1. 引言
学术界对布局的优化有不少应用研究,本项目认为有缩短生产周期,减少空地,减少物料的停留、搬运和库存,可以释放产能。基于鱼骨图 [1],对其工艺流程与车间现状分析得出如下问题:车间物流路径多有回流且移动距离过长,产品工序又较多,各产品路径混杂不清晰;暂存区较多,且每个暂存区内都堆积很多产品,搬运不及时,导致通道拥挤;车间内有许多废弃设备未及时清走,占用较多面积,问题设备未及时修理。系统布置设计方法(SLP) [2] 是工艺专业化布局时常用的方法,缪瑟 [3] 提出系统布置设计(SLP),车间布局规划正式成为一门具有学科方向和技术体系的学科。如今,SLP由当初的按经验做事到定量分析再到有自己专门的知识体系和特有符号再到如今和建模仿真和算法 [4] 联系到一块,发展的越来越好。布局优化也不只应用在制造业 [5]、学校 [6]、超市 [7] 以及物流电商 [8] 都可以应用到。
本文综合运用了SLP布局 [9] 的方法与Flexsim仿真模型 [10],通过对YK企业遇到的实际问题出发,找到实际有效的解决方法,以达到为企业增加利润创造营收的目的。
2. YK工厂案例分析
YK公司是一家致力于再生塑料的回收、再生和应用的高科技制造和循环经济企业。专业生产环保画相框线条、环保成品框、PS塑料仿木框条等装饰材料。目前由于疫情影响,YK企业七八月份的订单激增,外加要与某大型跨国家居用品企业达成合作意向,搬运成本、设备空间不足等问题日益突出,库存严重影响了生产效率等一系列问题。根据长远考虑,改善工厂的布局变的尤为重要(工厂南北距离100 m,东西距离180 m)。
2.1. 主要产品工序分析
根据YK公司2018年下半年到2019年上半年一年的销售清单和物料清单,找出很少的几种产品,但是其需求量却大到需要为它们建立专门的生产线。通过计算分析M0393-MP、M0508-MP、M0016KC-MP、M0782KC-MP且尺寸为11 × 13英寸的喷漆像框占比超过70%为喷漆像框主产品。随后,对这4种喷漆像框进行流程分析。其喷涂相框的流程见图1。
通过流程分析可知喷漆像框主要产品物流路线为2000.8 m。由于喷漆像框组装线产能不足,需要进行东西厂调拨,增加了物流成本,所以可以平衡产线增加喷漆像框组装线;同时,由于工厂设备集群的原因,像框排切高频等工序需要去200米以外二期高频设备上进行加工,搬运距离较远,为减少搬运,由设备集群改为产品集群。
2.2. 工厂布局分析
由于工厂仓库摆放托盘为四层四列紧密式摆放,不方便叉车取货,应改为三层留有通道式的摆放模式。根据当前的销售量以及未来的订单预测,原材料仓库应为150 m2。
根据订单需求及产能,该工厂日生产像框2800箱,因为每天的产品都要当天入库及验收,由于货物堆放太高会造成安全隐患且不利于叉车运输,所以规定使用规格1.4 m × 1 m × 1.2 m的托盘叠放三层,工厂采取抽样是验收,所以验收区域经计算采取15 m2区域即可。
考虑叉车出入问题及工人流动问题,设置主物流通道为3 m,不走叉车的物流通道为1.5 m (可以走2个人的距离),产线与产线的物流通道为0.8 m (可以方便产线检修的距离)。工人上班时间规定为早8:00到晚8:00午休吃饭时间1个小时。
工厂的占地面积为18,000 m2左右,生活、办公区域约占80 m2,托盘的存放面积为2262 m2,另外为了增加产品的多样性,增加企业市场竞争力,新增铝合金产线区域和白坯帆布画区域1606.53 m2,总作业区域11,998.8 m2,面积利用率为66.66%。
3. 管理模式改善
3.1. Y工厂管理现状
Y工厂现状是每个的车间各自为政,车间之间的沟通联系基本没有,车间与车间之间都是断点,管理人员没有配套成套的概念,都在为了自己车间的业绩,抢地盘似的生产。整个工厂被各自车间分成了4个区块,孤岛似的生产,导致各个车间的产能不匹配,管理成本也会造成浪费。
3.2. 成套库的管理模式
