1. 引言
磷对于大部分钢铁产品来说都是有害元素,因为磷在晶界偏聚会降低钢的韧性及塑性,显著降低钢的冲击韧性,使钢在低温状态发生冷脆现象。磷还能引起钢材的回火脆性,降低钢材的力学性能、可焊性、抗裂纹性及抗腐蚀性能 [1]。随着钢铁工业的发展客户对钢材质量的要求日趋严苛,特别是低温用钢、海洋石油平台等高性能用钢产品要求w(P)小于0.01%甚至0.005%以下 [2]。
对于高硅、高磷铁水,传统转炉炼钢工艺为达到脱硅、脱磷目的,通常增加石灰、镁球等辅料用量以提高熔渣碱度脱磷,转炉大渣量冶炼易引起喷溅、氧枪粘钢等现象,造成金属回收率低、氧枪消耗高、炉衬寿命低等问题。
针对铁水成分不稳定带渣量大的现状,为实现低磷钢冶炼目标,长材事业部炼钢分厂在顶底复吹转炉进行了石灰石双渣脱磷工艺实践,在脱碳阶段加入石灰石造渣优化脱磷动力学条件提高脱磷率,不仅减少了造渣辅料用量,而且降低了钢铁料消耗,取得了良好的经济效益。
2. 入炉铁水及主要辅料指标
长材事业部炼钢分厂有4座公称容量为70 t的顶底复吹转炉,底吹供气原件有6个,氧枪为4孔拉瓦尔型。转炉以一铁总厂铁水为主,表1为铁水成分表。由表可以看出,硅含量平均0.51%左右,磷含量平均0.155%左右,转炉冶炼主要难点在于脱磷。传统单渣法采用增大石灰用量提高炉渣碱度的大渣量操作模式,钢渣分离差,钢铁料消耗较高。转炉主要冶金辅料指标见表2。
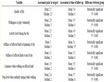
Table 1. The temperature and composition of molten iron
表1. 铁水温度及成分
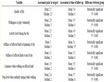
Table 2. Technical indicators of main slag making materials for converter
表2. 转炉主要冶金辅料指标
3. 顶底复吹转炉石灰石双渣工艺路线
李宏 [3] 提出用石灰石替代石灰作为造渣辅料的方法,即在转炉吹炼前期加入石灰石,利用转炉的物理热完成石灰石煅烧分解过程,用煅烧后的石灰参与脱磷反应。杜玉涛 [4] 研究了在转炉双渣脱磷期用石灰石代替石灰做造渣剂的“石灰石双渣法”,实现了脱磷与降本的目标,但在吹炼前期存在不同程度的低温喷溅现象,分析原因是石灰石分解吸收热量使熔池温度升温放缓,中期石灰石分解及碳氧反应产生的大量CO2气体带动炉渣涌出炉口。
事业部实践在转炉双渣脱碳期加入石灰石,达到既利用石灰石作为冷料平衡转炉冶炼富裕热量使熔池温度均匀上升,又利用石灰石分解产生的CO2气体优化脱磷热力动力学条件提高脱磷效果的目的,大幅减少双渣脱磷期加入石灰石引起的低温喷溅现象。
转炉石灰石双渣脱磷工艺过程分两个阶段:脱磷阶段利用上炉次高碱度、高w(FeO)留渣及少量石灰快速造渣,利用冶炼前期低温条件充分脱磷后,排出前期高磷炉;脱碳期加入石灰石、少量石灰、剩余镁球等渣料快速造渣,确保终点成分合格。顶底复吹转炉石灰石双渣脱磷实践工艺路线为:
1) 上炉次出钢留渣操作:上炉出钢后留40%~60%高碱度、高氧化性炉渣,加入适量调渣剂调质,用N2溅渣快速冷缺固化,作为前期造渣辅料;
2) 脱磷期吹炼及倒渣操作:高枪位大氧压点火(枪位1.8~2.1 m,氧压0.90~1.0 Mpa)→正常枪位及氧压去除硅锰(枪位1.2~1.4 m,氧压0.70~0.75 Mpa)→适当提高枪位前期脱磷(枪位1.4~1.6 m,氧压0.70~0.75 Mpa)→提枪倒渣。控制合适的一次倒炉温度、炉渣碱度以及渣中w(FeO)保证一倒脱磷率。脱磷期结束提枪,缓慢倒炉排出约60%的高磷炉渣,以减少脱碳期回磷量;
