1. 烟气中氮氧化物的概况与控制的技术特点及其分类
氮氧化物的生成是燃烧反应的一部分:燃烧生成的氮氧化物主要是NO和NO2,统称为NOX [1] 。氮氧化物是燃煤排放的污染源之一,占我国NOX排放总量的60%以上,其中燃煤工业锅炉排放约250万吨 [2] 。按照目前的排放控制水平,到2025年我国氮氧化物排放量将达到2363~2914万吨,将超过美国成为世界第一氮氧化物排放大国,因此,控制氮氧化物的排放问题已是刻不容缓。
氮氧化物的治理越来越受关注,目前在水泥制造行业控制氮氧化物的技术主要有:燃烧控制技术、炉内喷射吸收剂和烟气脱硝技术。
1.1. 燃烧控制技术
氮氧化物生成的最大特点是与燃料的燃烧工况与燃烧方式密切相关,因此,可通过控制燃烧技术来降低氮氧化物生成量及氮氧化物的排放浓度,从而降低氮氧化物的排放,这项技术统称为低NOX燃烧技术 [3] 。在各种NOX减排技术中,低NOX燃烧技术是目前采用最广、相对简单、比较经济且行之有效的方法。
1.2. 在炉内喷射脱硝剂
炉膛喷射脱硝类似于炉内喷钙脱硫过程,实际上是向炉膛上部喷射某种物质,能够在一定条件下还原已生成的NOX以降低排放量。炉膛喷射脱硝包括炉膛喷水或注入水蒸气、喷射二次燃料、以及喷氨等方法。
1.3. 烟气脱硝技术
实现工业化应用的炉内喷射脱硝工艺主要有两类:选择性催化还原(SCR)脱硝和选择性非催化还原法(SNCR)脱硝。
2. 烟气脱硝技术现状
亟待解决经高温反应而产生的烟气的脱硝问题,目前市场上使用的烟气脱硝技术有液体吸收法,如碱溶液吸收法,但NO难溶于水和碱液,使得此法脱硝效率低;固体吸附法,如使用分子筛、活性炭、天然沸石、硅胶和泥煤等吸附剂进行吸附,但固体吸附法操作复杂,运行成本高,脱硝效率低,难以得到广泛地推广使用;同时脱硫脱硝技术,如电子束照射法、脉冲电晕法、液膜法和介质阻挡放电等离子体法等,但这些方法都存在操作难度高,不适宜大规模使用等缺点;催化还原法,如选择性催化还原法(SCR)和选择性非催化还原法(SNCR),催化还原法是目前应用最广泛的两种烟气主流脱硝工艺方法,大约占75%以上。此外,还有络合吸收脱硝和目前在推广的强制氧化–吸收还原脱硝工艺方法。
3. 烟气脱硝工程技术种类
目前烟气脱硝工程技术采用的技术有选择性催化还原法(SCR)和选择性非催化还原法(SNCR)等 [4] 。
3.1. 选择性催化还原(SCR)脱硝技术
选择性催化还原法,即SCR技术 [5] 是目前来说使用最为成熟的烟气脱硝技术,它采用的是炉后脱硝的方法,最早是由日本在1960~1980年期间完成其商业化的运行。而我国的环保行业起步则相对较迟,对于SCR催化剂的应用也相对滞后。在1999年时,我国内陆地区第一次引进了SCR催化剂,并将其用在火电行业的烟气治理上,随着SCR催化剂的不断推广与普及,SCR脱硝技术已经成为减少氮氧化物排放过程的关键技术之一,目前,SCR技术已经广泛地应用在电厂和焚烧厂等工业烟气的脱硝工程上。SCR脱硝技术是以尿素、氨水或液氨产生的氨气作为它的还原剂使用,其原理是在有催化剂参与的条件下,向温度160~400℃的烟气中喷入氨水,选择性地与NOX进行反应,最终生成氮气和水 [6] [7] ,主要反应如图1所示:
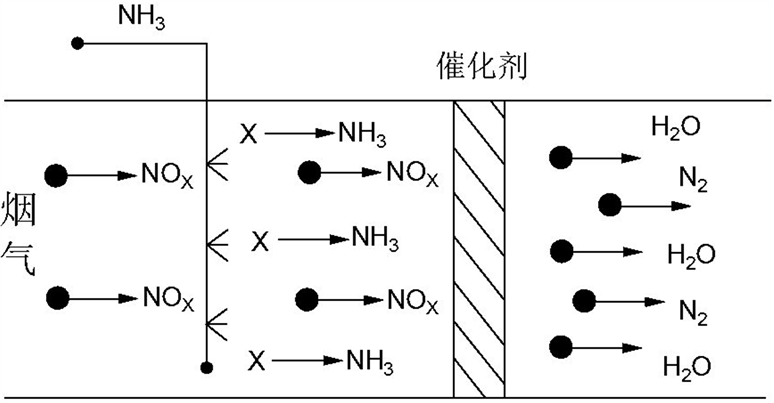
Figure 1. Reaction principle of selective catalytic reduction (SCR) denitrification technology
图1. 选择性催化还原(SCR)脱硝技术的反应原理
选择性催化还原(SCR)脱硝技术的具体反应方程式如下:
(1)
(2)
(3)
(4)
在烟气脱硝中所使用的SCR催化剂,具体可以分为:高温催化剂,其温度范围在300~400℃;中温催化剂,其温度范围在200~300℃;低温催化剂,其温度范围在160~200℃。对于不同类型的催化剂,其各自适应的反应温度也不相同,在实际的应用过程中,也会受限于具体的工艺流程、SCR安装的具体位置和排烟的具体温度参数等 [8] 。
SCR脱硝技术的优点在于其脱硝效率高,其脱硝效率可达90%以上,且没有副产物生成,不会造成二次污染,对于SCR的装置其结构简单,运行相对可靠,便于短期维护等,但是其缺点也是很显而易见的 [9] 。SCR法脱硝中使用的催化剂容易中毒从而失去活性,也会存在一些还未反应的氨气和烟气中的二氧化硫相互反应,会生成亚硫酸氨、硫酸铵和硫酸氢氨,它们容易产生腐蚀和堵塞设备,与此同时还会使氨的利用率降低,最终导致其投资的成本和运行的费用则相对较高。
3.2. 选择性非催化还原(SNCR)脱硝技术
对于选择性非催化还原,即SNCR [10] 的脱硝技术,在脱硝过程中无催化剂的参与,其温度范围为850~1100℃,它是一种将还原剂喷进炉腔内,使得烟气中的氮氧化物被还原脱除,最终生成氮气和水的清洁型脱硝技术。其中还原剂应选择含有氨基的氨水、尿素溶液等,但是目前来说,在生产应用中的过程中一般更偏向于选择尿素作为还原剂来使用,主要原因是由于使用尿素的操作系统更加安全,也不用担心会造成危险化学品氨源(氨气)的泄露,以至于产生新的二次污染 [11] 。
在850~1100℃的温度范围内,利用NH3或者尿素直接还原NOX,其主要反应 [12] 为:
NH3作为还原剂:
(5)
尿素作为还原剂 [13] :
(6)
若反应温度在850~1100℃的范围以上时,NH3易被氧气直接进行氧化,进而降低了要被还原的NOX含量。另外,若温度在850~1100℃的温度范围以下时,那么NH3的反应会不彻底,导致过量的NH3溢出并进而生成硫酸铵[(NH4)2SO4]等,由于硫酸铵容易堵塞空气预热器以及腐蚀装备,而且该最佳温度的范围区间较小。而随着负荷的不断变化,导致最佳温度范围的位置也在不断的变化。因此,要在炉腔内安装较多数量的喷嘴装置,且随着负荷的改变,也要变换相对应喷入点的具体位置以及喷嘴的数量,由于炉腔内反应物的停留时间较为短暂,难以与烟气进行充分的混合,进而造成最终的脱除效率降低。
