1. 引言
随着大部分陆地油气田的不断开发,常规油气资源的产量增长出现乏力,非常规资源已逐渐成为当前油气勘探的主要领域。可钻式桥塞分段压裂技术是目前国内外进行低渗透油气藏开发使用的主体储层改造技术 [1],其中,对桥塞快速有效的钻除是保证油气藏顺利投产的关键步骤。新疆油田页岩气、致密油储量丰富,钻磨桥塞作业量不断增长,但目前以瓜胶为主的钻磨液体系存在高温高剪切条件下易降解,粘度降低、携带能力下降的问题,这给低渗透油气藏的开发提出了巨大的挑战。针对以上钻磨液遇到的问题,徐庆祥等 [2] 采用滑溜水作为基液并优化了钻磨参数,获得了拥有较高降阻率和携岩能力的钻磨液体系,在大港油田取得了较好的效果。何吉标等 [3] 针对连续油管钻磨钻屑难以返出井口,易出现憋泵、卡钻等复杂情况,向钻磨液体系中引入多糖类高分子化合物作为流型改性剂,使其携岩能力提升两倍以上。李爱春等 [4] 在钻磨液中加入金属减阻剂,将金属摩擦系数有效降低25%~35%,减少了连续油管与套管内壁金属的摩擦阻力,在涪陵页岩气田的应用中显著提高了连续油管钻塞效率。本为针对新疆油田钻磨液遇到的难题,在钻磨液性能恶化机理的分析基础上,研制出一种抗温抗剪切的关键性增粘处理剂,进一步构建了低摩阻、抗温抗剪切、稳定性良好的无固相水基钻磨液体系及其配套工艺,并取得了较好的现场试验效果。
2. 新疆油田钻磨液技术难题
2.1. 所遇问题
2.1.1. 流体携带性差
桥塞卡瓦由铸铁浇铸而成,铁块密度大,在井眼内运移困难 [5]。桥塞胶皮钻磨碎块大,携带返出困难,容易造成连续油管憋泵和卡钻现象。
2.1.2. 钻磨工艺复杂
水平井钻磨施工参数及流体性能要求高,钻磨加压控制难度大,桥塞间残留原油、地层水液体会对钻磨液造成污染,处理不当易发生卡钻或无进尺等问题 [6]。
2.1.3. 钻磨液抗温能力差
钻磨液体系以瓜胶为主要材料,瓜胶等聚合物材料增粘程度高,在水溶液中呈现缠绕生物聚合物的性质 [7]。但抗剪切能力与热稳定性较差,80℃条件下主链糖苷键就会发生断裂 [8],造成钻磨液粘度下降,携带能力变差。新疆油田井深4000米以上井居多,地层温度约110℃ [9],在钻磨高温高剪切环境中,瓜胶钻磨液体系降解后造成磨屑携带能力下降,增加卡钻风险。
2.2. 解决对策
由以上问题分析可以看出,对于钻磨液性质的限制主要归结于瓜胶等材料的抗温能力差,改善钻磨液的抗温性是目前急需解决的技术难题。因此本文通过对处理剂分子结构和官能团的研究,研制出一种新型的水基钻磨液抗高温增粘剂,以此增粘剂为核心处理剂构建具有高携屑、抗剪切性能的无固相钻磨液体系,从而降低卡钻概率,保障钻磨桥塞的连续作业,发挥出连续油管钻磨桥塞的带压、高效、投产快速等优势 [10]。
3. 耐温增粘剂的研制
本文研制一种抗温性能良好的聚合物增粘剂,并命名为SDT-108,以下为其合成方法及性能评价。
3.1. 分子结构设计
1) 主链结构:采用C-C单键结构 [11]
聚合物的抗温能力关键在于主链的热稳定性。本文拟采用C-C链为主链对聚合物进行分子基础结构设计。C-C单键键长相对较短,平均键能很大,为347.3 kJ/mol,破坏C-C单键需要很高的热能。因此以C-C链为主链的聚合物拥有抗高温的基础结构,极难高温降解。
2) 侧链结构:采用C-C、C-S和C-N等结构
侧链主要是水化基团,侧链的断裂将引起聚合物水化作用的降低或完全丧失。因此本文拟采用C-C、C-S以及C-N等作为处理剂侧链的主要结构,因为他们拥有较高的热能,高温下不易断裂,具有很高的抗温能力。
3) 水化基团:采用数量足够的-SO3-基和-COO-基
分子中引入亲水能力强的-SO3-基和-COO-基,特别是-SO3-,在高温下仍然具有很强的水化能力,高温去水化作用弱,其适量的引入可使处理剂分子拥有良好的溶解性。
3.2. 合成原理
