1. 引言
镁合金作为最轻质的金属材料之一,近年来引起了航空航天,交通运输等领域的极大关注 [1] [2] [3]。其中含稀土的镁合金由于其在强度和抗蠕变性能等方面的优势,正取代传统镁合金成为人们新的研究热点 [4] [5]。镁合金在作为结构材料服役时,必然会承受长期的循环载荷,这对稀土镁合金的疲劳性能提出了要求。镁合金的疲劳寿命通常包括三个阶段:应变局域化、裂纹萌生、裂纹扩展三个阶段,在高应力水平下,疲劳寿命以裂纹扩展为主,而在低应力水平下,裂纹萌生占主导地位 [6]。晶界通常是裂纹扩展过程中的主要阻碍之一 [7] [8],而晶界取向差在其中扮演着重要的角色 [9] [10] [11]。Ludwing [12] 通过研究晶界和晶体取向对短裂纹扩展行为的影响,发现如果裂纹扩展路径与目标晶粒的滑动面之间的夹角较大会阻碍扩展。Chao [13] [14] 发现微观结构的不均匀性导致裂纹扩展速率的波动。由于初期的裂纹扩展速率较慢,对于整体的疲劳寿命贡献较大,因此对裂纹早期的扩展过程研究对提高稀土镁合金的疲劳性能十分重要。
由于镁合金具有独特的密排六方结构,这使得其在轧制过程中容易形成明显的织构,而这些织构会对镁合金的疲劳性能产生影响。Park [15] 等研究了各向异性对轧制AZ31镁合金疲劳行为的影响,发现垂直轧制方向样品的疲劳性能优于沿轧制方向的样品,Xiong [16] 等通过研究轧制态AZ80合金的疲劳行为也得到类似的效果。然而目前对于织构的研究大多集中于材料的循环软硬化行为,对于裂纹萌生及扩展规律的研究还比较少。本文通过研究不同织构镁合金的疲劳行为,探明晶粒组织对镁合金早期疲劳裂纹行为的影响规律,为提高镁稀土合金服役性能提供理论基础。
2. 实验材料及方法
通过在Ar气氛保护下的电阻炉中熔化高纯度的Mg (>99.93%),Mg-30 wt.%Gd,Mg-30 wt.%Y和Mg-30 wt.%Zr中间合金来制备名义成分为Mg-6Gd-2.5Y-1Nd-0.5Zr的合金铸锭。用电感耦合等离子体原子发射光谱仪(ICP-AES)测定了合金的实际化学成分为Mg-5.8Gd-2.4Y-0.78Nd-0.45Zr (wt.%)。铸锭在520℃下均匀化退火处理14 h,然后在室温下水淬,切出一部分样品在225℃时效24 h,标记为T6态。另一部分样品在均匀化退火后立刻进行热轧,轧制温度为500℃,每道次压下量10%,总压下量为70%,每道次中间在500℃下退火5~10分钟。轧制后板材在500℃下固溶处理两小时后立刻水淬,随后在225℃时效24 h,标记为T5态。
室温拉伸参考国标GB/T 228.1-2010在DDL100电子万能材料试验机上进行,拉伸速率为2 mm/min。疲劳试样按照GB/T3075-2008设计,其标距长度为10 mm,横截面积为10 mm × 6 mm。为避免加工影响,对样品的表面进行了抛光。在室温下使用电液伺服控制疲劳试验机(SDS100)进行应力控制的疲劳试验(频率20 HZ,应力比R = −1,方向为沿轧制方向)。为了观察疲劳裂纹的萌生和扩展,扫描电子显微镜(SEM, FEI Quanta-200)检查了样品的显微组织和疲劳断裂表面。考虑到疲劳的最后阶段会导致断裂面附近的形态变化,采取疲劳断口下方约800 μm处的试样进行微观结构表征。在观察金相时,将样品抛光,然后使用5 μg柠檬酸,4 ml硝酸和96 μmL乙醇组成的溶液中蚀刻10 s。使用电子背散射衍射(EBSD, Oxford)系统观察疲劳前后样品的晶体取向和织构,使用HKL Channel 5软件处理EBSD结果,以获得极图和晶粒尺寸。
