1. 引言
潜孔钻机作为当前工程通用的大型凿岩钻孔设备 [1],因其具有钻孔深、效率高、钻孔直径大等特点,广泛应用于煤矿业的开采、建筑基础开挖、水利、交通、电站及国防建设等多种大型工程中。然而随着轻量化设计 [2] 逐渐应用在液压传动技术领域,将执行元件速度提高的同时,也要求潜孔钻机、潜孔钻车等凿岩采掘设备液压缸活塞杆速度越来越快 [3],有的甚至高达每秒几十米。液压缸是潜孔钻机的主要执行元件之一 [4],如图1所示,当潜孔钻机推进油缸拖动负载以较高的速度运行到末端时,如果未涉及缓冲装置,往往会发生剧烈的冲击和振动,伴随产生刺耳的噪声,甚至使紧固件松动,损坏潜孔钻机的零部件。针对液压缸缓冲结构国内外学者进行了大量研究,丁凡 [5] 研究了圆锥形缓冲装置的缓冲过程;武晓凤等人 [6] 设计了一种复合型缸内缓冲结构,该复合型缓冲结构缓冲过程平稳、冲击小。为此,本文根据潜孔钻机推进油缸的高速运动特点,设计了一种缸内缓冲装置,分析了缓冲装置的缓冲原理,通过建立数学模型对其进行仿真,并搭建实验平台进行验证。
2. 推进油缸的结构及缓冲原理
图1为潜孔钻进推进油缸的结构示意图,主要是由缸筒、活塞、缓冲活塞、活塞杆、端盖等组成。在活塞杆上设计了两个台阶,其中活塞一端与活塞杆第一处台阶限位固定,另一端采用六角开槽螺钉紧固,而缓冲活塞在复位弹簧的预紧力作用下与活塞杆上的第二处台阶处限位固定。在推进油缸的快速推进过程中,无杆腔进高压油,推动活塞快速向右运动,如图2所示,当缓冲活塞随活塞杆向右运动至端盖时,进入缓冲阶段,此时活塞杆带动活塞继续向右运动,但由于缓冲活塞是锥形结构,液压油的通流面积变小,缓冲活塞与活塞之间形成了一个有效的缓冲腔,缓冲腔内的液压油只能通过缓冲活塞与活塞之间的缝隙流出,形成了一个环形节流缓冲过程,从而降低活塞的速度,达到缓冲的效果。
假设在该缓冲过程中,流动状态层为紊流,则缓冲腔的流量为:

式中:
为流量;
为流量系数;
为缓冲腔开口截面积;
为缓冲腔的压力;
为出口处压力;
为液压油密度;
为缓冲腔面积;
为活塞位移;
为缓冲腔体积;
为能量系数。
1:法兰;2:活塞;3:缓冲活塞;4:活塞杆;5:缸筒;6:后端盖。
Figure 1. The structure of the propulsion cylinder
图1. 推进油缸的结构
1:活塞;2:缓冲活塞;3:活塞杆;4:缸筒。
Figure 2. Buffering device
图2. 缓冲装置
3. 仿真研究
为了更好的了解潜孔钻机推进油缸缸内缓冲装置的缓冲过程,根据上述数学模型,如图3所示,建立仿真模型,在Matlab中采用四阶的龙格–库塔法进行仿真研究 [7],假设油缸连接管道均为短且粗的,且油管内的摩擦损失和流体质量影响忽略不计,油缸各个工作腔内各处的压力处处相同,油液温度和体积弹性模量可认为是常数,油缸部分参数如表1所示。
在油缸的缓冲过程中,缓冲末速度和缓冲腔峰值压力是重要的性能指标,直接影响着缓冲装置的缓冲效果。图4为油缸活塞杆的速度和缓冲位移之间的关系。由图4可知,该缓冲装置的缓冲行程约为15 mm,当活塞杆初始速度分别为12 m/s、15 m/s以及18 m/s时,在活塞杆位移约为2.8 mm左右时,活塞杆的速度降至最低,可从18 m/s降至2.9 m/s,降幅高达83.9%,而且活塞杆会以2.9 m/s的速度运动至缓冲行程结束,活塞杆的减速缓冲效果良好。
