1. 概述
目前公司所采用的模压和凝胶注模成型后进行真空压力浸渗制备铝碳化硅复合材料的工艺方法具有一定的局限性,现有成型工艺路线无法制备大尺寸大壁厚的碳化硅预制件,且受预制件孔隙率的限制,无法制备体积分数较低(<40%)的铝碳化硅复合材料;同时,真空压力浸渗工艺受设备尺寸、功能等限制,不能浸渗2系、7系等高强度铝合金,局限了所制备铝碳化硅材料的性能,无法满足某些特定需求。而且加工大、中型结构件只能购买粉末冶金法制备的大尺寸SiCP/Al坯锭进行切割,材料利用率低,加工量大,加工成本高。
粉末冶金(Powder Metallurgy)因其制备的材料具有高强度、高塑性等特点已成为制备复合材料结构件的重要手段。因此,通过对粉末冶金方法制备SiCP/Al复合材料进行总结和研究,选取适合的制备方法,逐步开展粉末冶金法制备SiCP/Al复合材料工艺技术研究,为日后大中型结构件用坯锭的自主开发和降低材料成本打下基础。
SiCP/Al复合材料主要有下列几种制备方法(表1)。
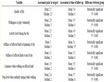
Table 1. Main reparation methods of SiCP/Al composites [1]
表1. SiCP/Al复合材料主要制备方法 [1]
粉末冶金法作为最先应用于制备SiCP/Al复合材料的方法之一,相比其他方法具有成分设计自由度宽,界面反应易于控制和工艺简单等优点,在SiCP/Al复合材料的制备和研究方面具有广阔的应用潜力。其增强颗粒的含量可在0%~70%任意调节,而且增强相分布更为均匀,能够避免高温界面反应的产生,制备过程可控,可实现制品的近净成形(图1) [2]。
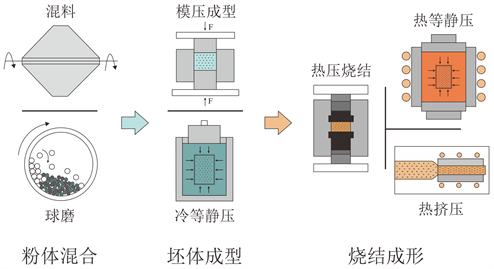
Figure 1. Common process methods of powder metallurgy [3]
图1. 粉末冶金常用工艺方法示意图 [3]
粉末冶金法虽然有一定的不足之处,例如粉末成本高,制品大小和形状受限,韧性较差等;但随着粉末冶金技术的发展,这些问题都在逐步解决,例如粉末热挤压技术和等静压成型技术已能够制备出大型和异形制品,材料性能也得到了明显提高等。
2. 粉末冶金制备SiCP/Al复合材料的选材
(一) 增强体的选取
在工业生产中,制备SiC的主要方法是使用石英砂、石油焦等原料在高温电阻炉中反应炼制出大块的SiC,再经机械破碎、酸碱洗和筛分等多个步骤,最终得到不同粒度SiC粉体,其中通常应用于制备SiCP/Al复合材料的微米级SiC的粒度为3.5 μm~63 μm (w3.5~w63)。
SiC由于具有高熔点(2735℃)、高弹性模量(450 GPa)和低密度(3.2 g/cm3)等优势,能够在一定条件下与合适的铝基体产生良好的界面结合,因此SiCP/Al复合材料能兼具二者的热力学性能。
(二) 基体的选取
基体粉末通常采用雾化法生产出的球形铝粉或球形铝合金粉,其制备方法通常为先将铝金属融化,然后通过雾化喷嘴用高压惰性气体喷出,最后在冷却塔中冷却、气碎和分级得到不同粒度的制品。
常见的SiCP/Al复合材料用铝合金基体有2000、6000、7000系等,需要根据应用领域和技术指标来选取基体的成分和牌号,以达到降低制备成本,提高材料性能的目的(表2)。
