1. 引言
等离子电弧喷涂(Plasma-arc wire spraying)是一种新型的热喷涂工艺,其中电弧既用于熔化阳极金属线材料(自耗电极),也用于加热等离子气体,等离子气体则用于雾化和加速喷涂材料撞击基体形成涂层。该方法具有低成本、高产量、涂层性能优异等特点,广泛应用于航空航天、海洋工程及原子能工程等高科技领域 [1]。
在等离子电弧喷涂过程中,金属线材的熔融与液滴的形成及脱落是影响涂层微观结构和质量的主要因素。而熔滴的脱落频率及脱落半径则主要取决于熔滴和等离子射流之间的相对速度、熔融金属的物性参数及入口流速 [2]。到目前为止,诸多学者建立了带有外阳极金属线的等离子电弧发生器的数学模型,对金属线材在等离子射流中的加热、熔化及尖端金属熔滴的形成与破碎过程进行了大量的研究 [3] - [9]。而在具体操作与应用中,只有了解各种物性及操作参数对熔滴形成过程的具体影响与主次关系,才能对金属熔融液滴的形成与脱落做到准确的调控。因此,有必要对各种物性及关键操作参数在熔形成及脱落过程中的影响规律及影响程度进行更加深入的研究。
本文建立了高速等离子气体驱动下金属熔滴形成与脱落过程的数学模型,对熔融金属的物理性质(表面张力、粘度、密度)以及入口流速对熔滴形成及脱落的影响进行了研究,并分别分析了各个参数影响熔滴形成及脱落的主次程度。所获结论可以为优化等离子电弧喷涂过程提供理论参考。
2. 物理过程与数学模型
2.1. 物理过程
等离子体电弧喷涂工作原理如图1所示。在喷涂过程中,截面半径为
、速度为
的金属线材以垂直于等离子体流的方向向等离子体电弧给进,金属线材的前端连接着电源正极,等离子气流以速度
且垂直于金属线材方向喷出。在靠近电弧中心时,线材前端被高温等离子体射流加热熔化。假设金属线材熔融前沿平行于等离子体流流动方向,并且金属线材熔化速度等于其给进速度。则在金属线材的端头就会形成特性厚度为
的熔融金属层,即金属液膜。随着熔化的进行,液膜变厚,最终从金属线材的端部脱离,如图2所示。
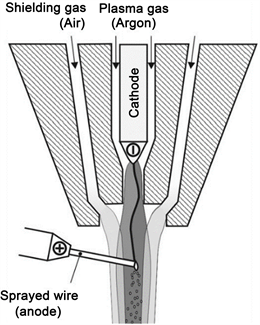
Figure 1. Schematic diagram of plasma-arc wire spraying
图1. 等离子体电弧喷涂工作原理图
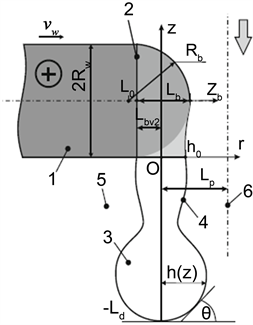
Figure 2. Schematic diagram of molten droplets formed by metal wire under plasma-arc wire spraying
图2. 金属线材在等离子射流下形成的熔滴示意图
图2中,1为固态金属线材,2为熔融前沿位置,3为熔融的液滴,4为熔滴和等离子流交界面,5为等离子流动区域,6为等离子体发生器产生的对称轴线。金属熔滴在高速等离子射流的拖拽力的作用下加速脱落,脱落之后的熔滴在高速气流的作用下发生多次破碎,大直径的熔滴最终形成大量的细小液滴,被加速到达基板形成涂层。
金属熔滴的形成及脱落过程是一个非常复杂的过程,其中不仅有缓慢的流体形态的变化而且有剧烈的流体界面破碎现象发生。此过程中包含了两个主要的阶段,第一阶段为熔滴的形成阶段(drop formation),即金属线材端头的液膜受到等离子体射流的作用熔融,在末端缓慢形成熔滴,并且随着金属液体体积量的增加,熔滴的体积随之增加。当熔滴体积未到临界体积值(由液体的表面张力等因素决定)时,熔滴会稳定地悬挂在末端。当熔滴的体积增大到超过临界体积值时,熔滴的运动开始进入到第二个阶段,即熔滴脱落(drop detachment)阶段,此时熔滴出现颈部,并且在粘性力和重力的作用下熔滴高度
