1. 概述
建筑行业每年钢材表观消费超过4亿吨,占我国钢材总耗用量的50% [1]。然而建筑用钢服役环境普遍较为恶劣,钢材与周围环境易发生化学或电化学作用(称为腐蚀)导致质量损失和机械性能劣化,形成安全隐患。为了减少腐蚀、延长钢材服役时间,表面涂层技术被大量使用,其中应用最广泛的即为防腐涂料。通过在材料表面涂敷防锈漆层以实现隔离钢材与环境,从而实现减缓氧化腐蚀速度,保持钢材或钢结构机械性能的目的。但是,由于钢材服役过程中复杂环境因素和动态荷载影响,漆层下钢材往往在服役一段时间后开始出现局部腐蚀 [2],而此种涂层下腐蚀隐蔽性更强,其在交变荷载下由于强度不足产生的突发性事故更具破坏性;同时,用于腐蚀检测的常规方法,如视觉法、电阻抗法等,因为防腐漆层的阻隔而难以应用。所以,研究漆层下钢材腐蚀的无损检测方法对保障建筑用钢安全具有重要的价值。
工业领域常用的超声(UT, Ultrasonic Test)检测技术 [3],由于超声波在材料表面处产生明显的回波噪声,因而该技术并不适用于钢材表面腐蚀,尤其是早期腐蚀的无损检测。涡流(EC, Eddy Current)和漏磁(MFL, Magnetic Field Leakage)等电磁无损检测技术对导体材料电导率或磁导率变化敏感,因而原理上可以检测钢材表面腐蚀;但是涡流线圈的阻抗变化体现的是探头下方材料电导率的平均变化,而霍尔传感器输出电势反映的是其下方材料因磁导率减小而泄漏的磁场强度 [4] [5] [6],因此上述两种电磁无损检测技术所用探头尺寸限制了其检测分辨率,不利于点蚀等小尺寸腐蚀的检测。近年来兴起的脉冲涡流热成像(ECPT, Eddy Current Pulsed Thermography)技术,因其具有快速和非接触检测表面裂纹的能力而得到广泛关注 [7] [8] [9]。
湖南大学何赟泽 [10] 提出采用ECPT技术结合主成分分析和独立成分分析算法,实现腐蚀空泡的无损检测,并进一步识别无腐蚀区域、腐蚀空泡,以及破裂空泡。虽然独立成分对应不同的温度特征,具有更加明确的物理含义,但同时缺陷特征也被分离,不利于腐蚀轮廓重构。杨瑞珍 [11] 通过分析焦耳热在钢材表面和缺陷表面的生成、辐射过程,提出了基于ECPT技术和快速傅里叶变换的相位分析法,对0~6个月腐蚀的试样进行腐蚀轮廓重构和腐蚀时间无损评估。但是焦耳热的横向传播使得基于相位方法的重构图像轮廓较为模糊,且因为相位选择缺乏客观依据,限制了该方法应用。南京工业大学丁松 [12] 采用像素点温度曲线偏度作为特征,重构涂层下钢材表面腐蚀轮廓,并通过腐蚀区与激励线圈偏度均值的差分,实现对0~6个月不同腐蚀试件的无损评估。但是,由于钢材腐蚀后磁导率和电导率的变化极为复杂,其对温度变化曲线偏度的影响具有显著的非线性特征,因而该差分信号难以区分10~12个月的腐蚀试样。
针对以上问题,本文通过对焦耳热分布深度的理论分析及其对热传导过程的影响,提出基于红外图像主成分分析的漆层下钢材表面腐蚀的轮廓重构和腐蚀时间无损评估方法。实验结果证明,该方法不仅具有客观性强便于工程应用的特点,而且能够准确识别出0~10个月不同腐蚀试样,具有更好的应用前景。
2. 检测原理
2.1. 腐蚀形成机制
