1. 引言
近年来,随着人们的环保意识也不断提高,新能源汽车行业发展迅速,逐渐取代燃油车占据了一定的市场地位,而伴随着新能源汽车数量的增长,安全性、舒适性的需求也逐渐有目共睹 [1] 。汽车车架作为新能源汽车的关键支承,它作为汽车底盘的核心部件,对汽车整机的性能和结构可靠性有着重要的影响,在行驶过程中受到及其复杂的交变载荷影响,在不同工况下产生结构失效,许多企业在传统结构上加以改造的同时,组建燃料电池、电机以及伺服控制元件,也要考虑轻量化设计,以提高电池效率 [2] [3] 。基于有限元法可以缩短研发周期,弥补传统设计的短板,因此对新能源汽车车架的有限元分析及模型再设计非常有意义。
方朝等人提出一种纯电旅游观光车车架,并通过多次局部迭代拓扑优化的方法对其进行了精细化设计 [4] 。陈和娟以轻量化赛车为研究对象,应用ANSYS软件对车架结构进行了有限元分析,验证了车架的弯曲扭转刚度 [5] 。马嘉俊等人在参考传统边梁式车架的基础上,应用6000系铝合金材料设计了一种直驱式电动汽车副车架,并利用NX10.0软件优化了车架结构,为新能源车架轻量化设计提供了依据 [6] 。但目前,大梁式车架仍为主流车架形势 [7] ,采用合理方法对车架适应性改进,才能充分发挥新能源汽车的性能以及现代化优势。
本文以某型新能源轿车车架为研究对象,使用ANSYS Workbench分别进行相应的状态约束,重点模拟了车架在满载弯曲、满载扭转,平衡工况下新能源汽车主梁的静力学特性分析以及动力学模态分析,并通过相应的计算验证新材料力学性能是否满足强度和刚度的要求。
2. 新能源轿车车架结构分析与有限元模型