逐渐增加,熔滴最小颈宽逐渐减小,进而形成液线,液线以下连接的部分逐渐发展为球形。计算时当颈缩部位直径小于10−6 m后就认为主熔滴发生了脱离,即液线断开,球形主熔滴发生脱落,而金属线材末端遗留的熔融态液体会逐渐形成下一个熔滴。
2.2. 数学模型
2.2.1. 控制方程
基于以上对熔融金属液滴形成和脱落物理过程的分析,本文建立了二维轴对称模型来进行模拟。假设线材已经达到了熔融温度,且气液两相均为不可压粘性流体,互不相溶,只进行动量交换。则流体动力学控制方程表示如下:
质量连续性方程:
(1)
轴向动量守恒方程:
(2)
径向动量守恒方程:
(3)
式中:μr和μz分别为径向和轴向速度分量,P为压力,ρ是液体金属的密度,μ为液体金属的动力粘度系数。Fz为轴向体积力,其包括重力ρg和粘性拖拽力Fd。
熔融金属液滴内的压力值由下面的表达式确定 [9]:
(4)
式中:
是表面张力系数,单位:mN·m−1,
是外部环境的压力,单位:Pa,K为金属液滴表面处的主曲率,
,可以用以下参数来计算:从点
计算出的液滴表面的母线的圆弧的长度s,单位mm,正切于表面而形成的角度
,单位rad,熔滴横截面的半径h (如图3所示),单位mm。
和
是相互垂直的表面曲率。并且s与
互相关联,它们之间的函数关系为 [9]:
(5)
由于等离子气体的速度很大,通常为100~800 m/s,等离子气体的流动状态为湍流,而金属熔滴的初始速度较小(0.1~4 m/s),所以在交界面处的粘性拖拽力不能忽略。通过对数近壁函数可以推导出粘性拖拽力的表达式如下:
(6)
式中:
为等离子体与金属液体的速度差的平方,Kar是卡曼常数,取0.44,E是壁面粗糙度,对于光滑表面时取8.8,
为距离壁面的无量纲高度,本文取值400 [10],由此可以将上式简化为:
(7)
将切应力化成轴向方向的体积力的形式,其表达式如下:
(8)
式中:r为熔滴的横截面半径,单位mm。
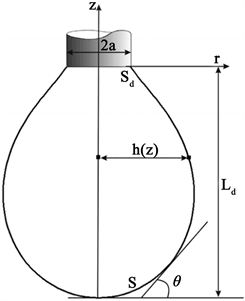
Figure 3. Diagram of curvature calculation
图3. 曲率计算示意图
2.2.2. 网格划分及边界条件设置
文献 [11] 使用VOF方法对于在自然条件下液滴滴落过程的自由表面进行了追踪计算,并与以丙三醇溶液为研究对象的实验过程进行对比,证明了VOF方法的可行性。本文同样采用VOF方法来模拟熔滴形状变化过程。本文计算域及网格划分见图4。
图4中,1,3为等离子体流的速度边界条件入口;2为熔融金属液滴速度边界条件入口;4,5,6为压力边界条件出口;7为各处压力参考点。在计算区域中将金属线材前端部分设置为速度入口边界条件(velocity inlet),金属液滴脱落方向的界面和周围气流的界面设置为压力出口(pressure outlet)边界条件(压力为标准大气压力)。将几何区域的对称轴设置为对称边界条件,该边界条件上物理量的径向梯度为0。
3. 结果与讨论
