1. 研究现状
随着“双碳”的实施,风能和太阳能等新型可再生能源的开发和应用取得了进步 [1] [2] 。中国2022年新增光伏并网装机容量87.41 GW,但风电和光伏发电还存在“弃风”和“弃光”现象,这严重的浪费了电力资源 [3] [4] ,故采用具备储能技术的先进电力系统 [5] [6] 。在大规模储能电站热仿真模型发展过程中,Bernardi等提出了锂离子电池热平衡原理及计算方法,后续研究如Thomas等对其进行简化,Wang等建立了电池热模型 [7] ,Rizk等将不可逆热视为由定电阻引起的产热 [8] 。杨勇证明了考虑电池产热率随温度以及电池荷电状态变化的仿真方法能有效提高热模型温度估计的准确度 [9] ,Zhao等探究了电池热平衡与充放电倍率、内阻、活性粒子大小及电极厚度等因素的关系。Li等建立了三维电化学–热模型描述磷酸铁锂电池的电化学反应,Du等基于有限元理论建立了电池内部产热三维模型。Zhao等设计了多集流片的电池结构以减少电子传输损耗,提高能量密度。电热耦合模型通过电流守恒建立电模型,可用于计算产热率分布。Kwon等提出了基于电流守恒的电池电极电位计算方法,Kim等建立了层叠式锂离子电池的电热耦合模型。吴彬等建立了二维电模型计算电池的电流和产热功率,并提出了一种极耳优化结构。
2. 储能锂离子电池热电应力对产热影响规律
探究磷酸铁锂电池的老化特性,研究老化对产热的影响,寻找电池老化后正负电极的极化热、反应热、欧姆热变化规律,以及老化后电池的温升变化规律。同时,研究不同充电以及放电倍率下电池的老化程度和产热、温升变化规律,以及不同环境温度对电池老化程度和产热规律的影响。
2.1. 电池热物性参数测试
2.1.1. 电池熵热系数及OCV~SOC曲线测试
熵系数用于电池充放电过程中的反应热计算。基于反应热计算公式(1),本文通过测试不同温度下SOC-OCV曲线,并根据OCV随温度变化拟合,获得不同SOC状态下的熵系数,测试过程如图1所示。
(1)
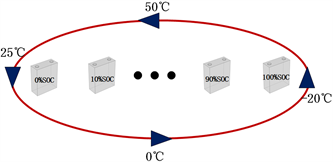
Figure 1. Entropy coefficient testing process
图1. 熵系数测试过程
在恒温箱中测试不同SOC状态下的电池,恒温箱温度依次设置为50℃、25℃、0℃、−20℃和25℃。在每一个温度条件下充分搁置后获取OCV变化数据,根据OCV和温度数据计算熵系数。
2.1.2. 电池比热容测试
用28 W加热板在绝热环境加热电池,假设热量全被吸收,测量电池温度,用Origin软件进行温度与时间的线性拟合,计算电池的比热容c。
2.2. 电池性能测试
2.2.1. 不同工况下电池充放电性能测试
对容量为280 Ah电池在不同温度下(−20℃,0℃,10℃,25℃,45℃)和不同倍率下(0.5 C, 0.25 C)进行恒流恒压充电和恒流放电实验。
2.2.2. 不同工况下电池内阻测试
在25℃的实验室环境内,分别以0.5 C和0.25 C的倍率对电池进行HPPC (Hybrid Pulse Power Characteristic)测试,测试过程分为充电和放电两个阶段。根据公式(2)、(3)和(4)获取不同SOC (State of Charge)下的充放电内阻。以5% SOC为一次测试步长,依次测取0.25 C和0.5 C倍率下电池的充放电内阻测试。
(2)
(3)
(4)
2.2.3. 不同工况下电池循环性能测试
在25℃实验室环境下,对50.5 Ah#3电池以1 C倍率、50.5 Ah#5电池以2C倍率、50.5 Ah#3电池以0.5 C倍率和282 Ah#6电池以0.5 P倍率进行充放电循环,设置老化循环的SOC区间为10%~90%。实验结果如表1所示。
