1. 引言
根据我国中长期油气管网规划,2025年我国计划建设的长输管线总长将达到24万公里,其中天然气、原油、成品油管道里程数分别达到16.3万公里、3.7万公里、4万公里。截至2019年底,我国已建油气管道总长超过14万公里,其中天然气管道约8万公里,管道约3.5万公里,成品油管道约3.0万公里。随着油气管道输量和运距的不断增加,管道建设越来越多地使用了大口径(如1219 mm、1422 mm)、高钢级(如X70、X80)的管线钢管,即油气管道向高钢级、高压力、大口径的趋势发展。焊接作为管道施工中的重要环节,在管道工程的施工和安全运行中扮演着重要角色 [1] [2]。
目前,高钢级大口径管道工程的焊接施工方式以自动焊为主,该焊接方式应用的主要目标是提高焊接质量稳定性和一致性。为达到这个目标,作为焊接施工的重要原材,钢管的力学性能与几何尺寸等是影响焊接施工质量的重要因素。本文从4个方面阐述了为了保障自动焊环焊缝质量,在钢管技术条件方面建议采取的设计提升措施。
2. 提升方向
2.1. 关于钢管化学成分
2.1.1. 关于钢管合金元素含量限定
对于管线钢这种热轧钢,为了获得高强度、高韧性和良好的焊接性,其化学成分设计是在C-Mn-Nb微合金的基础上,添加适当的Cr、Ni、Mo等合金元素。而这些合金元素的含量对钢管强韧性能的优化也起着至关重要的作用 [3] [4]。目前不同国家关于钢管的设计标准中,如GB/T 9711《石油天然气工业管线输送系统用钢管》和API Specification 5L,对钢管部分合金元素含量波动范围较宽泛,而这些元素往往对焊接质量,特别是环焊缝的断裂韧性影响较大 [5]。以Ni、Mo和Cr元素为例,如图1所示,虽然都满足相关标准要求,但不同钢厂同种合金元素含量波动较大,影响钢管化学成分的稳定性,进一步影响焊接质量的稳定性。



Figure 1. Statistics of alloy element content of different manufacturers
图1. 不同厂家合金元素含量统计
对Ni、Mo和Cr三种合金元素与C、Si这些元素的离散程度进行对比,如图2所示。可以看出合金元素Ni、Mo和Cr含量的离散性要远远高于C和Si。

Figure 2. Element dispersion statistics
图2. 元素离散度统计
跟各个国家的国标相比,各个国家的企业和工程标准要相对较严格。以Ni、Cr和Mo为例,由表1~3可以看出,这些标准的要求均要严于其国标,同时有的企业标准中还以钢管壁厚作为划分依据,不同壁厚,同种合金元素含量要求不同,是不同规格钢管的生产和性能的综合体现 [6] [7]。这也是在工程钢管设计上值得借鉴和学习的。
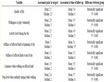
Table 1. Statistics on the requirements of X65 steel alloy elements in different enterprise or engineering standards
表1. 不同企业或工程标准中对X65钢级合金元素要求统计
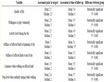
Table 2. Statistics on the requirements of X70 steel alloy elements in different enterprise or engineering standards
表2. 不同企业或工程标准中对X70钢级合金元素要求统计
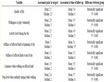
Table 3. Statistics on the requirements of X80 steel alloy elements in different enterprise or engineering standards
表3. 不同企业或工程标准中对X80钢级合金元素要求统计
因此,针对不同企业和不同工程的具体情况,为了优化钢管的化学成分,收窄合金元素含量的波动范围,提高现场焊接环焊缝的力学性能稳定性,在设计文件中对于这些合金元素含量的波动范围应进行限定。经过限定后,如图3所示,可以看出Ni、Mo和Cr这些合金元素的波动范围有所缩窄。经统计,如表4,Ni、Mo和Cr元素含量波动范围分别缩窄了0.022%、0.065%和0.033%,元素含量缩窄率分别约为15.6%、41.9%和18.9%。