2.1. 结构分析
该车架由两根横梁、两根纵梁以及两根辅助梁组成,中间部位设计驾驶室简图以辅助有限元分析,相互之间通过焊接连接在一起。每段梁均采用空心管材,电池储藏盒设计于中部和后部,电池盒与主梁之间采用阻燃PC/ABS材料连接,既能实现轻量化,又能起到阻燃、耐低温的作用 [8] 。
车架具体设计数据为:长3200 mm,宽770 mm,高250 mm,主梁截面长24 mm,宽16 mm电池储藏室长度2000 mm,该新能源车架结构简图如图1所示。
2.2. 三维模型建立
通过Solidworks三维软件对新能源轿车车架进行建模,基于能量最小化原则,结构的简化表示和上负载的实际表示视作等效负载,建模过程中过滤掉影响较小的因素 [9] 。新能源车架三维模型如图2所示。
2.3. 材料及网格划分
车架材料选用铝合金7系7075-T6,该系型材焊接性能较为出色,重量轻,抗氧化能力强,可满足新能源车架的使用要求,材料力学性能如表1所示,车架的重量为113.278 kg,而使用常规结构钢合金的底盘实际重量为210 kg左右 [10] 。
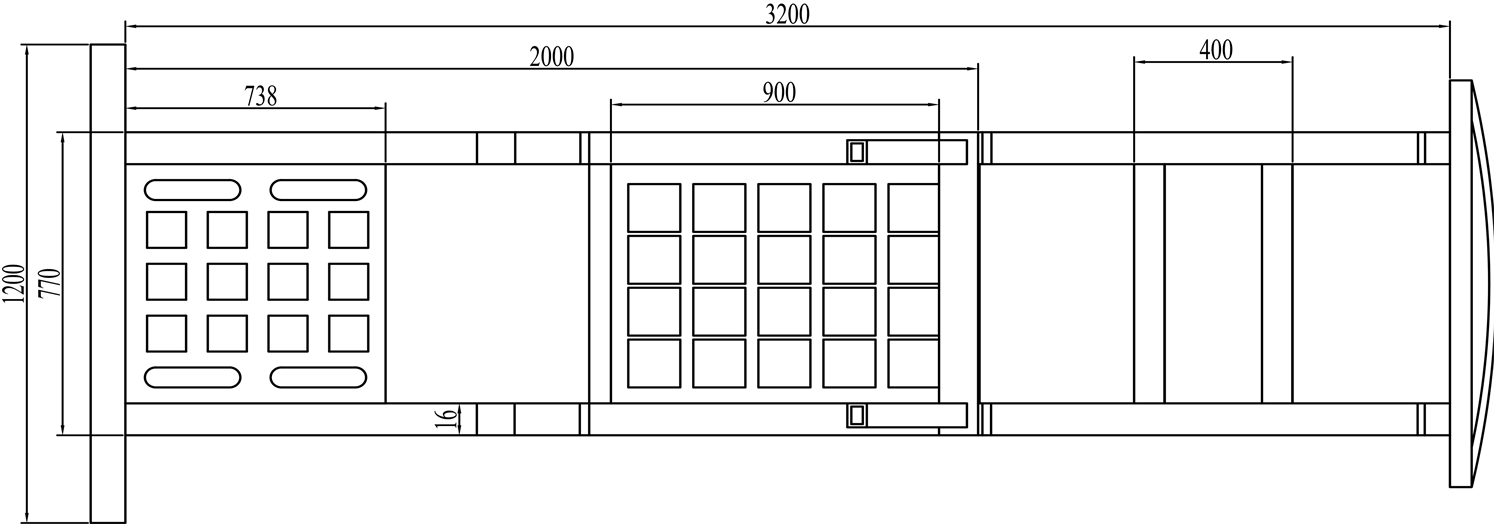
Figure 1. Schematic diagram of new energy frame structure
图1. 新能源车架结构简图
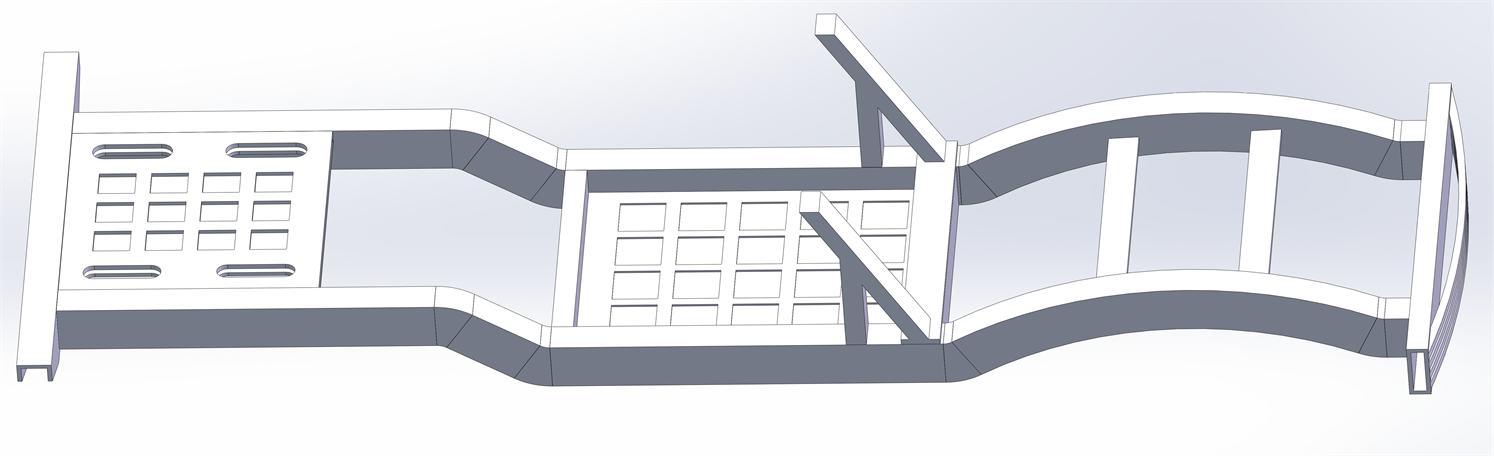
Figure 2. A three-dimensional model of the vehicle frame
图2. 车架三维模型
