1. 背景介绍
按照《地铁设计规范》要求,地铁车辆车辆段的检修设施应包括列车吹扫设施。吹扫作业是城市轨道交通车辆在检修前必须经过的一步,主要目的是用于车辆部件,尤其是针对车底重要部件的清洁,从而便于车辆的检修。
根据目前对市场的调研情况,国内已经投入运营的车辆段中,并没有效果良好的智能吹扫系统,对于车底的吹扫作业方式大多数为人工作业为主,作业时扬尘大,对现场环境污染严重,作业人员须穿戴防护服及呼吸器,作业强度大,工作效率低下,因此吹扫作业一直是现场作业人员的痛点,急需一种智能吹扫装置来解决上述问题 [1] [2]。
因此,本文通过研发地铁列车智能吹扫系统,旨在降低地铁列车吹扫耗时,提高列车吹扫的效率;降低吹扫作业后环境中的扬尘浓度,改善作业环境。
2. 系统组成
本文研发的地铁列车智能吹扫系统包括中央控制系统、电控系统、定位系统和吹扫系统,总体构架如图1所示。地铁列车智能吹扫系统一共采用三台智能吹扫机器人,可以根据中央控制系统发出的指令对浮沉积聚严重的部位进行重点吹扫,同时对吹落的灰尘进行同步收集 [3],经过滤达标后排放,从而大大提高吹扫作业的工作效率、降低作业人员劳动强度、改善吹扫作业的工作环境 [4]。
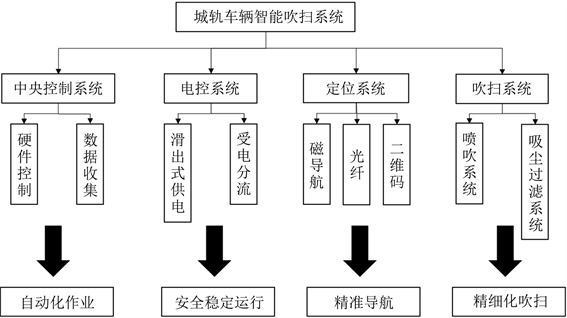
Figure 1. The general structure of the intelligent purge system of the subway train
图1. 地铁列车智能吹扫系统总体构架
地铁列车智能吹扫系统三维视图如图2所示,其中,1代表吹扫机器人的中央控制系统,下面通过智能AGV小车搭载;2代表光纤定位器;3代表中间吹扫机器人的智能机械臂;4代表吸尘过滤系统;5代表二维码带;6代表二维码读码器;7代表喷吹系统。中控系统通过输入的程序实现对整个吹扫过程进行管控;电控系统包括滑触线供电以及受电分流;定位系统有两大部分组成,一是磁导航模块,二是二维码+光纤定位模块;通过在地面上铺设磁条,在AGV小车上装载磁导航传感器,可以通过磁导航实现对小车走行趋势的定位,同时将二维码带固定在滑触线的安装支架上,读码器固定在集电器夹具上,光纤定位器安装在设备上,光纤+二维码的形式实现吹扫设备对列车关键部位的定位;吹扫系统包括吸尘过滤系统和喷吹系统 [5]。
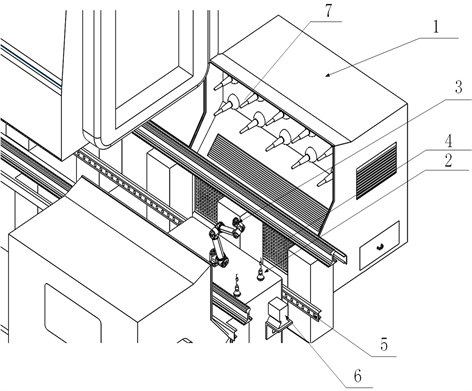
Figure 2. The schematic diagram of the intelligent purge system of the subway train
图2. 地铁列车智能吹扫系统示意图
3. 分部介绍
3.1. 中央控制系统
中央控制系统相当于整个智能吹扫系统的“CPU”,依托程序算法和大数据的支持,负责硬件控制和数据的收集分析,对吹扫系统的其他三个机器人实现集中控制,一键启动;并对实时的作业过程中反馈的信息进行实时处理;通过智能规划行进路径,实现吹扫装置在运行过程中的精确定位,控制吹扫装置对车底重点位置的重点清扫;并控制对吹扫装置对吹扫的灰尘进行集中收集,经过充分过滤后排放,全程自动化除尘,并且实现除尘和集尘的同步进行,彻底实现吹扫作业的自动化作业流程,提高作业效率;同时,为中央控制系统在远端还配有工控触摸屏,该触摸屏采用全模具铝合金压铸成型,是投射式电容控制屏,允许VGA & DVI多种视频信号输入,支持嵌入式、VESA多种安装方式,采用面板钢化玻璃,防护等级达到IP65,可以实时投屏显示吹扫作业进度并实现远程控制。