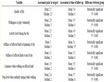
Table 1. Results of cyclic aging experiments
表1. 循环老化实验结果
3. 储能电池电热耦合模型构建
构建该锂离子电池的电热耦合模型。在构建模型过程中,应考虑电荷守恒,对电池内集流体上的电势分布进行求解,并进一步求解极板间的电流分布。此外,还应根据电流分布计算电池的产热率分布。最后,依据产热率分布计算电池的温度,并将其与试验数据进行对比,以验证模型的温度预测能力。
3.1. 电池电热仿真及有效性验证
3.1.1. 锂离子电池产热模型
锂电池在充放电过程中会产生热量,主要由于内部化学反应、物质消耗与生成以及内阻的存在。电池的产热量遵循Bernardi电池产热方程,等式右边依次为焦耳热(不可逆热)、反应热(充电过程的可逆热)、混合热和相变潜热。在实际计算中,混合热和相变潜热可忽略,因此产热功率的计算公式可以简化为公式(6)的形式。
(5)
(6)
在实际充放电过程中,电池的开路电压无法实时测量,为方便计算,焦耳热部分常用电池内阻产热代替计算,因此公式(6)可以进一步等效为公式(7)。
(7)
电池充电过程中的工作温度受到产热功率、比热容、散热环境、电动势和内阻的影响。这些因素通过公式(8)热平衡方程来决定温度变化。在充电过程中,产生的热能一部分存储在电池内部,另一部分由散热功率决定。
(8)
电池的正极极耳材料为铝,负极极耳材料为铜。在电池充电过程中,正负极耳产生的热量为焦耳热,其产热源计算公式如(9)所示:
(9)
3.1.2. 锂离子电池传热模型
锂电池的正常充电工作温度为0℃、−45℃,放电工作温度为−20℃、−60℃。本文所采用的电池为平液设计,电池内部的电解液基本不流动。因此,锂离子电池传热模型只考虑内部热传导。根据固体传热理论,电池内部的温度分布满足如公式(10)所示的固体传热基本方程。
(10)
其中温度的初始条件如公式(11)所示。
(11)
电池传热模型的三类边界条件如公式(12)所示。其中第一类边界条件包括电池间传热和对液冷板散热;第二类边界条件为与外部环境的对流换热;第三类边界条件为对外部环境的热辐射。
(12)
3.2. 模型有效性验证
在实验部分参数测量以及上述产热和传热模型建立的基础上,设计电池倍率充电产热实验,从而验证所建立模型以及所测参数的准确性,为后续仿真提供依据。所设计实验过程如图2所示,步骤如下:
1. 布置热电偶,连接数据采集器,热电偶的布置位置如图3所示;
2. 电池连接充放电机,放入25℃温箱静置3小时。
3. 设置充放电机工步,对电池进行0.25 C和0.5 C倍率充电。
4. 建立电池3D产热模型,导入实验参数进行仿真。
5. 对比实验与仿真数据,误差≤ 2℃,满足指标。
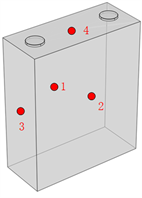
Figure 3. Schematic diagram of thermocouple arrangement
图3. 热电偶布置示意图
3.3. 仿真结果准确性验证
为验证仿真结果的准确性,本文采用仿真网格的细化,即将仿真网格精细一倍,所得结果并未发生变化。
4. 集装箱式储能电池系统建模与热管理系统设计
建立集装箱整体物理模型,分析传热流动仿真方法和数学模型。基于有限元仿真方法对电池箱进行数值模拟,获得电池箱流动和传热规律。在此基础之上,分析影响因素并优化,获得满足要求的电池箱热管理方案。
4.1. 液冷模型