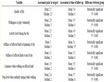
Table 1. Mechanical property parameters of 7075-T6 aluminum alloy
表1. 7075-T6铝合金的力学性能参数
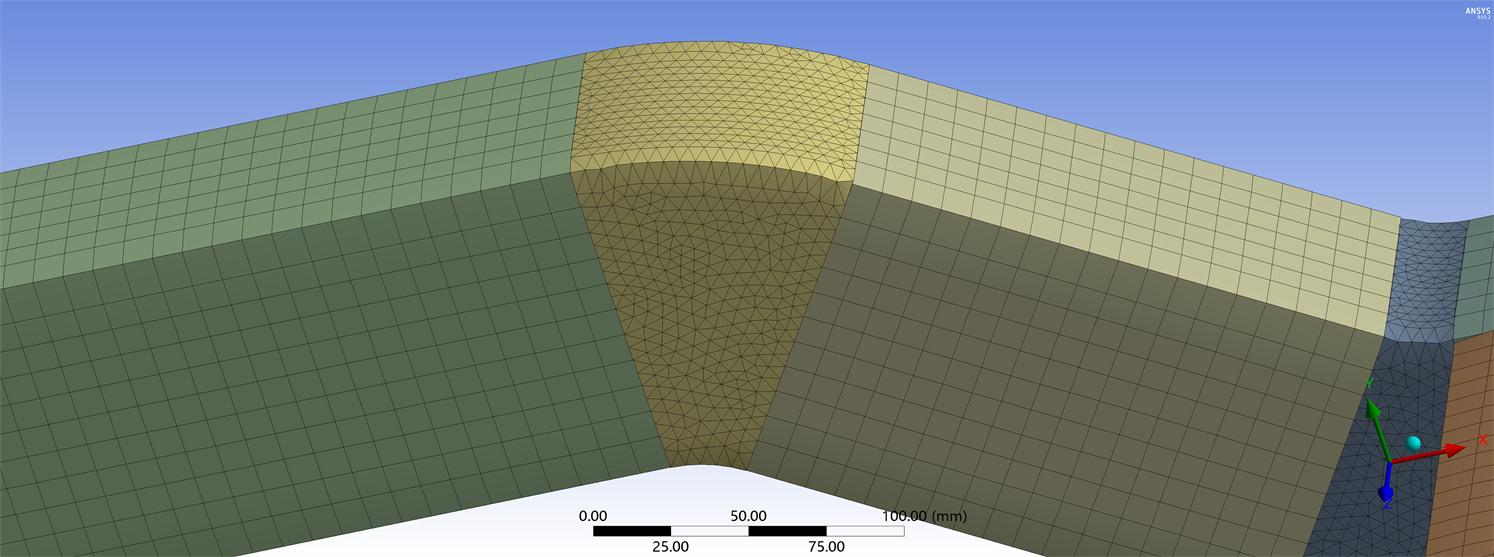
Figure 3. Schematic diagram of grid partitioning strategy
图3. 网格划分策略示意图
将车架模型导入Ansys Workbench建立分析项目,网格的的疏密程度直接影响CPU的计算时间,为提高计算效率,通过Spaceclaim模块抽取中面,并将一般网格大小设置为5 mm,局部为3 mm,主梁应用四边形单元,局部特殊区域应用三边形单元,两种单元类型组合使用,相应方法如图3所示,对于局部区域,减小单元尺寸是最有效的网格细化策略,其本质是减小整个建模与的单元尺寸,从而提高网格精度,进而确定好焊接模型的接触关系,这里取面与面、面与边识别的容差值为3.9 mm,最终划分了238,420个节点,250,918个单元,划分结果如图4所示。

Figure 4. Grid partitioning model for the main beam of the vehicle frame
图4. 车架主梁网格划分模型
2.4. 车架基本载荷的确定
在对车架主梁结构分析过程中,确定实际中涉及的集中载荷,它对应的载荷包括驾驶员及其他成员、动力电池、电机、白车身以及备胎等等,本文研究主要载荷及其对应的分布位置如表2所示。