通过SLP规划设计的布局,设计了可以储存2天产能线边库,要求定位定容定存,减少丢料缺料的现象发生。并且针对YK企业管理各自为政的问题,设立了成套库的管理模式。设立成套库 [11],以成套库为核心进行拉动式生产,让原先散乱,各自为政的自制车间,在组装车间之前成套的流动下去,保证了组装车间的生产不停产。并且给YK企业的管理者提出了产品工艺的整体流程的概念,用整体流程穿各自车间按照计划去行驶,以成套库建立为核心,建立拉动式生产,以计划部制定计划定拍工序,再组装。组装开始定拍工序前面拉动自制后面进行包装工序推动工序和组装工序推动式的生产。建立了拉动式的定拍生产见图2。
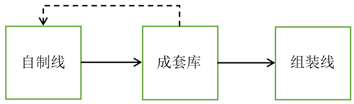
Figure 2. Pull production drawing of complete set warehouse
图2. 成套库拉动式生产图
自制线以每件产品为一套进入成套库,然后成套库在计划部的计划下进去组装线组装。成套库还可以通过库存反馈给自制线,拉动自制线的生产。
4. 基于SLP的布局规划
SLP方法是一种将物流分析与功能区之间关系密切程度分析相结合以求得合理布局的技术,在布置设计领域得到了广泛的应用,相对于一般数学模型法,其对影响因素的考虑更加全面,并将影响因素定量化 [12]。
由于该设计方法通常会利用表达性较强的图例符号或表格来总结作业单位间的物流强度与关系,会将彼此间物流强度较大的作业单位尽量安排在相近的位置,因此能够有效降低不同作业单位间物流运输成本与效率,在工艺专业化布局中十分常见,而基于SLP方法对车间设施的布置优化展开探究,自然也是十分必要且具有现实意义的。
SLP方法最初是从“工厂设计”逐渐发展而来的,主要针对工厂、车间内部的平面布局设计与车间设备布置,能够设计出最为简捷的物料搬运路线,在提高车间内部空间利用率、生产资源利用率的同时,简化车间流程,而要想将在实际设计中对SLP方法进行灵活应用,则需要车间工艺路线情况展开分析 [13]。从目前来看,主要产品喷漆像框的交叉物流严重,搬运距离造成的浪费过多。
4.1. 各作业之间物流强度与非物流强度分析
物流关系分析主要是工艺流程分析,是设施布局的前提。各条路线上的物流移动量就是反映工序或者作业单位之间相互关系密切程度的基本衡量标准,一定时间周期内的物料移动量成为物流强度。
当量物流量:物流运动过程中一定时间内按规定标准修正、折算的搬运和运输量,计算公式:
(1)
F——当量物流;q——每个标准搬运单元的当量;n——单位时间内两设施间流动的标准单元数。
通过计算得到各个作业之间的物流强度,并且划分个作业之间的等级,A、E、I、O、U,强度依次降低见表1。
通过各等级的关系最后列出各个作业的物流强度关系图:非物流关系的密切程度用A、E、I、O、U评定,强度依次降低。意义划分为:绝对重要、特别重要、重要、一般、不重要、不靠近。经过实际的研究评定,制定出各个作业流程。
进行设施规划时,非物流关系也对整个作业流程有很大影响。通过参考工厂一线员工的工作,制定非物流关系的评价标准,具体如下:1) 作业设备的共享性,连续性;2) 环境关系;3) 作业流程的连续性;4) 各作业之间的员工工作的联系密切程度见表2。
注:1:原料库、2:电脑裁板、3:仓库、4:四面刨、5:线边库、6:涂装机、7:晾干、8:排切机、9:高频、10:定厚砂光、11:喷漆、12:喷涂晾干、13:异形、14:线边库(发东厂)。
通过物流关系分析6工序到7工序的物流强度高,应该尽量是这两道工序距离变近,减少搬运距离,1、2、3、4工序物流强度低,可以不优先考虑这几道工序之间的物流距离。其余工序物流强度适中,在满足6、7工序的前提之下尽可能减少工序之间的物流距离。
4.2. 综合相关性分析
进行综合分析需要先确定物流关系与非物流关系的权重,经过在工厂调研,工厂作业中物流关系占主导地位,非物流关系只占辅助地位,所以确定物流关系与非物流关系的权重比值为3:1,通常设置等级取值A = 4,E = 3,I = 2,O = 1,U = 0,X = −1。根据各功能区之间的物流关系和非物流关系,得到综合相关图见表3、见图3。
通过综合相关关系图分析排切和高频组装之间、砂光区域和喷漆区域的综合强度最高,等级为A,布局分析时尽可能减少之间的搬运距离,可以极大减少搬运上的浪费。四面刨和涂装区域、半成品库和成品组装区域的综合强度为E,进行布局分析是在满足工厂实际条件下缩短工序之间的物流距离。其余根据A、E、I、O、U、X的等级依次在满足等级高的条件下减少工序之间的距离,减少搬运。
