1. 引言
随着科学技术与信息产业的发展,现代工业产品正在向高度集成化、轻型化、智能化的方向发展,而钕铁硼永磁材料作为磁性材料中的“磁王”,其磁能积、矫顽力和剩磁都是最高的,使其在风力发电、新能源领域、工业机器人等领域具有广阔的应用前景 [1] 。一方面,NdFeB永磁材料的制造工艺一般为粉末冶金工艺,导致其在成型过程中容易在磁体表面形成微裂纹和微孔隙等缺陷,这导致在使用环境中的腐蚀介质容易通过磁体表面的缺陷进入磁体内部造成磁体的腐蚀,使磁体磁性能降低 [2] 。另一方面,NdFeB永磁材料中存在的多相结构以及各相之间的电位不同导致磁体内部容易形成原电池腐蚀,使其固有的耐腐蚀性不足。因此易于氧化 [3] 。且据研究结果表明 [4] - [9] ,NdFeB磁体的腐蚀主要发生在潮湿温热的环境中、高温环境中以及自身电化学腐蚀中。
工业上常用的钕铁硼磁体的抗腐蚀方法有元素添加法和表面涂层法 [10] [11] 。添加合金元素可以改善磁体自身的耐蚀性,但有时会降低磁性能,而且添加合金会提高生产成本,这限制了该方法的应用。表面涂层法主要有化学镀 [12] 、电沉积 [13] 和有机涂层 [14] 等。由于化学镀的镀液会添加众多的添加剂,所以会造成较重的环境污染问题。有机涂层虽然抗酸碱腐蚀的能力优秀,但其不耐高温潮湿的环境和抗老化性能较弱的缺点同样限制了其在工业生产中的应用。目前工业上主要以电沉积的方式在NdFeB磁体表面制备防护镀层。可用于NdFeB磁体表面电沉积的元素有Ni、Cu、Zn、Sn、Cr等,这其中常用的有电沉积Ni、Zn,目前NdFeB磁体主要以表面电沉积防护涂层提高磁体的抗腐蚀能力为主。可用于钕铁硼稀土永磁材料的电沉积的元素有Zn、Ni、Cu、Cr、Sn、Au、Ag等,工业上常用的有 [15] [16] [17] 电沉积Zn、电沉积Ni、电沉积Ni-Cu-Ni。除此之外研究人员还研究 [18] [19] [20] [21] 了电沉积 Zn-Ni,Ni-Co,Ni-Cr合金镀层以及Ni-P非晶态镀层等。
相比于纯Zn镀层,Zn-Ni合金镀层具有更好的抗腐蚀性能和力学性能,具有高耐蚀性、稳定的γ相单相组织的Zn-Ni合金镀层的耐蚀性比纯Zn镀层高5到8倍 [22] 。Zn-Ni合金镀层还有优良的力学性能,可塑性好,易于焊接,其氢脆性很小,耐高温,硬度高,非常适合作为钕铁硼材料的防护镀层。一般Zn-Ni合金镀液体系主要分为酸性和碱性两种,碱性体系的镀液阴极电流效率较低、沉积效率差。而酸性镀液体系具有镀液成分简单、容易维护、阴极电流效率高的优点,可镀较复杂零件。因此,本实验采用酸性醋酸盐体系在NdFeB磁体表面电沉积Zn-Ni合金镀层,研究了电沉积参数和基体粗糙度对磁体表面电沉积Zn-Ni合金镀层的微观形貌、组织结构、抗腐蚀性能及膜基结合力的影响。
2. 实验材料及方法
2.1. 实验药品和材料
本实验采用牌号为50 M、尺寸为直径10 mm、高5 mm的圆柱形钕铁硼磁体作为阴极待镀基体,以石墨电极作为阳极。实验药品有氯化锌、氯化镍、氯化钾、硼酸、柠檬酸、醋酸铵、糖精钠、氢氧化钠、碳酸钠、十二水合磷酸钠、草酸、硫脲、磺基水杨酸、氟氢化铵、甲酸、氨水,纯度均为分析纯。
2.2. 电沉积锌镍合金镀层工艺
钕铁硼磁体的电沉积工艺步骤如下:
基体胶封24 h (只露出待镀面)→打磨(400 #~1200 #的SiC砂纸)→酒精超声清洗→抛光→酒精超声清洗烘干→碱洗除油→无水乙醇超声清洗(3 min)烘干→酸洗除锈→无水乙醇超声清洗烘干→活化→冷热水冲洗试样表面→无水乙醇超声清洗烘干→电沉积→冷热水冲洗试样表面→酒精超声清洗烘干→性能表征。
碱洗液由碳酸钠(20 g/L)、氢氧化钠(5 g/L)、和磷酸二氢钠(60 g/L)组成,用甲酸和氨水调节PH至9~9.5,超声除油时间不宜太长否则基体表面会被氧化。
酸洗液由草酸(60 g/L)和硫脲(0.5 g/L)组成,酸洗除锈10~15 s。
活化液由磺基水杨酸(20 g/L)和氟氢化铵(12 g/L)组成,活化液时间30 s。
镀液组成为:ZnCl2 80 g/L、NiCl2∙6H2O 120 g/L、KCl 120 g/L、H3BO3 30 g/L,CH3COONH4 50 g/L、柠檬酸2 g/L、糖精钠0.5 g/L。
电沉积参数为:温度40℃~55℃,电流密度5~20 mA/dm2、pH 5.0、电沉积时间30 min、基体表面状态为400 #砂纸打磨~1200#砂纸打磨和基体抛光,两电极间距20~30 mm,搅拌转速200~300 rmp。
注:为避免酸洗和活化过程对基体粗糙度产生影响,在探究粗糙度的影响时400#、800#、1200#砂纸处理过的基体不进行酸洗和活化两个步骤。
2.3. 镀层性能表征
2.3.1. 形貌结构相组成
本实验采用JSM-7001F型扫描电子显微镜(SEM)来表征制备的Zn-Ni合金镀层的微观形貌,用扫描电镜自带的能谱仪(EDS)分析镀层的化学成分。采用Ultima IV型X射线衍射仪(XRD)分析Zn-Ni合金镀层的晶相结构和晶粒大小,采用Cu靶,波长为0.154056 nm,测试角度为20到80度,扫描速度为:0.02˚/s。
2.3.2. 抗腐蚀测试
采用CS350H电化学工作站测试制备的Zn-Ni合金镀层的动电位极化曲线和交流阻抗图谱。动电位极化曲线测试在三电极体系中进行,其中工作电极为有Zn-Ni合金镀层的钕铁硼试样,辅助电极为表面积10 mm × 10 mm的Pt电极,参比电极为饱和甘汞电极(SCE),测试溶液为3.5 wt%的NaCl溶液,扫描范围为相对于开路电位 ± 0.25 V,扫描速度为0.5 mV/s,实验温度为室温25℃。交流阻抗(EIS)测试体系和动电位扫描一样,当试样在溶液中相应的开路电位稳定在10 mV以内时开始测试,频率范围为10−6 Hz~10−2 Hz,交流正弦波幅值为10 mV,利用塔菲尔区线性拟合获得自腐蚀电位(Ecorr)和自腐蚀电流(Icorr),采用ZSimpWin软件对EIS图拟合其电荷转移电阻Rp。
2.3.3. 膜基结合力和硬度测试
采用YH-1000万能材料实验机对基体与镀层之间的结合力进行测试。使用的是拉拔法,利用公式P = F/S,P是结合力,F是拉断镀层与粘合工装时所达到的力,S是试样的横截面积。采用HV-1000显微硬度计测试镀层的硬度,根据测试的试样镀层面积,均匀选取5个不同的点分别测试,取平均值作为镀层的硬度,以HV表示,测试时荷重200 N,加压时间10 s。
3. 结果与讨论
3.1. 锌镍合金镀层的微观形貌和成分分析