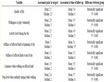
Table 2. Load table for main beam of vehicle frame
表2. 车架主梁载荷表
为将载荷施加到主梁上,研究过程还需要具体分析,合理有效并且贴合实际。本文在根据理论分析基础上,综合考虑满载时车架的承受方式,确定以均布施加这种载荷方式为主,汽车在行驶过程中又受路面状况、驾驶员习惯等不确定性因素影响,受到复杂的动静载荷联合施加,将上述相关载荷分别相关到一个动载系数上 [11] 。本文取动载系数Kv = 2,载荷分布方式如图5所示。在约束载荷施加过程中遵守以下规则:
1) 约束施加保证模型不存在欠定义,避免模型移动产生较大的计算偏差;
2) 约束中亦不存在模型过定义;
3) 遵守力学平衡规则,如主梁反力与被施加的其他载荷相等;
4) 载荷大小方向定义明确。
3. 新能源车架静力学特性分析
3.1. 不同工况下的结构静强度分析
静强度工况状态,即车辆沿着良好的路面做匀速直线运动,或处于静止转态。在纯弯曲边界条件中,限制右后方主梁的六个自由度,左前方Y方向自由度释放,右前方Y方向平动。仿真结果如图6所示,从应力云图可知,纯弯曲工况下,最大位移出现在主梁前部,最大应变0.7943 mm,说明在车架在平衡状态时,前部动力引擎部分对车架的载荷影响较大。而在车辆的设计过程中,一般车架弯曲挠度要求控制在10 mm以内 [10] ,这也是为了汽车的安全可靠性考虑,所以仿真结果显示远低于参考值,意味着该变形铝车架总成在抗弯曲性能较为良好。
图7是计算出的等效应力结果。由应力云图可知,纯弯曲工况下,最大应力出现在副驾驶靠背所在的横梁部分,最大应力