钢材与周围环境发生的氧化腐蚀最为普遍,研究其氧化过程及检测方法最具代表性。研究表明,钢材氧化腐蚀是一个缓慢的渐变过程,如图1所示:在材料与环境接触表面最先生成的是氧化亚铁(FeO),之后在氧化亚铁层上再生长出一层氧化铁(Fe2O3);随着氧化进程推移,在氧化亚铁层与氧化铁层之间会形成一层复杂的铁磁性氧化混合物(Fe3O4) [13]。由于腐蚀产物中存在多种铁基氢氧化物,如Fe(OH)、Fe(OH)3、α-FeOOH等,并且出现在腐蚀的不同阶段,所以钢材腐蚀物的电导率、磁导率、热导率等多种参数均随着腐蚀程度而变化,而这也构成了腐蚀无损检测的物理基础。
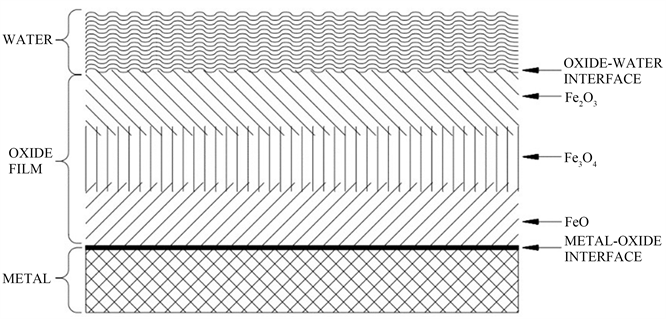
Figure 1. Schematic of oxide corrosion on steel surface
图1. 金属表面氧化腐蚀原理
2.2. 脉冲涡流热成像技术原理
脉冲涡流热成像是一种典型的多物理场耦合无损检测技术,检测系统结构如图2所示,该系统利用交流励磁单元产生的交变磁场在导体材料表面感应产生电涡流;而导体表面的电涡流将依据焦耳–楞次定律(公式1)产生焦耳热:
(1)
其中,Q为导体表面电涡流产生的焦耳热,I为电涡流,R为电涡流流经的材料电阻,t为电涡流存续时间。由公式(1)可知,匀质导体表面产生的焦耳热正比于电涡流的平方,而由于腐蚀区域电导率和磁导率均与无腐蚀区域存在差异,从而产生不同的焦耳热分布。激励停止后,由于焦耳热非均匀分布必然导致被测材料中感应加热区与原理激励线圈的未感应区存在温度差异,从而在高、低温区之间产生热传导,热传导与焦耳热的关系如公式(2)所示 [14]。
(2)
其中,
是被测材料电导率,Js是电涡流密度。
是材料密度,Cp和k分别是材料的比热容和热导率。在这一阶段,由于腐蚀区域与无腐蚀区域的热导率、表面辐射率均存在差异,从而表现为被测材料在停止激励后的热耗散过程及其红外辐射显著依赖于表面腐蚀状态。特别地,由于常用的防腐涂层多为非导电材料,因而对ECPT系统产生的激励磁场没有影响,这也使得ECPT技术成为涂层下金属材料表面腐蚀无损检测与评估的有效手段。

Figure 2. Diagram of ECPT system for corrosion detection
图2. ECPT腐蚀检测系统结构图
由于腐蚀导致材料表面热分布差异,并且腐蚀与未腐蚀材料的表面辐射率也不一样,因此红外热像仪采集被测试样的热辐射信号,并由计算机对数据特征提取和图像重构,以实现对漆层下钢材表面腐蚀的无损识别与评估。
2.3. 红外辐射数据特征提取算法
主成分分析(PCA, Principle Component Analysis)是一种降维和降噪计算方法 [15],其通过计算随机数据的最大方差所在方向及其正交方向,从而将原数据集投影在新向量空间,以呈现数据特征。PCA方法提取数据特征的原理如图3所示,图中1stPC方向为随机信号方差最大的方向,体现了数据分布的主要方向(在PCA中定义为第一主成分,贡献率最大),与其正交且方差次之的方向称为第二主成分(图中2ndPC方向)。由于这一新投影空间包含了原随机数据的主要特征(通常要求85%以上),因而可以用来表征原数据集而不会损失主要信息。
由于腐蚀的存在使得其周围的温度分布不均,产生较大的温度梯度,主成分分析法通过对温度变化较大的图像区域信息进行提取,并将信息包含在第一、第二主成分中。通过对于该第一、第二主成分信息进行图像重构,可以用于识别腐蚀位置和轮廓。