图1为不同工艺参数下制备的Zn-Ni镀层的SEM图,采用抛光基体、沉积温度为55℃、沉积时间30 min时,不同电流密度下制备的镀层如图1(a)~(d),从形貌可以看出,当电流密度较小为电流密度为5 mA/cm2时,锌镍合金镀层由许多亚微米颗粒团簇组成(见图1(a)),这是由于阴极极化较弱导致形核功率较低从而导致晶粒粗大,使得镀层粗糙不致密,此时光泽度不好,颗粒间有部分孔隙,EDS测得的Ni含量为26.16 at%。当电流密度增大到10 mA/cm2时,阴极极化加强,此时形核功率增加结晶性变好,使得镀层晶粒变得细致(见图1(b)),亚微米颗粒团簇已经消失,镀层逐渐致密,孔隙率下降,镀层变得更加平整有光泽。当电流密度继续增大到15 mA/cm2,制备的镀层表面出现具有丝状的晶粒簇,这可能是由于晶体的形核功率大于生长功率镀层晶粒进一步细化(见图1(c)),使得致密性较电流密度为10 mA/cm2时制备的镀层略有提升。当电流密度增大到20 mA/cm2时,此时较大的电流密度可能导致阴极表面析氢严重从而使得镀层表面变的疏松多孔不致密(见图1(d)),孔隙率大大提升。
在基体抛光、沉积时间30 min和电流密度为15 mA/cm2下,用不同的电沉积温度所得的镀层形貌如图1(e)~(h)所示,当电沉积温度为40℃时,较低的沉积温度导致了较低的沉积速率从而使得镀层生长不完整,镀层颗粒粗大、疏松多孔、不致密不完整(见图1(e));当电沉积温度为45℃时,如图1(f)所示,温度的提高使得沉积速率增加使得镀层生长加快,镀层孔隙率开始下降且变得致密,但颗粒间仍然有沟壑存在;当电沉积温度为50℃,如图1(g)所示,镀层颗粒变得均匀、细致、完整,颗粒间沟壑逐渐消失,致密度有较大提升;当电沉积温度为55℃,如图1(h)所示,较高的沉积温度使得镀层晶粒生长速率较高,镀层晶粒生长的更加完整使得镀层更加平整。
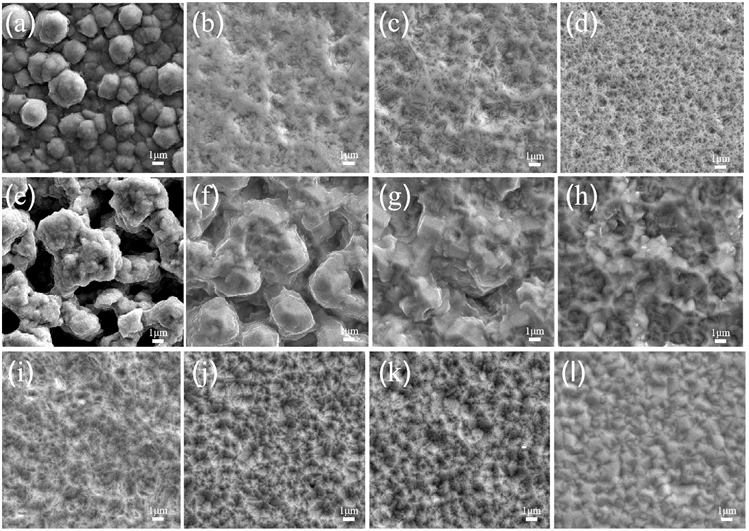
Figure 1. Surface morphologies of the Zn-Ni coatings prepared under different parameters: (a) I = 5 mA/cm2; (b) I = 10 mA/cm2; (c) I = 15 mA/cm2; (d) I = 20 mA/cm2; (e) T = 40˚C; (f) T = 45˚C; (g)T = 50˚C; (h) T = 55˚C; (h) 400#; (i) 800#; (j) 1200#; (k) Polished
图1. 不同参数下制备的Zn-Ni镀层表面形貌(a) I = 5 mA/cm2;(b) I = 10 mA/cm2;(c) I = 15 mA/cm2;(d) I = 20 mA/cm2;(e) T = 40˚C;(f) T = 45˚C;(g)T = 50˚C;(h) T = 55˚C;(h) 400#;(i) 800#;(j) 1200#;(k) Polished
在沉积温度为55℃时,电流密度为15 mA/cm2下,沉积时间30 min,不同基体粗糙度所得镀层形貌如图1(h)~(k)所示,基体采用不同目数的金相砂纸打磨、抛光后,制备的镀层表面形貌相似,这可能是由于仅改变基体粗糙度不会改变晶粒的生长速率从而使得镀层生长形貌相似。镀层均为山峰形颗粒组成,颗粒间紧密结合,颗粒以一定的晶面生长,成多棱形山峰。能看到图1(c)、图1(h)和图1(l)在相同工艺下的镀层形貌出现不同,可能是在不同批样品制备过程中机械搅拌速度和电极之间的放置距离不同导致的。