,结合位移情况分析可知满载时车辆前部载荷对结构影响最大。代入式
,可得安全系数S = 8.99远大于1。即该车架有很大的安全裕度,满足强度要求。
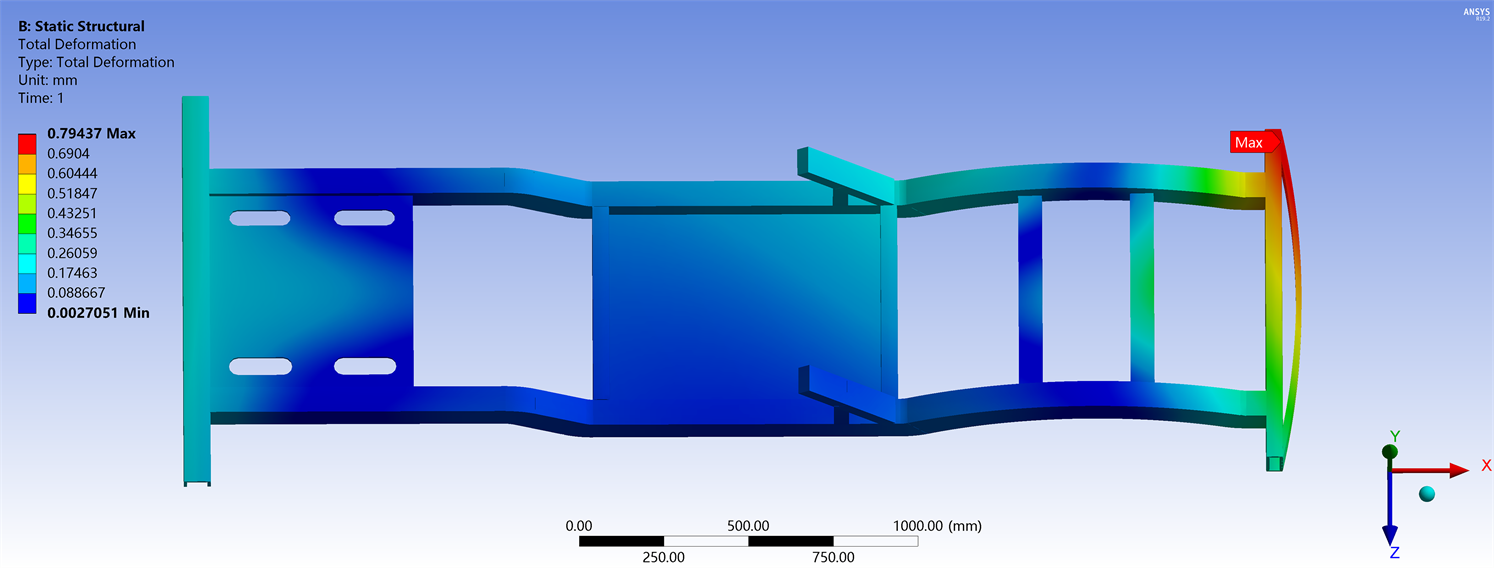
Figure 6. Pure bending total strain cloud map
图6. 纯弯曲总应变云图
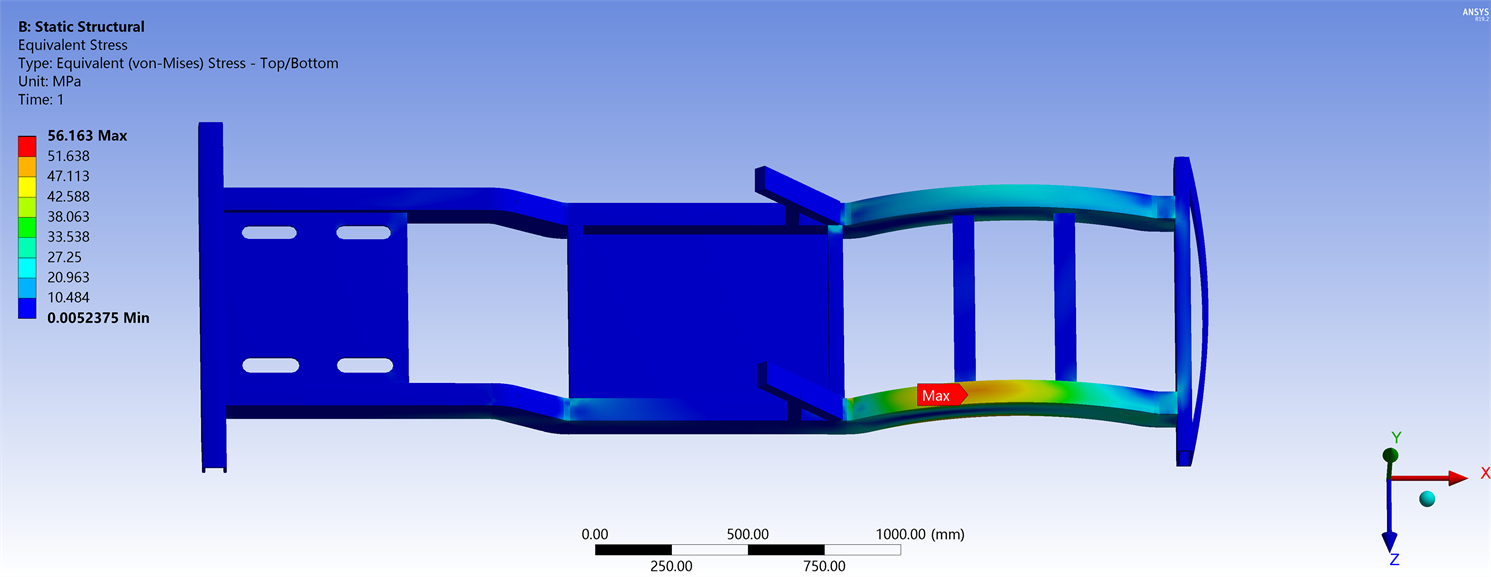
Figure 7. Equivalent stress nephogram for pure bending condition
图7. 纯弯曲工况等效应力云图
3.2. 动强度分析
载荷施加与平衡状态工况相同,考虑在车辆在行驶过程中,路过特殊地形导致车轮悬空的情况,车架的支撑状态将发生变化,该扭转模拟轿车在路过坎坷路段时,左前轮与右后轮悬空,释放自由度并为其他两个轮子添加固定支撑,由云图可知,最大位移出现在前部横梁部分,发生4.5146 mm的位移,而后部横梁变形较小,原因是仅固定了右前与左后的车轮,车架在电机、动力电池等其他载荷作用下向下变形,最大变形位置如图8所示,车架各部分变形均小于10 mm,最大应力为120.85 MPa,出现在副驾驶处的横梁部分,计算安全系数为4.2 > 1。综上所述,该模拟工况下应力和应变均满足设计要求。满载扭转工况等效应力如图9所示。
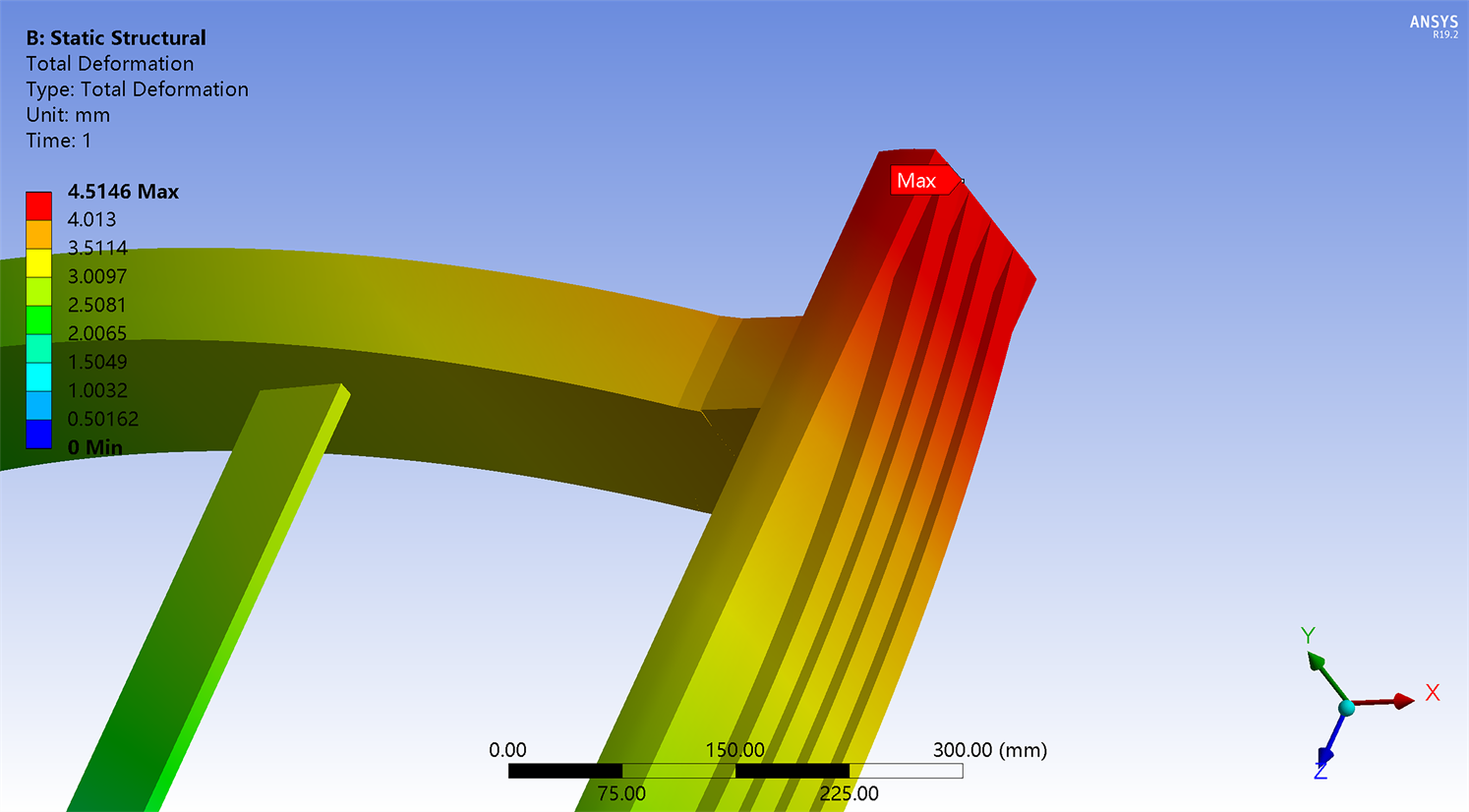
Figure 8. Full load torsional displacement cloud image
