1. 引言
中药生产复杂,当前我国对生产工艺考察仅针对产品终端含量值进行离线检测,耗时且成本巨大,无法监控生产过程中产生的异常 [1] 。美国贝尔实验室Shewhart博士在1924年5月绘制出第一张质量控制图,1929 年,贝尔电话公司的Dodge和Romig发表了论文《抽样检查方法》,提出用抽样检查代替全数检查的方法来保证产品的质量 [2] 。工信部起草的《“十四五”智能制造发展规划》中指出生产过程精密管控、装备故障诊断等是智能制造技术攻关的关键核心部分 [3] [4] 。
为及时反馈生产过程中存在的异常原因,美国食品药品监督管理局指出在生产过程中应将终端检测重心向过程控制转移,指出过程分析技术PAT,可将原材料、中间体及关键质量特链接起来的分析控制系统 [5] [6] 。近年来,研究发现PAT过程分析技术与光谱、色谱和质谱等检测手法联用,对生产周期、关键质量参数、原材料和中间体进行控制,达到最终产品符合标准 [7] [8] 。近红外光谱NIRS技术不断发展,已被广泛应用于制药、农业、食品以及医学等各个领域,为中药材质量的快速评价提供了新的分析手段 [7] [9] [10] [11] [12] 。NIRs具有检测快,不破坏样品可同时反馈化学和物理信息的优点,因此常用于过程在线监控 [13] 。
多变量统计控制(Multivariate Statistical Process Control, MSPC)是利用不同变量之间存在的关系(相关性)可使用统计程序同时监测多个相关变量,适用于连续和断续过程。本研究以银杏叶粗提液聚酰胺层析洗脱过程为例,建立洗脱轨迹,考察此方法在连续生产过程中的可行性,对生产进行实时监控,以期为中药材生产批次间差异或异常点判别提供方法参考。
2. 材料与方法
2.1. 仪器与药材
MicroNIRPAT-U光谱仪(购自ViaViSolutions公司),聚酰胺层析树脂60 kg,银杏叶药材由上海杏灵有限公司提供。
2.2. 提取工艺
称取一定银杏叶药材,进行水提醇沉得到提取液,进行粗提液浓缩,得到提取浓缩液。将浓缩液进行聚酰胺树脂层析纯化。将银杏叶浓缩液先注入层析柱中,后通过95%乙醇进行洗脱,银杏叶洗脱过程约40 min,1 min采集3次光谱每个批次约120条光谱,洗脱工艺图如图1所示。
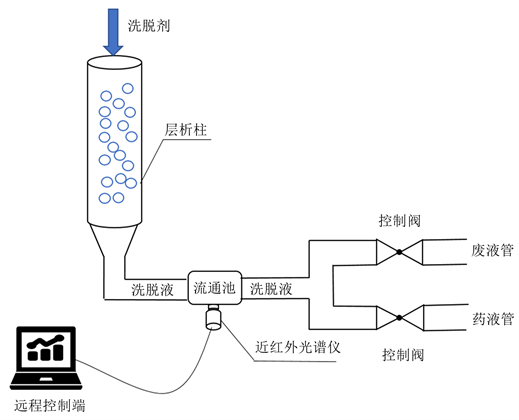
Figure 1. Polyamide elution process diagram of Ginkgo folium
图1. 银杏叶聚酰胺洗脱工艺图
2.3. 批次设计
提取试验批次如表1,其中1~6光谱来源于银杏叶聚酰胺层析纯化正常工艺(NOC),用于建立正常活动流程轨迹。批次8和9来源于生产异常光谱生产批次。
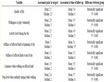
Table 1. Elution batch design table of Ginkgo folium
表1. 银杏叶洗脱批次设计表
2.4. 光谱采集
采集方式为透反射法,以流通池为参比及背景,光谱扫描范围为908.1~1676.2 cm−1,扫描次数为100次。
