨磨耗,造成车轮的多边形磨损。所以研究弹性振动模态阶数对轮轨蠕滑力的影响十分必要。图11为弹性振动模态阶数模型的一位左轮的纵向蠕滑力时域响应和频谱特性,从时域响应可知,总体波动范围在±20 kN,在0~5 s和20 s后,一阶横弯和二阶伞形的波动范围要比其他模态大1/10左右。说明
(a) 横向振型时域响应
(b) 垂向振型时域响应
(c) 横向振型频谱特性
(d) 垂向振型频谱特性
Figure 11. Time-domain response and spectrum characteristics of wheel-rail longitudinal creep forces in different modes
图11. 不同模态的纵向蠕滑力时域响应和频谱特性
在此处两种模态会造成较大的纵向蠕滑力。从频谱特性可以看出,在中高频段纵向蠕滑力的频率幅值出现差异,在频段20~200 Hz、200 Hz以后,一阶横、垂弯相继出现较大幅值。说明一阶横、垂弯会造成较大的纵向蠕滑力,继而会加速车轮与钢轨的磨耗,可能会引发轮对的局部磨耗和车轮不圆的形成。
3.2. 模态阶数模型的动力学响应统计最大值对比分析
通过对图12不同模态阶数轮对处踏面接触点位置波动对比图分析可知,刚性体模型以及一阶模态模型的波动幅度比较小,而较小的踏面接触点带宽,会加剧车轮与钢轨的局部磨耗,可能会引发车轮不同程度的磨耗问题以及车轮失圆的现象。
(a) 左轮踏面接触点位置对比图
(b) 右轮踏面接触点位置对比图
Figure 12. Comparison diagram of the position of contact point of one wheelset tread with different mode models
图12. 不同模态模型的一位轮对踏面接触点位置对比图
为了研究轮对弹性振动模态阶数间的动力学响应差异,图13比较分析了不同模态阶数一位轮对的轮轨横、垂向力统计最大值,如图13(a)所示,轮对为刚性结构的轮轨横向力最大,而轮对柔性化后总体呈现较小值,其中一阶垂弯最小,主要原因是轮对柔性化后弹性振动模态能够较大程度上缓和轮轨作用力,分析图13(b)可知,轮轨垂向力的表现趋势和轮轨横向力相同,同样是刚性体模型最大,一阶垂弯模态次之。说明一阶垂弯模态的结构振动能够较大的缓和车辆对轨道动态作用。所以在建模时,只把轮对考虑成刚性结构会过高的评估轮轨动态作用。
(a) 轮轨横向力对比图
(b) 轮轨垂向力对比图
Figure 13. Comparison diagram of wheel-rail force of one wheelset tread with different mode models
图13. 不同模态模型的一位轮对轮轨力对比图
如图14所示,比较分析了轮对为刚性结构模型和弹性振动模态阶数模型的横、纵蠕滑力统计最大值。通过图14分析可知,相比较轮对的刚性结构模型,弹性轮对各阶模态的蠕滑力都比较大,最大相差1.8 kN。主要原因是弹性轮对的结构振动在轮轨接触点处产生速度分量,导致在计算轮轨蠕滑力时除存在刚性轮对产生的速度分量外,还包含轮对结构振动产生的速度分量,所以弹性轮对轮轨蠕滑力与原来由刚性轮对计算的结果有较大差异。各阶模态模型间相比较可知,图14(a)的纵向蠕滑力较大值出现在一阶、二阶垂弯,最大值达到23.7 kN,其他模态的纵向蠕滑力区别不是很大;图14(b)的横向蠕滑力较大值出现在一阶扭转,最大值到达了25.3 kN,其他模态的横向蠕滑力基本一致。这说明一、二阶垂弯和一阶扭转模态是造成较大蠕滑力的重要原因。所以轮对的柔性化建模能够较真实的反应轮轨作用关系,能够较为准确的给维修人员提供理论依据。
(a) 纵向蠕滑力对比图
(b) 横向蠕滑力对比图
Figure 14. Comparison diagram of creep force of one wheelset tread with different mode models
图14. 不同模态模型的一位轮对蠕滑力对比图
4. 不同速度对弹性振动模态阶数影响分析
为了研究不同速度下的弹性振动模态阶数以及轮对钢性化的轮轨纵向蠕滑力的差异,如图15比较分析了一位轮对在不同运行速度下各阶模态的轮轨纵向蠕滑力统计最大值。如图15(a)所示,不同速度下不同模型表现出的轮轨纵向蠕滑力作用规律不同,图中可以看出各阶模态的轮轨纵向蠕滑力呈现非线性增长,但是弹性轮对建模的轮轨蠕滑力小于刚性轮对建模的,最大值差0.97kN,并且速度的不同也改变了各阶模态轮轨纵向蠕滑力的差值,所以速度能够激发各阶模态弹性结构,从而导致轮轨纵向蠕滑力的变化;通过分析图15(b)不同速度下的轮轨纵向蠕滑力增长率可知,一阶、二阶横弯出现最大增长率,分别为3.97%和6.07%约是刚性化轮对的三倍,通过纵向蠕滑力变化规律可知,速度能够较好的激发弹性轮对的一阶、二阶横弯模态。