基于上述数学模型,本文分析了熔滴的表面张力、动力粘度、密度以及入口处熔融液滴的流速等物理量对熔滴形成及脱落的影响。
3.1. 不同工况下熔滴的形成过程
为了分析液态金属的物性以及初始速度对于熔滴脱落过程的影响,本文设置了八种不同的工况,详细参数设置见表1。设定金属线材入口端口半径为0.184 mm,表面张力系数范围为0.4~1.4 N/m;密度范围为5600~7860 kg/m3;动力粘度范围为0.004~0.008 Pa·s;决定金属熔滴的入口初始速度的因素很多,包括等离子气体的速度、金属线材前端在电弧中的位置以及金属线材的物性等等,本文引用Kharlamov [6] 的计算结果设定熔滴的入口初始速度。
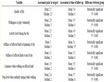
Table 1. Eight different working conditions
表1. 八种不同工况的参数设置
图5为8种工况下熔融金属线液滴的形成与脱落过程。如图所示,各工况下金属熔滴的形成过程类似,初始阶段金属线材前端在等离子射流的作用下熔化形成熔滴,随着金属液体体积量的增加,熔滴的长度不断增加,体积不断增大。当熔滴的体积超过临界体积值时,在表面张力作用下熔滴开始出现颈部,颈部区域半径的缩小导致熔滴颈部的拉普拉斯压力与等离子射流的粘性拖拽力增大,从而使颈部液体加速流向主熔滴,直至颈部半径缩小到临界值时主熔滴发生脱落。
对比图5中8种不同工况下熔融金属线液滴的形成与脱落过程可知,当工况不同时,主熔滴的最终形成时间与脱落半径也不同,后文重点分析在其他参数不变时改变各个单一参数设置对主熔滴形成时间与脱落半径的影响。
3.2. 表面张力的影响
表面张力系数是表征表面张力大小的物理量,是讨论液滴的表面现象、了解液滴性质的重要物理参数,它与温度、压强、气相或液相组成以及液体种类等均相关。图6所示为不同表面张力系数下金属熔滴形状对比图,分别截取自图5中的工况(3)、工况(2)与工况(1)。其中熔滴入口处的流速为1.45 m/s,熔滴密度为7200 kg/m3,动力粘度保持0.006 Pa∙s不变。
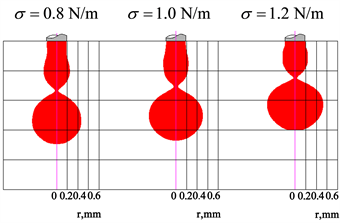
Figure 6. Molten droplet shape contrast under different surface tension coefficients
图6. 不同表面张力系数下熔滴形状对比
从图6中可知,不同表面张力系数下金属熔滴的形状有所不同。由于表面张力对熔滴的表面产生一个相当于向内的拉力的作用,因此,当表面张力系数增加时,熔滴的表面受到的拉力增加,阻碍了熔滴的下降,使熔滴形成时间增长,从而有更多的金属液体可以流入主熔滴内部,因此随着表面张力系数的增加,主熔滴半径也有所增加。
从数值上看,当表面张力系数由0.8 N/m增加到1.2 N/m的时候,主熔滴的体积增加约14.6%,而熔滴形成时间增加了26.3%,从这个角度出发,表面张力对熔滴形成时间的影响要略大于其对主熔滴半径的影响。
3.3. 动力粘度的影响
表面张力和动力粘度在金属熔滴的形成及脱落过程中起着非常特殊的作用,熔滴的形态在两者的共同作用下产生变化。图7是三种不同动力粘度下的熔滴形状对比图,分别截取自图5中的工况(5)、工况(1)与工况(4),其中熔滴入口处的流速为1.45 m/s,熔滴密度为7200 kg/m3,表面张力系数为1.2 N/m。