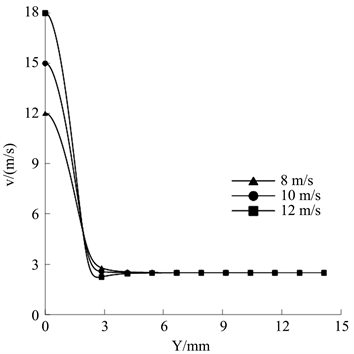
Figure 4. The relationship between the speed of the piston rod and the buffer displacement
图4. 活塞杆的速度和缓冲位移之间的关系
图5为油缸活塞杆位移与缓冲腔压力之间的关系。由图5可知,在推进油缸的缓冲过程中,在不同的进口压力下,当活塞杆位移为1.4 mm时,缓冲腔的压力均为最高,特别是在进口压力为14 MPa时,缓冲腔的最高压力为17.2 MPa,是进口压力的1.2倍,当缓冲腔的压力大于油缸进口压力时,可以很好阻滞活塞杆的运动,降低其速度,随着位移的继续增大,缓冲腔的压力逐渐变小并趋向于平稳,但此时缓冲腔的压力也高于进口压力,可以持续对活塞杆进行降速的效果。
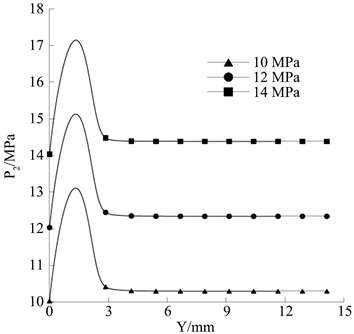
Figure 5. The relationship between piston rod displacement and buffer chamber pressure
图5. 活塞杆位移与缓冲腔压力之间的关系
4. 实验研究
为了更好地验证缸内缓冲装置具有良好缓冲效果的稳定性和可靠性,搭建缓冲装置的实验方案进行试验研究,实验方案见图6,为提高油缸的伸出速度,油缸采用差动的连接方式 [8]。通过实验测得油缸缓冲过程中活塞的速度变化,为缸内缓冲机构的优化设计进行改进。
1:油箱;2:液压泵;3:单向阀;4:方向阀;5:开关阀;6:液压缸。
Figure 6. Experimental schematic diagram
图6. 实验原理图
实验测得的油缸速度与位移曲线如图7所示,虚线为活塞杆的位移,实线为活塞杆的速度,其中图7(a)为初始速度为15.1 m/s,图7(b)为初始速度为18.7 m/s。由图7可知,油缸缸内缓冲装置约在活塞杆位移为756 mm左右开始进行缓冲,与油缸整体行程一致,缓冲时间较短,当初始速度为15.1 m/s,缓冲时间约为36 ms,当初始速度为18.7 m/s时,缓冲时间约为42 ms,可见该缸内缓冲装置的缓冲时间较短,可实现快速缓冲效果。
(a) 初始速度为15.1 m/s (b) 初始速度为18.7 m/s
Figure 7. Speed and displacement of oil cylinder
图7. 油缸速度与位移
5. 结语
本文通过对潜孔钻机推进油缸结构上的创新,设计了缸内缓冲装置,得到的结论如下:
1) 分析了缸内缓冲装置的缓冲过程,根据其缓冲原理,建立数学模型,并在Matlab中进行仿真分析,得到了潜孔钻机推进油缸缸内缓冲装置在缓冲过程中的活塞杆位移和缓冲腔的压力变化,仿真结果表明,在缓冲过程中,缓冲腔的压力会持续升高,且均高于进口压力,可以达到降低活塞杆运动速度的目的;
2) 设计缓冲装置测试的实验方案,进行实验,研究缸内缓冲装置在缓冲过程中活塞杆速度随位移的变化,结果表明,当初始速度为18.7 m/s时,在缓冲时间约为42 ms可将速度降至0,基本实现了快速缓冲效果,对比了仿真结果和实验结果,发现两者的变化趋势是一致的,也证明了仿真模型的合理性。
基金项目
浙江省高校国内访问工程师“校企合作项目”(FG2020221)。