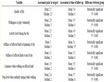
Table 3. Comprehensive relationship table
表3. 综合关系表
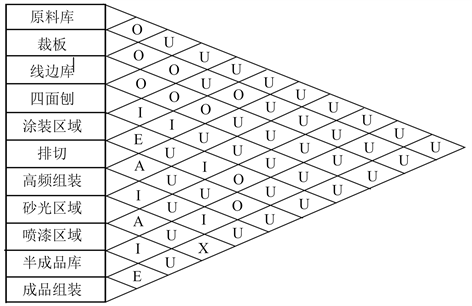
Figure 3. Comprehensive correlation diagram
图3. 综合相关关系图
4.3. 线性关系图分析
根据综合相关图制定的强度等级,绘制物流与作业单位的相互关系图,用图例、符号、数字、颜色画出各个作业单位之间的相互关系。绘制时不考虑作业单位的实际位置和作业单位所需要的面积,各个作业单位之间的密切程度用线条的多少对应等级符号来表示。根据YK企业要求的喷漆不能动的前提,绘制出的线性关系图见图4:
根据线性关系图并且结合工厂实际画出经过SLP布局之后的CAD图纸见图5:
5. 3D仿真及改善成果分析
5.1. Flexsim参数设置
1) 发生器参数设置:根据实际测量数据,包括发生器到仓库的距离和订单统计时间,发生器1、2的时间都为1.29 s/个。
2) 叉车数据:作业时间5 min。
3) 根据暂存区的不同托盘数量也有不同,板条暂存区:12个托盘,四面刨暂存区:5个托盘,高频养生暂存区:12个托盘,涂装暂存区:20个托盘,砂光暂存区:18个托盘,半成品库:36个托盘。
4) 货架参数:层数为3层,列数为10列。
5) 处理器时间根据实际作业时间设定,涂装机的工作时间为3.28 s/个,砂光线的工作时间为3.16 s/个,静电线的工作时间为3 s/个,排切机的工作时间为3.6 s/个,高频组装的工作时间为3.6 s/个。
6) 合成器的加工时间为3~8 s/个。
5.2. Flexsim仿真和3D建模
为验证方案的可行性,通过flexsim仿真软件 [14] 仿真方案的布局。仿真展示见图6。
通过运行仿真模型,可知道在实际生产中1天的库存及每天生产的成品,方便与改善前做出对比。
利用3D软件进行空间比例1:1的比例进行空间模拟,对产线,线边库的摆放和叉车的装货周转进行空间上可行性进行确认。3D展示见图7。
通过3D图可知布局的合理性,直观表达出规划布局的优缺点。
5.3. Flexsim仿真和3D建模结果分析
仿真模型运用10 h,即36,000 s,点击运行,对仿真模拟开始分析,主要对设备情况加以分析。
改善后通过对布局的调整,管理模式的改善,从仿真中可看出暂存区的拥挤率见图8:
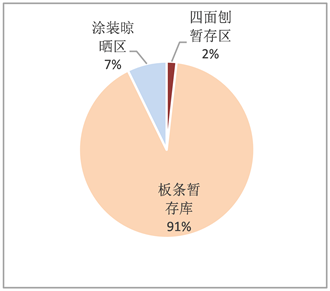
Figure 8. Congestion rate of temporary storage area after improvement
图8. 改善后暂存区拥挤率
从改善前的各个作业区间线边库杂乱变成只有3个位置的暂存区存在拥挤现象,改善后只有板条暂存库的拥挤率为91%,对比改善前大大降低,减少了各个作业期间的暂存区拥挤问题。
通过仿真报告,可分析出改善后喷漆像框产能为7684个/天,包覆像框产能为29,975个/天,总产能为37,659个/天,对比改善前喷漆像框产能增加1684个/天,包覆像框产能增加5975个/天。
6. 总结
本案例运用了设施规划与物流和工业工程的基础知识,通过各个产品的流程分析,以产品贯穿流程,通过SLP布局的方法规划布局作出了改善,叉车电拖工人减少了5人,货车调拨司机减少2人每日节约了2800元物流成本。工厂日产能从6000个喷漆像框,20,000个包覆像框增加到7684个喷漆像框,29,979个包覆像框,面积利用率增加了13.33%,增加两种新产品的产线,改变了仓库管理模式,以成套库进行拉动式的生产。导入了产品工艺的整体流程的概念。用整体流程穿各自车间按照计划去行驶,以成套库建立拉动式生产,拉动前自制车间往成套库去流动,增加了产线平衡率,缩短了产品制程周期,释放了产能;节约的物空间面积安排新的产品及组装线,可见,产能的提升不一定是设备的增加,可以通过布局优化等现场管理提升产能。