3.2. 电控系统
电控系统相当于整个智能吹扫系统的“安全门”,包括滑触线供电及受电分流的方式;采用多级管式安全防护滑触线,安装于低于走行轨底部的桥墩侧面,做好绝缘处理、安全防护的工作,每间隔20米设有1个急停断电按钮,当吹扫装置出行故障或者遇到危险状况时,电控系统会及时将整个吹扫装置受电的总开关自动断掉,确保吹扫作业的安全运行;同时,电控系统负责受电分流,为整套吹扫设备的顺利持续运行提供必要条件。
3.3. 定位系统
定位系统包括两方面的定位,一方面是对AGV智能小车的定位,一方面是针对吹扫关键部位的定位;针对AGV智能小车的定位,采用磁导航进行导航,在地面铺设磁条,使AGV智能小车沿磁条运行,在车内装有磁导航传感器,可以监测磁条上的磁场的存在,让小车可以辨识运动的方向,保证AGV智能小车在预设的规定轨道内行驶;第二种定位是AGV小车运行到列车关键部位的定位,采用光纤+二维码的定位方式:二维码带固定在滑触线安装支架上,读码器固定在集电器夹具上,光纤定位模块安装在设备上,用于确定作业起始位置。
在吹扫库地面铺设绕避障碍物的导航磁条,如图3所示。三台机器人从起始位置依次出发,基于霍尔效应,利用磁导航传感器感知导航磁条发出的磁场信息,根据实际吹扫库内的环境变化,绕避所有障碍物,其中:
导航磁条的直线地段运行时,地面上导航磁条的磁场变化信息是相同的,三台机器人按直线运行;绕避障碍物进行拐弯时,在弯道的起始端,导航磁条的磁场变化信息发生变化,磁导航传感器感知磁场变化的信息,通过预先设定的指令,进行转弯动作;地面铺设地导航磁条发生分叉时,在分叉的起始端,磁导航传感器接收到两个不同的磁场变化信息,即收到岔路信息,按照预设的路径向不同的岔路运行。

Figure 3. The schematic diagram of the navigation magnetic strips
图3. 导航磁条示意图
车底智能吹扫吸尘机器人上安装有读码器,具体如图4所示,用于读取设置在轨道桥桥墩内侧面的二维码带所记录的停放在该二维码带处的车底设备的信息确定车底重点清洁部位坐标;读码器包括激光发射源1-1、接收器和读码器支架1-2;激光发射源和接收器通过读码器支架固定在所述车底智能吹扫吸尘机器人上,前者向二维码带发射激光,后者接收反射光读取坐标信息。
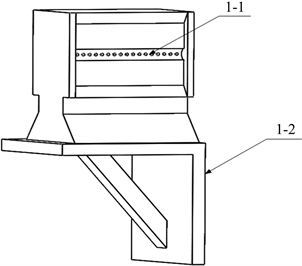
Figure 4. The schematic diagram of the code reader
图4. 读码器示意图
3.4. 吹扫系统
吹扫系统包括两大系统,一是吸尘过滤系统,一是喷吹系统;三台智能吹扫机器人上均搭载吸尘过滤与喷吹系统,可以同时实现对车底、车侧的除尘与吸尘;吸尘过滤系统采用集成式多级过滤装置,采用筒式的滤芯、片式的滤网,集尘斗内设置有压差传感器,该系统在吹扫作业过程中是持续运作的,保证作业的封闭空间内处于微负压的状态,防止除尘作业时灰尘四处飞溅,造成环境的污染;另一大系统是喷吹系统,通过程序控制的灵活、柔性的机械臂,可以针对车底重点吹扫部分进行清洁,吹风喷嘴有集束式、扁平式、鸭嘴型等,每隔3~5秒实现对需要清洁的部位进行脉冲式吹扫,将积聚的灰尘吹落,落入吸尘口,精确度高,相应速度快 [6]。
3.4.1. 吸尘口分析