3. 结果与讨论
3.1. 微观组织与力学性能
图1是两种合金的EBSD检测结果,这可以帮助我们了解合金的晶粒组织状态。从图中可以看出,两种合金均呈等轴晶状,由于再结晶退火的作用,在T5态合金中并未观察到如其他变形镁合金中明显的变形晶粒。在取向上,可以看到T5态合金内部红色的晶粒明显增多,晶体取向趋于一致。从极图中也可以看到,T6态合金的晶体取向整体呈散漫分布,表现出随机取向,最大极密度为2.13,而T5态合金则含有明显的基面织构,极密度达到15.65。
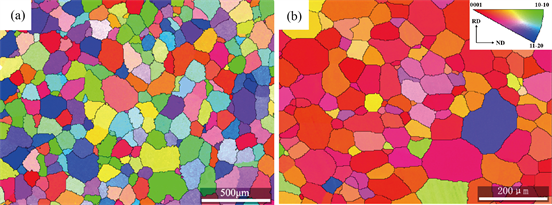
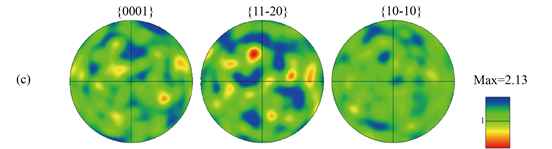
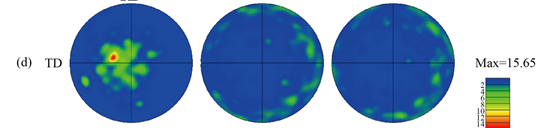
Figure 1. EBSD observation of theMg-6Gd-2.5Y-1Nd-0.5Zr alloys under different structure conditions: (a) Inverse pole figureof T6 alloy; (b) Inverse pole figureof T5 alloy; (c) pole figureof T6 alloy; (d) pole figureof T5 alloy
图1. 不同组织状态Mg-6Gd-2.5Y-1Nd-0.5Zr合金的EBSD检测结果:(a) T6态合金反极图;(b) T5态合金反极图;(c) T6态合金极图;(d) T5态合金极图
图2是两种合金的晶粒组织状况统计图,包括晶粒尺寸分布图、晶界取向差分布图以及施密特因子分布图。T5态合金经过轧制处理后,晶粒组织得到细化,平均晶粒尺寸从92.1 μm降低至50.6 μm。相
较于T6态合金,T5态合金的平均晶界取向差从62.32˚降低到44.01˚,平均施密特因子从0.381降低到0.278。总的来说,T5态合金内部的晶粒组织相较于T6态合金更加均匀,晶体取向趋于一致。由于具有更低的晶界取向差,T5态合金在晶粒间的变形更加协调,而较低的施密特因子则增加了晶粒内部变形的难度。
表1为两种合金的室温力学性能。T5态合金的强度相较于T6态合金略有增加,抗拉强度提升了14.6%,而延伸率提升了70.6%,这些室温力学性能的变化主要与晶粒尺寸的细化有关。图3是两种合金的疲劳寿命曲线图。在107循环次数的条件下,T6态样品的疲劳强度为70 MPa,而T5态样品的疲劳强度为85 MPa,提升了接近20%。由于晶粒尺寸对时效态镁合金的疲劳性能影响十分有限 [17],可以认为织构的不同是影响两种合金疲劳性能差异的主要原因。
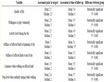
Table 1. Tensile properties of the Mg-6Gd-2.5Y-1Nd-0.5Zr alloys under different structure conditions
表1. 不同组织状态Mg-6Gd-2.5Y-1Nd-0.5Zr合金的室温拉伸性能
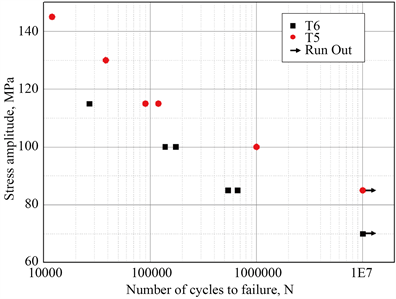
