1. 引言
光学材料熔石英玻璃因具备高透过率和低散射的特性,被高功率激光系统中被广泛使用,如美国国家NIF点火工程、菲涅尔透镜以及太空望远镜等重要项目均选用熔石英玻璃作为关键材料。光学元器件材料的加工工艺通常包括磨削、研磨和抛光等步骤,其中抛光工艺被视为最为关键的一环,直接影响元器件的最终表面质量。然而,目前在精密抛光加工工序中仍存在抛光效率不高、面形精度较差以及去除速率较慢等问题 [1] [2] 。
为改善磁流体(Magnetic fluid, MF)颗粒分散性好但因粘度较低导致抛光力较弱和磁流变液(Magnetorheological fluid, MRF)虽具有较强的粘度,但分散性较差特性的缺点 [3] ,Shimada首次提出了磁性复合流体MCF,将微米级羰基铁粉、磨粒、α-纤维素等与含有纳米级磁性微粒子的MF混合而成,使得MCF同时具有两种材料的优点 [4] ,在永磁铁的作用下,磁性粒子分散稳定并形成具有黏性的Bingham的抛光头,可以产生较大的抛光应力,实现材料的快速去除,并获得光滑无损伤的加工表面。磁性复合流体抛光(Magnetic compound fluid, MCF)相比其他能量场辅助加工的方法,具有成本低、装置简单、使用范围广等优点,能在实现高效率抛光熔石英元件的同时并获得较高的表面质量。
近年来,国内外学者对MCF抛光展开了丰富的研究。焦黎等 [5] 研究了卧式MCF抛光中,空间磁场分布对熔石英元器件材料去除特性的影响,建立了磁场分布的解析表达式并验证了改变磁极分布方式对熔融石英玻璃材料去除率的影响;Guo等人 [6] 通过对立式MCF抛光过程中抛光间隙、磁铁转速和MCF浆料载体转速工艺参数的研究,通过分析抛光区域的应力分布,确定了抛光过程中抛光应力与材料去除率之间的数学模型。林龙侨等 [7] 针对磁辅助抛光(MCF)过程,在不同的主轴转速、加工间隙、抛光时间和抛光路径条件下进行了深入研究,以探索微结构材料去除特性和保形情况的变化规律,并确定了最佳的抛光工艺参数。魏久翔等 [8] 开展了微沟槽MCF抛光和UMCF抛光工艺参数研究,结果表明:引入超声振动可有效改善微槽底部的抛光表面质量,并获得了不同参数下表面形貌、粗糙度和去除率的变化规律。上述的研究,从试验和理论分析上探究了磁辅助抛光技术在光学元件制造和应用方面等难题,推动了MCF抛光技术的快速发展。
为探究磁辅助抛光间隙对抛光元件特性的影响,本文以熔石英玻璃为加工对象,结合实验和理论分析,研究了磁性复合流体抛光间隙对MCF抛光特性,如抛光深度、抛光斑空间几何形貌、表面粗糙度和紫外光透过率的影响规律,揭示了抛光材料去除机理,明确MCF抛光可实现对熔石英玻璃抛光体积的高效去除并能获得光洁的表面,为后期采用MCF抛光工艺提供相应参考,为实际应用加工提供参考和指导。
2. 试验
2.1. 磁辅助抛光原理与设备
本实验采用自行搭建的卧式抛光机床对熔石英玻璃进行磁性辅助抛光。如图1所示,该设备由水平主轴驱动、磁通密度为0.4 T 的环形磁铁以nt 的转速进行回转运动,形成空间磁场。抛光轮由环形铷铁硼磁铁和左右两侧的挡板组成,环形磁铁和挡块具有相同的外径40 mm和内径25 mm,厚度分别为8 mm和4 mm,并将抛光轮下方与工件之间的距离定义为抛光间隙