吸尘口最简单的形式是敞开的管口,当吸尘口开始吸气时,负压随之在吸口周边形成,附近的空气则从各个方向流入吸尘口,吸入气流随之产生。一个敞开的吸气管口,当面积较小时,可看作“点汇”。假定流动无阻力,吸尘口外流线是以吸尘口为中心的径向线,等速面是以吸尘口为球心的球面,如图5所示。
(a)(b)
Figure 5. The schematic of point convergenceradial and equipotential surface of velocity
图5. 点汇气流径向线和等速面示意图
吸尘流量与等速面速度及距离的关系有:
(1)
式中Q——气体流量,3 m/s;
v1、v2——球面1和2的气体流速,m/s;
r1、r2——球面1和2的半径,m。
根据式(1)可知,点汇外某点处空气流动的流速与该点到罩口中心的距离平方成反比。因而在设计安装集气吸尘罩时,必须尽可能地减小罩口与含尘空气之间的距离,从而增加吸尘效率。如果吸尘口的四周设有挡板,如图5(b)所示,则其吸气范围将减半,其等速面变为半圆球面,吸气量为:
(2)
比较式(1)和式(2)可见,在同等距离、同等速度下,周边有挡板的吸气量比周边没挡板的吸气量少一半。故而在外部集尘器设计时,应尽量缩小吸气范围,以便提高控制效果。
但在实际情况中,集尘罩的吸尘口截面积相对较大,不可被简单的看作点汇来分析,加之气体运动时也不可忽略阻力。根据空气动力学的相关知识可知,吸气管口周围的气流等速面是椭球面。
矩形吸尘罩轴线上气体流动的流速分布为:
(3)
式中v0——吸尘口空气流动平均速度,m/s;
vx——距离吸尘口x处的气体流动速度,m/s;
A0——吸尘口的截面面积,m2;
x——吸口外部某点至吸尘口的间距,m;
a0、b0——矩形吸尘口长和宽,m;
不管吸尘口的形式如何,其目的都是在吸尘口周围产生一定的负压,强迫周围气体流入口内从而达到收集粉尘的目的。吸气量的大小,一般情况下认为是将吸尘口内以及吸尘口周围的含尘空气全部吸走并在吸尘口内产生适当真空度所需的空气量。因此在有了吸尘口的外形尺寸和吸尘口的气流速度分布即可求得吸尘口的吸风罩。吸尘口的理论吸风量和吸尘口距粉尘源的间距、吸尘口截面积、粉尘捕吸速度有关。其中粉尘捕捉的最小控制风速,可根据表1选取:
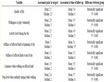
Table 1. The form of the minimum control wind velocity
表1. 最小控制风速表
因为采用的压缩气体对地铁车辆底部喷吹除尘,粉尘脱离元器件表面具有一定的逃逸速度,但在除尘作业区域内的密封性相对较好,所以综合考虑选取吸尘口捕吸风速为0.7 m/s。针对吸尘口风量的计算公式为:
(4)
式中x——含尘空气源距离集气口的最远距离,m;
A——吸尘口面积,m2;
vx——捕吸速度,m/s。
由式4可以看出得到吸尘口吸尘风量与距离、吸尘口面积及控制风速之间的关系。与距离的平方及吸尘口面积之和成正相关,与控制风速成正比。
由式4中(5x2 + A),当距离较大时,即5x2较大,吸尘面积A的变化对(5x2 + A)的值影响较小,而由于列车尺寸超过三米,故在本次仿真中改变吸尘口尺寸而产生的影响不太明显,而当吸尘距离较小时,吸尘口尺寸参数变化的影响较为明显。
