1. 引言
为实现双碳目标,响应国家节能降碳,优化能源结构,实现煤电机组超低排放,对火力发电行业进行燃煤锅炉低氮燃烧和减碳排放改造将是重要的研究领域之一。
富氧燃烧技术是主要的低氮燃烧技术之一 [1] ,又称为燃烧中碳捕集技术,是最具潜力的新型碳减排燃烧技术之一 [2] 。生物质能是一种重要的可再生能源,具有零碳特性,然而,生物质具有热值低、分布不集中、集中收集成本昂贵、供应受季节影响等特点,直燃生物质易造成炉内结焦,同时燃烧过程产生大量的氯元素和碱金属也会对炉膛造成腐蚀,危害锅炉运行,因此将生物质通过处理形成生物质气并与煤粉混燃,可以解决生物质利用存在的上述问题。
国内外针对富氧条件下生物质与煤粉混燃进行了广泛的研究。文献 [3] [4] [5] 研究表明,生物质与煤在富氧条件下燃烧的最高反应温度比空气氛围的要低,且生物质的加入可以改善煤的燃烧特性;Liu Hao等 [6] 利用顶烧式燃烧炉对比研究O2/CO2气氛与O2/N2气氛下火焰燃烧温度,结果表明在O2/CO2气氛下O2浓度维持在30%时煤粉燃烧效率与O2/N2气氛中基本相同;Chen等 [7] 对鼓泡流化床中煤与生物质在富氧下的混燃过程进行了研究,结果表明,与煤粉燃烧相比,在焦燃烧区,混燃的温度比煤粉的要低10 K,同时,烟气出口有较低的CO2浓度;彭龙飞等 [8] 研究发现:在O2/CO2气氛下,炉膛温度由于CO2较大的比热容而下降,随着气氛中氧气浓度的提高,使煤粉燃烧强度增大,炉内温度上升,让煤粉燃烧特性得以改善。在生物质与煤粉混燃的NOx排放研究方面。Liu等 [9] 计算结果表明,相比空气气氛,O2/CO2气氛中NOx排放量将减少75%左右,且NOx主要为燃料型NOx;Zhang等 [10] 研究表明,在富氧燃烧的还原性区域有更多的挥发分氮转变为NO,而在氧化性区域NO的转化受到抑制,但挥发性氮对其影响较小;王鹏乾等 [11] 认为提高炉膛温度和O2/CO2气氛中二氧化碳体积分数将增加NO2浓度,高体积分数的CO2能促进NO2的还原,而高体积分数的O2在一定程度上对NO2的还原有抑制作用;文献 [12] 研究了生物质与煤在循环流化床炉中富氧混合燃烧时污染物的生成机理,表明,与煤粉单独燃烧相比,生物质/煤燃烧过程中,燃料N转化率和SO2排放量较低,且随着生物质掺烧比升高,燃烧N转化率不断降低,SO2排放量不断降低;文献 [13] [14] 表明,与空气气氛相比,21% O2/79% CO2气氛下NO的排放量较低,燃料N转化率较低。Stanger和Singh等 [15] [16] 研究表明在富氧条件下,生物质气与煤粉混燃过程产生的CO2随着氧气浓度的提高而提高,可以采用碳捕集的手段进行收集;Chowdhury等 [17] 通过数值模拟研究了空气气氛与30% O2的富氧气氛下,不同煤/生物质的混合比下混烧的燃烧与排放特性,结果表明,当增加了生物质的比重后,炉内将产生更高浓度的CO,从而产生更高浓度的CO2。