与SCR工程技术相比,SNCR工程技术无需使用催化剂,并且在反应时使用的还原剂选择灵活,可以是氨,也可以是尿素,相比,SCR烟气的温度范围相对较低,而且尿素也必须要制作成氨后,才可以喷到烟气中。为了满足反应温度所需要的范围,因此对氨喷射的控制,其要求就非常之高,在这一关键点上面也会造成了SNCR脱硝的效率相对不高以及运行的稳定性相对较差,但是对SNCR的投资成本相对较低一点来说,可以适用于低效且快速脱硝的工艺领域,例如水泥窑和玻璃窑等工业用炉和城市垃圾焚烧炉等,这些都是能够直接使用尿素的,而且不会有将SO2转化成SO3的问题及其所带来问题的影响 [14] [15] [16] 。
3.3. 强制氧化–吸收还原(FO-AR)脱硝技术
强制氧化–吸收还原法烟气脱硝技术首先利用强氧化剂(如臭氧、二氧化氯、亚氯酸钠等)将废气中含量较大的NO进行部分的氧化,则生成NO2,再通过调节改变NO2与NO的氧化度,随后,在雾化状态下,NO2、NO与吸收还原剂溶液在脱硝塔内将进行还原反应,得到可以洁净排放的N2、CO2和H2O等产物 [17] 。
NO不溶于水,难以吸收,通过氧化性很强的氧化剂将NO可快速氧化,并转化为NO2或其他高价氮氧化物,如N2O5,而NO2能够溶于水,且比NO价态高,易于被吸收并产生相关的还原反应。
强制氧化部分(部分NO):
(7)
还原反应(以尿素为吸收剂):
(8)
在强制氧化–吸收还原的脱硝反应过程中,其发生反应的条件相对较为温和,且对运行装置的腐蚀性很小,在运行过程中,可以由具体的环保要求和废气中氮氧化物的具体含量来进行随时地调整,该操作步骤较为简单、安全,也可以进行间歇性运行,其操作的弹性较大,在烟气的脱硝过程中,没有固体催化剂的参与,所以无需对大批量的固体催化剂进行投资更换,减少了一定的风险投资,且脱硝反应过程中脱硝使用化学品有机还原剂或金属螯合剂等,是固体或是配置水溶液的状态,在存储、运输和使用过程中其安全性以及环保性更高,脱硝反应过后得到的产物有H2O、CO2和N2等洁净气体,不会产生二次污染物,由于其运行的温度较低,因此能够在40~80℃下进行稳定地操作,烟气经过湿法或半干脱硝之后的温度比较低,这正好符合强制氧化–吸收还原法的操作温度范围。因此,在湿式或半干法脱硝之后,选择强制氧化–吸收还原法脱硝是比较经济的选择,易于在工程上得到推广应用。
3.4. 智能活性氨基还原(IAR)脱硝技术
智能活性氨基还原脱硝技术基本原理与传统SNCR脱硝有类似性,但不是完全相同,一方面,通过在低氮分级燃烧的分解炉还原区,喷入活性氨基干粉脱硝组份,在含氧量较低的环境下,与烟气中NOX反应生成无污染的N2和H2O,并且与喷入的煤粉共同起活性还原组份,反应非常快;另一方面,在原来SNCR喷入氨水区,改用活性氨基液体组份,完全可代替氨水和尿素的功效,而且产生的N2和H2O,对环境没有污染,这样,其高温区和次高温区,采用活性氨基成分不同,其控制原理也都大不相同,为此,基于目前最先进的大数据技术,寻找最佳窗口温度和环境条件参数,有针对性地进行双重脱硝控制。