基于以上分析,吸尘口与吹扫区域距离较小时,吸尘口面积对整体吸尘效果影响较大,在距离较大时,吸尘口尺寸对整体吸尘效果影响可以忽略。所以,利用侧面吸尘口捕捉速度较低的逃逸灰尘,利用底部吸尘口捕捉吹扫区域灰尘。
3.4.2. 喷嘴分析
气体自喷嘴条缝管口向外喷射,在空间构成一股气流称为气体淹没射流。喷吹系统的喷嘴使用风刀,风刀吹出一道等温扁射流,其形状如图6所示。气流自M点喷嘴喷出。出口断面上的速度认为均匀分布,皆为v0且流动为紊流。取射流轴线M0为x轴。由于射流为紊流型,紊流的横向脉动造成射流与周围介质之间不断发生质量、动量交换,带动周围介质流动,使射流的质量流量、射流的横断面积沿x轴方向不断增大,形成了向周围扩散的梯形体状流动场,如图6中的梯形体CADF。由于刚喷出的射流速度仍然是均匀的。在沿x轴方向流动过程中,射流不断带入周围介质,不仅使边界扩张,而且使射流主体的速度逐渐降低,速度为v0的部位(如图6中AoD锥体)称为射流核心,其余部分速度小于v0称为边界层。射流边界层从出口开始沿射程不断的向外扩散,带动周围介质进入边界层,同时向射流中心扩展,至某一距离处,边界层扩展到射流轴心线,核心区域消失,只有轴心上的速度为v0。射流这一断面为图6上的BoE,称为过渡断面或转折断面。以过渡断面分界,出口断面至过渡断面称为射流起始段,过渡断面以后称为射流主体段。射流起始段一般都很短,在工程设计中实际意义不大,在吹扫除尘中,主要是利用射流的主体段,其轴心速度和断面流量分别为:
(5)
(6)
式中,v0——射流出口速度,m/s;
α——射流紊流系数,扁射流α = 0.11~0.12;
s——断面距吹气口距离,mm;
b0——矩形吹气口宽度,mm;
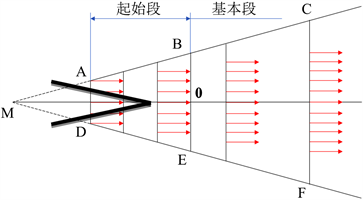
Figure 6. The schematic of jet velocity distribution
图6. 射流速度分布示意图
由理论公式可以得出,流经风刀过后的压缩空气,会变成一道冲击气流,该气流流速快、强度非常大、流量多,可轻吹落附着在地铁列车底部元器件上的粉尘。
由气动技术理论知识可知,气流通过喷嘴时,出口处的流动马赫数M = 1时,则为音速流动,此时p1/p0 = 0.528 (p1为喷嘴外绝对气压,p0为喷嘴内绝对气压);当流动马赫数M > 1时,则为超音速流动,此时p1/p0 < 0.528。在收缩喷嘴处,压缩空气向标准大气喷射,当流动速度达到音速时,无论怎么提高喷嘴内的背压,气体的喷射速度都不会再提高,此时将出现壅塞流,所以喷射速度最大为音速,即340 m/s。参考喷嘴的技术参数,取喷嘴内的空气压力为0.7 MPa,标准大气压为0.1013 MPa,显然p1/p0 = 0.149 < 0.528,由此可知流经喷嘴后空气流将以音速向外喷射。喷嘴标准状态下的流量:
(7)
式中,v0——射流出口速度,m/s;
α——射流紊流系数,扁射流α = 0.11~0.12;
s——断面距吹气口距离,mm;
b0——矩形吹气口宽度,mm;
分别对集束式和扁平式两种类型喷嘴在相同输入条件下进行仿真,验证喷吹气流吹扫效果。选取喷嘴为质量入口,工作压力6 bar,工作流量612 L/min,可计算得质量流量
。仿真速度云图分别如图7、图8所示。
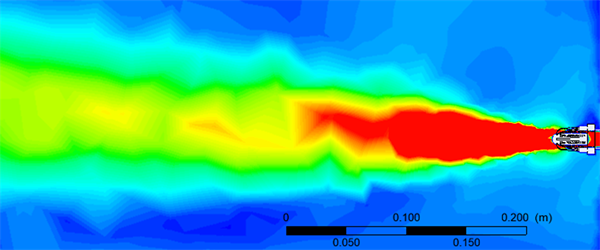
Figure 7. The simulation charts of cluster nozzle air current