终上所述,国内外对生物质与煤粉在富氧条件下的燃烧特性、CO2与NOx排放有深入研究,但对于CO2与NOx协同控制排放上的研究还比较空白,本文通过数值模拟与文献印证的方法系统研究了富氧下生物质气与煤粉混燃过程中生物质气掺烧比对NOx与CO2的协同排放控制。为我国优化能源结构,提高热能动力系统的运行灵活性,降低碳排放,控制NOx污染,提供技术理论支撑。
2. 研究对象及物理模型
2.1. 350 MW四角切圆锅炉概况
以某电厂350 MW四角切圆煤粉锅炉为研究对象,此锅炉为亚临界压力、一次中间再热、平衡通风、燃烧器四角布置、双切圆悬浮燃烧、固态排渣、整体结构为全悬吊结构、露天布置及Π型布置的强制循环汽包锅炉。锅炉具体尺寸为宽度14620 mm,长度为12430 mm,高度为55800 mm。燃烧器基本型号为M-PM低NOx燃烧器,布置于炉膛四角形成切向射流,每组燃烧器高13106 mm,并配有13层喷口,分别为五层一次风燃烧器(A-E)、五层二次风燃烧器(AA-DE)和三层燃尽风燃烧器(OFA1-OFA3),其中一次风燃烧器(A-E)携带煤粉。一次风喷口的尺寸(宽 × 高)为480 mm × 480 mm,二次风喷口的尺寸(宽 × 高)为640 mm × 520 mm,燃尽风的喷口尺寸(宽 × 高)为640 mm × 400 mm。锅炉燃烧的假想切圆直径分别为1140 mm和1740 mm。锅炉本体尺寸、燃烧器布置和炉膛横截面如图1所示。
本文中富氧混燃下,采用的煤种为神化混煤,其特性参数见表1,生物质气采用秸秆气,其燃料特性见表2。
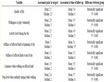
Table 1. Proximate and elemental analysis of coal
表1. 煤的元素分析与工业分析
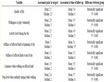
Table 2. Biomass gas characteristics
表2. 生物质气的燃料特性
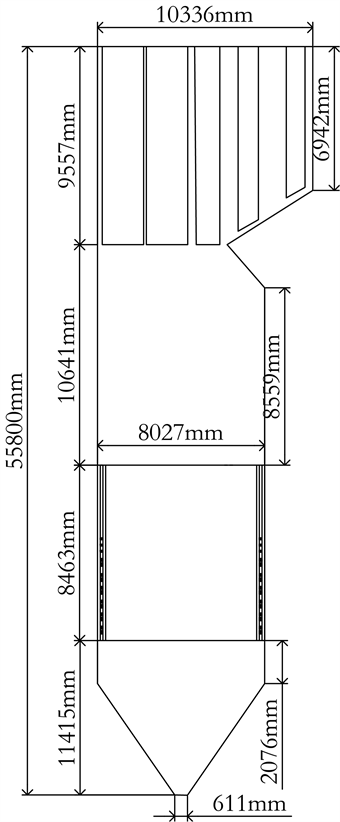
Figure 1. The schematic diagram of boiler body dimensions, burner arrangement and furnace cross-section