Figure 3. Statistics of the content of alloying elements of different manufacturers after being restricted
图3. 不同厂家合金元素含量经限制后的统计情况
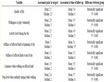
Table 4. Statistics on the narrowing of alloying element content range
表4. 合金元素含量范围缩窄情况统计
2.1.2. 关于感应加热弯管碳含量及Pcm的限定
用感应加热方式生产的弯管,其管材的金相组织、强度、冲击韧性及可焊性等均会因钢管的二次加热发生变化,感应加热弯管母管的化学成分、质量性能对热弯工艺及最终弯管的性能有着重要影响 [8] [9]。一般来说,感应加热弯管与线路用钢管在化学成分上的差异主要体现在碳含量上,其余合金元素的差异主要体现在碳当量上,而这两个指标对钢管的焊接性影响显著。通过对收集的X65、X70和X80感应加热弯管的碳含量和碳当量进行统计可以得出(如表5所示),目前企业标准中对于感应加热弯管的碳含量和碳当量规定范围较宽。通过数据统计,结合各钢厂的生产情况,从设计上可以继续加严这两项指标,以更好的控制感应加热弯管的现场焊接质量。
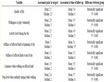
Table 5. Statistics of carbon content and carbon equivalent of induction heating bend
表5. 感应加热弯管碳含量和碳当量情况统计
2.2. 关于钢管强度
2.2.1. 钢管屈服强度区间的限定
为了更好了使焊材和母材进行强度匹配,对钢管母材的拉伸强度波动区间进行限定是目前设计中对钢管技术条件要求的重要一项内容。关于钢管拉伸的强度波动区间,一般各个国家标准中的要求较为宽松,但是其企业或工程标准中对钢管拉伸强度区间,特别是对屈服强度区间的限定较为严格。图4统计的是相关的企业和工程标准中对X65、X70和X80等级钢管拉伸强度区间的限定。由此可以看出,法国燃气和壳牌这些企业标准中对钢管的屈服强度波动区间限定较严格,不同钢级的屈服强度区间均统一为120 MPa。
因此,在钢管设计文件中,通过参照其它企业或工程标准,也对不同等级钢管的屈服强度区间进行缩窄,保证钢管母管与焊材的高强匹配,保证自动焊接质量。通过对制管厂家X65、X70和X80三种钢级拉伸屈服强度区间的统计,数据来自五家制管企业共36,895组数据,如图5所示。可以看出,如果均以屈服强度区间为120 MPa进行限定,X65钢级的合格率为98.4%、X70钢级的合格率为98.6%、X80钢级的合格率为99.5%,这三种强度等级的钢管合格率较高。因此,在钢管设计中可以统一屈服强度区间,限定屈服强度上限,从而使钢母材与焊材更好地进行强度匹配,提高自动焊接质量。



Figure 4. Comparison of the tensile strength interval of pipes with different strength grades in the standard
图4. 标准中不同强度等级钢管的拉伸强度区间对比



Figure 5. Interval statistics of actual yield strength of pipes with different strength grades
图5. 不同强度等级钢管的实际屈服强度区间统计
2.2.2. 钢管纵向拉伸强度的要求
从环焊缝强度匹配角度,与焊材强度匹配的其实是钢管纵向拉伸强度,因此为了环焊缝能达到其强度匹配要求,应对钢管纵向拉伸强度指标进行规定。在国内外的一些企业或工程标准中,俄罗斯博–乌天然气管道工程标准、俄罗斯西伯利亚力量管道工程标准增加了纵向强度要求,且允许低于其横向拉伸强度。目前在建的中俄东线天然气管道工程(永清–上海)的钢管技术条件中也提出直缝埋弧焊管纵向指标的屈服强度和拉伸强度的最低值可以降低为横向指标最低值的95%。
2.3. 关于钢管管端几何尺寸及其加工
首先,由于自动焊接工艺对钢管几何尺寸要求较高,特别是对钢管管端的不圆度和周长差等控制严格。因此从设计角度,根据焊接工艺评定情况严格控制钢管管端尺寸,保证现场焊接组对精度,提高焊接质量。
其次,从管端加工角度,为了避免大口径天然气管道不等壁厚连接而产生的焊接、无损检测和应力集中问题,通过对国外文献、工程案例等研究,基于我国对这些变壁厚焊接接头所采用的焊接工艺、无损检测方法和拟期望降低的焊接应力集中系数,对于直管–直管、直管–感应加热弯管的不等壁厚连接都进行了设计优化,即在钢管厚壁侧进行内孔锥型坡口的加工,示意图如图6所示。通过应力分析计算和考虑环焊缝无损检测操作,得出不同类型(直管–直管或直管–弯管)的孔锥型坡口尺寸,即在期望应力集中系数为1.05、1.15情况下,计算最小锥孔长度分别为83~115 mm (直管–直管中的L值)和25~40 mm (直管–弯管中的L值) [10]。为了提高坡口的加工精度,感应加热弯管的内锥孔型坡口由制造厂家加工完成,钢管的内锥型坡口由钢管厂加工,也可由施工单位现场加工。从设计角度,还会对坡口表面粗糙度、坡口加工表面壁厚一致性、坡口表面检测及坡口保护等提出相关要求,为确保自动焊接质量提供保障。

