1. 引言
滑油泵作为航空发动机滑油系统的重要组成部件,主要用于发动机轴承和传动齿轮部分润滑油的输送和回收。由于泛摆线油泵具有结构紧凑、体积小、重量轻、填充性好、压力脉动小等特点。在经过国内外众多学者对其成型方式,工作特性及容积效率等方面研究的基础上。目前,我国和欧美一些发达国家的航空发动机上已经开始广泛应用泛摆线油泵。
提高泛摆线滑油泵的转速,可以减小转子的几何尺寸,使油泵的体积减小,在同样的转子配合间隙下,内转子转速的提高会因节流作用的加强而使泄漏减弱,有利于容积效率的提高[1] 。由于航空发动机滑油泵一般是由发动机主轴或附件机匣传动[2] ,提高转速,能有效减少变速结构重量,从而达到减轻发动机重量的效果。
研究结果表明在保证各种间隙不变的条件下,随着转速的增加,流量脉动也会显著增大。而泵的流量脉动和压力脉动,造成泵构建的振动产生噪声。转速增加对噪声的影响一般比压力增加还要大[3] 。在实际应用中发现,由流量脉动引起的压力脉动会产生较大冲击。有人通过设计一种储油槽,来降低摆线泵工作过程中产生的脉动,但是效果并不明显。工程应用中常采用在出口处添加稳压阀、定压阀的方式,在泵限压范围内随时根据泵内压力的高低来调节泵出油口处的空间大小,从而达到稳压的效果。通过实验发现,增加稳压阀后,泵的脉动频幅不及原来的1/3,从而大为降低了由此产生的噪声和振动[4] 。这样做无疑增加了发动机重量。
为推动航空发动机用泛摆线滑油泵向高转速化方向发展,降低流量脉动,本文拟开展流体结构耦合研究。分单级泵和多级泵分别对进、出油槽结构进行优化,并对其流量特性进行仿真分析,为以后航空滑油泵的设计提供依据。
2. 泛摆线泵流量特性计算
摆线泵受其结构影响,只能采用轴向进、出油方式。随着容积腔容积的不断变化,完成进油和排油工作。
摆线泵的瞬时流量是指某一时刻排出泵的液体体积,其计算公式为:
(1)
摆线泵的理论平均流量是指单位时间内排出泵的液体体积,其计算公式为:
(2)
式中:
——内转子齿数;
——内转子转速;
——齿厚;
——齿扫过最大面积。
摆线泵的流量脉动是由啮合点位置不断变化,导致工作容积不断变化引起的,其计算公式为:
(3)
本文分析中采用同一内、外转子,因此
不变。为了使数据更为简单、直接,将以:
表示流量脉动,反映脉动情况。
3. 单级泵结构对流量脉动率的影响分析
齿数z、创成系数k、弧径系数h是影响流量脉动的主要因素, [5] 其中随着齿数的增加,单位体积的排量减小,流量脉动呈减小趋势;而增大创成系数k,减小弧径系数h会使泵的流量脉动率减小,但是会增加泵的体积。简而言之,对泛摆线泵来说,在转子参数选择方面,为保证低流量脉动,必须以牺牲流量为代价。而内转子齿数为偶数时的脉动要比奇数时的小。本文则提出在进、出油槽结构方面进行优化,以求在保证正常流量的情况下,降低脉动。