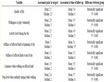
Table 2. Composition and properties of aluminum matrix composites [4]
表2. 铝基复合材料常用基体成分及性能 [4]
(三) 基体和增强体的粒度选取
基体和增强体的粒度选择和搭配非常重要,能够直接影响混料效果,通常二者的粒径选取有下列几种类型(表3)。
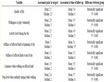
Table 3. Particle size ratio of aluminum matrix and SiC reinforcement
表3. 铝基体和SiC增强体粒径配比
王武杰 [12] 发现当SiC粒径 < 8 μm时,SiC颗粒容易出现团聚现象,导致复合材料的致密度和力学性能降低。
郝世明 [13] 利用Hasselman-Johnson模型较好地预测了SiC颗粒尺寸对SiCP/Al复合材料导热系数的影响,在界面结合基本良好的情况下,复合材料中的SiC颗粒的最小临界粒径为9.6 μm,当SiC颗粒体积分数一定时,随着SiC颗粒尺寸的增加,复合材料导热系数提升;而对于SiCP尺寸大于20 μm的复合材料,SiC颗粒的破裂是复合材料的主要裂纹源。
在制备复合材料时添加镁粉作为助烧剂,利用镁和铝极易在低温反应生成低熔点共晶相,有效破除铝粉表面氧化层,促使SiC颗粒与铝合金基体结合(图2)。
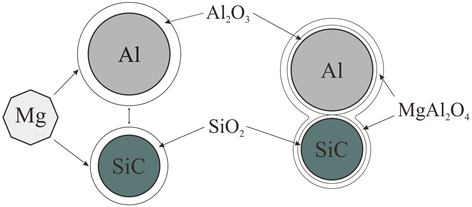
Figure 2. Effect of Mg element on SiCP/Al composites fabricated by powder metallurgy
图2. Mg元素在粉末冶金制备SiCP/Al复合材料中的作用
(四) 增强体的预处理
由于SiC在高温下容易和Al合金发生反应,生成脆性的有害相Al4C3,而SiC表面通过氧化后生成氧化层,能够抑制有害界面反应的发生。但过厚的氧化层反而会降低界面结合强度,影响复合材料性能。
由图3可以看出,SiC表面出现明显氧化层和棱角钝化现象,但在1100℃氧化6 h后,氧化层开始开裂和破碎剥落,会对复合材料致密化产生不利影响。因此可通过控制反应温度和时间调整氧化层厚度,在较低温度(500℃~800℃)对SiC颗粒进行氧化处理。

Figure 3. SiC particle morphology after oxidation at 1100˚C [7]. (a), (d) Oxidation 2 h; (b), (e) Oxidation 4 h; (c), (f) Oxidation 6 h
图3. SiC粉体在1100℃氧化后颗粒形貌 [7]。(a)、(d) 氧化2 h; (b)、(e) 氧化4 h; (c)、(f) 氧化6 h
3. 混料方法
(一) 机械混合
普通机械混料即通过不断旋转和翻滚使粉料间运动方向交叉,大大增加相互接触概率,同时混料机的转速较低,发热量低,能够减少铝基体粉末的氧化机会。常用的混料设备主要有Y(V)型混料机、双锥混合机、真空混料机等。
(二) 球磨混合
球磨的原理是在重力和离心力的配合下,运动的球磨介质对物料施加冲击、摩擦和剪切力而使其均匀混合。常用的球磨设备主要有卧式球磨机、搅动球磨机、行星球磨机等。