Figure 6. Inner taper hole groove in butt-welded joints with unequal wall thickness
图6. 不等壁厚对焊接接头头内锥孔型坡口型式
2.4. 关于钢管焊接工艺评定适用性
2.4.1. 焊接环境
为了减小现场焊接焊口与焊接工艺评定的差异,首先两者要从焊接环境上吻合,因此焊接工艺评定的焊口要在实际施工现场、由工程实际焊接施工人员完成,使焊接工艺评定中的焊接环境要素与施工现场匹配度达到100%,以提高钢管焊接工艺对工程的指导和适应性 [11] [12] [13]。
2.4.2. 评定用钢管
钢管各因素对自动焊焊接工艺评定的影响,在目前的设计文件中已进行明确规定,即自动焊的焊接工艺评定,其不需重新评定的壁厚覆盖范围为±3.2 mm。若钢管的壁厚变化超出允许的偏差范围应重新进行焊接工艺评定。在施工前,当L485 (X70)及以上钢管的化学成分发生变化,应进行焊接工艺冲击韧性试验。这里的钢管化学成分变化主要体现在碳含量以及碳当量Pcm上。在设计文件中一般规定如下:
1) 当C ≤ 0.12%时,Pcm增加≥0.02%,
2) 当C > 0.12%时,CE增加≥0.03%,
;
3) C增加≥0.02%。
同时,结合目前在建管道工程项目的焊接工艺评定情况,为从C含量和Pcm含量角度提高焊接工艺评定的适应性,建议钢管的出厂质量证明文件上对C含量和Pcm数值精确到0.001%。
在以往管道工程中,一般只对线路的直管–直管对接环焊缝进行焊接工艺评定。而直管–弯管的对接环焊缝不单独进行的焊接工艺评定。与管线钢相比,感应加热弯管用钢管的碳含量和碳当量较高,其冶金成分、强化机制均有很大的不同,使得两者的焊接性存在较大的差异 [14] [15] [16]。本文对X65、X70和X80三种等级的感应加热弯管和线路管的碳含量、碳当量Pcm进行了对比。如表6可以看出,首先,线路用钢管的碳含量和碳当量都要低于弯管。其次,线路用钢管的碳含量和碳当量的标准差均要小于弯管,这说明弯管的碳含量和碳当量离散度更大,即不同钢厂对于弯管母管的碳元素和合金元素添加含量的差异较大。通过SPSS软件的分析,如表6所示,同种钢级的感应加热弯管和线路管的碳含量、碳当量Pcm具有显著性差异,均值虽相差较小,但数据分布的离散程度不同。因此,在进行焊接工艺评定时,直管–直管的焊接工艺评定覆盖范围(如碳含量和碳当量的要求)不一定能涵盖直管–弯管,建议直管–弯管应单独进行焊接工艺评定,保证该位置环焊缝的焊接质量。
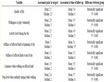
Table 6. Difference between line steel pipe and induction heating bend
表6. 线路钢管与感应加热弯管的差异
2.4.3. 评定取样及监测等
在焊接工艺评定的相关标准中,如GB/T 31032《钢制管道焊接及验收》,对焊接工艺评定的内容规定的较为宽泛,造成在实际工程出现许多不确定性,增加了安全风险。因此,在工程的焊接工艺评定设计文件要求中,要对焊评的试验检测取样过程、焊评质量的监测等都进行了明确规定。如焊接工艺评定时,应采用相同的焊接工艺参数连续完成至少3道无损检测合格焊口的焊接,并随机抽取其中一道焊口进行环焊缝理化性能检验。同时,随机抽取另外一道焊口委托具有CMA或CNAS资质的第三方检验机构进行环焊缝理化性能检验。两道焊口的环焊缝理化性能检验必须全部合格,且第三方检验机构的检测报告应附在焊接工艺评定报告中。这些设计提升措施都使最终现场施工的焊接质量得到有力保障。
3. 结论
通过在设计上对钢管提出的相关要求,使钢管对自动焊接工艺的适应性逐步提高,保证工程焊接质量。主要体现在以下几个方面。
1) 合理限定钢管中对环焊缝断裂韧性影响显著的合金元素含量波动范围,以稳定环焊缝的焊接质量。同时应进一步对感应加热弯管的碳含量和碳当量进行限定,提高其焊接可控性。
2) 从设计角度,根据各厂家提供的数据,可进一步限定X65、X70和X80钢级钢管的屈服强度波动区间,使其与焊材更好地满足强度匹配要求。同时,应规定直缝埋弧焊钢管的纵向拉伸强度指标,使其环焊缝达到很好的强度匹配条件。
3) 提高焊接工艺评定与现场焊接施工的匹配度。当钢管中对焊接质量影响显著的碳含量和碳当量发生变化时,应补充相关试验进一步验证焊缝性能。根据线路用钢管与感应加热弯管中碳含量和碳当量的差异,建议直管与弯管的连接焊口单独进行焊接工艺评定。
参考文献
NOTES
*通信作者。