具体技术要点:(1) 通过双向控制,其间隙时间有1~5分钟,可以随时在氨基干粉脱硝和氨基液体脱硝来相互调整,同时根据燃烧对象成份可以实现提前预测与分析判断;(2) 对原有在分解炉的还原区喷入煤粉,可进行改进,一方面,提高活性氨基与碳氢化合物的还原效果,另一方面,在三次风量作用下,提高燃煤的燃烧效率;(3) 对氨基液体脱硝的相对扁平化喷枪的布置,可采用分级布置,将喷枪布置在更加宽的温度窗口区间,实时跟踪工况参数的变化,及时调整并分别控制活性氨基液体脱硝的喷射位置及喷射量,从而达到提高脱硝效率的目的;(4) 在控制方案上,完全采用在不同温度窗口下的开放式控制,首先在分解炉的还原区,根据NOX的总含量,喷入氨基干粉脱硝,使得从源头得到大幅度降低烟气中NOX的量,从而可减少后面液体脱硝的压力,在液体脱硝喷枪布置上,有多个点环流作用,根据实际工况情况,可采用集中式分布脱硝的智能化控制,而不是采用单一化学计量比的方式,通过收集到的广泛数据信息,形成输入参数,通过控制策略,找到该工况条件下的控制方案的优先级,灵活调配投入多点处的喷枪,以及各路喷枪的流量和压力,以做到相对精准脱硝。
4. 低氮分级燃烧技术
4.1. NOX的生成机理
对环境污染最为严重的是NO和NO2,通常用NOX来表示这两种成分的总量。NOX可分为三种类型:燃料型NOX、热力型NOX和快速温度型NOX [18] 。
4.2. 燃料型NOX的生成机理
燃料氮氧化物是煤中氮转化生成的氮氧化物,它分为挥发分氮氧化物及焦炭氮氧化物。由于燃料中的有机氮存在于某些复杂的化合物中,与空气中氮相比,其结合键能量较小,因而这些有机化合物中的原子氮较容易分解出来,氮原子的生成量大大增加,通过热解过程,通常可以释放出N、CN、HCN、NH3等含有氮元素的中间基团,而这些中间基团可进一步地进行的反应存在两种不同的趋势。即一种是与火焰燃烧过程中形成的含氧的中间基团(O、OH、O2等)发生氧化作用形成NOX,增加NOX的排放;另一种趋势则是与已经形成的NO发生还原作用形成N2,导致NOX浓度降低。通常中间反应物的形成是很快的,最终燃料氮氧化物形成量就取决于两个平行反应之间的竞争。与其他反应机理相比,燃料氮氧化物的形成强烈依赖于形成过程中不同反应物的浓度比例关系,而与温度的关系并不显著。作为简化处理,通常认为影响燃料NOX中起主要作用的中间产物是NH3和HCN。对于煤粉燃烧而言,煤粉中的含氮量对燃料氮氧化物的形成量具有最显著地影响。在相同的燃烧条件下,NOX生成量是随着燃料中氮含量的增加而增加的。随着空气过剩系数α的降低,燃料NOX的生成量呈下降趋势,在α < 1的区域内,这一趋势则变得更加明显。与热力型氮氧化物的形成不同,燃料氮氧化物的形成与温度的关系并不明显 [19] 。
4.3. 热力型NOX的生成机理
热力型NOX的形成需要有游离的氧原子作为引发剂,热力型NOX的形成和燃烧温度的关系很大,所以通常也把热力型NOX称为温度型NOX。在温度低于1500℃时,热力型NOX的形成量较少;当温度超过1800℃时,NOX的主要来源是热力型NOX。热力型NOX的形成和氧气浓度或者说空气过剩系数的关系也很大,最大的热力型NOX形成量总是偏移出现在α > 1的区域内。热力型NOX通常是介稳反应,随着烟气在高温区域的停留时间的延长或提高燃烧温度加快反应速度都将不可避免地增加热力型NOX的形成 [20] 。