,具体抛光参数见表1。
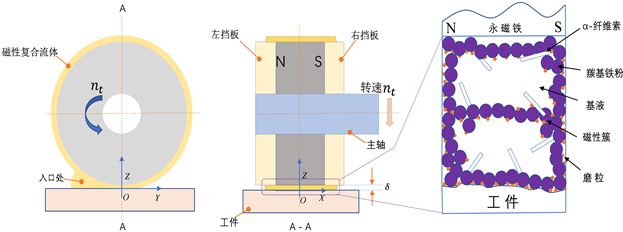
Figure 1. Polishing structure and polishing schematic diagram
图1. 抛光结构示意及抛光原理图
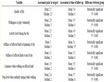
Table 1. Polishing test parameters table
表1. 抛光试验参数表
图1所示为磁性微粒链化过程的示意图。在没有外部磁场作用时,磁性微粒分散无序。当外部磁场加入后,磁力将推动微粒按照磁力线逐渐定向排列,形成磁偶极子,并逐渐连接形成链状结构。随着外部磁场强度的不断提高,微粒链状结构进一步形成柱状或复杂的团簇结构。当外部磁场移除后,微粒将恢复到最初的无序分布状态。MCF抛光依靠正压力和剪切力的共同作用实现工件的材料去除。在外部磁场的作用下,MCF会附着在抛光轮上并形成具有剪切力的粘弹塑性Bingham流体,其中非磁性磨粒均匀分布于磁性簇表面。在抛光过程中,磁性簇对工件表面产生挤压、摩擦和剪切作用,使MCF与工件表面间的磨粒受到不同的作用力,并在工件表面产生微小的挤压变形,去除工件表面的不平整部分。同时,磁性簇的剪切力和摩擦阻力促进了抛光过程中的磨料在工件表面上的移动,在表面产生摩擦和磨损,最终形成光洁的表面。
2.2. 样品制备
本实验以40 mm × 40 mm × 10 mm的熔石英玻璃作为加工对象,工件在抛光前经过W5~W10碳化硅双面研磨,初始表面粗糙度Ra为0.65~0.85 μm,其亚表面裂纹在4.5 μm以内,抛光液由磁性颗粒(主要成分为7.5 μm铁粉和10 nm Fe3O4)、非磁性磨粒(1 μm氧化铈)、
-纤维素和等离子水按照62:10:3:25的质量比例配置而成,其中磁性颗粒中铁粉和Fe3O4质量比为21:10,抛光前,先对元器件进行研磨预处理,以达到表面光滑、无明显缺陷的效果。首先调整机床X轴和Y轴,将工件待加工区域放置于抛光轮中心位置正下方,再下调Z轴使得抛光间隙
分别为0.5、1.0、1.5和2.0 mm,确定好位置后,开启装置进行抛光。然后,使用微量滴管向环形磁铁的圆周表面均匀滴入5~10 g的抛光液来进行定点抛光,本实验中使用的元器件,将它们各自划分为4个区域:0.5 mm、1.0 mm、1.5 mm和2.0 mm,抛光完成后,对每个抛光斑的轮廓形貌、表面粗糙度和紫外光透过率进行测试。
2.3. 表面轮廓、粗糙度检测和透过率检测
使用Taylor Surf i200表面轮廓仪对抛光斑截面轮廓进行检测。将探针按照图1所示的抛光斑X向和Y向,进行采样测试,为了确保获取到抛光斑的准确轮廓,在两个方向上采集两条以上的轮廓数据。使用三丰SJ-210表面粗糙度测量仪对元件进行表面粗糙度检测,并设定采样的长度为2 mm。在研磨的表面(抛光时间为0 min)进行采样,并记录元件的原始粗糙度值,在各抛光内测量3~5组数据,并将其平均值定义为该抛光斑的粗糙度结果。采用LS-108H透过率仪器检测元件的紫外光透过率,测试光斑直径约为1 mm,各待测表面均测试4个点,并将其平均值定义为透过率测量结果。