传统的进、出油槽设计原则是在形成最大容积腔前,保证进、出油槽不沟通,以防止油液从高压区,通过各种配合间隙,泄漏到低压区,导致流量下降,容积效率降低。
这种油槽结构的密封区域边界一般是由形成最大容积腔和最小容积腔时的4个啮合点位置确定。如图1所示。
计算公式如下:
(4)
(5)
(6)
(7)
(8)
(9)
(10)
4. 单级泵结构优化
因为泵的工作腔从吸油腔突然与压油腔相通会产生流量和压力突变 [3] ,为了达到在保证体积不变,齿数不变的前提下,减小流量脉动的目的。本节根据高转速泵,转速高的特点,尝试在形成最大容积腔的瞬间沟通进、出油槽,利用惯性将油液从低压区带入高压区。并对不同密封面积,不同的进出油槽间距进行仿真分析。如图2中,(a)所示结构是在传统结构的基础上,增大进、出油面积,延长进、出油时间。(b)所示结构则是在(a)的基础上,在形成最大容积腔的瞬间,对进、出油槽进行沟通。
4.1. 控制方程及湍流模型建立及网格划分
针对摆线泵工作状态内部油液流动的实际情况,忽略油液温度变化,泵内部油液流动的控制方程为:
(11)
(12)
(13)
(14)
式中:
为密度;
为时间;
为速度矢量;
、
和
分别为速度矢量在x,y,z方向上的分量;
为动力粘度;
、
和
分别为作用在液体微团上的体积力。式(11)为流体运动的质量守恒方程,又称为连续性方程;式(12)、(13)、(14)为流体运动的动量守恒方程,又称为Navier-Stokes方程(N-S方程)。
摆线泵的内部流动比较复杂,多为湍流运动,其特征是在运动过程中液体质点具有不断的互相混掺的现象,速度、压力等物理量在空间和时间上均具有随机性质的脉动值。三维瞬态N-S方程,无论对层流还是湍流都适用;但对于湍流,如果直接求解,对计算机的内存和计算速度要求都极高,目前还不能在实际工程中应用。工程中,广泛应用k-ε模型对湍流进行模拟,可以取得与实际比较吻合的结果 [6] [7] 。
4.2.模型建立及网格划分
仿真计算域为摆线泵内部的油液流动区域。根据设计的泛摆线泵的几何尺寸,计算出与形成密封区域相关的啮合点坐标。在solidworks中建立泵的三维模型,反向抽壳出流体域,生成STL文件,如图3所示。
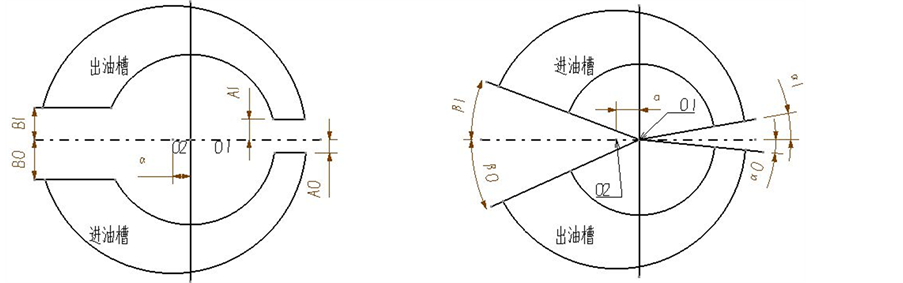
Figure 1. Two traditional cavities’ structure
图1. 两种传统油槽结构
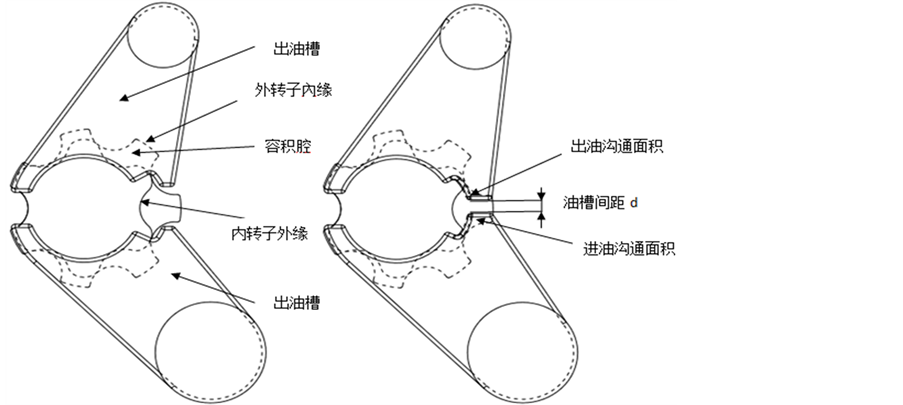
Figure 2. The fluid domain of improved pan-cycloid pump