图8. 满载扭转位移云图
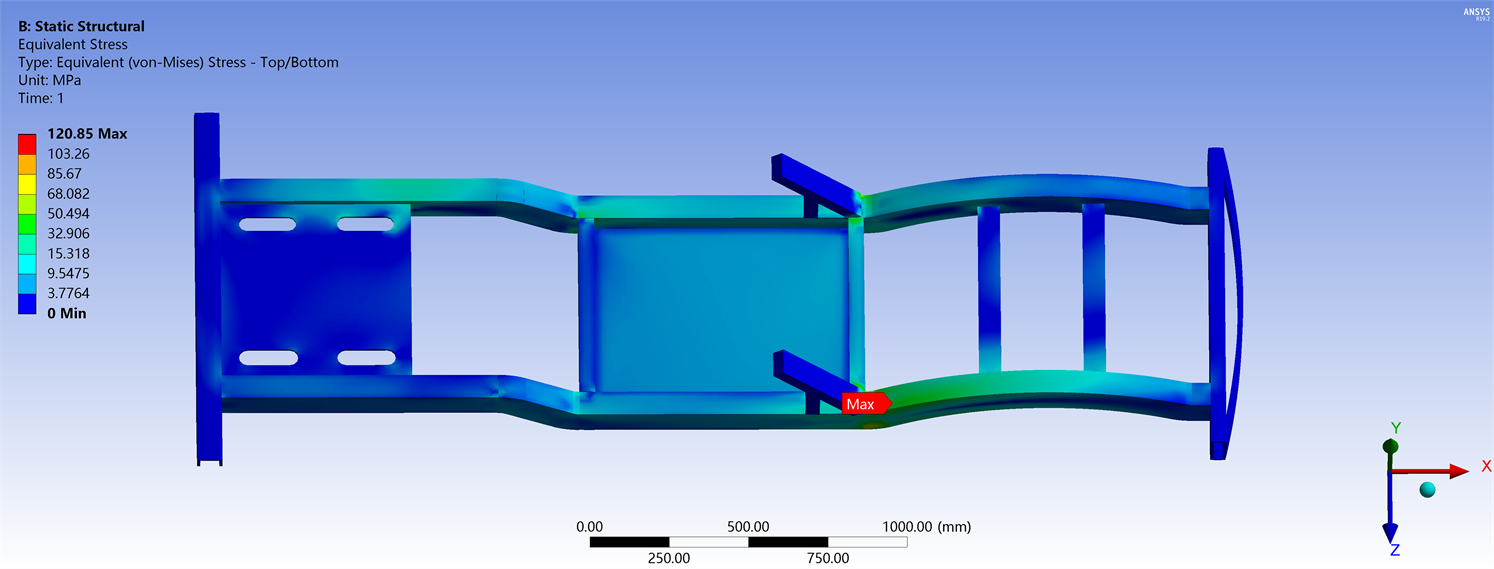
Figure 9. Full load torsional stress nephogram
图9. 满载扭转应力云图
3.3. 扭转刚度分析
扭转刚度的计算方法,在分析车架的扭转刚度时,只保留了重力,在电动机前梁所处位置分别添加2000 N大小相等,方向相反的假定远程作用力,并约束车架后部纵梁及其连接点x,y和z等3个自由度,载荷示意图如图10所示。
扭转刚度的计算方法:
(1)
式中:M为作用力矩;L为车辆轮距的一半;θ为扭转角度;F为施加的外力。
校核方法:由于本文使用的7系铝合金仍为金属塑性材料,因此依据材料力学第四强度理论作为准则,应力表达式:
(2)
其中
为三个定义的主应力,
为材料的屈服强度。
由上述分析得F = 2000 N,L = 500 mm,计算出扭转角度为θ = 0.368˚,则车架的扭转刚度为2717.39 N·m/(˚),由于本文研究的车架是新能源通用车辆上的,依据经验值 [12] ,只要扭转刚度不小于1700 N·m/(˚)就可以认为设计模型的扭转刚度达标。
4. 新能源车架动力学特性分析
4.1. 研究方法
尽管新能源汽车通过电动机替代了传统的燃油机,噪声、振动得到明显的改善,但新型结构的设计仍然需要研究它的固有频率以及整机的共振特性,采用合理的方法研究车架结构的动应力仍然有意义,本文基于计算分析法,对结构进行模态分析,确定了各阶振型,为新能源汽车主梁结构未来设计提供了一定的参考价值。本文在研究过程中考虑到实际工况,利用软件优势构建多自由度弹性系统,依据表达式(3),求出n个特征解