表1给出了了不同参数下制备的Zn-Ni镀层的Ni含量,可以看出,镀层的Ni含量在19.7 at%到26.16 at%范围,随着电流密度的升高,镀层中的Ni含量在不断下降,这可能是由于阴极析氢反应和Zn-Ni异常共沉积导致的,随着析氢反应不断消耗阴极附近镀液中H+会促进阴极表面Zn(OH)2的生成,在阴极表面吸附的Zn(OH)2会在阴极继续放电,此时不会妨碍Zn2+的沉积,但会阻碍Ni2+的沉积 [23] 。由表1可知,随电沉积温度不断升高,镀层的Ni含量逐渐增加,这是因为随着电沉积液温度的升高,一方面体系能量升高,传质过程变快使得阴极极化减弱,这会使得Ni2+的析出电位正移,析出更容易,另一方面温度的升高使得析氢反应加剧阻碍了沉积液中金属离子的沉积导致浓差极化变大,阻碍了锌镍异常共沉积的进行,更有利于Ni2+金属的沉积。由表1可知,采用不同目数的金相砂纸打磨的基体或抛光的基体,制备的镀层Ni含量变化不大,可见,基体表面粗糙度对镀层成分几乎没有影响。
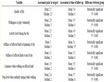
Table 1. Ni contents of the Zn-Ni coatings prepared under different parameters
表1. 不同参数下制备的Zn-Ni镀层的Ni含量
3.2. 镍锌合金镀层的相组成分析
图2给出了不同工艺条件下制备的锌镍镀层的XRD图谱。由图2可以看出几乎所有镀层的相结构都呈现为γ相的Ni5Zn21,并且具有(600)面取向生长的特点,部分合金还有镍的存在。有研究认为 [24] ,Zn-Ni镀层如果为单一的γ相,由于其为单相金属间化合物,有较好的热力学稳定性,因而耐蚀性最高。从电化学上考虑,由于不同锌镍合金的电势具有η相 < γ相 < α相,如果镀层为复相结构的合金,因为两相具有不同的腐蚀电势,故它们之间容易形成腐蚀微电池,降低了抗腐蚀性,而如果Zn-Ni合金由单一的γ相构成,无腐蚀微电池产生,因而耐蚀性会很好。所有的XRD图谱,在2θ的角度为42.5˚和62.5˚左右都出现了(330)和(600)晶面。有些镀层在44˚左右出现了面心立方的Ni(111)晶面,说明镀层中出现了镍。这可能是由于在较低电流密度5 mA/cm2和10 mA/cm2下,较弱的阴极极化使得Zn-Ni异常共沉积反应较弱,使得Ni2+的沉积比较高电流密度时的阻碍更弱,因此N2+的析出更多,这导致了Ni的出现。而在沉积温度40℃下,较低的沉积温度一方面同样会使异常共沉积反应减弱,而Ni2+的沉积电位比Zn2+更高 [25] ,这更有利于Ni2+的析出,另一方面温度较低时,体系的能量更低,这可能会导致Ni2+更难进入Zn-Ni合金晶格中,使得一部分Ni的单独析出,从而导致Ni的出现。
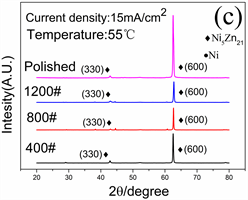
Figure 2. XRD patterns of the Zn-Ni coatings prepared under different parameters