图2. 改进型泛摆线泵流体域
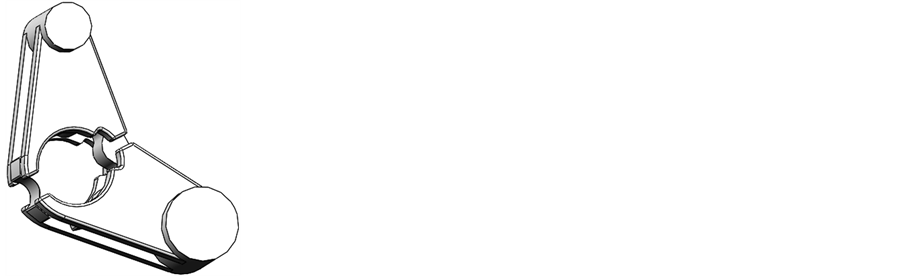
Figure 3. The fluid domain of single-stage pan-cycloid pump
图3. 单级泛摆线泵流体域
将生成的STL文件导入pumplinx,按区域划分,静止区域生成通用网格,旋转区域选择转子网格划分,生成动网格,连通MGI面后。共生成网格数:213327,节点数:895847,面元数:405965,如图4、图5所示。
在流动过程中由于齿轮的啮合以及飞行高度增加会造成局部的滑油气化成气态以及析出气体,因此,在模拟过程中添加空化模型,采用了混合两相模型计算气液流动流场,同时根据空化模型预测气液两相之间的质量交换。计算中假定流动为等温过程,忽略相变潜热。添加k-ε湍流模型,假定流场完全是湍流,而忽略其他分支之间的粘性。根据航空滑油相关参数设置动力粘度系数,油液密度等。
4.3. 进、出油槽沟通位置对流量特性影响的仿真分析
本节主要分析了滑油泵高空工况和地面工况工作时,油槽不同沟通位置对滑油泵流量特性的影响规律,详见表1。研究的因素包括进口压力、出口压力、转速、润滑油温度以及含气量。
分析不同沟通位置对滑油泵流量特性的影响时,分别取地面工况和4 km工况、6 km工况、8 km工况、10 km工况进行对比研究,其中地面工况取进口压力为海平面标准大气压力101.325 kPa,高空工况进口压力取高度为10 km时的标准大气压力26.3 kPa,详见表2。其余条件各工况相同(转速设置为:15000 r/min,出口压力设置为:0.5 MPa,含气体积百分比1%,滑油参数根据某航空滑油设定,滑油温度设置为:343 K)。
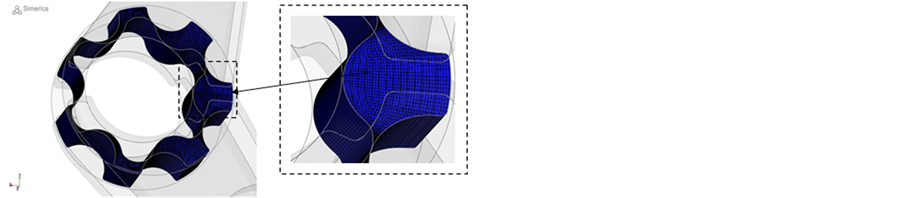
Figure 4. Grid: Single-stage pan-cycloid pump volume chamber in fluid domain
图4. 单级泛摆线泵容积腔流体域网格
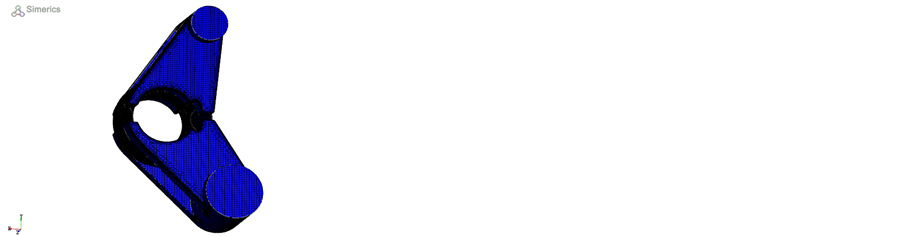
Figure 5. Grid: The fluid domain of the inlet and outlet cavity of the single-stage pan-cycloid pump
图5. 单级泛摆线泵进、出油槽流体域网格
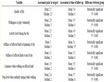
Table 1. Settings of communicating location
表1. 沟通位置设置