3. 试验结果
3.1. 抛光斑形貌
使用表面轮廓仪沿抛光斑X向和Y向进行表面轮廓检测,抛光斑的尺寸如下表2所示。图2所示为抛光斑的截面轮廓,平行于抛光轮轴向的X方向上,抛光轮与被抛光表面的相对速度较大,因此抛光斑的截面呈“W形,中间位置的深度最浅;在垂直于抛光轮轴向的Y向上,抛光轮与被抛光表面的相对速度较小,因此抛光斑的截面呈“V”型,两侧位置的深度较浅,表明材料去除量较少。在MCF抛光过程中,抛光斑的X向和Y向尺寸由抛光间隙
时的1.52 mm、1.24 mm分别提升到抛光间隙
时的3.26 mm和2.35 mm,抛光深度也随着抛光间隙的减小在不断加深,最大深度MRdmax从
的2.02 μm提升到
的6.15 μm,同时间MCF抛光下是前者最大深度的3.05倍。当抛光间隙减小时,抛光斑的最大深度在逐渐向抛光轮的两侧移动,基本呈现对称的形状。
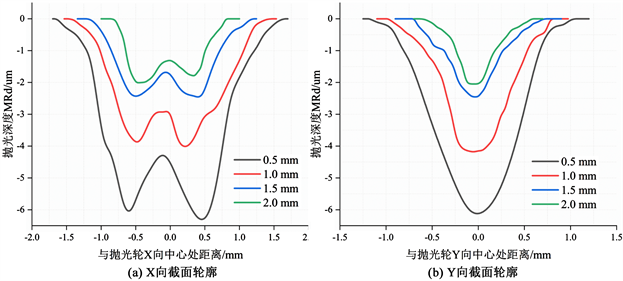
Figure 2. The polishing section profile changes with time
图2. 抛光截面轮廓随时间变化
3.2. 材料去除率
为确定各抛光斑的材料体积去除情况,利用抛光斑X向与Y向截面轮廓,并结合三维仿真软件对抛光斑三维模型重构与体积分析。抛光间隙
时抛光斑的三维几何形态如图3所示,计算可得材料去除体积为7.68 × 10−6 mm3。基于同样的方法计算出其余3个抛光斑的体积去除量MRv,分别为2.31 × 10−6 mm3 (
)、1.05 × 10−6 mm3 (
)和0.52 × 10−6 mm3 (
),结果见表2,
的抛光体积去除是
时的材料去除体积的14.78倍,减小抛光间隙可以使得抛光去除体积增大。
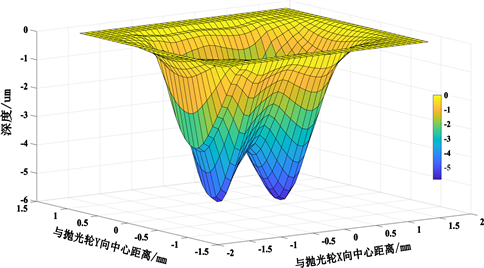
Figure 3. Reconstruction of polishing spot 3D model
图3. 抛光斑三维模型重构
为进一步探究磁性复合流体抛光材料去除速率的特性,将抛光最大深度MRdmax与抛光时间的t的比值定义为材料最大深度去除效率MRRdmax,即MRRdmax = MRdmax/t,图4为不同抛光间隙下所对应材料最大深度去除效率MRRdmax:当抛光间隙
时MRRdmax最大,可达到1230 nm/min,随着抛光间隙的增大,材料去除率呈现快速下降的趋势,当抛光间隙
时,MRRdmax = 40.4 nm/min,加大抛光间隙不利于材料去除率的保持,因此,选择合适的抛光间隙是十分重要的。
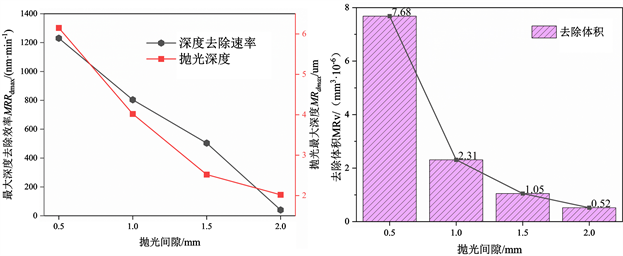
Figure 4. Variation of polishing depth with polishing gap