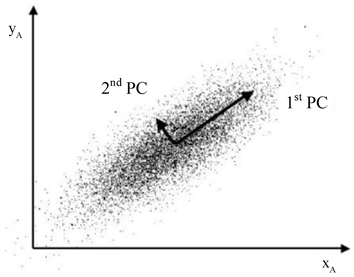
Figure 3. The schematic of feature extraction based on PCA
图3. PCA特征提取原理
3. 实验系统设置
3.1. 实验样本设计
低合金钢因机械性能优异且制备容易,因而在建筑、交通、压力容器等领域应用广泛。本文以工程常用的Q345钢制备试样,其典型成分(重量%)为:C < 0.22,Si 0.05~0.15,Mn < 0.65,Ni < 0.3,S < 0.05,P < 0.04,Cr < 0.3,N < 0.012,Cu < 0.3。试样被切割为300 × 150 × 3 (长 × 宽 × 厚) mm3的板材共计5件;除中间位置留有30 × 30 mm2的方形区域外,其余面积覆上防腐涂层以保持钢材表面初始状态;随后将试样置于腐蚀环境中分别静置1,3,6,10和12个月,使其中间未保护区域发生不同程度腐蚀;待试样腐蚀完成后再用防腐漆覆盖全部表面,只在腐蚀位置做线以标记;试样中间位置腐蚀后表面状态和覆以防腐漆后表面状态如图4所示。
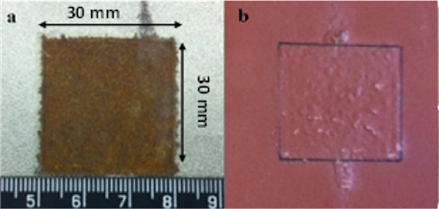
Figure 4. The images of (a) 1 month uncoated sample, (b) 1 month coated rust patch
图4. (a) 一个月腐蚀试样表面(b) 覆以防腐漆层一个月腐蚀试样
3.2. 实验系统设置
本文所用腐蚀检测系统如图5所示,其中脉冲发生器用于同步感应加热源和红外摄像仪,以完整记录材料感应加热和冷却降温全过程。感应加热器选用Cheltenham的EasyHeat224提供380Arms交流励磁电流,其可跟据负载特性自适应调节输出功率。研究表明 [16],钢的电导率和相对磁导率分别为4.68 × 106 S/m和60,而腐蚀产物接近0.75 × 106 S/m和4。故系统将激励频率设置为260 kHz,以在样品表面产生焦耳热。试样表面红外辐射采用FLIR公司非制冷型红外摄像仪A655SC进行数据采集,其满屏(640 × 480 pix)采样率50 Hz,最大帧频可达200 Hz (640 × 240 pix)温度灵敏度小于30 mK。
电涡流分布深度规律可依公式(3)计算:
(3)
式中,f为激励频率,
和
分别是导电材料的电导率和磁导率。考虑到试样材料是铁磁性金属,电导率和磁导率都比较大,由公式(3)计算得钢材未腐蚀和已腐蚀区域电涡流趋肤深度分别为56 μm和570 μm;且实验中设定激励源励磁时间200 ms,因而可视为表面瞬时热源,利于提高红外图像信噪比。
4. 结果与讨论
分析可知,由于红外摄像仪所获取的辐射量矩阵必然含有环境温度波动、仪器自身噪声等干扰因素,因而可将其输出结果视为含有随机噪声的数据集;而焦耳热初始分布取决于材料的电导率、磁导率,热传导过程取决于各点温度差和热导率,所以运用PCA方法从含有随机噪声的数据集中提取主要信息,并依据方差最大原则(各点之间温度梯度也最大)计算数据集主要特征是具有物理依据的可行方法。据此,本文采用Matlab 2016软件对红外热像仪输出的图像序列进行主成分分析,并尝试以PCA方法提取的特征值进行腐蚀图像重构和腐蚀程度评估。