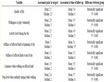
Table 2. Vacuum degree under different heights
表2. 不同高度下的真空度表
之所以选择不同的进口压力来代表不同的工作高度,是因为滑油系统大多是自由通风的系统,滑油箱经通风器与大气相通,因此滑油箱内的压力等于飞机所处的当地大气压力,因此进口压力是随着工作高度而变化的。
完成不同进口压力条件下的内啮合摆线齿轮泵特性数值计算,表3给出表1中4种情况在地面工况,4 km工况、6 km工况、8 km工况、10 km工况下的实际流量和流量脉动仿真结果,如表3。
根据表3数据得出图6和图7所示结果。
图6和图7可以看出,在沟通较小面积的情况下:
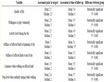
Table 3. Flow characteristic simulation result for different communication parts under different heights
表3. 不同高度下的不同沟通部位流量特性仿真结果
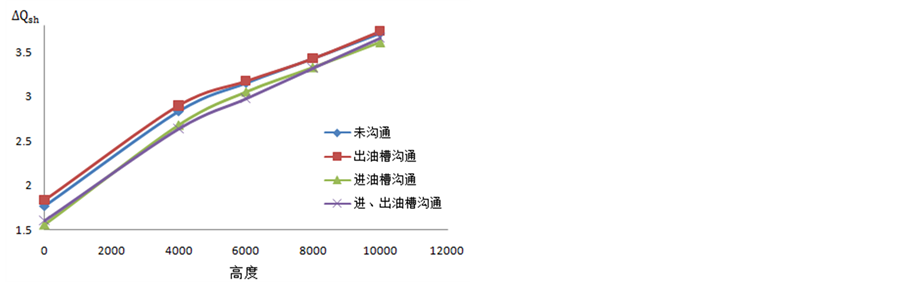
Figure 6. Curve: The influence of communication position on the flow pulsation in different height
图6. 不同高度下油槽沟通位置对流量脉动的影响
1) 随着工作高度增加,流量脉动增加。而实际流量则随工作高度下降而下降,与实际情况相符。且从两图中可以看出,进油槽沟通和进、出油槽同时沟通的情况下,不论从流量脉动方面还是实际流量方面来说,两者差别不大,相对来说优于未沟通和出油槽沟通的情况。
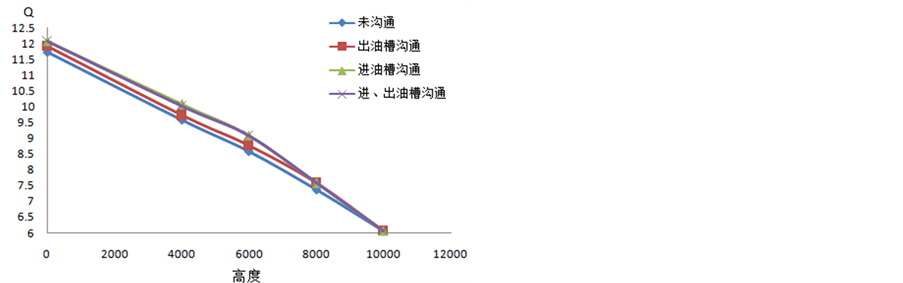
Figure 7. Curve: The influence of communication position on the actual flow in different height
图7. 不同高度下油槽沟通位置对实际流量的影响
2) 三种沟通情况相比未沟通时,实际流量都有不同程度的增加,这是由两方面原因造成的:a)为实现沟通,分别增加了进油面积、出油面积或两者同时增加,这就延长了进、出油时间,进出油量就有所增加;b)高转速下,油液被惯性得从进油槽带入出油槽,流量增大。且这两种因素的共同作用大于泄漏作用。