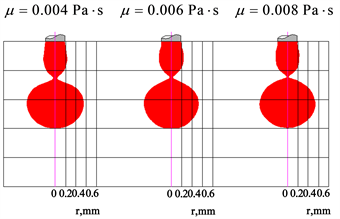
Figure 7. Molten droplet shape contrast under different dynamic viscosity
图7. 不同动力粘度下熔滴形状对比
如果不考虑表面张力的作用,那么随着金属液体动力粘度的增加,液体内部的粘滞力会逐渐增加,阻碍液体下落,导致熔滴的形成时间逐渐增加;同时由于粘滞力的增加,熔滴在颈缩处所能承受的最大拉力也随之增加,意味着可以承受更大体积的熔滴,因此主熔滴的半径也会逐渐增加。由此可知,金属液体的表面张力和粘度在各自单独产生作用的时候会对熔滴的形态产生相同的影响。不同的是,表面张力对于熔滴形成及脱落的影响要明显大于动力粘度,如图6与图7所示,在熔融金属线液滴的形成及脱落过程中表面张力的作用处于主导地位,动力粘度的影响较为微小。
3.4. 密度的影响
图8是在两种不同的密度下熔滴最终脱落前的形状对比图,分别截取自图5中的工况(8)与工况(3),其中金属液滴入口处的流速为1.45 m/s,表面张力系数为0.8 N/m,动力粘度为0.006 Pa∙s。
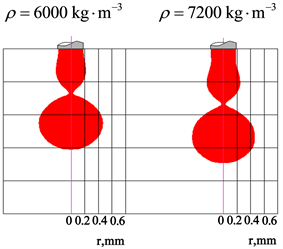
Figure 8. Molten droplet shape contrast under different densities
图8. 不同密度下熔滴形状对比
在实际生产应用中,添加了其他不同密度的材料会使金属线材的密度发生改变,从而对熔滴的形成与脱落过程造成影响。由图8可以发现,随着金属线材密度的增大,主熔滴的长度增大并且其成型半径也稍有增加,熔滴的形成时间则相应减少。
3.5. 入口流速的影响
在等离子体电弧喷涂过程中经常通过控制入口流速来控制液滴生成及脱落。图9显示了不同入口流速下熔滴即将断裂时的形状对比,分别截取自图5中的工况(7)、工况(1)与工况(6)。其中熔滴的密度为7200 kg/m3,表面张力系数为1.2 N/m,动力粘度为0.006 Pa∙s。
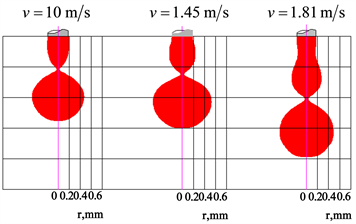
Figure 9. Molten droplet shape contrast under different inlet flow rates
图9. 不同入口流速下熔滴形状对比
从图9中可以看出,随着入口流速的增加,主熔滴的长度明显增长,熔滴形成所需要的时间逐渐减少,而主熔滴的成型半径有所增加,但变化不大。从数值上分析,当入口流速从1.0 m/s增加到1.81 m/s时,主熔滴的半径增加了约42.9%,熔滴的形成时间减少了38.9%。这说明相比于表面张力系数和粘度,入口流速对于熔滴的形成具有更加显著的影响。
4. 结论
本文对高速等离子气体驱动下金属线材熔融液滴在不同工况下的形成及脱落过程进行了数值模拟,并分析了相关物性(表面张力、动力粘度、密度)以及金属熔滴入口流速对熔滴形成及脱落的影响。通过分析得出以下主要结论:
1) 表面张力和动力粘度与熔滴的形成时间和主熔滴的脱落半径成正相关,其中表面张力处于主导地位;
2) 金属线材的密度和熔滴入口处的流速与主熔滴的长度及脱落半径成正相关,与熔滴的形成时间成负相关,且入口流速的影响更为明显。
NOTES
*通讯作者。