图1. 锅炉本体尺寸、燃烧器布置和炉膛横截面示意图
2.2. 物理模型
根据350MW四角切圆锅炉的具体结构尺寸,建立锅炉三维物理模型,如图2(a)所示。由于本文重点研究富氧条件下煤粉在炉内流动与燃烧特性,故在建立物理模型的过程中可不考虑锅炉炉膛上部的过热器与再热器部分,这样处理虽会导致炉膛出口的温度上升,但不影响炉膛出口的组分浓度。
本文采用分区划分网格方法,使用高质量六面体网格。为准确的模拟和描述燃烧器区域的速度、温度和组分等物理量变化梯度大的特性,对燃烧器区域的网格进行适当加密,锅炉网格模型如图2(b)所示。
(a)锅炉三维模型
(b)锅炉网格模型
Figure 2. Boiler 3D and mesh model
图2. 锅炉三维和网格模型
分别采用网格数为69万、92万和113来进行网格无关性检验,从图3(a)与图3(b)中可以看出,直线α (x = 6.215 m,y = 7.31m,z = 0~55.8 m)沿炉膛高度方向的温度与速度在三种网格下的变化趋势一致,且误差较小,因此为保证计算精度,同时节省计算时间,采用92万网格进行模拟计算。
(a) 直线α沿炉膛高度的温度分布
(b) 直线α沿炉膛高度的速度分布
Figure 3. Grid independence test results
图3. 网格无关性检测结果
3. 数值计算方法与模拟工况
3.1. 数学模型
富氧条件下CO2替代了空气中的N2,CO2的化学物理特性与N2有明显不同,同时生物质气具有低热值和高流动性,且含有还原性气体CO与H2,两者的共同作用导致富氧下四角切圆锅炉内煤粉掺烧生物质气与纯煤粉燃烧在炉内流动、辐射换热、煤粉热解及气相物质的燃烧,以及NOx生成等方面均有显著差异,因此,通过研究富氧混燃机理,选择合适的数学模型及数值计算方法,对提高数值模拟的准确性至关重要。
1) 煤粉颗粒运动
基于生物质气与煤粉富氧混燃的特点以及四角切圆锅炉炉内的流动特性,炉内煤粉颗粒的运动采用欧拉–拉格朗日坐标下的随机轨道模型计算,与空气相比,富氧气氛的密度与粘度发生改变,导致煤粉颗粒的运动方式也相应发生变化,采用公式(1)来描述煤粉颗粒在富氧氛围中的运动,其中煤粉颗粒运动主要考虑气体阻力与重力影响 [18]
(1)
式中,
为煤粉颗粒质量,kg;
为阻力系数;
与
为富氧气体与煤粉颗粒密度,kg/m3;
为煤粉颗粒投射面积,m2;
与
分别为富氧气体与煤粉颗粒速度,m/s;
为煤粉颗粒体积,m3;G为重力加速度,m/s2。
2) 气相湍流流动
煤粉富氧混燃与煤粉空气燃烧在气相湍流流动的建模中区别不大 [19] ,采用Realizable