3) 选择出油槽沟通。此时,滑油实际流量相对未沟通情况有所增加,流量脉动增大。这是因为在高转速条件下,滑油能够惯性的从进油槽进入出油槽,瞬时流量最大值增加,但是由于在瞬时流量取最小值附近时,出油槽部分沟通,间隙增加,泄漏能力增强,同时高压区(出油区)附近流通截面积增大,低压区(进油区)附近流通截面积保持不变,相对高压区较小,由质量连续性定理可知,滑油从高压区泄漏至低压区时,单位时间内泄漏流量增加,泄漏流动量增加,瞬时流量最小值变小,所以脉动增大。且对于整个过程来说,惯性带入的油量作用大于泄漏的油量,所以实际流量增大。
4) 选择进油槽沟通。此时,滑油实际流量相对出油槽沟通的情况又有所增加,流量脉动却比未沟通时更低。这是因为在高转速条件下,进油槽部分先沟通,低压区附近流通截面积增大,高压区附近保持不变,泄漏流在低压区速度较慢,在瞬时流量取最小值附近时,泄漏速度相对较低,泄漏流动量较低,最小值增大,所以流量脉动减小。
5) 进、出油槽同时沟通。此时,滑油实际流量相对于未沟通和出油槽沟通时要大,而小于进油槽沟通时的值,流量脉动仅大于进油槽沟通时。前面提到过容积式泵的压力脉动是由容积腔的变化引起的,当密闭容积腔打开瞬间压力容易过大,因此本文接下来的研究主要采取这种结构。
在此基础上,为了进一步确认沟通面积和油槽距离对泛摆线滑油泵流量特性的影响规律,分地面和10 km高空进行分析,设置出口沟通面积1.3 mm2,改变进口沟通面积,图中沟通面积为进、出油口总沟通面积,得出如下数据(见图8~图11):
从图8~图11,可以看出:
1) 随着沟通面积的增加和油槽间距的缩小,泛摆线泵实际流量呈现:先增大后减小的趋势。地面状态下实际流量最大值出现在沟通面积为:0~5.19 mm2之间,油槽间距:3.1~4.0 mm之间,改善效果有限。高空状态下实际流量最大值出现在沟通面积为:7.03~8.85 mm2之间,油槽间距:1.9~2.5 mm之间,较不沟通的情况,提高约10%。
2) 随着沟通面积的增加和油槽间距的缩小,泛摆线泵流量脉动呈现:先减小后增大的趋势。地面状态下实际流量最小值出现在沟通面积为:0~5.19 mm2之间,油槽间距:3.1~4.0 mm之间,改善效果有限。高空状态下实际流量最大值出现在沟通面积为:5.19~8.85 mm2之间,油槽间距:2.5~3.1 mm之间,较不
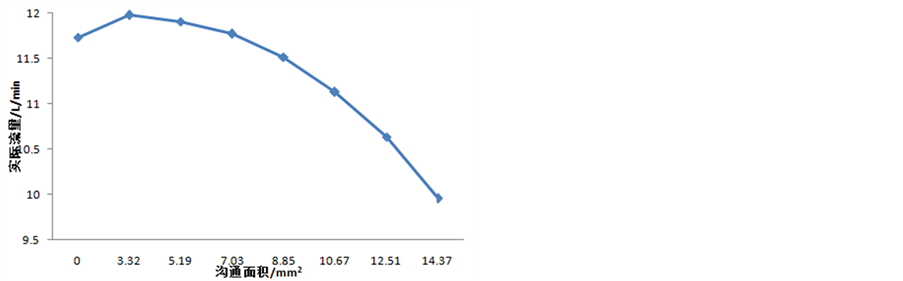
Figure 8. Curve: Effect of communicate area and cavity distant on actual flow of ground state
图8. 地面工况沟通面积及油槽间距对实际流量的共同影响
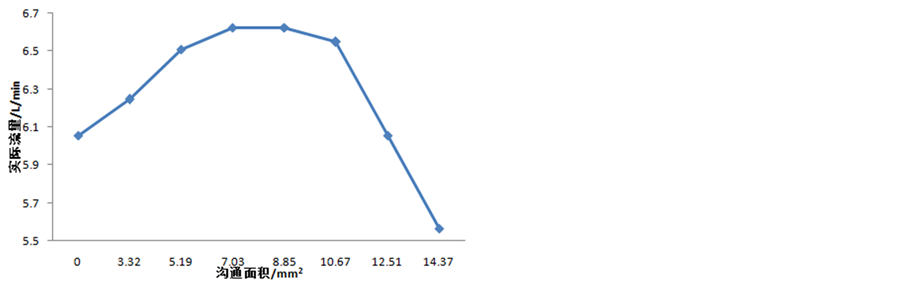