高能球磨制备的材料颗粒分布均匀性优于机械混合,其中,高转速、长时间的球磨有利于颗粒分布均匀化,与延长球磨时间相比,提高球磨速度对改善SiC颗粒的分布更有效。从图4(c)可以看出,高能球磨能够将球形Al粉挤扁成片状和长条状;棱角尖锐的SiC颗粒在一定程度上被整形,使两者能够更好地均匀混合。中低体分SiCP/Al复合材料由于SiC含量较少,在球磨混料过程中实际上是在将SiC粉体“挤”进Al粉体中。
球磨方式主要分为干法球磨和湿法球磨两种,干法球磨不添加液态介质,但对于易氧化的粉体来说,需要通入保护性气体或过程控制剂(如硬脂酸)。而采用湿法球磨不仅能够使原料混合更加均匀,所加入的球磨介质还能够有效隔绝空气,避免Al合金粉在球磨过程中因摩擦生热而发生严重氧化。
当球磨机转速较高时,如图5(b)所示,这时物料不仅靠球与球之间的摩擦作用,也靠球落下时的冲击作用混匀,此时的效果最好。
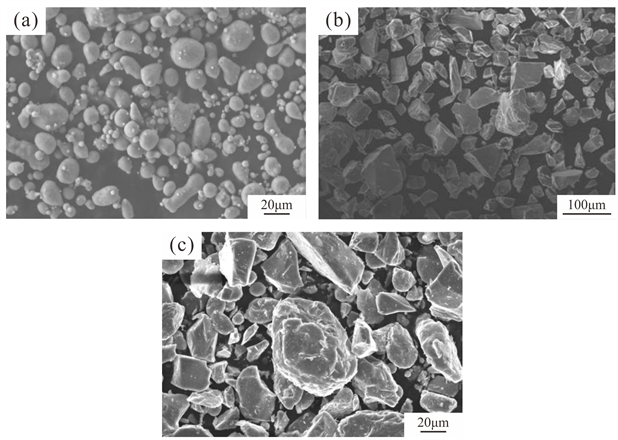
Figure 4. SEM image of high energy ball milling mixture [7]. (a) Pure Al powder before ball milling; (b) SiC particles before ball milling; (c) Mixed powder after ball milling
图4. 高能球磨混合SEM图 [7]。(a) 球磨前的纯Al粉;(b) 球磨前的SiC颗粒;(c) 球磨后的混合粉体
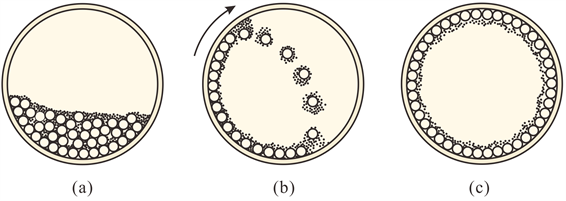
Figure 5. The state of ball and material at different rotational speed of ball mill tank [2]. (a) Low speed; (b) Suitable speed; (c) Critical speed
图5. 球磨罐转速不同时球和物料的状态 [2]。(a) 低转速;(b) 适宜转速;(c) 临界转速
4. 坯体成型方法
成型是粉末冶金工艺过程的第二道基本工序,是使混合粉末密实成具有一定形状、尺寸和强度坯体的工艺过程。主要分为普通模压成型和特殊成型两大类,后者包括等静压成型、挤压成型和轧制等。
(一) 模压成型
模压成型又叫做冷压成型,是将混合粉末装入钢模中通过模冲对粉末加压,卸压后将压坯从阴模中顶出的工艺过程。
在压制过程中,无论是单向压制还是双向压制都会出现压坯密度分布不均匀的现象,原因主要是粉末颗粒与钢模壁之间摩擦引起压制压力沿压制方向的压力损失,使压制过程中力的传递和分布发生改变(图6)。
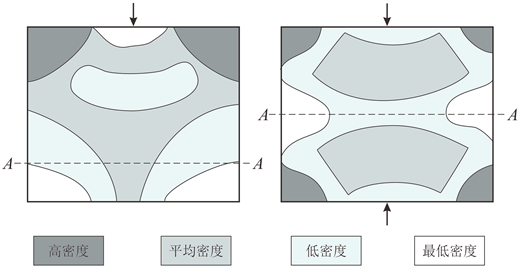
Figure 6. The density distribution of single and bidirectional compacts [2]
图6. 单、双向压坯的压坯密度分布图 [2]
在实际操作过程中可以采用将粉体装入薄壁金属包套后模压并结合专用模具使压力分布更均匀,进而提高压坯质量和生产效率。
(二) 冷等静压成型
冷等静压的压制过程与冷压成型不同,流体介质传递压力是各项相等的,所采用的弹性模套(如橡胶)本身受压缩变形与粉末颗粒受到的压缩大体一致,因此它们之间的摩擦力很小,压坯沿纵断面的密度均匀分布。