图4. 抛光深度随抛光间隙的变化规律
3.3. 表面粗糙度和透过率
初始熔石英表面经过研磨预处理,研磨表面的大量机械缺陷使其粗糙度Ra约为0.80 μm。使用金相显微镜(M230-21BLC, 100×)观察不同抛光间隙下的熔石英微观表面形貌,结果如图5所示,元件表面机械缺陷随抛光间隙的减小逐渐减少,表面粗糙度显著下降。当抛光间隙
时,工件表面会出现一定的机械缺陷和材料残留,当抛光时间保持不变时,随着抛光间隙的减小,元件表面的机械残留逐渐被清除,表面粗糙度提升显著,当抛光间隙
为0.5 mm时,粗糙度下降率ROD分别为89.37%,随着抛光间隙的减小,粗糙度下降率呈现快速下降的趋势,但下降率ROD仍保持在53%以上,如图6所示,则表明MCF抛光可以实现材料表面微观形貌的快速提升,磁辅助抛光为无损抛光加工,所以采用MCF抛光不会对抛光元件引入新的损伤,可以实现理论上的光学材料超光滑表面的结果。
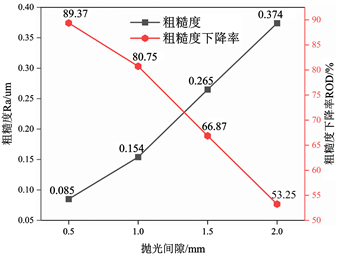
Figure 6. Roughness and polishing clearance diagram
图6. 粗糙度与抛光间隙示意图
抛光熔石英元件的紫外光透过率如表2所示,未抛光元件的初始透过率仅为24.25% ± 2.5%。图7表明元件透过率和粗糙度二者呈现较为显著的线性关系,当抛光间隙
时和
紫外光透过率分别提升至46.58% ± 1.2%、43.12% ± 1.05%,分析可知,透过率基本随抛光间隙的减小呈现上升趋势,拟合度曲线R2 = 99.98%,因本实验中仅对熔石英进行单面抛光,未抛光的一面仍为粗糙研磨表面,因此,元件透过率不超过50%,由于透光率和粗糙度都受表面机械缺陷影响,所以较低的表面粗糙度意味着元件能达到较高的透光率。
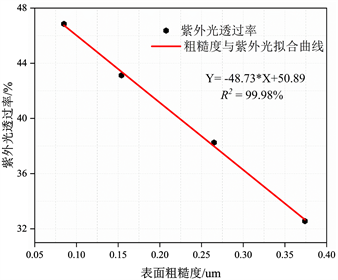
Figure 7. Curve of the relationship between UV light transmittance and surface roughness
图7. 紫外光透过率与表面粗糙度关系曲线
4. 分析与讨论
4.1. 抛光间隙与磁感应强度
磁性复合流体抛光液在磁极形成的高梯度磁场作用下,形成具有粘塑性的Bingham流体的柔性缎带,实现对光学元件等加工工件表面的高精度材料去除。在磁性复合流体抛光中,磁性颗粒在磁场作用下形成磁簇,再将抛光磨粒挤压到待抛光元器件表面,利用磨粒对元件的作用力实现材料去除。根据Preston方程 [9] 可知,材料的去除率与抛光轮转速及抛光轮与元件之间的压力等参数有关,材料去除率公式如下:
(1)
式中,K表示Preston函数系数,当选取特殊的工艺参数时K一般为常数;P表示加工工件表面抛光区域所承受的正压力;V表示加工工件表面与抛光区域内抛光液的相对速度,本试验中取V = 300 r/min。
在MCF抛光中,抛光轮上的磨粒在磁场力的作用下向元件表面挤压,通过对非磁性磨粒的向下挤压实现材料的去除,所以,MCF抛光元件的材料去除量受到抛光液的磁化压力Pm的影响,其中Pm的求解如下:
(2)
式中,
为磁流体抛光液中磁性微粒的体积之比,
表示真空中的磁导率,
表示磁流变抛光液中磁性微粒,H表示工件表面外加磁场的强度。
其中,磁场强度H与磁通密度B之间存在下面的关系:
(3)
式中,x 是磁性微粒的磁化系数。由上述(2),(3)式可知,磁场强度和磁通密度直接影响抛光液磁化压力Pm并对抛光去除直接关联。
为探究MCF抛光的材料去除机理和抛光斑形貌的形成过程,使用有限元方法对永磁铁表面不同位置处的磁场强度进行仿真分析。如图8(a)所示为平行于磁铁回转轴心的距离为1.0 mm的红色直线,并对直
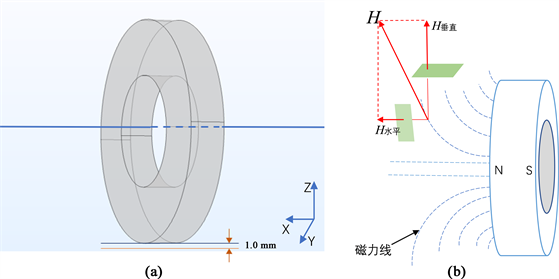
Figure 8. Schematic diagram of the magnetic field analysis. (a) Magnetic field position diagram; (b) Magnetic field strength measurement diagram
图8. 磁场分析示意图。(a) 磁场位置示意图;(b) 磁场强度测量示意图
线按照图8(b)进行垂直分量与水平分量的磁感应强度分析,总磁场强度与磁铁水平分量和垂直分量见公式(4)。
(4)
仿真参数如下:铷铁硼的磁铁外径为40 mm、内径为25 mm、宽度为8 mm,剩余磁通密度为0.4 T,抛光间隙
、1.0、1.5和2.0 mm。并利用手持高斯计(天恒TD8260)在不同间隙下的环形磁铁回转轴心的直线上进行磁通密度测量(0 mm、±2 mm、±4 mm、±6 mm、±8 mm、±10 mm),且每个位置各测量5次,并将其平均值定义为该位置磁感应强度的测量结果。图9为永磁铁垂直方向和水平方向实际测量的磁场强度值,同时利用公式(4)对其进行计算总磁场的强度。
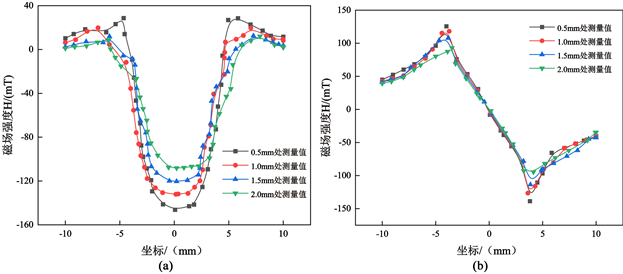
Figure 9. Magnetic field density distribution. (a) Horizontal measurement; (b) Vertical measurement
图9. 磁场密度分布。(a) 水平方向测量值;(b) 垂直方向测量值
图10为抛光间隙
时的磁通密度分布示意图,在水平方向上,磁感应强度垂直于表面,磁感应强度在抛光轮的中心位置(x = 0 mm位置处)为零,在靠近磁铁左右端面时逐渐增强,在距离0位置约±5 mm处达到最大值约为11 0mT。在垂直方向,垂直于回转轴心,在x = 0 mm位置处,磁感应强度最大,约为143 mT,并沿着X方向两侧逐渐减小。总磁感应强度呈现倒置的“W”形,即在0位置较小,在靠近磁铁两侧端面时逐渐增强,在端面的边缘附近达到最大值,远离端面后,磁感应强度迅速减小。其中,仿真示意图和实测图基本呈一致的趋势,磁场分布规律为:磁铁中间位置处磁感应强度略小,沿着磁铁两端逐渐增强,并在端面处能达到最大值,当抛光间隙