、
、
,从而得到若干个固有频率和固有振型。
(3)
式中,u为固有振型,ω为固有频率,K、M分别代表车架结构的总刚度矩阵和总质量矩阵。
4.2. 车架自由模态分析
车辆在实际环境下受不同激励源的影响,产生共振将对车架结构产生破坏,存在安全隐患,本文研究了该新能源车架的自由模态,通过Workbench建立分析项目,提取车架的前12阶模态,重点分析了路面及电动机两个激励源的振型影响,如表3总结了该车架各阶模拟频率及振型计算结果。
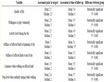
Table 3. Modal frequency and mode characteristics of frame
表3. 车架模态频率及振型特征
由表3可知,前六阶固有频率较小且远低于路面激励的30 Hz振动频率,且前六阶结构振型特征未发生明显变化,所以可忽略不计。该车架自由模态各阶振型云图如图11至图16所示。
依据仿真结果可以看出,车架第七阶固有频率为40.376 Hz,振型为Y轴负方向的弯曲振动,第七阶振型云图如图11所示,峰值出现在前部横梁区域,并且与车架的实际使用工况接近。
八阶模态固有频率为64.126 Hz,振型表现为车架两端X轴的反向扭转振动,并呈向腹部递减的状态,第八阶振型云图如图12所示,九阶模态固有频率为72.154 Hz,振型为Z向正方向弯曲振动,变形最大区域出现在车架前部,第九阶振型云图如图13所示,十阶模态固有频率为108.03 