由计算可知,PCA方法所得第一和第二主成分(PC, Principal Component)的贡献率之和接近90%,这意味着前两个主成分分类包含原始热图像序列的大部分信息,因此,本文仅对1st和2ndPC进行分析和讨论。所有样品的第一个和第二个PC的重建图像如图6所示,图中,(a)、(c)、(e)、(g)、(i)是1stPC的图像,几乎无法检测腐蚀区域;然而,(b)、(d)、(f)、(h)、(j)所示2ndPC的重建图像,除10个月腐蚀试样外均可以清楚地看出腐蚀的轮廓。
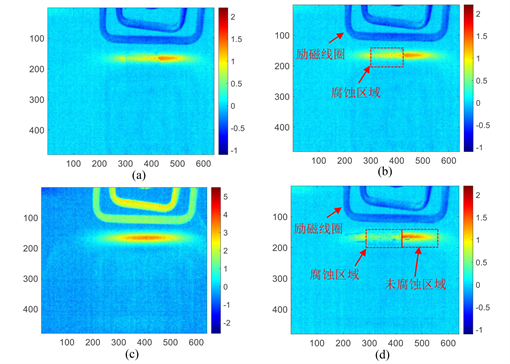
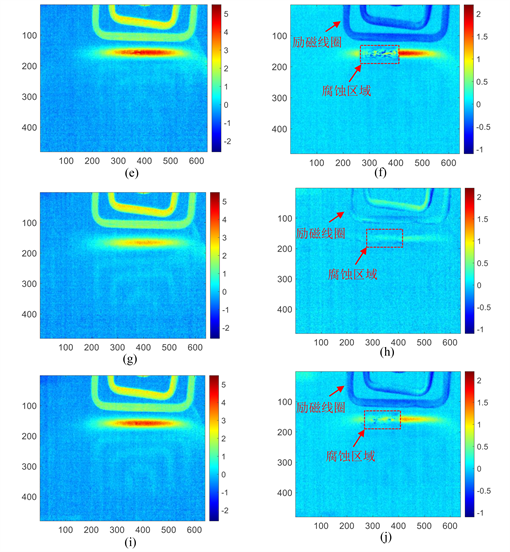
Figure 6. The reconstructed images of (a) 1st PC for 1-month corrosion; (b) 2nd PC for 1-month corrosion; (c) 1st PC for 3-month corrosion; (d) 2nd PC for 3-month corrosion; (e) 1st PC for 6-month corrosion; (f) 2nd PC for 6-month corrosion; (g) 1st PC for 10-month corrosion; (h) 2nd PC for 10-month corrosion; (i) 1st PC for 12-month corrosion; (j) 2nd PC for 12-month corrosion
图6. (a) 1个月腐蚀1stPC重构图;(b) 1个月腐蚀2ndPC重构图;(c) 3个月腐蚀1stPC重构图;(d) 3个月腐蚀2ndPC重构图;(e) 6个月腐蚀1stPC重构图;(f) 6个月腐蚀2ndPC重构图;(g) 10个月腐蚀1stPC重构图;(h) 10个月腐蚀2ndPC重构图;(i) 12个月腐蚀1stPC重构图;(j) 12个月腐蚀2ndPC重构图
图6中可见,虽然主成分一的贡献率最高(由PCA原理可知),意味着其含有原数据集最多的特征信息,但是,以原数据在新坐标系中1stPC轴的投影值重构图像却不能清晰区分腐蚀区域与无腐蚀区域;相反地,主成分二虽然贡献率远低于主成分一,但用原数据集在其上投影值以重构图像却可以清晰分辨,其中3、6、12个月腐蚀尤其清晰,故本文重点对2ndPC重构图像展开分析与讨论。
根据参考文献 [17],感应热功率( )由以下因素决定:
(4)
其中,
是励磁电流,
和f分别是样品的磁导率和励磁频率。
是电导率,它与温度T和
有关。
和
分别是电阻率温度系数和电导率在
时刻。考虑到以下实验的温度变化不超过0.72℃,公式(4)可以
简化为
。在实验设置下,
为常数。基于产生焦耳热的公式(2)和
,公式(4)
可以在相同的加热条件下改写为等式(5)。
(5)
这意味着磁导率的增加和电导率的降低会导致温度升高,即磁导率增加和电导率下降会导致温度上升,这与0个月、1个月和3个月腐蚀的试样的表现一致。进一步地,未腐蚀区域和腐蚀区域中各像素点的最大温度变化(200 ms温度值减去0 ms温度值)加以平均,所有腐蚀试样的最大温度变化列于表1中进行比较。
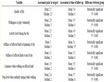