模型所得到的模拟结果与实验结果十分接近。
3) 辐射传热
炉内的辐射传热采用DO模型,与空气相比,富氧中高浓度的CO2促进了煤粉燃烧过程中的辐射传热,因此通过修正的富氧WSGG模型来计算气体的吸收系数,其中气体混合物的总发射率ε为:
(2)
式中,
为基于气体温度下第i组灰气体的发射率加强系数,通过式(3)计算;
为第i组灰气体的吸收系数;P为所有吸收性气体的分压的总和,atm;L为辐射的行程长度,m。
(3)
式中,
为关于富氧气体温度的多项式的系数,系数
与
的值参照文献 [20] 来设置。
(4) 煤粉热解
煤粉的热解采用单速率方程模型,挥发分析出的速率表达式如(4),其中指前因子A为4.68 × 1011 s−1,活化能 为1.559 × 108 J/kmol。文献 [21] 通过热重分析研究了烟煤在富氧与空气中的热解过程,从图4中可看出两种气氛下煤粉的热解与挥发分析出差异不大。因此适用于煤粉空气燃烧的单速率方程模型也同样适用于富氧燃烧,其表达式为:
(4)
式中,W为挥发分质量,kg;K为挥发分析出速率,s−1;R为理想气体常数;T为反应温度,K;A为指前因子;
为反应活化能,J/kmol。
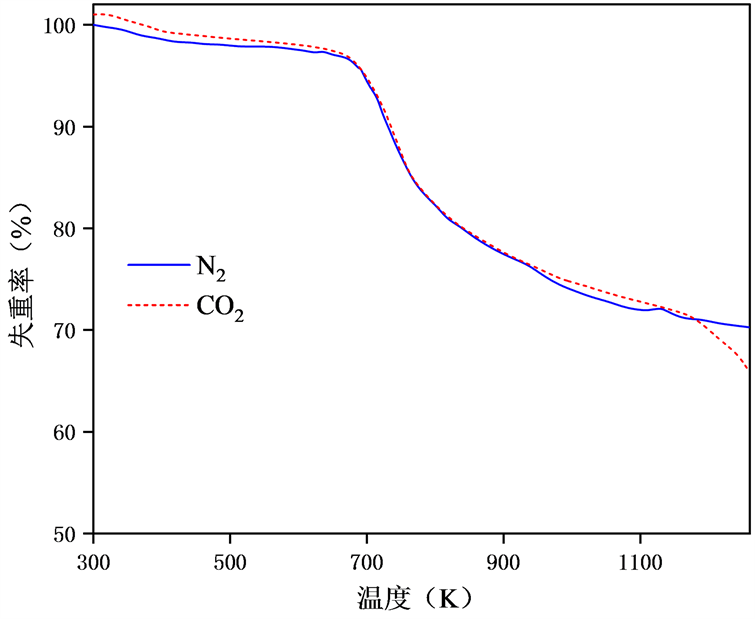
Figure 4. Pyrolysis of bituminous coal in N2 and CO2
图4. 烟煤在N2与CO2中的热解
5) 煤粉热解挥发分及生物质气的气相燃烧
煤粉热解挥发分与生物质气的燃烧采用有限速率/涡耗散模型,煤粉挥发分燃烧的反应如式(5)~(7),生物质气燃烧的反应如式(7)和(8),对应的指前因子A与活化能
见表3。
(5)
(6)
(7)
(8)
6) 焦炭燃烧
焦炭燃烧过程主要进行气化与氧化反应,采用多表面反应模型模拟焦炭的非均相燃烧,多表面反应通过动力/扩散模型进行建模,相关反应如下:
(9)
(10)
(11)
其中,反应(9)~(11)的速率由公式(12)~(14)来计算,相应的指前因子和活化能见表3。
(12)
(13)
(14)
式中,
为焦炭颗粒的消耗速率,kg/s;
为氧化剂(即CO2、H2O、O2)分压,Pa;DO为反应扩散速率系数,m2/s;
为焦炭的化学反应速率,kg/(m2∙Pa∙s);C1为扩散速率常数;
与
分别为焦炭颗粒温度与环境温度,K;
为焦炭颗粒直径,m。
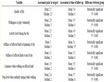
Table 3. Kinetic parameters of pulverized coal volatile fraction and char combustion