4.4. 快速温度型NOX的生成机理
空气中的氮分子在着火的初始阶段,生成快速温度型NOX,与燃料燃烧的中间产物烃(CHi)等发生撞击,生成中间产物CN和HCN等,再经氧化,最后会生成NOX。其转化率的高低取决于过程中温度水平和空气过剩条件。快速温度型NOX的产生是由于氧原子的浓度远超过氧分子离解的平衡浓度的缘故。当氧原子的浓度比平衡时的浓度高出十倍,在火焰的内部会迅速发生反应,形成NOX。由于氮氧化物形成总量中快速氮氧化物仅占3%~5%,因此在讨论NOX减排作用时,通常可以忽略快速温度型氮氧化物的影响 [21] 。
4.5. 水泥窑的NOX的形成特点
在水泥生产过程中,分解炉和回转窑是两个主要的生产烧成设备,新型干法水泥窑是NOX的主要生成点。生料的分解过程主要在分解炉内完成,分解后的产物会进入回转窑,继续进行高温煅烧,最后形成水泥熟料。在整个水泥的生产过程中,其中产生的煤粉有60%~70%进入分解炉,炉内的温度一般控制在850℃~1000℃范围的内,在这个温度下,基本可以不考虑快速型和温度型NOX的形成,主要会形成燃料型NOX。回转窑内主要是煅烧时物料的熔融和重结晶过程,物料的反应温度必须超过1400℃,因此通常将水泥窑主燃烧器形成的火焰温度控制在1800℃~2200℃之间,这样在回转窑内燃料型NOX和温度型NOX均有较大的形成比例,其中会有少量快速型NOX生成 [18] 。
4.6. 目前水泥窑脱硝措施主要从三个阶段入手 [22]
(1) 燃烧前预处理:主要指原料、燃料的脱氮或者采用低氮原料、燃料。由于我国现有资源结构和能源政策的限制,加之其难度大,成本高,使得这些措施一般难以实现。(2) 燃烧过程控制:即控制煅烧过程中氮氧化物的生成。一般采用低氮燃烧器、分级燃烧或加入矿化剂等手段。(3) 燃烧后处理:是在烟气排放前减少排放,常用的方法有选择性非催化还原法(SNCR),选择性催化还原法(SCR),以及目前开展的强制氧化吸收还原(FO-AR)法等。
4.7. 分级燃烧脱氮及基本原理
4.7.1. 脱氮原理的反应概况
水泥熟料生产过程中,燃料燃烧产生的NOX主要有两种类型:燃料型NOX、热力型NOX。热力型NOX主要是温度高于1500℃时,空气中的N2和O2反应而生成的。回转窑中烧成带火焰温度高达1500℃以上,除产生燃料型NOX以外,大量助燃空气中的氮在高温下被氧化产生大量的热力型NOX。在分解炉燃料燃烧温度约为950~1200℃,在此温度范围内,主要生成燃料型NOX。有关NOX的控制方法国际上把燃烧中产生的NOX的所有控制措施统称为一次措施,即为低氮燃烧技术。窑系统排出废气中的NOX,主要是在窑内煅烧带高温条件下产生,预分解窑中窑内所用燃料比愈多,相应的窑用煤比减少,生成的NOX也相应减少,这主要是由于烟气对窑中NOX有稀释和一定的还原作用。
4.7.2. 分级燃烧脱氮反应的基本原理
在分解炉内建立还原燃烧区,将原分解炉用煤的一部分均匀分布到该区域内,使其缺氧燃烧(第一级燃烧区域内空气过剩系数小于1)以便产生CO、CH4、H2、HCN和固定碳等还原剂 [23] 。这些还原剂与窑尾烟气中的NOX发生反应,将NOX还原成N2等无污染的惰性气体。此外,煤粉在缺氧条件下燃烧也抑制了自身燃料型NOX产生,从而实现水泥生产过程中和垃圾焚烧发电过程中的NOX减排。主要化学反应如下:
(9)
(10)
(11)
4.7.3. 降低氮氧化物排放的技术比较
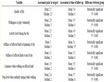
Table 1. Comparison of technologies for reducing nitrogen oxide emissions [22]
表1. 降低氮氧化物排放的技术比较 [22]
如表1所示,根据“工艺成熟、技术先进、经济合理”的选择性原则,采用分解炉分级燃烧技术和精细化操作相结合的低氮分级燃烧技术,对分解炉进行相应改造,分级加入燃料,在分解炉的锥部及下端形成还原区或扩大还原区,以还原窑内产生的热力型氮氧化物,并且可以抑制燃料型NOX的产生,同时再配合操作优化调整,控制窑内的燃烧气氛,以达到减少窑头煤粉燃烧空气过剩系数,降低窑尾烟气氧含量,从而降低并稳定NOX的减排效果。
4.7.4. 低氮分级燃烧技术的工艺流程及分解炉结构
通过在窑尾烟室用煤,在分解炉底部和窑尾烟室形成还原气氛,窑尾烟室及分解炉底部的氧气(O2)含量会下降,相应的一氧化碳气体含量会增加。该法采用的是先进的新型干法预热预分解技术,具有超大型单机产量,这不仅极大地降低了热耗,提高了劳动生产率,并且,分解炉中的CaCO3还可以达到有效吸收SOX的目的,降低SOX的排放,而且分解炉中的煤粉低温燃烧,可以大大降低NOX的生成和排放 [24] 。
分解炉的位置在窑尾烟室之上,下部分为进行NOX分解还原的低NOX段,上部分为主炉段,进行生料分解和煤粉燃烧燃尽过程,分解炉中的煤粉全部从低NOX段下部喷入到窑尾烟室,C4段下料经过分料阀,25~30%的物料会加入到低NOX段,其余物料加入到主分解炉段的下部,三次风从主炉段的下部加入,低NOX段的煤粉在低氧含量的窑尾烟气中部分燃烧 [25] ,工艺流程和分解炉的结构如图2所示:
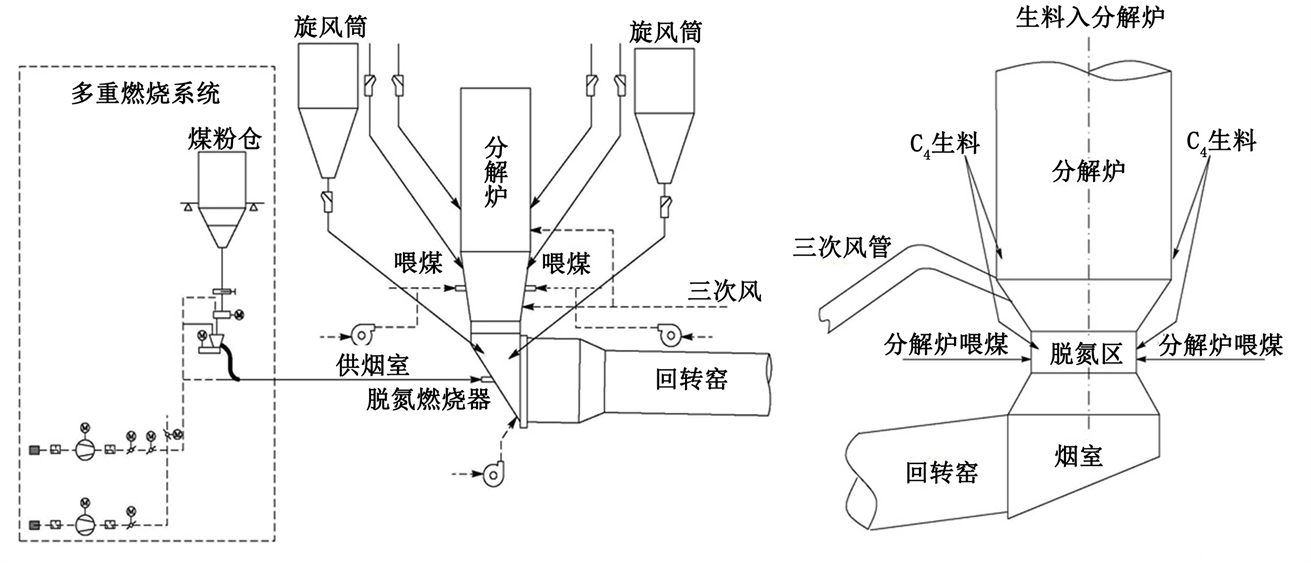
Figure 2. Process flow of low nitrogen staged combustion technology and structure of decomposition furnace [26]
图2. 低氮分级燃烧技术的工艺流程及分解炉的结构 [26]
根据低氮分级燃烧技术的工艺流程及分解炉结构,可知,分级燃烧脱氮效果明显需要工况参数:(1)在窑尾的氧含量一般要在1~4%之间;(2) 还原性物质还原NOX所需的停留时间为0.5~3.0 s;(3) 窑尾温度为875~1150℃,强力还原区温度900℃以上;(4) 脱氮区扩大为强力还原区,可大幅度的提高还原效果,提高反应效率。
4.7.5. 低氮分级燃烧技术的主要途径