为0.5 mm、1.0 mm、1.5 mm和2.0 mm时,其最大的磁感应强度值为分别为158.25 mT、143.64 mT、126.31 mT和110.15 mT。当离开磁铁表面后,磁通密度H向外的衰减速度急速增加,因此,选择合适的抛光间隙对MCF抛光加工是极其重要的。
4.2. 材料去除率分析
磁场分布的强弱对抛光磨粒(CeO2)在形成磁性簇过程中的作用十分重要,磁感应强度越大,MCF形成的抛光链(磁性簇)也就越稳定。因为强磁场会增加抛光头上吸附的磨粒数量,提高作用于元件表面的有效磨粒数量,同时使得单颗磨粒对元件的切削作用力增强。因此,磁场空间分布规律直接决定着抛光头对元件作用力的大小,并影响材料去除量和最终的抛光斑形貌。
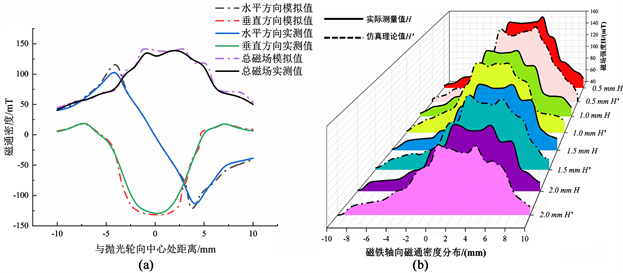
Figure 10. Distribution of magnetic fields at different gaps. (a) 1.0 mm polishing gap; (b) Magnetic flux density at different polishing gaps
图10. 不同间隙磁场分布示意。(a) 抛光间隙1.0 mm元件表面磁通密度分布;(b) 不同抛光间隙下磁通密度仿真值和实测值
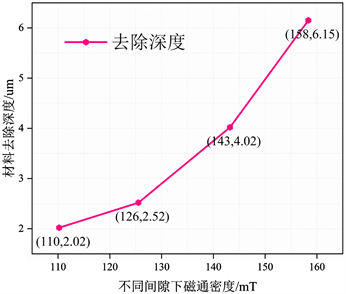
Figure 11. Magnetic flux density curve relationship with the depth of material removal
图11. 磁通密度与材料去除深度的关系曲线
图11为4个不同抛光间隙下最大抛光斑深度与最大磁通密度的关系曲线,结果表明,当抛光时间保持不变时,材料的去除深度随着磁通密度的增加而显著增加。因此,抛光斑表面形貌的形成与磁场分布规律及抛光加工间隙有关,当抛光间隙
为0.5 mm时,抛光轮边缘磁通密度越高处对应材料去除量越大,而抛光轮中部磁场最弱处材料去除量则最低,因此会形成“W”形抛光斑。随着抛光间隙的减小和抛光斑表面长宽尺度增加,材料去除深度最大位置将逐渐向磁通密度最强的磁铁端面靠近。
5. 结论
采用磁辅助抛光技术对熔石英玻璃进行了定点抛光加工,研究了不同抛光间隙下MCF抛光,并对抛光斑轮廓进行了三维形貌重构及去除体积求解、粗糙度、透过率测试等,结合理论分析和实验测试分析永磁铁磁通密度的分布,通过本文的研究可得到以下结论:
(1) 抛光斑沿着平行于抛光轮的轴向方向和纵向方向截面轮廓分别呈现出“W”和“V”形,相同抛光时间下,减小抛光间隙,UMCF抛光能获得的更大的抛光斑长度、宽度及抛光深度;
(2) 在本实验的条件下,材料抛光深度去除效率在抛光5 min、抛光间隙
为0.5 mm时,最大可达最大1230 nm/min,增大抛光间隙使得材料去除效率有所下降;
(3) 空间磁场的分布会直接影响材料去除量,且材料去除深度还受到抛光间隙的影响。建立了材料深度去除量与磁通密度之间的关系曲线,发现抛光斑截面呈“W”形轮廓的形成与磁通密度分布规律有关。同时,随着抛光斑长宽尺度的增加,材料去除深度最大位置也会逐渐向磁通密度最强的磁铁端面靠近。