表3. 煤粉挥发分与焦炭燃烧的动力学参数
7) NOx的排放
采用后处理的方法计算炉内NOx的生成,对于煤粉空气燃烧,NOx的生成一般采用基于自由基O和OH浓度的部分平衡法来计算。基于Zeldovich机制,NOx的生成有主要为反应(15)和(17),当处于富氧环境下,可能存在NO的再燃反应(17)。同时,生物质气中存在还原气体CO与H2,能够还原煤粉燃烧过程中产生的NO,从而降低炉膛中NOx生成量,反应为(18)~(20)。
(15)
(16)
(17)
(18)
(19)
(20)
3.2. 边界条件
各一次风燃烧器及二次风入口设置为质量入口边界;出口设置为−40 Pa压力出口边界。壁面设置为无滑移边界条件,设置壁面温度为700 K,壁面发射率为0.6。设置离散项的类型为reflect,其中,冷灰斗底面温度设置为460 K,壁面发射率设置为1,离散相类型设置为trap。假定煤粉的粒径服从Rosin-Rammler分布,平均粒径为56 μm,分布指数为1.5。
3.3. 模拟工况
本文为研究富氧下煤粉掺烧生物质气过程中生物质气掺烧比对NOx与CO2的协同排放规律,在29% O2/71% CO2氛围下,采用生物质气热值掺烧的方式,在保证进入炉内总热值不变的情况下,设置生物质气的掺烧比例分别为0、5%、10%、15%、20%、25%、30%、35%,且生物质气从燃烧器C层喷口射入,具体工况设置如表4所示。
模拟方案1~8中生物质气的温度均为363 K,一次风温均为337 K,二次风和燃尽风风温均为484 K。
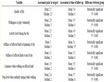
Table 4. Simulation of working conditions
表4. 模拟工况
4. 计算结果与分析
4.1. 温度分析
图5和图6分别为不同生物质气掺烧比下炉膛纵截面、煤粉燃烧层和生物质气燃烧层温度云图和沿炉膛高度方向截面平均温度分布图。从图中可以看出,在不同生物质气掺烧比例下,炉膛内的温度分布特点是相同的,高温区域主要分布在燃烧器区域和燃尽区域。燃煤锅炉掺烧生物质气后,在煤粉与生物质气层均能形成良好切圆,使燃烧过程趋于稳定。
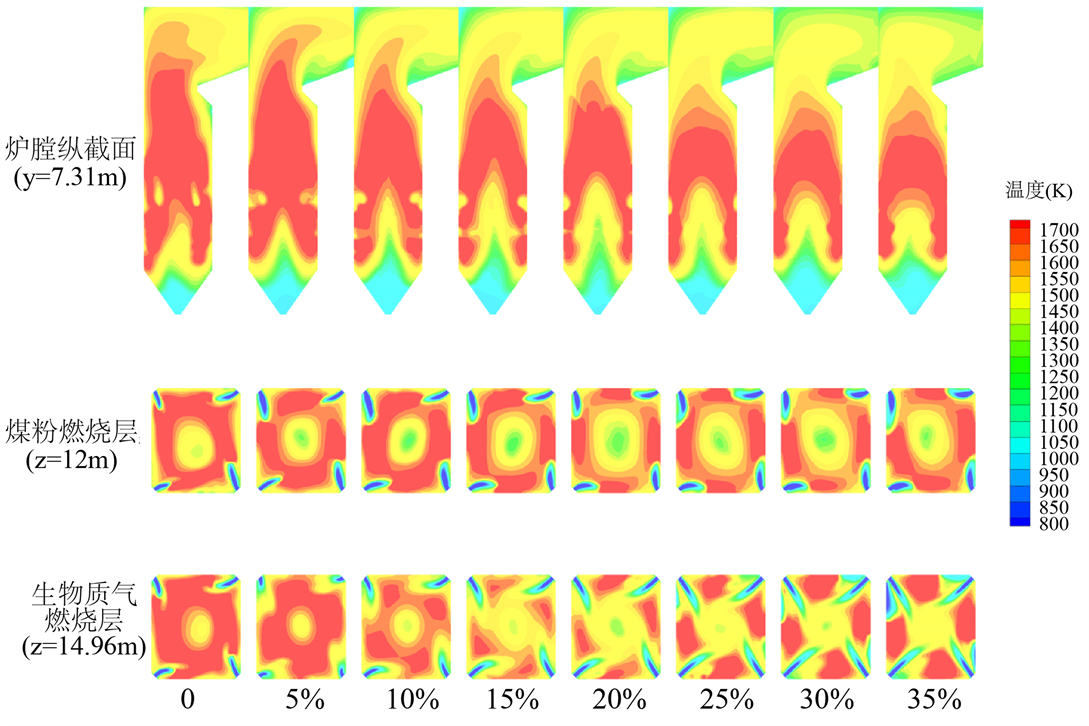
Figure 5. The temperature clouds of the longitudinal section of the furnace, pulverized coal combustion layer and biomass gas combustion layer with different biomass gas blending ratios