图2. 不同参数下制备的Zn-Ni镀层的XRD图谱
从图2(a)可以看出,锌镍镀层按(600)面取向生长,且随着阴极电流密度的不断增加,(600)面的峰强在不断增强,这可能是由于电流密度越大导致镀层生长越厚。在电流密度较低时有Ni(111)晶面出现,当电流密度增加到15 mA/cm2之后Ni(111)晶面消失,由于阴极极化的增强使锌镍异常共沉积反应变强导致镀层Ni含量降低,镀层转变为单一γ相的Ni5Zn21。从图2(a)还可以看出,当温度升高时,(600)和(330)面的峰强比在不断增强,说明提高温度可以使镀层晶粒按(600)面取向生长,但在温度较低时,较低的体系能量导致了Ni(111)面的出现。不同粗糙度下的镀层XRD几乎也是表现出很强的按(600)面取向生长,且此时电流密度和沉积温度都较高,因此,没有Ni(111)面的出现。
图3是锌镍镀层晶粒尺寸和硬度随电沉积参数的变化,晶粒尺寸是根据XRD谱的(600)面的衍射峰的FWHM,用Scherrer公式(1)来计算锌镍合金镀层的晶粒尺寸。
(1)
式中K为Scherrer常数(取0.89),D为晶粒尺寸(单位:nm),β为积分半高宽度(单位:rad),θ为衍射角,λ为入射X射线波长。由图可见晶粒度对硬度有决定性的影响,变化趋势和晶粒度保持一致。
在不同电流密度下制备的锌镍镀层晶粒尺寸在39 nm到57 nm之间,硬度在509 HV~548 HV。随着阴极电流密度的增加,锌镍镀层晶粒尺寸先减小后增大,当电流密度为15 mA/cm2时,锌镍镀层的晶粒尺寸最小为39 nm,此时镀层的硬度达到最大,电流密度继续增加时晶粒尺寸重新增大。这可能是由于当电沉积电流密度较小时,形核功率小,晶体的生长功率大于形核功率导致晶体粗大;当电沉积电流密度增大到15 mA/cm2时,形核功率增大大于晶体的生长功率,镀层晶粒变的细小使得镀层硬度提高;电沉积电流密度进一步增大时,析氢加剧,镀层表面的氢气阻碍了后续离子的还原过程,使得晶粒生长变粗。
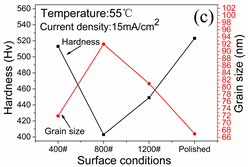
Figure 3. Hardness and grain sizes of the Zn-Ni coatings prepared under different parameters: (a) Current density; (b) Plating temperature; (c) Surface conditions
图3. 不同参数下制备的Zn-Ni镀层的硬度和晶粒度(a)电流密度;(b)电镀温度;(c)表面状态
由图3(b)可知,锌镍镀层晶粒尺寸晶在53 nm到65 nm之间,随沉积温度的上升先减小后增大,锌镍镀层的硬度在315 HV到550 HV之间,并随温度的上升先增大后减小。当电沉积温度为50℃时晶粒尺寸最小为53 nm,此时镀层硬度达到最大550 HV,也更加致密(图1(g))。这可能由于较低温度导致体系的能量较低,沉积速率低从而导致镀层晶粒粗大,随着温度升高,体系能量提高,镀液离子热运动加快使得阴极附近浓差极化加强使得形核率上升,最终使得镀层晶粒细化,硬度提高。而当温度过高时,析氢反应加剧使得金属离子的还原受阻,导致镀层晶粒变粗,镀层硬度下降。
