1. 引言
叶轮作为轴流风机的重要部件之一,其机械性能直接关系到风机的运动性能及稳定性,对整个轴流风机的通风性能起到关键作用 [1]。随着城市轨道交通建设项目的不断增多,轴流风机作为城轨地铁车站的主要通风机械,其工作性能和安全性的提高成为迫切解决的问题之一 [2]。轴流风机运行过程中,叶轮周围空气流动将对叶片产生作用力致使叶片发生一定程度的变形,从而导致叶片表面载荷分布的变化。因此为提高轴流风机的工作性能和使用寿命,必须对叶轮与周围流场的流固耦合作用进行分析。国内外学者对叶轮及叶片的流固耦合作用进行大量研究,主要集中在航空工程和风力发电领域 [3] [4] [5] [6]。管德、周盛等人主要对机翼、航空发动机中的气动弹性进行了系统研究,奠定了国内气动弹性理论发展的基础 [7] [8];王伟龙、吕品、杨瑞、张旭等人进行了风机流固耦合等方面的仿真分析,得到了工况条件对叶片载荷分布、变形、模态等方面的影响规律 [9] [10] [11] [12]。目前,国内外的研究主要针对单个叶片,但对于整个叶轮的流固耦合分析较少。
本文采用CFX、Ansys软件基于Ansys Workbench平台对地铁轴流风机叶轮组件进行流固耦合数值模拟分析,得到叶轮的流场计算结果,再将流体产生的表面压力对应地施加在结构有限元模型上,从而获得叶轮在流固耦合作用下的应力及变形分布 [13] [14]。通过与文献中的实验结果对照,验证了叶轮组件有限元模型的准确性,并且根据数值模拟结果提出优化建议。
2. 理论基础
2.1. 流体计算模型
流体系统的运动必须满足质量守恒定律、动量守恒定律和能量守恒定律,而根据这三大定律可得到流体模型计算方程,即雷诺平均N-S方程 [15],数学表达式为:
(1)
式中:
为守恒变量向量;
、
、
为对流项通量向量;
、
、
为黏性项项通量向量。
2.2. 结构计算模型
轴流风机叶轮为多自由度非线性结构,其结构模型计算方程即为结构动力学运动方程 [16],数学表达式为:
(2)
式中,M、C、K分别为结构的质量阵、阻尼阵及刚度阵;
、
、
分别为随时间变化的加速度向量、速度向量及位移向量;
为作用在叶片上面的时变载荷。
3. 流固耦合有限元分析
3.1. 叶轮有限元模型建立
叶轮组件由叶片,轮毂及其他部件组成,具体见下图1所示,各部件材料见表1。由于主要的关注部件为轮毂及叶片,因此对其他零部件进行相应如下简化处理:1) 仅保留叶片及轮毂两零部件;2) 去除紧固的铆钉并填充处理;3) 风机的导风外框。根据导风外框外径和形状,建立相应简化模型如图2、图3所示。
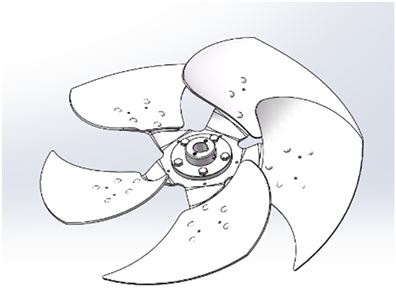
Figure 1. Outline drawing of impeller assembly
图1. 叶轮组件外形图
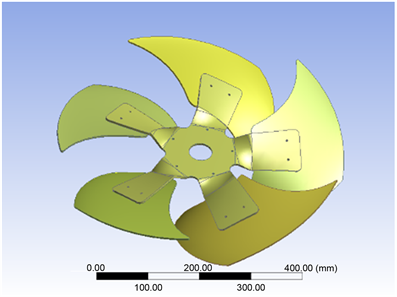
Figure 2. Impeller assembly simplification
图2. 叶轮组件简化
图4、图5给出了风机叶片及流场区域的有限元离散处理过程。流体力学分析对网格质量要求高,因此对旋转域进行网格细分,其中流场区域划分的有限元单元节点数目为6,127,169个,有限元单元网格数目为4,165,283个;叶轮组件划分的有限元单元节点数目为1,574,458个,有限元网格数目为875,568个。
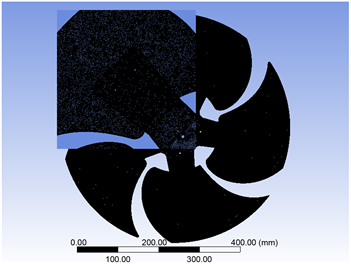
Figure 4. Meshing on the back of the impeller assembly
图4. 叶轮组件背面网格划分
3.2. 叶轮流场仿真分析
根据实际工况,对叶轮流场模型施加边界条件:设置流场入口进风量为6500 m3/h,即入口速度约为7 m/s,旋转域流场转速为1450 rpm,旋转方向为绕Y轴顺时针,出口边界压力相对压强为0 Mpa。
基于流体域模型和边界条件进行仿真计算,得到了流场流线分布图如图6所示,由图6可知气流沿Y方向流进风机入口,气体流速在接近入口处明显增大,并在风机旋转的影响下出现一定的预旋,进入叶轮后随着叶轮对气流的不断做功,气流轴向流动速度不断增大,气流在叶轮旋转域内的流速由顶部到根部沿径向逐渐降低,流速呈阶梯状分布,气流在出口处主要沿轴向螺旋前进。