郝心想等 [6] 在其专利中将混合粉末包套进行冷等静压成型并对坯锭除气,进行热等静压致密化烧结,制备出组织均匀致密,轻质高强度的颗粒增强铝铜基复合材料。
冷等静压在实际操作中需要注意装模和脱模过程,升压过快容易出现中心密度低的现象,压制结束后卸压也不宜过快,容易造成压坯开裂。
5. 烧结方法
烧结是粉末冶金生产过程中最基本的工序之一,从根本上来说,粉末冶金是由粉末成形和烧结这两道基本工序组成的,同时,烧结也是制备粉末冶金制备SiCP/Al复合材料的最后一道重要工序,对产品质量起着“把关”作用。
(一)热压烧结法
热压烧结由于加热和加压同时进行,使混合粉体处于热塑性状态,有助于颗粒的接触扩散和流动传质的进行,能够增强铝基体与SiC增强体的结合,有效提升材料致密度,实现高性能SiCP/Al复合材料的制备(图7)。
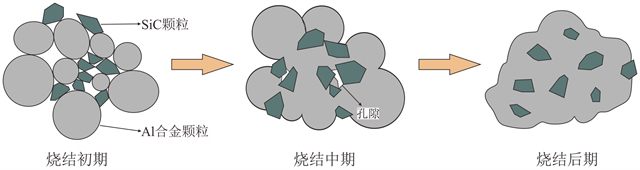
Figure 7. Hot pressing sintering process diagram
图7. 热压烧结过程示意图
从图8中可以看出,当热压温度在580℃~600℃时界面清洁,结合良好,复合材料的强度和塑性均为最佳值;当温度高于620℃时,界面开始出现MgAl2O4和Al4C3脆性相,会使力学性能下降,增加腐蚀敏感性,降低界面强度。因此,当采用热压烧结法制备SiCP/Al复合材料时,为避免或减少有害的界面反应发生,应严格控制热压烧结温度。
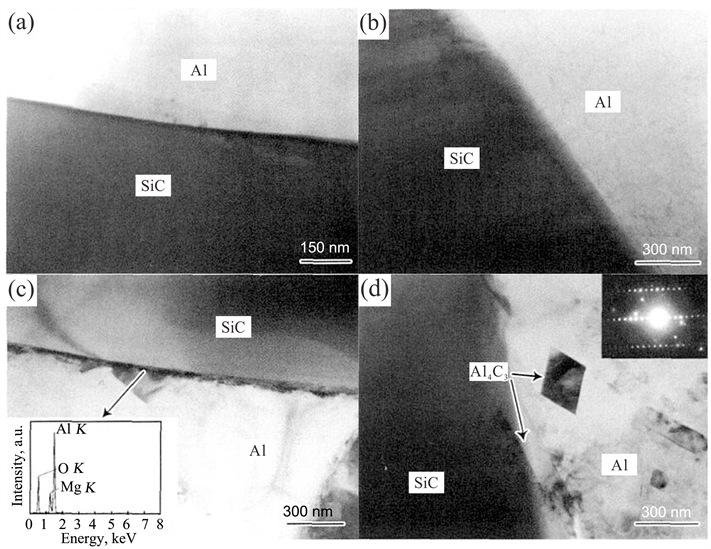
Figure 8. Interfacial TEM images of SiCP/2009Al composites prepared at different hot-pressing temperatures [11]. (a) 580˚C; (b) 600˚C; (c) 620˚C; (d) 640˚C
图8. 不同热压温度制备的SiCP/2009Al复合材料界面TEM图 [11]。(a) 580℃; (b) 600℃; (c) 620℃; (d) 640℃
金鹏等 [11] 研究了真空热压温度对15 vol.% SiCP/2009Al复合材料的微观组织和力学的影响,发现复合材料的致密度在580℃时达到最大值。
王东等 [5] 在其专利中分别在铝镁共晶温度以上的460℃和580℃~620℃进行分步热压烧结,制备出性能优异的大尺寸高体分SiCP/6061Al坯锭。
热压烧结法能够对SiCP/Al混合粉体进行长时间真空保压烧结,使其界面充分结合,制备出性能良好的高致密复合材料,但其设备成本较高,需要较长时间的工艺试验进行摸索。
(二) 热等静压法
热等静压法是将粉末压坯或把粉末装入包套后置入热等静压及高压容器中,利用惰性气体对热等静压模具中的物料进行各向均匀加压的同时加热烧结成型得到复合材料的加工工艺(图9)。热等静压处理能够有效消除合金中的微观孔洞,通常通过热等静压法制备或强化的复合材料组织分布均匀,无偏析、缩孔和气孔等缺陷,综合性能良好。
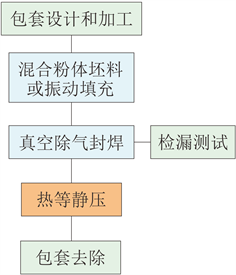
Figure 9. Hot isostatic pressing process flow diagram