在不同基体粗糙度下所得镀层的晶粒度是随着基体粗糙度下降先增大后减小,在粗糙度较大和基体抛光后得到的镀层性能较佳。这可能是在粗糙度较大时,基体的表面积变大,离子电沉积的附着位点较多使晶粒细化,使得镀层的硬度较高;当镀层基体较为平整光滑时,镀层的结晶性最佳,取向生长最好,所以得到比较细化的晶粒,也使得镀层硬度较高。
3.3. 镍锌合金镀层的抗腐蚀性能
图4为不同参数下制备的Zn-Ni镀层钕铁硼磁体在3.5 wt%氯化钠溶液中腐蚀所得的Tafel曲线图,表2为锌镍镀层的Tafel曲线电化学参数拟合结果,从动力学上来说,自腐蚀电流越小,说明腐蚀发生的越慢。从表2可知,当电沉积阴极电流密度增加时,制备的镀层试样的自腐蚀电流密度先降低后增加。由前面的分析可知,电沉积电流密度为15 mA/cm2时制备的Zn-Ni镀层晶粒度最小,微观形貌最致密,此时具有最小的自腐蚀电流和最正的自腐蚀电压,抗腐蚀性能最好;当电沉积温度升高时,Zn-Ni镀层样品的自腐蚀电流先减小后增大,由前面的分析可知,镀液温度为50℃时制备的镀层晶粒度最小,微观形貌最致密,此时具有最小的自腐蚀电流,抗腐蚀性能最好。与自腐蚀电流不同,随着镀液温度的升高,Zn-Ni镀层样品的自腐蚀电压是逐渐升高的,实验温度范围内,镀液温度为55℃时,自腐蚀电压最高,这可能是由于随着温度的升高镀层相组成发生了变化,导致电位的变化。从表2还可以看出,当砂纸目数增大时,制备的镀层样品的自腐蚀电流呈上升趋势,在基体抛光时所制备的镀层样品自腐蚀电流最小和自腐蚀电压最正,抗腐蚀性能最好。由前面的分析可知,基体抛光所制备的镀层晶粒尺寸最小,表面最致密符合这一结果。
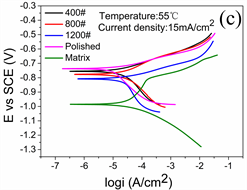
Figure 4. Polarization curve of coating under different parameters: (a) Current density; (b) Plating temperature; (c) Surface conditions
图4. 不同参数下所得镀层的极化曲线(a)电流密度;(b)电镀温度;(c)表面状态
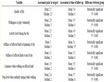
Table 2. The Tafel curve electrochemical parameter fitting results of Zn-Ni coatings prepared at different process conditions
表2. 不同工艺条件下制备的锌镍镀层的Tafel曲线电化学参数拟合结果
3.4. 镍锌合金镀层的结合力
图5是不同工艺参数下制备的镍锌镀层与基体间的结合力,由图5(a)可知,随着沉积电流密度的增加,膜基结合力先上升后降低。当电流密度较低为5 mA/cm2时对应的结合力较低为5.32 MPa,可能是由于沉积速率较低时形成的圆形晶粒团簇粗大多孔,镀层和基体的有效结合表面积较少导致膜基结合性能不好。当电流密度增加到10 mA/cm2时结合力增加将近一倍为10.31 MPa,这是因为阴极极化增强使得形核功率增加,镀层开始变得致密平整镀层结合力有较为明显的提高。电流密度继续增加到15 mA/cm2,此时膜基结合力达到最大值13.1 MPa。这可能是由于形核率继续提高导致离子在阴极反应的还原反应加快,使镀层与基体结合的更加牢固。而当阴极电流密度进一步增加到20 mA/cm2时,基体和镀层的结合力出现的下降变成9.03 MPa,可能原因是当电流密度过大,阴极析氢变得严重,氢气无法快速排出阻碍了金属离子的还原镀层开始变得疏松,并且高的电流密度会加剧副反应生成氢氧化锌胶体导致镀层内应力变大,最终使得膜基结合力下降。