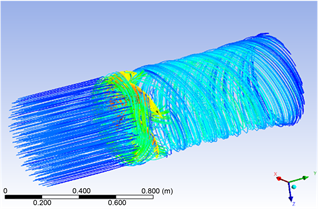
Figure 6. Flow field streamline distribution diagram
图6. 流场流线分布图
叶轮表面压力云图如图7所示,由图7可知叶片后缘受到流场Y向正压力、其最大值为+3.42 × 10−3 MPa,而叶片前缘则受到流场Y向负压力、其最大值为−4.49 × 10−3 Mpa;流场区域中叶片前后缘表面应力值均较大、二者方向相反,这主要和流体因叶片前后缘形状不同而导致其速度分布不同有直接关系。另外通过图7可以发现叶片表面应力在叶片边缘处最大,叶片根部和轮毂处应力最小,应力由边缘向根部沿径向逐渐减小;这是由于在旋转过程中越靠近叶片边缘,气流流速越大,表面局部应力也随之增加,而叶片根部和轮毂处气体流速小且存在边界层分离的现象,表面应力进一步减小。
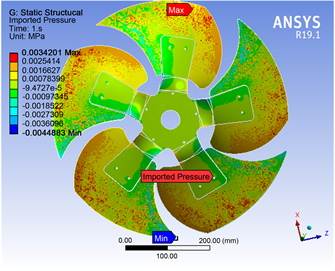
Figure 7. The surface stress nephogram of the impeller in the flow field
图7. 流场中叶轮表面压力云图
3.3. 叶轮结构仿真分析
将流场作用下叶轮表面压力分布结果导入结构强度分析模块,施加+Y方向的标准重力加速度。并且,由于轴流风机工作时,叶轮中心轴处于固定状态,因此对叶轮中心孔施加固定约束,边界条件施加如图8所示。
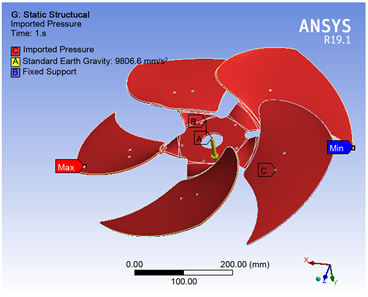
Figure 8. Boundary condition application diagram
图8. 边界条件施加图
通过求解结构动力学运动方程可得叶轮组件的应力及变形云图,如下图9、图10所示。根据图9应力云图所示,最大等效应力67.597 Mpa,位于轮毂部件定位孔处,应力敏感区均匀分布在轮毂根部过度处,虽然低于SUS304的屈服强度,但仍是整个叶轮组件组最危险点,易发生疲劳破坏,这主要是因为在旋转过程中虽然叶片在气流作用下产生一定的表面应力,但是由于表面应力较小,虽可产生一定影响但起不到决定作用,而对叶轮等效应力的大小和分布起到决定作用的是叶轮旋转产生的离心惯性力。根据总变形图10所示,叶片外侧变形最大,变形量均在1 mm以上,最大变形量出现在叶片前缘附近,值为1.521 mm,叶片根部和轮毂处变形最小,变形量甚至接近0 mm,变形从叶顶到叶根沿径向不断减小,这主要是因为在旋转过程中虽然离心惯性力对于叶片变形起到决定作用,但叶片形变也受到气动力一定程度的影响,特别是叶顶受影响最大,因此叶轮在考察形变和刚度时需要考虑流固耦合的影响,而变形量的大小正是离心惯性力和气动力共同作用的结果。
3.4. 实验对照
根据文献 [17] 可知,在实际运行过程中,叶轮断裂裂纹出现在轮毂定位孔处附近,向轮毂根部过度处扩展,最终发生断裂(如图11所示),这与其最大应力位于定位处、应力敏感区位于轮毂根部过度处的仿真分析结果相一致,验证了叶轮组件有限元模型的正确性。
4. 优化建议
为减少叶轮断裂现象,提高轴流风机的可靠性,根据有限元仿真结果,提出以下优化建议:
1) 增加轮毂安装部分板材厚度,提高轮毂安装部分整体强度;
2) 适当增大定位孔直径,减小应力集中系数;
3) 增大轮毂根部过度直径,或对其形状进行优化,减轻轮毂根部过度处的应力敏感性。
5. 结论
本文以轴流风机叶轮组件为研究对象,建立了叶轮组件的有限元模型,分析了轴流风机的流固耦合作用,得出结论如下:
1) 在流体作用下叶片前后缘表面应力值均较大,但方向相反,这可能主要与前后缘附近的流体速度分布不同有关;
2) 在流固耦合作用下叶轮最大等效应力点位于轮毂部件定位孔处,应力敏感区均匀分布在轮毂根部过度处,变形量最大处位于叶片外侧近前缘处;
3) 对比实际运行中的叶片断裂情况,验证了叶轮组件有限元模型的正确性;
4) 可通过增加轮毂安装部分板材厚度、增大定位孔直径、优化轮毂根部过度处形状等途径,提高叶轮组件的可靠性。
NOTES
*通讯作者。