Table 1. The maximum temperature variation of uncorroded and corroded region
表1. 未腐蚀和腐蚀区域的最大温度变化
从表1中可以看出,在1个月和3个月内,未腐蚀区域的最大温度变化低于腐蚀区域。初始腐蚀产物,针铁矿α-FeOOH和赤铁矿α-Fe2O3,的电导率低于钢。此外,赤铁矿显示弱铁磁性,针铁矿在室温下为反铁磁性材料 [18] [19]。根据公式(5),在早期阶段,腐蚀区域的温度升高更明显。然而,随着时间的推移,不仅磁导率和电导率发生变化,而且腐蚀层厚度与表面状态也发生变化(如图7(a)~(c)所示),6个月腐蚀区域表面明显比1个月腐蚀的表面粗糙了许多;而10个月腐蚀表面不仅形状不规则,而且出现明显的分层和剥离。由于腐蚀产物分层,导致涡流和焦耳热的产生均是发生在不同层,且腐蚀物层之间的空气热导率(0.026 × 10−2 W/(mK))远低于钢材(45 W/(mK))本身及其腐蚀产物(0.55 W/(mK))热导率,故而长期腐蚀(10个月及以上)存在更为复杂的热分布和热传导过程。另一方面,随着腐蚀时间增加,腐蚀层厚度也随之增厚(如图7(d)所示),考虑到腐蚀产生产物的电导率、磁导率与钢材差异明显,可知焦耳热的初始分布即比无腐蚀区域要更深。由公式(3)计算可得,未腐蚀区域焦耳热初始分布深度约56 μm,而腐蚀的出现必然引起焦耳热分布深度增加(涡流分布深度增加,能量密度降低),在相同激励电源条件下将导致表面温度降低,与公式(5)形成相互制约,故而表面温度将出现非单调变化,如表1中数据所示。
对比表1中的数据,6个月的腐蚀样品的未腐蚀区域的温度变化高于腐蚀区域。由于腐蚀产物的导电性和磁导率明显小于钢,这导致更深的热分布和更低的表面温度。比较3个月和6个月腐蚀的温度变化,本文认为电导率降低在早期腐蚀中主导焦耳热的产生和初始分布。
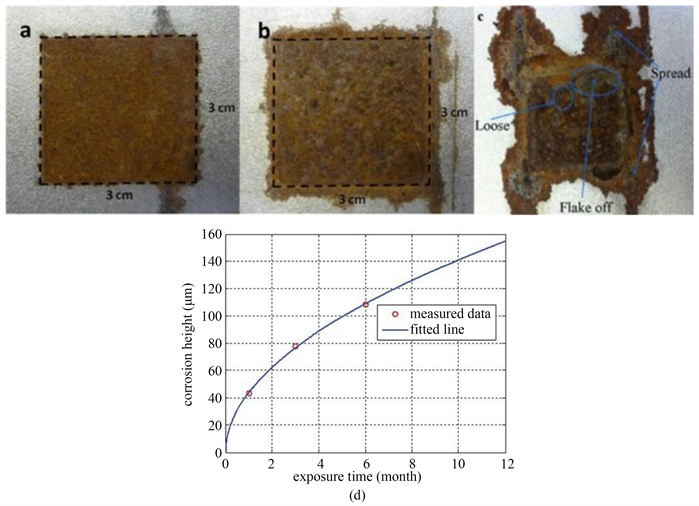
Figure 7. Image of corrosion state: (a) 1 month sample, (b) 6 months sample, (c) 10 months sample, (d) heights versus exposure time [18]
图7. 腐蚀区域表面状态(a) 1个月,(b) 6个月,(c) 10个月,(d) 腐蚀厚度与腐蚀时间曲线
进一步分析表明,焦耳热分布深度增加会导致PCA方法的前提——表面单一热源传导——被破坏,如纯腐蚀区域存在显著的亚表面加热(约570 μm)。这就意味着当励磁电源停止后,未腐蚀区域表面焦耳热在向下传导过程中,还有相邻的来自腐蚀区域的亚表面热源的横向热传导,这将使得传导过程并非仅有单一热源,故而PCA方法仅从原理上分析已无法区分长时间腐蚀所带来的差异。
根据文献 [10] 和 [11] 的热传导模型,在腐蚀区域和未腐蚀区域之间的热传导过程中会产生热波,任何波形都可以近似为不同频率下振荡的纯谐波之和。由于腐蚀区域和未腐蚀区域之间热脉冲波形的相位不同,因此可以采用快速傅里叶变换(FFT,Fast Fourier Transform)方法分析每一像素的相位特征,其基本原理如图8所示。红外热像仪采集热图像序列(图8(a)),其中每帧图像的一个像素点对应值都表示被测材料表面该点的温度值。将P点在对应每帧图像的像素值提取出来,就形成P点的温度变化曲线,该曲线形状如图8(b)所示。