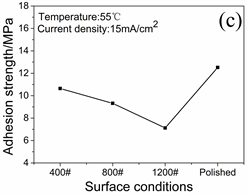
Figure 5. Adhesion strength of coating under different parameters: (a) Current density; (b) Plating temperature; (c) Surface conditions
图5. 不同参数下所得镀层的结合力(a)电流密度;(b)电镀温度;(c)表面状态
由图5(b)可知,随着沉积温度的升高,镍锌镀层膜基结合力先升高后降低,当温度为40℃时膜基结合力为3.55 MPa,这可能是由于较低的镀液温度导致体系的能量较低,沉积速率低从而导致镀层疏松多孔结合力最终导致结合力不佳,随着温度的升高,体系能量提高,镀液离子热运动加快使得阴极附近浓差极化加强使得形核率上升,最终使得镀层晶粒细化、细致、平整结合力较好。在沉积温度为50℃下制备的镍锌镀层具有最佳的膜基结合力13.67 MPa,当温度过高会使析氢增强使得镀层晶粒变粗、镀层变得疏松不平整,最终导致膜基结合力变差。
粗糙度对于膜基结合力的影响则与电流密度和电沉积温度有所不同。随着基体粗糙度的降低,膜基结合力是先减小后增大,在基体为抛光下所得到的镀层具有最佳结合力。在粗糙度较大时镀层的沉积位点较多起到了细化晶粒的作用,并且基体具有较大的等效表面积,这会让镀层与面积更大的基体相结合从而提高膜基结合强度,粗糙度降低时晶粒度变大,并且等效结合面积减小故而结合力减小。当基体表面被抛光至平整光滑时,膜基结合强度显著提高,抛光的基体表面光亮清洁,有利于涂层与基体间的相互作用,有利于外延生长,从而使附着力明显提高。
图6为测试镀层膜基结合力后断裂面的表面形貌SEM图。图6(a)、图6(b)分别为电沉积电流密度为5 mA/cm2和15 mA/cm2时制备的镀层的断口形貌,可以看到图6(a)的基体较为完整,镀层断裂面几乎垂直于基体,图6(b)的基体破碎较为严重,镀层断裂面也垂直于基体。它们对应的镀层膜基结合力分别为5.3 MPa、13.1 MPa;图6(c)和图6(d)分别为沉积温度50℃和40℃条件下制备的镀层的断口形貌,图6(c)基体保存完好,镀层断裂面垂直基体(镀层开裂是由于需要在拉拔实验后取下工件上的样品进行观察,利用真空热处理对样品进行210℃的加热处理)图6(d)基体出现破裂,且镀层断裂面呈现出较大的斜坡状。它们对应的镀层膜基结合力分别为13.67 MPa和12.52 MPa。