2.5. 过程轨迹图的建立
2.5.1. 数据预处理
采集的近红外光谱是包含批次、时间及波长的三维矩阵X (a × b × c),其中a代表波长,b代表批次,c代表时间,在建立MSPC过程控制之前,需要对数据展开降维分析,将相同批次中时间与光谱波段响应值展开为二维矩阵X1 (b × ac),选择按照矩阵变量的方式展开,每行包含同一批次不同时间点对应波段光谱响应值。如图2。
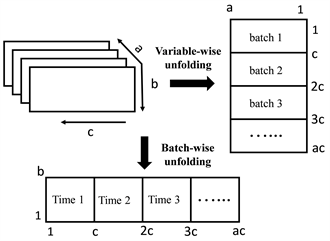
Figure 2. Expansion of near infrared spectral data matrix
图2. 近红外光谱数据矩阵的展开方式
2.5.2. MSPC控制图的选择
将原始测量数据首先通过PCA主成分分析进行降维,在主成分 > 80%条件下,得到最佳因子数后,使用PCA代替原始数据。研究选择主成分得分图和Hotelling’s T2建立洗脱过程轨迹图,T2统计算法可以指出每个变量到模型的距离测量,通过过程轨迹图可反应洗脱过程是否处在受控阶段,若超出控制线,则表明出现异常或模型不再适用。
3. 结果和讨论
3.1. NIR光谱分析
将展开的光谱数据导入The Unscrambler X软件(美国CAMO公司)进行处理,得到银杏叶聚酰胺层析纯化光谱,洗脱体系为纯水-95%乙醇如图3所示,为清除扫描过程中的噪声,对光谱进行一阶导光滑6点预处理。
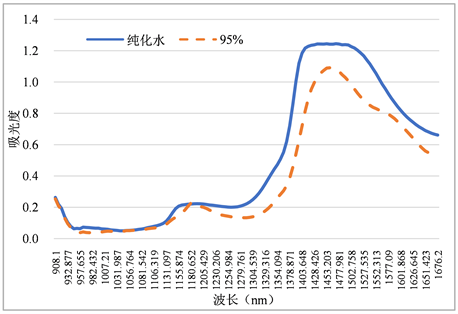
Figure 3. Near infrared spectra of Ginkgo folium elution process
图3. 银杏叶洗脱过程近红外光谱图
3.2. 提取过程的建立
将预处理后的数据导入软件,进行PCA降维分析,结果显示前两个主成分累计贡献率达到99%,说明前两个主成分代表了大部分的光谱数据,可以用作后续分析。
根据PCA建模结果得分图4可知,聚酰胺层析洗脱可分为三部分开始–洗脱–结束,在洗脱开始,洗脱液需要流出时间,因此初期散点集中。洗脱中期:洗脱溶剂逐步换成95%乙醇,光谱发生显著变化,散点分散。洗脱结束:95%活性成分逐步洗脱出来,变化较少,散点集中。见图4箭头方向为洗脱进程趋势。
选择6个NOC批次光谱建立PCA模型,作为轨迹监控模型,将置信区间选择为95%,考察样本Hotelling’s T2值是否在区间范围内,使用PC-1作为主成分得分轨迹控制图,如图5所示。轨迹中段出现波动表示体系内溶剂出现波动变化较快,推测由于溶剂提取物溶出度不同,随着时间,提取物逐渐减少,轨迹趋于平滑。

Figure 4. Trend diagram of Ginkgo folium elution process
图4. 银杏叶洗脱过程趋势图
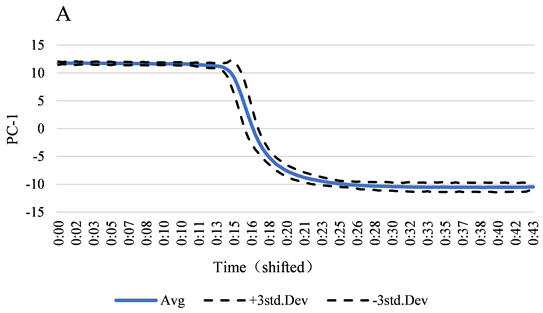
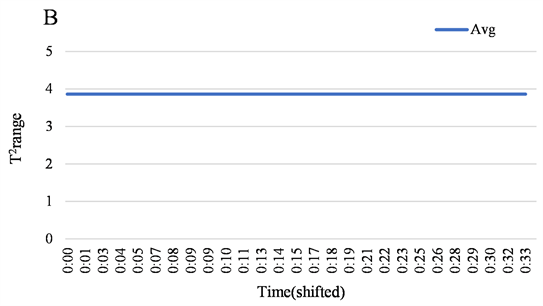