Hz,其振型表现为绕腹部的弯曲扭转组合振动,第十阶振型云图如图14所示,十一阶模态固有频率为109 Hz,振型为Y向的弯曲振动,第十一阶振型云图如图15所示,十二阶模态固有频率为159.85 Hz,其振型表现形式与前几阶略有不同,但其中心位置基本没有变化,第十二阶振型云图如图16所示,最大变形出现在电动机固定梁上,最大变形为17 mm左右,七至十一阶每一阶的固有频率在小于40 Hz的范围增加,十二阶模态固有频率最大为159.85 Hz,七至十二阶固有频率范围为40~160 Hz,均大于路面激励的30 Hz。
通过分析车架的前十二阶最大固有频率,结合汽车用电动机转子振动频率的经验值600~5000 Hz,不会产生共振,根据仿真结果,该车架前12阶固有频率均低于电动机转子固有频率,可知车辆在正常行驶过程中,避免了共振现象,验证了该设计结构的合理性。
5. 结论
本文通过Solidworks建立车架模型,并结合有限元分析方法,设计了一种应用7系铝合金材料的新能源轿车车架,重点关注了新研发车架的强度、扭转刚度及可靠性等,分析得出以下结论:
1) 应用的新材料7075铝合金的力学性能优越,满足车架的设计要求,实现了轻量化设计,车架设计质量为113.278 kg,达到减重的目的,但目前材料价格昂贵,随着新材料的普及,具有广阔的发展应用前景。
2) 通过对车架静态特性分析可知,该车架乘员下的横梁部分出现应力集中现象,为后续新能源车架最优设计方案,提供了一定的指导意义。
3) 对车架的模态分析可知,车架虽满足设计要求,但固有频率仍与阶次正相关,寻求一种合理的策略减低车架固有频率并使其收敛,对新型车架的设计方式产生了积极影响。