液冷电池模组由24块单体电池组成6 × 4结构,连接结构为1P24S。液冷模型计算成本低,通过加装底部冷板给电池组换热,冷板尺寸为764.8 × 522 × 20 mm,冷板内存在10 mm粗流道。单体电池间距为10 mm,电池模块放置于冷板正中央。汇流排采用铝制结构连接电池的两个极耳。横向汇流排尺寸为58 × 108 × 2 mm,纵向汇流排尺寸为72 × 89 × 2 mm。
冷板的主要功能有两方面:保护电池模组和作为支撑结构。此外,冷板与电池模组接触,增大接触面积,使热量有效传递到沟道内的液体介质。目前铝制材料是主要选择,成本低且导热能力满足需求。搭配水作为冷却剂,冷板和水的物理参数如表2所示。
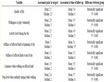
Table 2. Parameters of the physical properties of the liquid cold plate and the coolant
表2. 液冷板与冷却液物理属性参数
液冷系统运行时,水作为冷却剂从入口通过冷板与电池换热,热量带离系统。模型初始流速为0.6 m/s,雷诺数约3000,采用k-w湍流模型。同时,电池与外部环境自然对流换热,换热系数为10。模型初始温度、外部环境温度和冷却液流入温度均为25℃。
4.2. 液冷方案
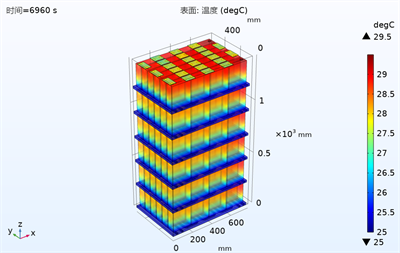
Figure 4. Temperature distribution at the end of 0.5 C rate discharge of liquid-cooled module of large-scale energy storagebattery cabinet
图4. 大规模储能电池柜液冷模组0.5 C倍率放电结束温度分布
在蛇形沟道实际应用中,随着冷板内部嵌入蛇形沟道的长度逐渐增加,冷却液温度增加,出口位置换热效率降低,电池模组温差大。为解决此问题,设计了双蛇形流道,冷板两侧分别设置入水口,入水口流速为1.0 m/s,经测试可显著降低电池模组的温差。
对液冷模组进行网格剖分与0.5 C倍率放电的温度仿真,如图4所示。底部到顶部温度逐渐升高,这是因为只在底部加装冷板,冷却效果差。但冷板导热能力强,0.5 C倍率下电池产热量不多,所以液冷电池模块最高温度29.4℃,温差4.4℃,满足热管理要求。
对该液冷模组进行阵列来模拟大规模锂离子储能电池系统的一个储能电池柜的情况,将液冷模组以相同条件进行仿真之后对该储能电池柜液冷模组模型进行了网格剖分与0.5 C倍率放电的温度仿真。储能电池柜液冷模组模型的最高温度被控制在29.8℃电池温差被控制在4.8℃以内,满足热管理要求。
5. 结语
本文针对锂电储能系统的研究过程,完成280 Ah功率型锂电池的热特性测试,包括熵系数,内阻不同环境以及不同倍率下电池充放电时的温度测试,以及完成280 Ah电池循环老化实验。最后对大容量锂离子电池的产热及传热模型进行仿真和验证,以时变热源输入,分析电池不同工况运行下的产热情况,并根据相应特点设计了液冷电池模组。此外,本文还将以集装箱储能系统作为研究对象,开展热管理系统优化研究,以抑制电池最高温度和最大温差作为目标。这将有助于推进电池热管理技术的发展,并促进电池在储能系统中的应用。本文的创新点在于综合考虑电池的产热特性和环境因素,建立电热耦合模型,并将其应用于储能系统的热管理中,为提高储能系统的能效和实用性提供新思路和解决方案。
项目
国家级大学生创新创业训练计划项目:大规模储能电站热仿真模型构建,项目编号:202210214142。
参考文献