(a) 纵向蠕滑力统计最大值
(b) 纵向蠕滑力变化率
Figure 15. The statistical maximum value and change rate of longitudinal creep force of different velocities all the modes
图15. 不同速度各阶模态的纵向蠕滑力统计最大值及变化率
如图16(a)所示,比较分析了各阶模态在不同运行速度时的轮轨横向蠕滑力作用规律,随着运行速度的增加,各阶模态的横向蠕滑力都是随速度的增加呈现非线性增长。并且各阶模态的轮轨横向蠕滑力最大值都比轮对刚性化的大,说明相比较刚性轮对一阶、二阶模态都能使轮轨横向蠕滑力加大,可能会引
(a) 横向蠕滑力统计最大值
(b) 横向蠕滑力变化率
Figure 16. The statistical maximum value and change rate of lateral creep force of different velocities all the modes
图16. 不同速度各阶模态的横向蠕滑力统计最大值及变化率
发车轮的磨耗加重。通过分析图16(b)可知,刚性化轮对模型100 km/h速度下的轮轨横向蠕滑力比60 km/h增长百分比约4.5%。各阶模态间相比较,一阶扭转、横弯模态的增长率较大,分别为10.3%和11.7%。
约是刚性结构的2倍,即速度对各阶模态的轮轨横向蠕滑力影响要大于刚性结构的,相比较各阶模态,速度的改变对一阶扭转、横弯模态影响最大,从而导致两种模态较大的轮轨横向蠕滑力。
图17为弹性振动模态阶数模型的一位左轮不同速度表现出的轮轨横向力作用规律,从图17(a)可以看出,各阶模态模型的轮轨横向力都是随速度的增加呈现非线性增长,且弹性体轮对的轮轨横向力都远小于刚性体建模的,最大值差2 kN,并且速度的不同也使各阶模态轮轨横向力产生差值,所以速度能够激发不同模态的弹性结构,从而导致轮轨横向力的变化。图17(b)为各阶模态不同速度的轮轨横向力增长率,从图中可以看出,弹性轮对模型中最大增长百分比为11.63%。刚性轮对最大增长4.02%,相差约三倍,其中弹性轮对一阶、二阶垂弯模态增长率最大。说明速度的改变能够较大程度的激发轮对弹性结构振动,且在各阶模态中,速度对一阶、二阶垂弯的影响最大。
(a) 横向蠕滑力统计最大值
(b) 横向蠕滑力变化率
Figure 17. The statistical maximum value and change rate of Wheel-rail lateral force of different velocities all the modes
图17. 不同速度各阶模态的轮轨横向力统计最大值及变化率
通过对图18(a)各阶模态不同速度的轮轨垂向力作用规律分析可知,轮轨垂向力同样也是随速度的变化呈现非线性递增,各阶模态模型的轮轨垂向力差距相差无几,所以各阶模态振型之间的轮轨垂向力区别不是很大。分析图18(b)轮轨垂向力速度变化的增长率可知,一阶垂弯模态出现最大变化率,说明各阶模态间的轮轨垂向力改变并不大,对比其他模态,速度对一阶垂弯产生一定的影响。
(a) 轮轨垂向力统计最大值
(b) 轮轨垂向力变化率
Figure 18. The statistical maximum value and change rate of Wheel-rail vertical force of different velocities all the modes
图18. 不同速度各阶模态的轮轨垂向力统计最大值及变化率
5. 结论
本文对轮对弹性振动模态阶数不同阶次模态进行单独建模,通过仿真分析各阶模态对动力学的影响,得出结论如下:
1) 通过对弹性振动模态阶数模型间的时域、频域对比可知,轮对的弹性结构能缓和轮轨横、垂向力,尤其体现在一阶横弯模态和二阶伞形;与此同时一阶横、垂弯模态会产生较大的轮轨蠕滑力,可能是造成轮对的局部磨耗和车轮失圆的一个重要因素。
2) 分析统计最大值可知,轮对的弹性振动一阶模态能够使轮轨作用力有较大的改变。尤其是一阶垂弯,较大程度上缓和了轮轨刚性作用,所以在建模时,只把轮对考虑成刚性结构会过高的评估轮轨动态作用;与此同时一、二阶垂弯和一阶扭转模态会造成较大蠕滑力,可能是导致轮轨磨损的重要原因。
3) 通过分析不同速度对弹性振动模态阶数的影响可知,对比不同模态阶数模型的轮轨蠕滑力,速度的改变对一阶扭转、横弯以及二阶垂弯模态的影响最大;对于轮轨横、垂向作用力,当轮对发生以一阶、二阶垂弯为主的振动时,速度对轮轨横向力的影响较为明显。说明速度的改变对弹性振动模态阶数的影响不容忽视。
基金项目
国家自然科学基金(52072249,11790282);河北省自然科学基金(E2018210052)。