图5. 不同生物质气掺烧比下炉膛纵截面、煤粉燃烧层和生物质气燃烧层温度云图
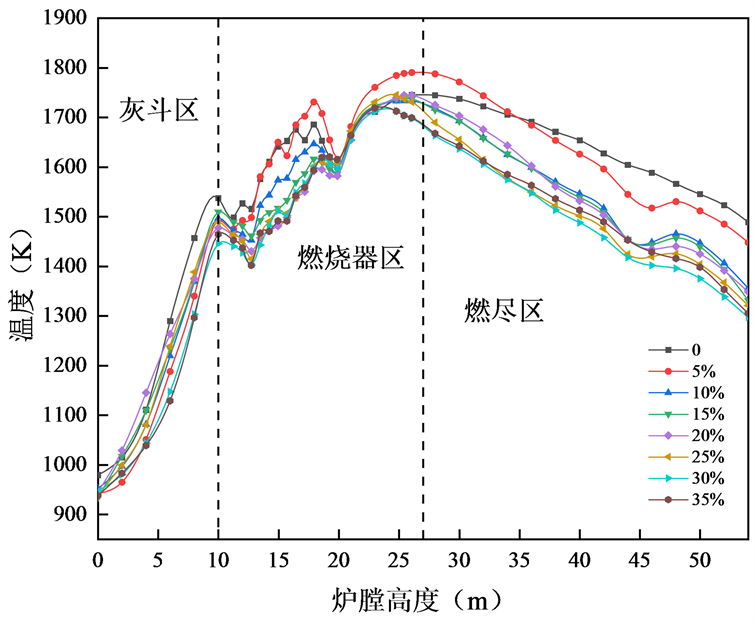
Figure 6. The average temperature distribution of the cross section along the height of the furnace
图6. 沿炉膛高度方向截面平均温度分布
随着生物质气掺烧比例的增加,炉膛内峰值温度整体为逐渐下降的趋势。主要由于生物质气的单位热值低于煤粉,相同质量的生物质气燃烧产生的热量小于煤粉燃烧产生的热量,导致炉内温度呈现下降的趋势。但当掺烧5%的生物质气时,出现最大的峰值温度,原因可能是生物质气燃烧所产生的热量虽然低于煤粉,但随着生物质气的掺烧改善煤粉的燃烧状况,使其比纯煤粉燃烧更为充分,释放出更多热量,从而使掺烧5%生物质气的炉膛峰值温度高于纯煤粉燃烧的炉膛峰值温度。随着生物质气掺烧的比例增大,C层,即生物质气燃烧层的切圆面积是逐渐减小的,当掺烧比例为0~20%时,截面的温度梯度逐渐变小,且变化明显,当掺烧比例为25%~35%时,温度梯度变化基本不变,说明当生物质气掺烧比例大于等于25%时,随着掺烧比例的增大对炉膛温度影响不大,说明生物质气的掺烧虽然产生的热值小于煤粉,但其高流动性改善了煤粉的燃烧效率,与文献 [8] 结论一致。
4.2. O2体积分数分析
图7沿炉膛高度方向截面平均O2体积分数分布。从图中可以看出,各工况下炉膛高O2浓度区域均在燃烧器区域,到燃尽区域后O2浓度均下降,主要原因在于燃烧器区随着富氧气流的进入使氧气浓度增加,然后随着煤粉与生物质气的燃烧消耗了富氧气氛中的氧气,导致氧气浓度的降低。随着掺烧生物质气比例的增加,燃烧器区域的高氧气浓度区域下降得越快,原因是在保证输入炉内相同热值的情况下,生物质气燃烧相比于煤粉燃烧所需要的氧气量更多。同时,当掺烧生物质比例增大时,炉膛内流动速度加大,炉膛出口的烟气流速增加,导致炉膛内O2浓度更低,有利于抑制HCN和NH3向NO的转化 [25] 。
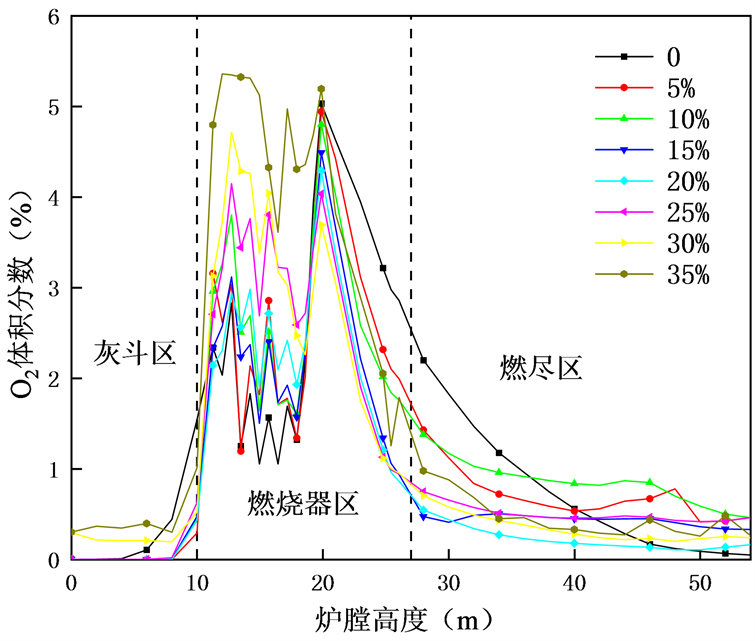
Figure 7. The distribution of the average O2 volume fraction of the cross-section along the height of the furnace
图7. 沿炉膛高度方向截面平均O2体积分数分布