图9. 热等静压法工艺流程图
修子扬等 [14] 采用热等静压对挤压铸造法制备的45 vol.% SiCP/Al复合材料进行二次加工后,致密度从原有的95.6%提高到99.2%,内部缺陷大大减少。同时材料硬度提高20%以上,力学性能明显上升。
热等静压技术虽然能够很好的制备和强化其他方法制备出的SiCP/Al复合材料,但目前国产热等静压设备差距较大,数量较少,且成本高昂,应用程度不高。
(三) 粉末热挤压法
粉末挤压成形技术是在金属与塑料加工的挤压工艺基础上演化而来的一种粉末冶金成形技术,一方面热挤压可以直接加工成形零部件,另一方面热挤压也可以提高复合材料的强度和塑性(图10)。其基本原理是在较高温度下使粉末体发生软化,形成黏性流体而产生黏性流动,然后在压力的作用下进入模具而成形为所需形状的致密部件。
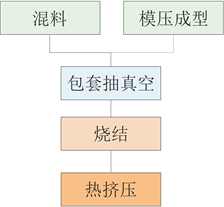
Figure 10. Process flow chart of powder hot extrusion
图10. 粉末热挤压法工艺流程图
郝世明等 [15] 在其专利中通过热挤压法提高热压烧结坯体的材料致密度,改善SiC颗粒均匀分布,提升了中低体分复合材料强韧性,使热力学性能明显提升。
王全兆等 [8] 在其专利中将SiC颗粒与2系或6系Al合金粉末装入金属包套内封焊,在普通电阻炉内加热的同时采用真空抽气装置进行抽气,再移至压机下进行热压复合,制得的SiCP/Al复合材料热力学性能良好,坯锭直径能够达到2 m。
粉末热挤压法对于包套的密封性和粉体的均匀度要求较高,需要保持长时间真空环境防止基体粉末氧化,此方法更适用于大型简单形状复合材料件的制备。
(四) SPS等离子烧结
放电等离子烧结工艺(Spark Plasma Sintering, SPS)是通过脉冲电流产生的等离子体活化金属粉末,降低其烧结温度,对烧结粉末施加压力产生热塑变形,并快速冷却,最终获得结构组织均匀,综合性能优异的复合材料的技术 [16]。
放电等离子烧结采用通-断直流脉冲电流产生放电等离子,使混合颗粒自身产生焦耳热并表面活化,进而使混合粉末自身发热进行烧结,其过程可视为颗粒放电、导电放热和加压的综合作用(图11)。
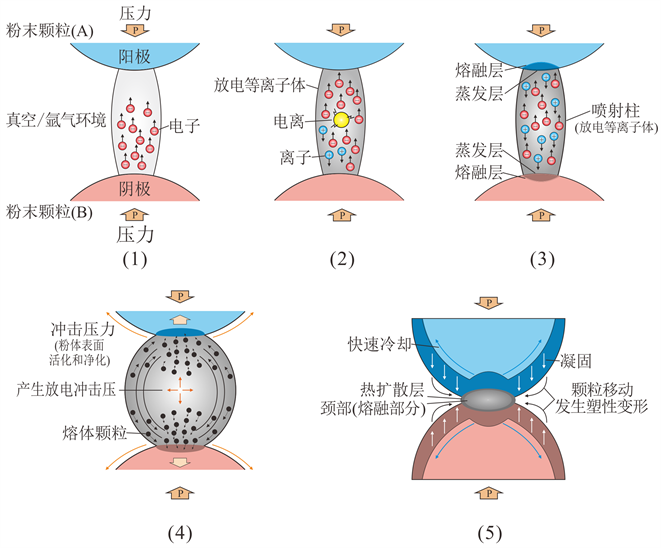
Figure 11. The process of spark plasma sintering [17]. (1) The initial stage of pulse discharge; (2) Discharge plasma generation; (3) Melting and evaporation of powder particle surface; (4) Generating discharge impact pressure and evaporation of molten particles; (5) Formation of sintering neck
图11. 放电等离子烧结过程示意图 [17]。(1) 脉冲放电初始阶段;(2) 放电等离子体生成;(3) 粉末颗粒表面的熔融和蒸发;(4) 产生放电冲击压和蒸发熔融颗粒的喷射;(5) 烧结颈形成