将每一像素点对应的温度值序列视为对温度曲线采样,因此需要离散傅立叶变换将信号分解为不同的频率分量。在本文中,根据以下一维离散傅立叶变换公式计算每像素的温度响应:
(6)
其中,
是采样时间间隔,n表示频率增量,N是采样数,
和
分别是
的实部和虚部。在此基础上可以通过公式(7)和(8)计算采频域信号振幅和相位:
(7)
(8)
本文依据公式(7)和(8)提取特定频率下所有像素的振幅和相位,并以每一像素的相位为特征值重建热图像。
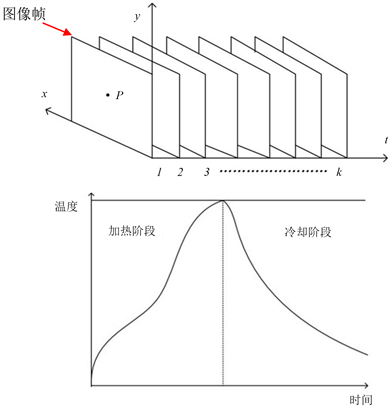
Figure 8. (a) Sequence of thermal images (b) Temperature curve of point P
图8. (a)红外图像序列 (b) P点温度变化曲线
通过红外特征重构图像识别腐蚀区域的基础上,本文在腐蚀区域和未腐蚀区域中(如图6(d)所示)各选取一30 × 80 pix区域,计算各像素点特征值(2ndPC和相位)均值后经归一化处理,以此作为评估腐蚀状态的特征参数,将其与腐蚀时间的对应关系绘制于图9。
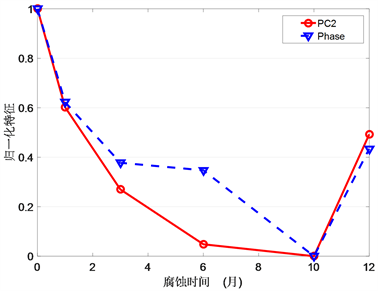
Figure 9. The relations between the corrosion time and the normalized features of the corroded region
图9. 腐蚀时间与区域内特征值均值归一化对应关系
从图9中可以看出,从未腐蚀区域到10个月腐蚀区域,归一化后的第二主成分和相位特征均值均随腐蚀时间单调减小,但是相位特征在腐蚀时间3~6个月过程中仅变化了5%,灵敏度显著小于第二主成分;而从10个月到12个月,随着的腐蚀时间增加,2ndPC和相位都逐步增大,呈现出显著的非单调特性。即便如此,与之前的研究 [10] [11] 相比,基于主成分分析的漆层下钢材表面腐蚀无损检测方法不仅可以满足早期腐蚀检测需要,且灵敏度明显高于现有的相位分析法;此外,第二主成分同样可以实现10个月以内表面腐蚀的识别和无损评估。
5. 结论
针对工程现场易出现的钢材漆层下腐蚀隐蔽性强、危害性大的问题,本文证明了脉冲涡流热成像技术可用于漆层下钢材的表面腐蚀无损检测。由于非均匀加热和环境温度波动影响热图像采集,本文采用了主成分分析方法进行红外图像序列的特征提取、图像重构及腐蚀程度无损评估,经与现有相位分析法比较,本文主要结论总结如下:
1) 虽然第一主成分的贡献更大,但第二主成分的重构图像可以更好地识别腐蚀区域。
2) 对于0~6个月早期腐蚀,第二主成分能够准确识别,并通过图像重构确认腐蚀轮廓。
3) 尽管腐蚀成分和厚度的复杂影响,归一化后的第二主成分仍具有良好的腐蚀评估性能,随腐蚀时间0到10个月单调减小;尤其是针对0~6个月内腐蚀时间无损评估,其灵敏度优于相位分析法。
4) 基于ECPT技术,电导率决定了早期腐蚀的焦耳热产生和分布(深度);然而,对于长期腐蚀(腐蚀时间超过10个月),腐蚀深度的影响加剧,使得红外信号难以表征腐蚀的物理性质。
基金项目
南京市建设行业科技计划项目(Ks2157)。
NOTES
*通讯作者。