1. 现状
针对某型航空发动机滑油压力传感器的检查维护,机务人员仅按维护规程进行外观检查和机上通电功能性检查,尚缺少明确的针对该型滑油压力传感器的计量检测标准规范,造成对判断传感器量值传递是否准确可靠缺少理论数据支撑。确定该型滑油压力传感器计量检测方法,填补标准体系的空白,可使机务人员开展传感器检测与排故工作更加科学、规范,对提升飞机质量和飞行安全具有重要意义。
2. 滑油压力传感器工作原理
滑油压力传感器采用单晶硅为基体,使用离子注入工艺和微机械加工工艺制造出的惠斯顿电桥,以及精密力学结构的硅敏感元件,在感受外界压力后,可实现所加压力与电流信号的线性转换,并可用激光修调厚膜电阻网络对敏感元件进行温度系数补偿。
传感器输入压力值x与输出电流值y的特性关系数学模型为
(x为输出电流值,单位mA;y为输入压力值,单位bar),压力测量范围为(0~10) bar,电流输出范围为(4~20) mA (见图1)。

Figure 1. Schematic diagram of the characteristic curve of the lubricating oil pressure sensor
图1. 滑油压力传感器特性曲线示意图
3. 确定滑油压力传感器的计量检测特性
3.1. 确定计量检测范围
滑油压力是表征发动机工作是否正常的重要技术指标之一。飞机维护规程中关于滑油压力值与发动机工作状态之间关系为:发动机规定滑油压力最低0.8 bar (转速低于3500 rpm)、最高7 bar,正常范围2 bar~5 bar。
传感器生产厂家提供的校验方法具体描述如下:在15 V供电条件下,使用压力校验仪依次设定表压压力值为2200 mbar、2000 mbar、1500 mbar、1000 mbar、500 mbar,使用万用表实时测量出电流值,将电流值换成压力值,其误差应满足不超过量程压力值的5%。
传感器生产厂家提供校验/检验范围为(0.5~2.2) bar,不能覆盖发动机正常工作规定的滑油压力值范围,以及产品原有的技术指标范围。根据GB/T 18806-2002《电阻应变式压力传感器总规范》中规定:“确定传感器性能特性的试验点应均匀分布在整个测量范围,其中应包括测量范围上、下限值或者接近范围上、下限(量程的10%以内)的点” [1] 。综上,为确保传感器整体性能可靠、准确,选择(0~10) bar作为滑油压力传感器检测范围。
3.2. 确定计量检测项目
通过查询国家现行有效的技术标准与规范,针对压力传感器的设计、试验、数据计算及检定方法均有相关标准。
GB/T 15478-2015《压力传感器性能试验方法》中静态试验项目主要包括:零点输出、满量程输出、非线性、迟滞、重复性、准确度、灵敏度等 [2] 。
GB/T 18459-2001《传感器主要静态性能指标计算方法》中压力传感器的静态校准特性包括:分辨力、灵敏度、回差、重复性、线性度、符合度、线性度加回差、不确定度、总不确定度、零点输出漂移、满量程输出漂移、热零点偏移等 [3] 。
综上,确定滑油压力传感器主要检验项目为预载检查、零点漂移、示值误差、迟滞误差。
3.3. 确定计量检测技术要求
参数为表压压力;量程为(0~10) bar;输出电流为(4.428~20.448) mA (见表1)。进行三次满量程压力加载,输出压力应该连续平稳,无跳变现象,记录实时数据。
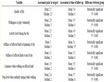
Table 1. Detailed Table of Indication Error and Hystereresis Error
表1. 示值误差与迟滞误差明细表
4. 确定滑油压力传感器的计量检测方法
4.1. 外观及附件检查
结合飞机维护规程有关内容及装备维修保障实际,确定滑油压力传感器的外观及附件检查应满足:滑油压力传感器的铭牌应完整、清晰,应具有出厂编号、型号规格、测量范围等信息;附带的技术文件中应完整说明产品名称、准确度等级、制造厂、额定工作电压(或电流)、输出信号、最大过载压力等信息;配套零部件应完好无损,外观不应有影响计量性能的锈蚀或损伤。各部件应装配牢固,不应有松动、脱焊或接触不良等现象。