采用水溶液共聚法,利用无机过氧化物引发剂热分解产生自由基,引发聚合反应,遵循自由基聚合原理,具有易控制、成本低的优点 [12]。
在链引发阶段,过氧化物热分解产生自由基,自由基具有较高的活化能,与发生碳碳双键断裂的单体某一端进行结合,形成单体自由基;继而开始链增长阶段,单体自由基与另一个单体的碳碳双键发生加聚反应,并持续进行下去,合成产物的链长度开始逐步增加,随后交联剂的加入会使已经具有一定长度的碳链相互交联,形成一定的空间结构,增强其聚合物的结构强度,不易降解;当产物达到足够的链长及有了一定的空间结构后,其反应活性会慢慢降低,直至失去活性,聚合反应终止,即链终止阶段,形成微交联聚合物增粘剂。
3.3. 合成原料、试剂
本增粘剂合成的原料为:一是2-丙烯酰氨基-2-甲基-1-丙烷磺酸(AMPS),因其带有磺酸基而具有较好的抗温性能;二是N-羟甲基丙烯酰胺(N-MAM),其增粘能力相对常用的丙烯酰胺更加出色。合成过程中所需的试剂有引发剂和交联剂,分别为过硫酸铵和N,N-亚甲基双丙烯酰胺(MBA)。上述实验原料与试剂皆为国药试剂,纯度皆为分析纯。
3.4. 合成方法
1) 称取一定量的单体AMPS和适量去离子水,充分进行混合后,用质量浓度为20%的NaOH溶液调节溶液pH值至中性。
2) 加入适量的单体N-MAM,充分搅拌使其溶解,然后将其倒入三口反应瓶中,并缓慢搅拌使其溶解均匀,通N2除氧30 min。
3) 升至反应温度,将引发剂过硫酸铵溶于一定的去离子水中,然后匀速滴入三口烧瓶,反应开始进行,转速200 r∙min−1。
4) 反应1 h后,将交联剂MBA [13] 溶于一定的去离子水中,然后匀速滴入三口烧瓶,缓慢搅拌。
5) 将三口反应瓶密封,在N2保护下再反应5 h。
6) 将产物取出,用乙醇沉淀,50℃真空干燥,即得聚合物样品。
3.5. 性能评价
通过与另外一种增粘剂PMHA-II进行对比,对SDT-108的抗温增粘能力进行评价。实验内容为测试两种增粘剂水溶液180℃下老化16 h前后的流变性能。流变性测试仪器为青岛海通达专用仪器有限公司提供的旋转粘度计,型号为HTD13285;高温老化实验仪器为青岛同春石油仪器有限公司提供的变频滚子加热炉,型号为BGRL-5。
溶液1#:蒸馏水 + 0.6% PMHA-II
溶液2#:蒸馏水 + 0.6% SDT-108
结果见表1所示。
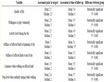
Table 1. Comparative experiment results of PMHA-II and SDT-108
表1. PMHA-II与SDT-108对比实验结果
由表1中实验结果看出,PMHA-II的表观粘度变化率为46.3%,SDT-108为35.1%,说明SDT-108的抗温性较强,SDT-108实验浆老化后的塑性粘度较PMHA-II更大,说明其提粘能力也优于PMHA-II,SDT-108为更好的高温增粘剂。
为满足现场生产需要,进一步考察了增粘剂SDT-108的抗剪切能力,所用实验仪器为青岛同春公司提供的变频告诉搅拌机,型号为GJSS-B12K,结果见表2所示。
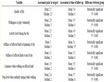
Table 2. Shear resistance evaluation results of solution 2
表2. 溶液2耐剪切评价结果
由表2中实验结果看出,在经过10,000 RPM剪切20 min后,表观粘度下降了18.3%,低于20%,表明增粘剂SDT-108具有良好的抗剪切性能。
4. 无固相水基钻磨液体系构建及性能评价
4.1. 体系构建