Figure 3. Fatigue life curves of the Mg-6Gd-2.5Y-1Nd-0.5Zr alloys under different structure conditionsunder fully reversed stress mode
图3. 不同组织状态Mg-6Gd-2.5Y-1Nd-0.5Zr合金的S-N曲线
3.2. 表面裂纹及疲劳断口分析
图4是两种合金表面微裂纹的金相照片。图中的微裂纹扩展路径的差异表明的两种合金在组织上的不同。由于具备基面织构,图4(b)中T5态合金的微裂纹大体上呈一条直线,相邻晶粒间的裂纹角度差别不大,而T6态合金的相邻晶粒间的裂纹则具有较大的方向差异。另外,T6态合金中萌生裂纹的数量较多,且在单一晶粒内存在多条平行的微裂纹,相反的是,T5态合金中较少出现次生裂纹,并且很少出现平行裂纹的情况,这说明T6态合金中应力集中的情况要严重得多。
图5是两种合金疲劳断口的扫描照片,其中左侧是裂纹萌生区的宏观照片,右侧为左侧相应区域的放大图片,区域用白色虚线框出。图5(a)是T6态合金的断口照片,在图中并没有发现明显的裂纹传播轨迹,也没有发现明显的夹杂与缺陷。T5态合金有着明显的裂纹传播轨迹,可以看到裂纹从样品左侧表面处萌生,随后向内扩展。整个裂纹扩展区域分布着大量的解离面,而在解离面周围可以看到细小的台阶状形貌。在T5态合金的断口照片中,同样可以看到大量的解离面与台阶状形貌,这种台阶状形貌广泛出现于各类稀土镁合金疲劳断口形貌中。然而,T5态合金的解离面之间的方向相近,台阶状形貌的数量更少,这使得T5态合金的断口显得比T6态合金更加平整,两种合金在断口上的区别与表面裂纹的金相组织照片相似,均来源于两种合金不同的织构。
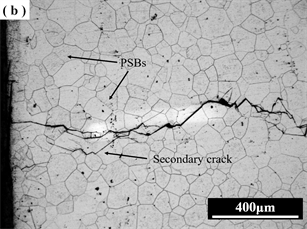
Figure 4. Optical micrographs of small cracks of the Mg-6Gd-2.5Y-1Nd-0.5Zr alloys under different structure conditions (a) T6 alloy σf = 115 MPA, Nf = 26,749; (b) T5 alloy σf = 115 MPA, Nf = 119,408
图4. 不同组织状态Mg-6Gd-2.5Y-1Nd-0.5Zr合金近表面裂纹金相照片:(a) T6态合金;σf = 115 MPA,Nf = 26,749;(b) T5态合金σf = 115 MPA,Nf = 119,408
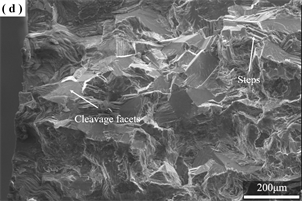
Figure 5. Overall fracture surface and crack initiation site of the Mg-6Gd-2.5Y-1Nd-0.5Zr alloys under different structure conditions (a) (b) T6 alloy σf = 115 MPA, Nf = 26,749;(c) (d) T5 alloy σf = 115 MPA, Nf = 119,408
图5. 不同组织状态Mg-6Gd-2.5Y-1Nd-0.5Zr合金的疲劳断口宏观形貌和裂纹萌生区(a) (b) T6态合金σf = 115 MPA,Nf = 26,749;(c) (d) T5态合金σf = 115 MPA,Nf = 119,408