4.3. CO2体积分数分析
图8沿炉膛高度方向截面平均CO2体积分数分布。从图中可以观察到,纯煤粉燃烧炉内CO2体积分数高,煤粉中掺烧生物质气后锅炉内CO2生成量减少,且随着生物质气掺烧比例的增加,炉膛内CO2浓度是逐渐降低的。原因可能是当煤粉中掺烧生物质气后,一方面生物质气中的低浓度CO2 (8%)对富氧气氛中的高浓度CO2 (71%)有稀释作用,另一方面生物质气的加入,增加了炉内烟气量和烟气速度,导致煤粉可能没有完全燃烧,而使CO2生成量减少 [26] 。因此,当掺烧过高比例的生物质气时,炉膛出口的CO2浓度较低,不利对CO2的捕集。当掺烧比例为0~20%时,炉膛出口的CO2浓度是整个炉膛内CO2浓度最高的位置,当掺烧比例为25%~35%时,炉膛出口的CO2浓度要低于灰斗区域的,表现在灰斗区域有CO2的富集。原因可能是当掺烧比例为0~20%时,由于掺烧生物质气的比例不高,生物质气使流场速度增加有助于改善煤粉燃烧状况,使其燃烧更为充分,产生更多的CO2;当掺烧比例为25%~35%时,炉膛中CO2浓度呈现下降趋势,原因是同等质量下煤的含C量大于生物质气,生物质气掺烧比例越高,燃烧产生的CO2越少 [27] ,同时也增加了锅炉的机械不完全燃烧热损失,因此当掺烧生物质气的比例更多时,可能会破坏炉膛良好的燃烧状况,从而影响锅炉热效率。
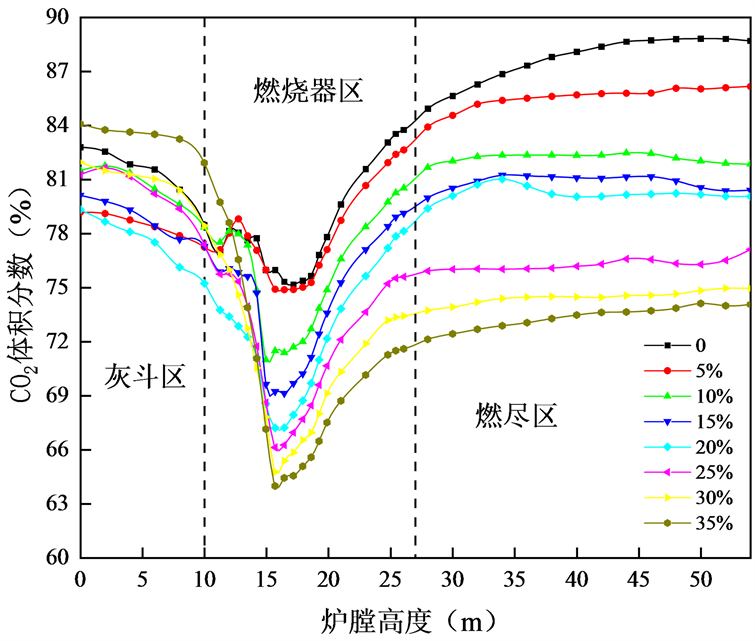
Figure 8. The distribution of the average CO2 volume fraction of the cross-section along the height of the furnace
图8. 沿炉膛高度方向截面平均CO2体积分数分布
4.4. NOx体积分数分析
图9沿炉膛高度方向截面平均NOx体积分数分布。从图中可以观察出,富氧气氛下纯煤粉燃烧的NOx体积分数分布与煤粉与生物质气混燃的NOx分布是不同的,纯煤粉燃烧时,高NOx浓度区域主要在燃烧器区域,而掺烧了生物质气后,高NOx浓度区域主要在灰斗区域和燃烧器区域,主要原因可能是掺烧生物质气后加强炉内的扰动,使部分燃料流向了灰斗区,使该区域的NOx浓度也偏高。随着掺烧生物质气的比例增加,炉膛出口的NOx体积分数呈现增加的趋势,主要原因是富氧氛围下燃烧,其温度比空气氛围下燃烧的温度要高,当掺烧了生物质气后,在高温环境下生物质气燃烧产生了大量的快速型NOx,而导致炉内整体的NOx含量上升 [28] 。当掺烧比例在10%~35%,炉膛出口的NOx浓度变化不大,因此,
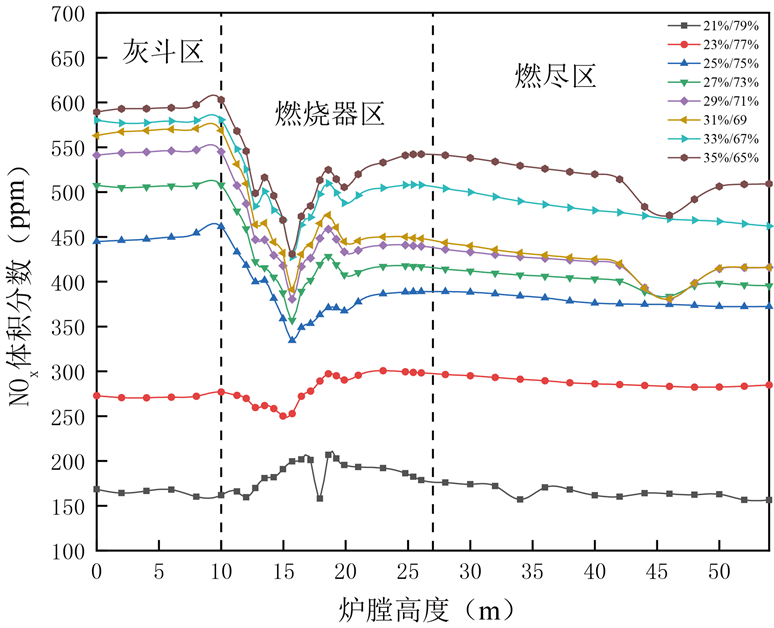