结合以往钻磨液应用经验,在上文研制的耐温增粘剂的基础上,结合其他各种单剂的优选,构建一套无固相水基钻磨液体系,并对其进行性能优化。最终配方为:水 + 0.5%聚合物增粘剂(SDT-108) + 0.3%流型改性剂(多糖类高分子化合物) + 0.2%复合增效剂 + 0.1%杀菌剂 + 0.05%消泡剂,各种单剂用量可根据不同性能要求加以调整。
4.2. 性能评价
对所构建的钻磨液进行体系性能评价,摩阻系数测试仪器为青岛海达通公司提供的润滑仪,型号为MOD.EP-B;密度测试仪器为青岛海达通公司提供的YM型液体粘度计。评价结果如表3所示。
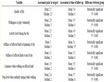
Table 3. System performance evaluation results
表3. 体系性能评价结果
表3中数据显示,本体系钻磨液老化后表观粘度下降17.4%,剪切后下降15.2%,下降率不超过20%,且都达到35 mPa∙s以上,拥有较好的耐温抗剪能力 [14];老化及剪切后的屈服值较高,均大于5 Pa,这利于携带桥塞碎屑出井;极压润滑仪摩阻系数 < 0.1 [15],拥有较好的润滑性,有利于降低泵压及缩短作业时间;密度为1.03 g/cm3,为低密度钻磨液体系。综合以上性能评价结果可以看出此钻磨液体系拥有高携屑、耐温能力强、低摩阻和低密度等优点。
5. 现场应用
5.1. 应用概况
构建的无固相高携屑水基钻磨液已在新疆油田作业区试验及应用二十余口井,均取得了较好的效果,单个桥塞钻除平均时间从40 min减少到20 min,平均单井钻塞时间从5~8 d缩短到2~4 d。作业过程中,泵送压力与循环压耗明显降低,减阻率达60%,卡钻等施工故障次数显著降低,极大提高了连续油管钻除桥塞的效率。
5.2. 应用实例
5.2.1. 现场概况
FNHW4304井是位于新疆风南4井区的水平井,井深4196 m,造斜点为2370 m,水平段上自2794 m至4162 m之间共有19个桥塞(全部为可溶桥塞),井深结构如图1所示,桥塞主要技术参数如下:
适用套管:外径Φ 127 mm,内径Φ 104.8 mm,钢级TP 125 V;
桥塞承压:≥70 MPa;
桥塞承温:70℃~80℃;
卡瓦:适用于TP125 V及以下钢级套管。
现有钻磨液问题为连续油管下井困难,钻磨液粘度下降严重,不能达到携屑要求,这主要是因为现有钻磨液的润滑性能较差,其中的瓜胶遇热分解失效,造成施工事故率高,严重影响除塞效率。
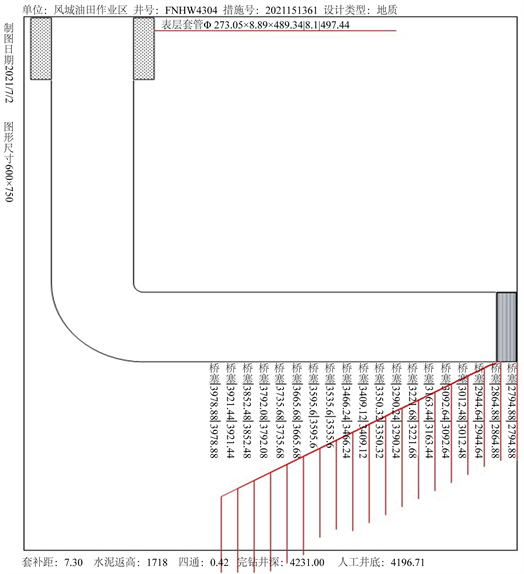
Figure 1. Chart of casing program of Well FNHW4304
图1. FNHW4304井井身结构示意图
5.2.2. 应用实例效果
施工钻压为500 kg,排量为350 L/min,钻遇3620 m处遇阻,在此之前钻除13个桥塞,平均单个桥塞钻除用时不到20 min,总施工时间为19个小时,平均循环压耗为1.5 MPa,反出钻磨液依旧拥有较高的粘度,携屑效果明显,施工中没有出现过因钻磨液问题导致的卡钻等复杂情况,表明此体系钻磨液在FNHW4304井中表现出良好的各项性能,达到了预期的施工效果。
6. 结论
1) 以瓜胶为主的钻磨液体系在高温环境下易降解失效,粘度、切力下降,钻磨碎屑难以返出井口,导致憋泵、卡钻等复杂情况,给低渗透油气藏勘探开发的有序推进提出了巨大的挑战。
2) 本文研制出一种聚合物增粘剂SDT-108以取代瓜胶在钻磨液中的作用,并在与另外一种常用的增粘剂的对比评价中表现出优良的耐温增粘能力。
3) 以SDT-108为核心处理剂构建了一套无固相水基钻磨液体系,并在实验室评价中表现出了良好的增粘、耐温、润滑和抗剪切等性能。
4) 此钻磨液体系在新疆风城油田作业区的试验与应用中表现出了良好的携屑和降摩阻性能,大幅度缩短了施工作业时间并有效降低了施工事故率,为此区块的钻磨桥塞作业提供了一种更好的钻磨液选择。