3) 脱碳阶段快速造渣操作:加入石灰石、少量石灰及其余辅料进行快速造渣,控制出钢温度、终渣碱度及w(FeO)含量保证脱磷效果;
4) 吹炼终点要求:压枪枪位0.9~1.0 m,氧压0.80~0.85 Mpa,压枪时间大于20秒,钢水成分、温度合格结束吹炼,出钢过程使用滑板挡渣,减少下渣量。
4. 顶底复吹转炉石灰石双渣工艺分析
4.1. 一次倒炉温度对前期脱磷影响
弄清不同时期脱磷反应的热力学条件,是制定转炉脱磷工艺的基础 [5]。过程温度是影响脱磷反应的重要因素。脱磷反应平衡常数与温度的关系式为:
(1)
图1为反应平衡常数随温度的变化趋势图,可以看出,温度对脱磷反应的影响非常显著,随着熔池温度的升高,平衡常数Kp逐渐减小。当温度从1300℃升至1650℃左右,反应平衡常数降至7个数量级,磷分配比大幅降低,不利于脱磷反应的进行。低温有利于脱磷反应。
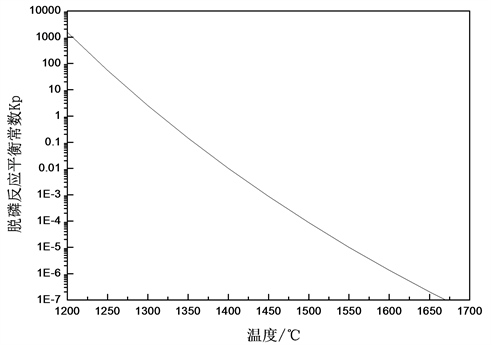
Figure 1. Trend diagram of reaction equilibrium constant change with temperature
图1. 反应平衡常数随温度的变化趋势图
双渣脱磷选择在碳氧反应开始之前吹炼前期的低温阶段。铁水中氧和硅的亲和力比磷强,在吹炼初期较低温度下,硅、锰比磷优先氧化,当硅氧化至痕量时,磷才开始大量氧化。但随着脱磷反应的进行和熔池升温,碳和磷会出现选择性氧化转变,即在低于某一温度时铁液中的磷优先氧化,反之碳优先氧化,磷的氧化受到抑制。碳磷选择性氧化方程式为:
(2)
令
,计算出碳磷选择性氧化的温度约为1435℃。有文献 [6] 认为,转炉升温过程中脱磷反应不会在温度刚达到或高于碳磷选择性氧化温度时停止,而是在高出一定范围内继续发生并逐渐减弱,这时磷元素处于被FeO氧化与被C还原的动态平衡中。文献 [7] 计算出的碳磷选择性氧化温度在1300℃~1350℃,而生产过程中一倒温度一般高出碳磷选择性氧化温度50℃~100℃。有人 [8] 通过工业实验得出将一次倒渣温度控制在1400~1440℃时,可取得较好的脱磷效果。本次石灰石双渣试验一次倒炉温度选择控制在1350℃~1450℃。
4.2. 一次倒炉碱度和w(FeO)对前期脱磷影响
一次倒渣碱度越高,渣中的CaO有效含量越高,LP越大,脱磷越完全。碱度继续增加,部分颗粒不能完全熔化,炉渣的黏度增大,导致炉渣流动性减弱不利于脱磷。碱度过高还会减少氧化铁活度,影响脱磷效率。渣中w(FeO)也是影响脱磷效率的主要因素,高w(FeO)炉渣能使磷呈现强烈的氧化趋势,(P2O5)与(CaO)结合成稳定的磷酸钙。冶炼过程随着(CaO)逐渐升高,大部分P2O5生成了3CaO∙P2O5。随着w(FeO)的升高,磷在炉渣和钢水中的分配比会随炉渣氧化性的增强而增大,w(FeO)的升高会促进渣中(CaO)的熔解,有利于脱磷反应的进行。当炉渣中w(FeO)含量超过一定值时,(FeO)会稀释渣中的(CaO)的有效浓度,炉渣的脱磷能力反而降低。由Healy磷分配公式推导出一次倒炉碱度、w(FeO)在脱磷阶段方程式:
(3)