Figure 9. The distribution of the average NOx volume fraction of the cross-section along the height of the furnace
图9. 沿炉膛高度方向截面平均NOx体积分数分布
为了更大规模地利用生物质,缓解能源短缺压力,可以稍微提高掺烧比例,对炉膛出口污染物的排放影响不大。
4.5. NOx与CO2协同排放分析
图10炉膛出口NOx与CO2体积分数。从图中可以看出随着掺烧比例的增加,炉膛出口的NOx浓度呈现逐渐增大的趋势,而CO2浓度变化则相反。这表明在掺烧不同比例的生物质气下,炉膛出口的NOx与CO2体积分数有负向协同的趋势。在保证捕集CO2所需能耗较低的同时也应控制好锅炉燃烧产生的NOx污染物,因此,在富氧下,向四角切圆煤粉燃烧锅炉中掺烧生物质气的比例最好为20%,此时炉膛出口的CO2体积分数为80.9%,NOx浓度为396 ppm,当生物质气掺烧比例低于20%时,对生物质气的利用较低,不能更大范围地使用生物质能,当掺烧比例大于20%时,炉膛出口过低的CO2浓度不利于CO2捕集,过高的NOx浓度增加了污染处理的费用。
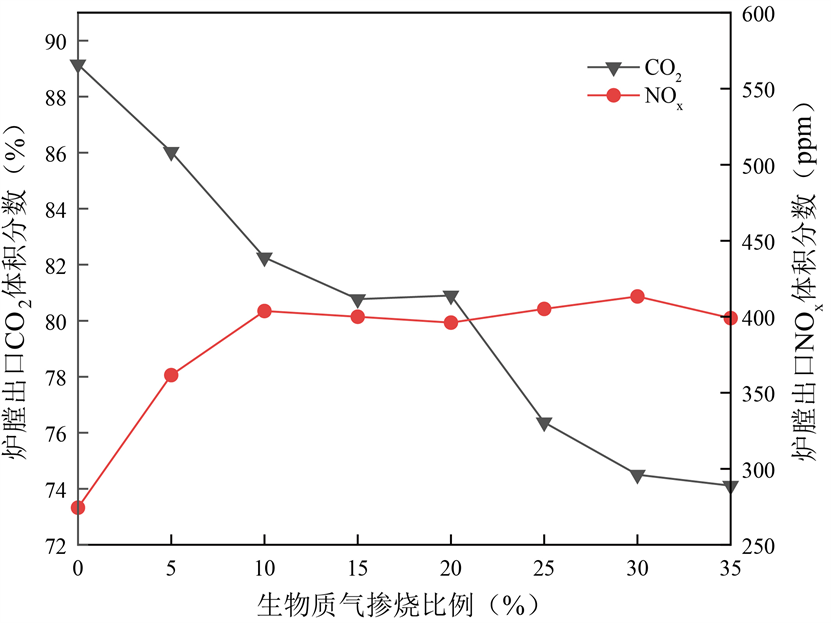
Figure 10. NOx and CO2 volume fraction at the furnace exit
图10. 炉膛出口NOx与CO2体积分数
5. 结论
本文以某350 WM亚临界参数四角切圆锅炉为研究对象,采用数值模拟研究了不同生物质气掺烧比对富氧下生物质气与煤粉混燃的NOx与CO2协同控制的影响,分别分析了各工况下炉膛温度分布、O2浓度分布、CO2与NOx生成特点以及炉膛出口NOx与CO2协同控制规律,得出结论如下:
1) 燃煤锅炉掺烧生物质气后,煤粉与生物质气燃烧均能形成良好切圆,且火焰分布均匀,表明,掺烧生物质气后不影响燃煤锅炉燃烧过程。
2) 随着掺烧生物质气比例的增大,炉膛出口的NOx与CO2体积分数有负向协同的趋势,表明,可以通过生物质气掺烧比来协同控制NOx与CO2的排放。
3) 当生物质掺烧比例为20%时,炉膛出口CO2体积分数为80.9%,NOx体积分数为396 ppm,此时生物质能的利用、CO2捕集及NOx污染物排放控制均能达到很好的协调。
本文研究成果可为实现燃煤电站锅炉的低氮燃烧与碳捕集提供技术理论支撑。
基金项目
国家自然科学基金重点项(51736007),国家重点研发计划项目课题(2021YFF0600604)。
参考文献
NOTES
*通讯作者。