Figure 5. Monitoring model of Ginkgo folium elution process (A: principal component score plot; B: hotelling’s T2 control chart)
图5. 银杏叶洗脱过程监控模型(A:主成分得分图;B:Hotelling’s T2控制图)
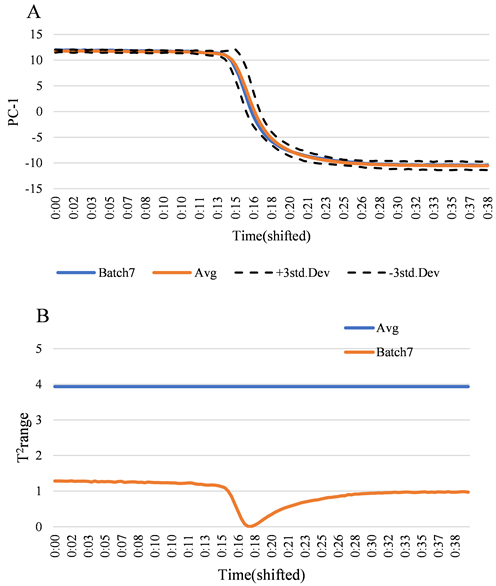
Figure 6. Monitoring model for Ginkgo folium elution process-batch 7 (A: principal component score plot; B: hotelling’s T2 control chart)
图6. 银杏叶洗脱过程监控模型–批次7 (A:主成分得分图;B:Hotelling’s T2控制图)
3.3. 轨迹图的验证
银杏叶聚酰胺层析洗脱过程轨迹图建立后,为考察此方法适用于PKS系统方法对洗脱过程监控,使用第7批次正常生产光谱进行验证,将PCA模型处理后的PC-1数据和T2值导入已建好的洗脱轨迹图中,结果发现无异常值点在轨迹外,且经过Hotelling’s T2验证各点均在控制限范围内,如图6所示。
将第8批次(药材质量差异大)和第9批次(30%乙醇)光谱数值经过PCA降维处理,考察轨迹图对异常生产的判别能力(如图7)。结果显示,第8批主成分轨迹图显示,在洗脱中间段部分存在差异,是由于药材质量差异大,导致在洗脱过程中成分含量的变化趋势产生异常,在Hotelling’s T2控制图中,异常部分较少。第9批次主成分轨迹图中显示从开始到结束洗脱全过程均是异常值,是由于乙醇体系的改变导致产生异常,根据T2控制图显示,数据异常部分较多,说明监测数据结构的变化。根据8和9批次轨迹图判定结果显示,主成分轨迹图与T2可对异常状况进行识别,PCA模式所建的轨迹图模型可用于对聚酰胺层析洗脱流程监控。
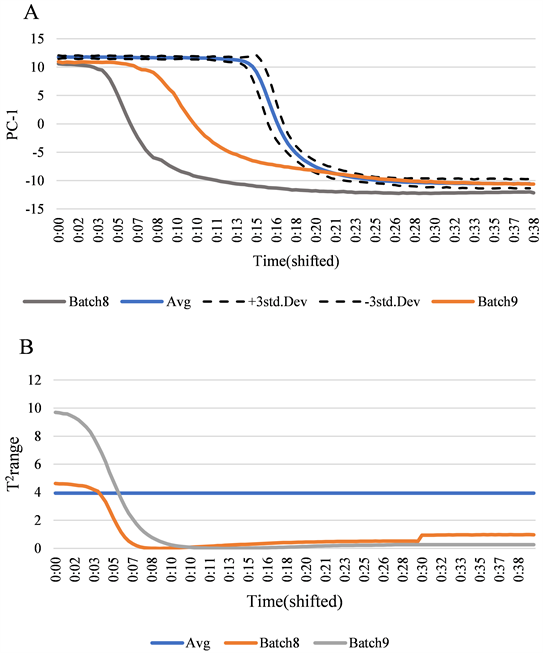
Figure 7. Monitoring model for Ginkgo folium elution process-batch 8-9 (A: principal component score plot; B: hotelling’s T2 control chart)
图7. 银杏叶洗脱过程监控模型–批次8-9 (A:主成分得分图;B:Hotelling’s T2控制图)
4. 结论
本研究以银杏叶粗提液聚酰胺层析洗脱过程为例,建立将NIR光谱与MSPC过程控制相结合的监控模型,结果表明此方法可对聚酰胺洗脱过程进行监控,并判定在洗脱过程中是否出现异常,并有效识别异常批次。说明此方法可广泛应用在中药生产领域,以期为中药生产智能化改进提供指导意义。
由于生产过程中可调节因素很多,该方法在后续研究中可采用其他原因异常批次进行检测,并根据不同生产条件对主成分选择进行判定,有针对的建立生产过程控制体系,以期对中药生产工段放行提供数据支持,增加风险管控能力。
课题项目
本研究由药典委的多变量统计过程控制技术指导原则的建立(2022Y08)资助。
NOTES
*通讯作者。