根据(3)计算在一次倒炉温度1380℃~1450℃,R = 1.5~2.0,w(FeO)为15%~20%时,LP为60~90,可满足一次倒炉脱磷要求。本次石灰石双渣试验一次倒炉碱度控制在2.0左右,w(FeO)控制在20%左右。
4.3. 顶底复吹转炉双渣脱碳期石灰石快速造渣
脱碳阶段使用石灰石快速造渣。石灰石首先分解,表面生成的CaO与碱性氧化物或铁的氧化物进行造渣反应,然后逐渐向里渗透,受到内层CaCO3的分解反应的限制,避免高熔点的2CaO∙SiO2的生成,生成了较多的CaO∙SiO2,CaCO3分解产生的CO2使半钢氧化性增强,促进快速化渣,生成了铁酸钙、正铁酸钙和橄榄石等低熔点化合物。分解产生的CO2不仅增加熔池搅拌强度优化脱磷反应动力学条件,CO2具有弱氧化性,可参与炉内氧化反应,有利于脱磷反应的进行。
加入石灰石造渣与石灰造渣相比,反应较激烈容易溢渣,主要是分解过程及碳氧反应产生的CO2带动炉渣涌出炉口产生的。在吹炼过程中石灰石采用少量多次加入、适当提高操作枪位控制炉渣活跃度。
5. 石灰石双渣试验分析
5.1. 试验铁水条件
转炉石灰石双渣及石灰双渣工业试验共进行73炉,试验钢种为Q235B,均为正常出钢温度(钢罐均正常状态)出钢。石灰石双渣试验共51炉:石灰石脱磷期加入试验25炉,脱碳期加入26炉;正常石灰双渣试验22炉。试验铁水条件如下表3所示。
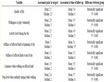
Table 3. Composition and temperature of test furnace molten iron
表3. 试验炉次铁水成分和温度
表4是双渣试验一倒脱磷渣成分表,可以看出,石灰石、石灰双渣前期渣碱度平均在1.85~2.01之间,w(FeO)含量在16.9~19.3%,渣中磷含量在2.65%~3.05%之间。
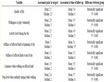
Table 4. Compositions of slag in early stage of double slag dephosphorization
表4. 双渣脱磷前期渣成分
5.2. 一次倒炉温度及碱度范围控制
图2是转炉石灰石双渣试验一次倒炉温度及炉渣碱度与一倒脱磷率关系图。可以看出,随着一倒温度的升高,一倒脱磷率先增后减,一倒脱磷率峰值区间在1370℃~1420℃之间,一倒脱磷率43.6%~62.7%,平均脱磷率54.2%;随着碱度的增加,一倒脱磷率呈上升趋势,碱度进一步增加(R > 2.1),一倒脱磷率逐渐降低。碱度在1.7~2.1区间时,一倒脱磷率较高。石灰石双渣工艺一次倒炉温度最佳范围在1370℃~1420℃,炉渣碱度范围1.7~2.1。
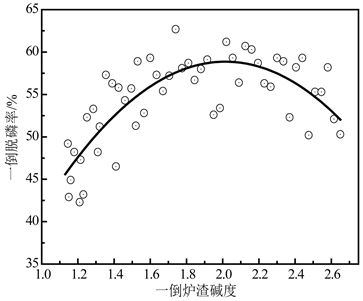
Figure 2. Influence of first deslagging temperature and slag basicity on the average dephosphorization rate
图2. 一次倒炉温度及炉渣碱度对一次脱磷率影响
5.3. 一次倒炉渣w(FeO)含量控制
图3为转炉石灰石双渣试验一倒脱磷率与渣中w(FeO)的关系图。由图可以看出,一倒脱磷率随渣中w(FeO)的增加而增大,渣中w(FeO)在区间17%~21%范围时可获得较理想的一倒脱磷率。当w(FeO) > 21%时,一倒脱磷率随渣中w(FeO)的增加逐渐降低。考虑一倒脱磷效果,一次倒炉渣中w(FeO)应控制在17%~21%。