4.2. 检测条件
根据《GB/T 15478-2015压力传感器性能试验方法》《GB/T 18459-2001传感器主要静态性能指标计算方法》等有关国家标准和规范,确定检测条件如下:
1) 检测设备的选择:整套检定设备检测引入的扩展不确定度U应不超过被检滑油压力传感器基本误差绝对值的1/2。
2) 环境条件:检测时的环境温度为(20 ± 5)℃。
3) 相对湿度:<80%。
4) 所处环境应没有影响压力传感器稳定输出的机械振动和外磁场。
4.3. 检测前准备工作
检测前,滑油压力传感器应在环境条件下放置2 h以上,方可进行检测。
将滑油压力传感器按要求与压力标准装置连接,对采用液体为传压介质的压力标准器,安装时应排除管路中的空气。压力传感器、激励电源、读数记录装置等仪器设备按规定连接方式连接,使其处于正常工作位置和状态。安装滑油压力传感器时,应尽量使传感器的感压面与压力标准器的参考平面在同一水平面上。检测系统正确安装连接后,至少需通电预热30 min。
4.4. 预载检查
对被检件加压至预压压力,稳定1 min后,缓慢通大气,连续进行3次。通过对被检件的三次满量程预载,可检查滑油压力传感器的内部结构是否工作正常,是否有泄露,输出信号是否平稳连续,是否有跳动现象,可将实时采集的数据以图形式显示并保存。
4.5. 零点漂移
即在规定的条件下和时间间隔内,零点输出值的变化量。
在规定的环境条件下,将滑油压力传感器通电预热及预压后,记录零点初始输出值
,每隔15 min记录一次零点输出值
(
),从开始记录起连续进行的时间不得少于1 h。
零点漂移:
式中:
为各零点输出值与初始零点输出值差值绝对值得最大值;
为满量程输出值。
在输入端没有输入信号的前提下,观察输出端的信号是否会出现缓慢变化或者上下波动的情况,在零点漂移严重的情况下,零点误差会影响、淹没有效信号,使放大电路不能正常工作。(产生该误差的原因有:环境温度变化、供电电压不稳定、运算放大器信号耦合电路故障等。)
4.6. 示值误差
即在计量器具指示的测量值与被检测量值的实际值之差。滑油压力传感器的准确度等级及基本误差/限应符合表2规定。
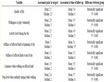
Table 2. Accuracy levels and basic error
表2. 准确度等级及基本误差
从测量下限点依次加压到测量上限点,然后再一次降压到测量下限点,完成正行程、反行程的一次测量流程,并计算每个测量点的示值误差,与滑油压力传感器的最大允许误差进行比较可判断传感器的测量性能是否正常。
4.7. 迟滞误差
即回程误差,对同一测量点的正行程与反行程输出信号的差值。
计算各检测点中,同一检测点正行程输出值的算术平均值与反行程输出值的算术平均值之差:
(
)。
传感器的线性:
其中:
为差值
中绝对值的最大值。
迟滞误差主要由压力传感器敏感元器件的物理性能或者机械部件的缺陷造成的,如传动机构的间隙、轴承的摩擦、弹性敏感元器件的弹性滞后等。
5. 检测记录格式(见表3)
参考国家和军用有关计量检定规程原始数据记录格式,结合已确定的滑油压力传感器计量检测项目,确定检测记录格式如下:
6. 检测结果处理
参考国家标准和军用标准相关计量规程,如其计量性能和通用技术要求符合规定的为合格,出具检测报告;如某一项不符合规定的为不合格,出具检测结果通知书,并注明不符合项 [4] 。
7. 检测周期
参考国家标准和军用标准相关计量规程,确定检测周期一般不超过一年。对于周期稳定性不合格的滑油压力传感器,检测周期一般不超过半年 [4] 。
8. 结论
按JJFL002-2010《国家计量检定规程编写规则》和GJB 1317A-2006《军用检定规程和校准规程编写通用要求》,结合滑油压力传感器工作原理,研究确定了滑油压力传感器计量检测范围、检测项目、检测技术要求等计量检测特性和检测方法,规范确定了检测记录格式和检测周期等,为机务人员和计量检定人员开展传感器的计量检测提供了理论依据,填补了技术规范体系上的空白,对于保证传感器量值传递准确可靠,提高飞机维修质效和飞行安全奠定了技术基础。
NOTES
*通讯作者。