图7(a)为镀层的失效界面模型,一方面,在界面处影响分子界面键的应力取决于局部斜度,其可以分解为两个分量。一个分量垂直于界面为δ,第二个分量沿界面平行为τ。垂直于界面的分量以拉拔的方式作用与镀层,与界面平行的分量拉着镀层沿着断裂面剪切成斜坡。可以把这两种作用于断裂面的情况表征为两种模式如图7(b)。拉拔标记为(I),在这种情况下,裂纹是一条垂直于应力的线。剪切模式标记为(II),断裂是在裂纹平面上的一个区域上的滑动剪切。界面上的剪切力可以通过有效的摩擦促进断裂面之间的“联锁”从而提高结合力 [26] 。若裂纹沿着仅由I模式延伸开裂径进行,即没有II模式的作用,那么镀层结合力就会比较低。如果它们遇到一些模式II阻力,方向就会改变使得“联锁”产生,从而提高结合力。纯I型荷载很弱,因为粗略地说,只有断裂线上的键在抵抗破坏。模式II会提供了更大的阻力,因为整个界面区域上的键都在抵抗负载。在镀层受到外力作用时,断裂面可以通过大量的模式II的锚定提供高附着力。此外,斜坡断裂面可能会降低I型方向上的应力,使其低于材料的I型破坏应力。随cos(ɑ)增加,界面破碎所需要打破的键更多,所需的能量(或力)将得到增大,从而增加镀层的结合力,这与图6的(d)和(f)所对应镀层结合力高的结果是吻合的。另一方面,界面处结合力大小还取决于基体和镀层之间键和的数量和强度,当仅由模式I延伸开裂将镀层垂直拔起,镀层和基体之间的结合力很高时,镀层的局部区域没有被拉断,而是连带基体使之出现强烈的破坏,这和图6(b)的结果是吻合的。
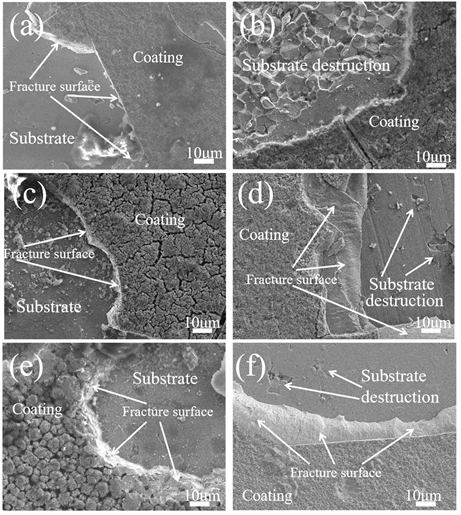
Figure 6. Surface morphology of fracture surface of coating after drawing: (a) 5 mA/cm2; (b) 15 mA/cm2; (c) 40˚C; (d) 50˚C; (e) 1200#; (f) Polished
图6. 镀层拉拔后断裂面表面形貌(a) 5 mA/cm2;(b) 15 mA/cm2;(c) 40℃;(d) 50℃;(e) 1200#;(f) 抛光的
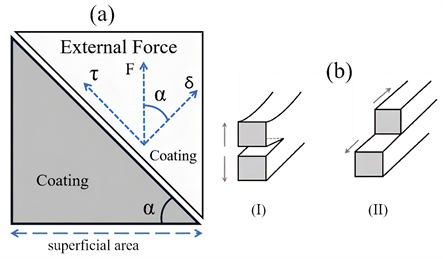
Figure 7. Mode of coating interface [27] : (a) Failure mode of coating interface; (b) Drawing crack model of coating
图7. 涂层的界面模型 [27] :(a)镀层的界面失效模型;(b) 镀层的拉拔开裂模型
4. 结论
采用醋酸盐体系的镀液在钕铁硼磁体表面直流电沉积了Zn-Ni合金镀层,研究了阴极电流密度、镀液温度和基体粗糙度对镀层抗腐蚀性能、硬度及其膜基结合力的影响,主要结论如下:
1) 制备的锌镍合金镀层主要为具有良好抗腐蚀能力的γ相Zn5Ni21,并按(600)晶面取向生长,部分镀层含有少量的镍相存在。
2) 锌镍合金镀层的抗腐蚀能力分别随阴极电流密度和温度的升高先增强后减弱,随粗糙度的降低先减弱后增强,在电流密度为15 mA/cm2、镀液温度为50℃、基体抛光时制备的锌镍合金镀层的Ni含量在22%到23%之间,具有最好的抗腐蚀能力。
3) 沉积电流密度为15 mA/cm2、镀液温度为50℃和基体抛光时的得到的镀层细致、平整、光亮,晶粒度最小,镀层硬度最大。
4) 沉积电流密度为15 mA/cm2、镀液温度为50℃和基体抛光时镀层膜基结合力最高,抛光基体制备镀层对提高膜基结合强度有较好的效果。
基金项目
国家重点研发计划青年科学家项目(2022YFB3505600)对本研究工作提供了资助。
NOTES
*通讯作者。