与其他工艺相比,SPS的优势十分明显:烧结温度低、时间短,烧结物的组织细小均匀、致密度高,可烧结复杂工件。而且SPS设备操作简单,生产门槛低,有利于复合材料的规模化生产(图12)。
王韬 [7] 采用高能湿磨混合工艺制备SiCP/Al复合粉体,利用SPS烧结技术保温10 min制备出的52 vol.%试样平均热导率为204 W/(m∙K),平均热膨胀系数为11.50 × 10−6/K。
康鹏超和武高辉 [9] 在其专利中将SiCP/Al复合粉体与粘结剂造粒后冷压的素坯置于放电等离子烧结炉中在真空或氩气环境下烧结即得SiCP/Al复合材料。
对于实际生产来说,SPS技术需要增加设备的多功能性和脉冲电流的容量,也需要研制比石墨模具强度和重复使用率更高的新型模具材料。
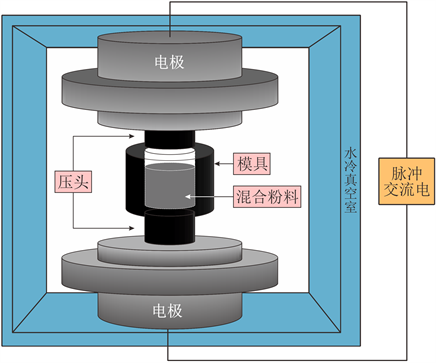
Figure 12. SPS sintering device schematic diagram [7]
图12. SPS烧结装置示意图 [7]
(五) 粉末触变成形
粉末触变成形技术综合了粉末冶金和触变成形两种技术的优点,使用了粉末冶金的混粉、压坯步骤和触变成形的部分重熔和成形步骤。克服了粉末冶金制备材料组织疏松和触变成形增强体较难复合和分布不均的缺点(图13)。
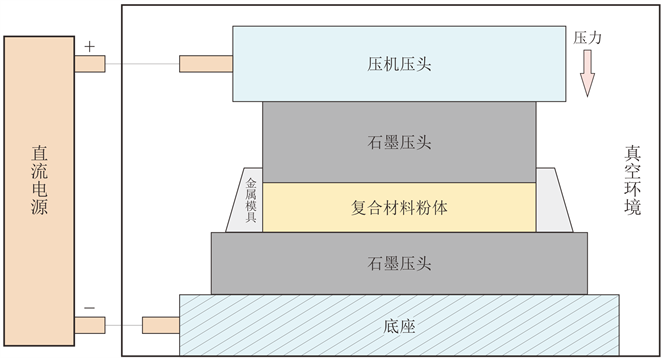
Figure 13. Schematic diagram of powder thixoforming sintering device [10]
图13. 粉末触变成形烧结装置示意图 [10]
汪洋 [10] 通过对SiC颗粒进行氧化和整形后,采用直热法粉末触变成形技术,结合热处理工艺制备的60 vol.% SiCP/2024Al复合材料,其微观组织致密,增强体颗粒无团聚现象,材料热导率达到了202 W/(m∙K),抗弯强度可达425 MPa。
影响该方法制备复合材料的因素较多且较难控制,还需要对材料进行较高温度的重熔,目前还没有专门的大型设备用于工业生产。
6. 结论与展望
通过项目组前期的研究工作和制备试验,发现粉体粒度的选择至关重要,SiC颗粒的预氧化时间过长,温度过高都会使粉体发生板结。而在最后的成形阶段,相比粉末与模具直接接触,采用金属包套后热量散失更少,材料的密度分布也更为均匀。
项目组采用粉末热挤压法制备的低体分SiCP/Al复合材料抗弯强度可以达到600 MPa以上,且具有一定的塑韧性,取得了阶段性成果,但仍与国内领先水平在热力学指标上具有一定差距,还需要进一步的性能调配和工艺优化研究工作。
SiCP/Al复合材料以其优异的性能在航空航天、电子封装等领域获得了广泛应用,为促进粉末冶金制备出SiCP/Al复合材料的进一步发展,更好地满足严格的工程需求,我们仍需加强以下研究:
1) 传统粉末冶金法依赖昂贵的真空热压烧结炉或热等静压炉,因此需要对现有粉末冶金方法不断改进和创新,突破对高成本大型设备的严重依赖,制备出高性能的SiCP/Al复合材料。
2) 结合粉末冶金新工艺新方法和先进可重复使用的精密模具设计,使粉末冶金法具备近净成形的优点,在保证材料性能的同时,大大减少机加成本,提高生产效率。
3) 根据SiCP/Al复合材料性能可设计可调控的特点,形成SiCP/Al复合材料成分库,通过应用场景和材料性能要求,结合仿真模拟,从材料成分、工艺等方向提升材料的综合性能。
参考文献