图7. 集束式喷嘴气流仿真图
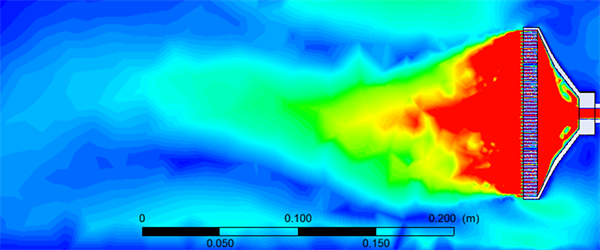
Figure 8. The simulation charts of flat and horizontal nozzle air current
图8. 扁平式喷嘴气流仿真图
在上图仿真中,两喷嘴输入压力为6 bar,流量为612 L/min,红色区域气流速度为40 m/s。集束式喷嘴喷出气流较为集中并且随距离的衰减较慢,扁平式喷嘴吹扫范围更宽且速度衰减较为明显。
基于以上分析,由于车底结构较为复杂,选用集束式喷嘴,吹扫气流束更加集中,有效距离更长。
4. 实施方案
车辆停稳后,先进行车底盖板的拆卸和存放,完成后人员撤离;确认作业范围内没有人和障碍物会对设备的运行造成影响后,主电柜合闸送电;三个机器人通电正常后,电控系统接收到受电指令,完成对各硬件的分流供电,进行安全自检;完成自检后,若没有发现问题,开启指示灯,准备进行启动;车底智能吹扫吸尘机器人和两侧的车侧智能吹扫吸尘机器人三者通过一键启动中控系统后,通过固定在指定位置的显示屏实时监控作业情况,如发现问题,通过设置的急停按钮使吹扫系统终止运行,等待解决问题后再继续正常运行;激活三个机器人内装有的磁导航传感器,开始根据地面铺设的导航磁条发出的磁场信息,开始初步定位,按照磁导航的信息使三台机器人分别移动到列车的两侧及车头底下;当吹扫系统运行到车辆端部时,通过装备在走行机构上的光纤定位器进行确定初始坐标,车底重点清洁部位的坐标由读码器读取二维码带提供;两侧的车侧智能吹扫吸尘机器人通过侧封体,将吹扫系统所到范围内形成封闭空间,并将封闭空间内营造成负压状态,防止除尘作业时灰尘四处飞溅,造成周围环境的污染;当吹扫系统运行到重点清洁部位时,车底智能吹扫吸尘机器人的多轴机械手工作,吹风喷嘴通过脉冲式作业,将积聚的灰尘吹落,吸尘口的负压抽吸持续运行,确保吹落的灰尘可及时收集;吹扫系统运行到车辆尾部,完成作业流程后,自动停靠到指定位置,同时由中控系统切断对各硬件的供电,设备处于断电状态,主电柜再切断滑触线的送电开关;完成断电动作后,再完成车底盖板的复位安装;完成作业后,停靠在车辆端部指定位置。
5. 结论
综上所述,采用地铁列车智能吹扫系统,具有以下功效:
1) 通过三台城轨车辆智能吹扫机器人实现对车侧以及车底的吹扫,吹扫、吸尘过程功能同步进行,高压气流直接把所需清洁表面的粉尘、污垢吹起,吹起的尘粒被除尘器瞬间吸走过滤,避免了二次扬尘,降低了作业后扬尘的浓度。
2) 通过三台城轨车辆智能吹扫机器人实现同步过滤自清洁,进入除尘器的粉尘先进入除尘装置过滤,剩余尘粒进入高效过滤器过滤,净化后的空气达标排放,保护周围环境。
3) 通过在走行机构如AGV小车内装有磁导航传感器,可以实时感应铺设在地面的导航磁条发出的磁场信号,实现AGV小车在运行过程的精确定位;通过二维码和光纤定位的配合,可以由程序自动计算坐标,实现对车辆关键部位的重点定位,准确清扫;同时,码带对灰尘和损伤不敏感,更可靠、更实用、更耐用。
4) 通过三台城轨车辆智能吹扫机器人可实现在地沟内、外侧灵活移动,拥有柔性、灵活的机械手,改良除尘喷嘴,融合噪声屏蔽、吸音降噪技术,使工作环境更加人性化。
5) 通过三台城轨车辆智能吹扫机器人实现设备的控制一建智能化启动,依托大数据和算法程序的支持,在作业期间,无需人工参与,全程自动化完成,吹扫作业效率大大提高。