5.4. 石灰石双渣工艺终点控制
表5为不同双渣工艺终点及过程控制情况,表6为不同双渣工艺终渣成分。三种双渣工艺终渣碱度平均为3.2~3.5,终渣w(FeO)在13.8%~14.9%,出钢温度基本在1640~1660℃,终点脱磷率68.5%~79.8%,平均脱磷率73.5%,不同双渣工艺脱磷效果均能满足生产需求。从试验炉次过程控制看出,与脱磷期加入石灰石造渣相比,在脱碳期加入石灰石过程温度均匀上升控制较平稳,喷溅基本可控,大幅降低了脱磷期加入石灰石引起的低温喷溅现象。
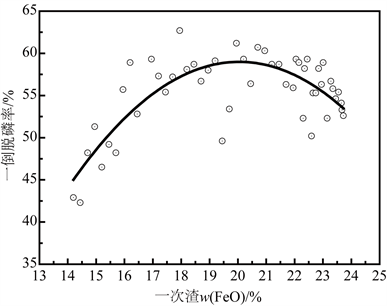
Figure 3. Influence of the w(FeO) in slag on the average dephosphorization rate
图3. 渣中w(FeO)对一倒脱磷率的影响
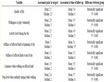
Table 5. Composition and temperature of end-point molten steel by limestone and Lime double-slag process
表5. 石灰石与石灰双渣工艺终点钢水成分与温度
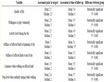
Table 6. Final slag composition of limestone and Lime double-slag process
表6. 石灰石与石灰双渣工艺终渣成分
5.5. 效益计算
表7为不同双渣工艺辅料用量、钢铁料消耗对比。可以看出,石灰石双渣与石灰双渣工艺辅料用量比传统单渣工艺降低14~15 kg/t,钢铁料消耗降低约6~7 kg/t;与石灰双渣工艺相比,石灰石双渣工艺使用石灰石代替石灰辅料降本约7.31元/t;不同时期加入石灰石双渣工艺辅料用量相当,但与脱磷期加入石灰石相比,在脱碳期加入石灰石过程控制平稳,钢铁料消耗比脱磷期加入石灰石造渣低约0.9 kg/t。
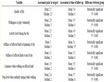
Table 7. Raw material and iron and steel material consumption in different process
表7. 不同工艺辅料用量与钢铁料消耗
6. 结论
1) 石灰石双渣工艺一次倒炉温度最佳范围在1370℃~1420℃,碱度在1.7~2.1,w(FeO)在17%~21%,满足脱磷热力学条件,一倒脱磷率均值54.2%;
2) 采用石灰石造渣产生的CO2增加熔池搅拌强度提高炉渣泡沫化程度,CO2可参与炉内氧化反应,有利于脱磷反应的进行;
3) 石灰石双渣法与石灰双渣终渣碱度R 3.2~3.5,w(FeO)含量13.8%~14.9%,终点温度1640℃~1660℃,脱磷率68.5%~79.8%,平均脱磷率73.5%,均可满足工艺需求;
4) 与脱磷期加入石灰石相比,在脱碳期加入石灰石,吹炼过程温度均匀上升,过程控制平稳,避免脱磷期加入石灰石引起的低温喷溅现象。脱碳期加入石灰石消耗比脱磷期加入石灰石低约0.9 kg/t;
5) 与传统单渣工艺相比,石灰石双渣与石灰双渣工艺辅料用量降低约14~15 kg/t,钢铁料消耗降低约6~7 kg/t。与石灰双渣工艺相比,石灰石双渣工艺降本约7.31元/t。