图6是两种合金裂纹扩展区的放大图片。图中清晰的展示了两种合金由于织构的不同导致的裂纹扩展差异。T6态合金的解离面之间存在明显的边界,而且解离面的尺寸与该合金的平均晶粒尺寸相似,说明这些解离面来源于裂纹沿滑移面扩展形成的截面。值得注意的是,T6态合金的解离面十分光滑,而T5态合金的解离面略为粗糙,这说明了裂纹在T5态合金内扩展遭遇到的阻力更大。由于裂纹扩展与晶粒内的位错滑移开动有关,而T6态合金的晶粒内施密特因子低于T5态合金,导致了两种合金的晶粒内裂纹扩展阻力的差异,这也可以解释两者解离面形貌的差异。在T5态合金的解离面上可以看到明显的河流花样,这些河流花样在经过边界时未被阻碍,说明位错滑移可以通过低取向差的晶界,同时裂纹也容易沿滑移带穿过这些晶界。由于T5态合金具有较强的织构,大部分晶粒的取向相近,使得断口整体显得更加平整。
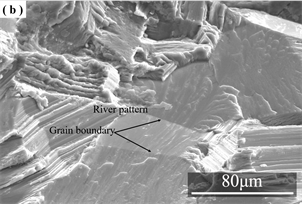
Figure 6. Fatigue fracture ofthe Mg-6Gd-2.5Y-1Nd-0.5Zr alloys under different structure conditions (a) T6 alloy σf = 100 MPA, Nf = 137,962;(b) T5 alloy σf = 115 MPA, Nf = 1,001,601
图6. 不同组织状态Mg-6Gd-2.5Y-1Nd-0.5Zr合金裂纹扩展区域扫描照片:(a) T6态合金σf = 100 MPA,Nf = 137,962;(b) T5态合金σf = 100 MPA,Nf = 1,001,601
3.3. 讨论与分析
在本实验中,两种材料之间的主要区别是轧制过程引起的结构变化。T5态合金具有强的基面织构,这使得合金内部的晶粒取向趋于一致,样品内部的晶界取向差和施密特因子均有所降低。在考虑织构对疲劳过程的影响时,应考虑疲劳过程的两个部分,即裂纹萌生与早期裂纹扩展。在疲劳裂纹萌生阶段,合金内晶粒间的协调变形起决定作用。由于裂纹的萌生来源于应力集中,而更高的协调变形水平可以使晶粒内的应力集中情况减弱,降低合金内部裂纹萌生的数量。由于T5态合金具备的基面织构,晶粒间的协调变形能力更强,这可以从T5态合金的断口形貌及表面裂纹路径看出。在疲劳裂纹扩展阶段,两种合金的裂纹扩展方式均为穿晶扩展,此时的织构则不利于抵抗裂纹扩展。由于位错滑移可以穿过低取向差的晶界,而织构会降低样品内部的平均晶界取向差,这使得T5态合金内的裂纹很容易跨晶界扩展。然而,需要注意的是,由于本实验中加载方向为沿轧向,这对于T5态合金来说,会使得样品内部的施密特因子大大降低,从而提高晶粒内部的位错滑移难度,这也反应在两种合金断口形貌的差异上,如图6所示。因此,T5态合金由于内部存在的织构,获得了更高的裂纹萌生及裂纹扩展寿命,从而在高应力水平与低应力水平下均提高了疲劳性能。
4. 结论
1) 在经过轧制和退火处理后,Mg-6Gd-2.5Y-1Nd-0.5Zr合金在107循环次数下的疲劳强度提高了15 MPa,达到了85 MPa;在104循环次数下提高了30 MPa,达到了145 MPa,织构的变化是疲劳强度提高的主要原因。
2) 基面织构的形成使得T5态合金的平均晶界取向差从62.32˚降低到44.01˚,平均施密特因子从0.381降低到0.278。晶界取向差的降低提高了晶粒间的变形协调性,抑制了裂纹萌生;施密特因子的降低抑制了晶粒内的位错滑移,增加了裂纹扩展阻力。基面织构的形成提高了合金在高应力与低应力水平下的疲劳性能。
NOTES
*通讯作者。