低氮分级燃烧技术的主要途径有:(1) 减少燃料周围的氧浓度,包括减少炉内过剩空气系数,以减少炉内空气总量;或减少一次风量和挥发分燃烬前燃料与二次风的掺混,以降低着火区段的氧浓度。(2) 在氧浓度较少的条件下,使燃料中的氮不易生成NOX,而且使生成的NOX经过均相或多相反应而被还原分解。(3) 在过剩空气的条件下,降低温度峰值,以减少热力NOX,如采用降低热风温度和烟气再循环等 [27] 。
4.8. 低氮分级燃烧下智能氨基干粉还原(IAR)脱硝工艺技术
在分解炉煤粉螺旋输送机上按比例加入干粉还原脱硝剂,与煤粉混合均匀后,利用煤粉输送设备分两级喷入分解炉。烟气以4 m/s左右的速度在分解炉中与汽化的脱硝剂混合反应,干粉脱硝剂主要分解成活性还原剂,如CO、H2、NH2、HCN,对熟料不会产生影响,还原后主要形成N2、CO2和H2O等洁净气体,随烟气排放,干粉脱硝剂助剂主要含有Ca、Si、Al、Fe等元素组成的多组分物料,经煅烧可直接进入熟料。并且这些含有Ca、Si、Al、Fe等元素组成的物料可作为煤粉的催化剂,提高煤粉的燃烧热值,从而可以适度减少煤粉使用量,以降低成本。主要位置如图3所示:
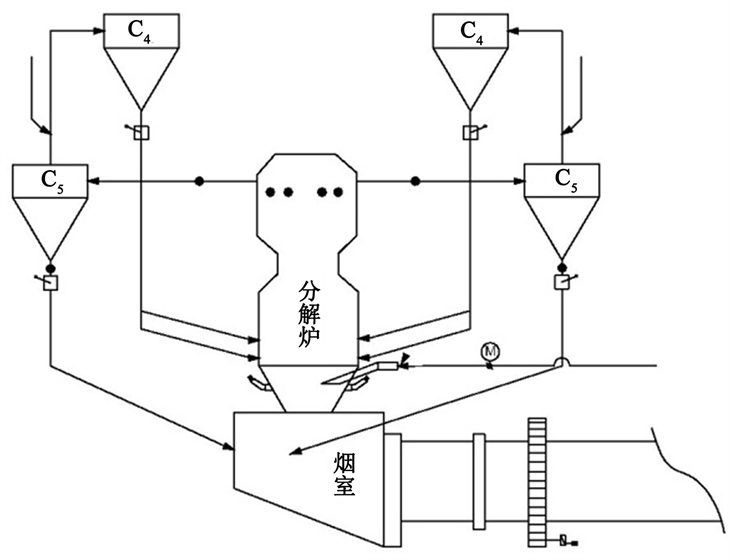
Figure 3. Schematic diagram of the arrangement of dry powder denitrification addition points and liquid spray gun positions [28]
图3. 干粉脱硝加入点与液体喷枪位置布置示意图 [28]
充分利用水泥窑的低氮分级燃烧在分解炉内780~900℃的温区,以4 m/s左右流动的烟气循环路径约20 m,即约有5 s的反应时间,分解炉内含氧量约小于等于2.0%,在该窗口温度下,干粉脱硝剂有效成分可迅速分解气化,在含氧量极低的条件下,有充足的反应时间,可提高脱硝效率,并且该试验方案运行方式简单。干粉还原脱硝剂在螺旋输送机加入煤粉中,经过转子秤计量、罗茨风机吹送,分两级直接喷入分解炉的炉膛,试验时设备无需做出较大的工艺调整和改动。在对称的两个C5级筒处,使用SNCR 脱硝工艺中氨利用率有限,为了还原NOx必然使用过量的氨,在不改变原先SNCR脱硝工艺与设备的前提下,一方面在煤粉中加入助剂,起到固硫脱硝的功效;另一方面应用含活性碳氢和氨基复合单元,在855~885℃范围内,从SNCR雾化喷枪的入口,喷射改性的脱硝剂水溶液组分。
5. 总结
随着民众对大气环境保护要求的不断提高和国家对各种有害气体排放浓度以及总量的要求越来越严格,水泥企业在环保方面的投资成本也越来越大,由此可见,低氮分级燃烧技术的应用正是顺应趋势的发展方向。为此,在低氮分级燃烧技术的基础上,充分利用分解炉内的参数与工况条件,同室温智能干粉脱硝技术,或前期推广的无氨化脱硝窑尾烧成的技术相结合,使得经高温反应而产生的NOX,在分解炉的还原区(扩大还原区)得到源头治理,进气脱硝效率可以达到90%以上,以减少后面SNCR脱硝的压力,以及降低氨与尿素的使用成本,并且智能干粉还原脱硝的运行成功,也可以减少目前应用水泥窑中段的相对不稳定的SCR工程技术,减少重投资和不必要的重复建设,具有重大的工程化应用前景与节能减排的意义。