Figure 9. Curve: effect of communicate area and cavity distant on actual flow at 10 km
图9. 10 km高空工况沟通面积及油槽间距对实际流量的共同影响
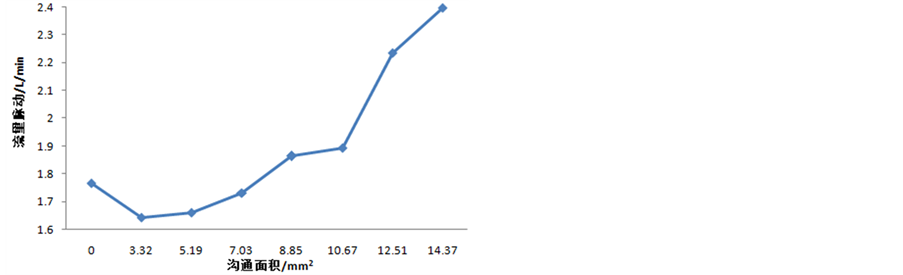
Figure 10. Curve: Effect of communicate area and cavity distant on flow pulsation of ground state
图10. 地面工况沟通面积及油槽间距对流量脉动的共同影响
沟通的情况,下降约13%。
5. 多级泵结构优化
摆线泵的流量和瞬时流量与中心距a的平方和转子宽度B成正比,而转子宽度B的值不宜取过大,
通常为12 mm以内。因此,为了保证充分供油,采用多级供油的方式,且各级共用一个进油口和一个出油口。此时,各级泵的流量脉动是叠加的,因此只要使各对转子流量脉动波峰错开,即可减小流量脉动。对于两对转子的泵来说,最佳情况为转子1流量脉动波峰与转子2流量脉动波谷同时出现。本文取内转子齿数z1 = 4的泛摆线泵,在原型的基础上错开45度,对多级串联式油泵采取错相位法进行优化及仿真验证。
5.1. 模型建立及网格划分
仿真计算域为摆线泵内部的油液流动区域。根据设计的泛摆线泵的几何尺寸,计算出与形成密封区域相关的啮合点坐标。在solidworks中建立泵的三维模型,反向抽壳出流体域,生成STL文件,将生成的STL文件导入pumplinx,按区域划分,静止区域生成通用网格,旋转区域选择转子网格划分,生成动网格,连通MGI面后。如图12、图13所示。
共生成网格数:400633,节点数:1566072,面元数:700987。
共生成网格数:461318,节点数:1852316,面元数:81170。
添加湍流模型和空化模型,假定条件与4.2中相同。
5.2. 错相位法与原型对比仿真
仿真时,两对转子拥有相同结构参数,设定相同转动方向,且转速相同,进口压力:大气压,出口压力:0.5 MPa,滑油温度343 K,根据航空滑油相关参数设置动力粘度系数,油液密度等。忽略容积腔因泵体材料热胀冷缩引起的体积变化,且油温不变。见图14、如图15。
对比串联错相位法及原型两级泛摆线泵流量脉动图,如图16、图17,发现对于内转子齿数为4,两
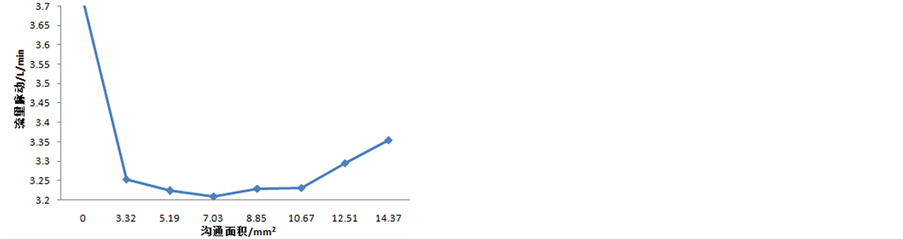
Figure 11. Curve: Influence of communicate area and cavity distant on actual flow at 10 km
图11. 10 km高空工况沟通面积及油槽间距对实际流量的共同影响
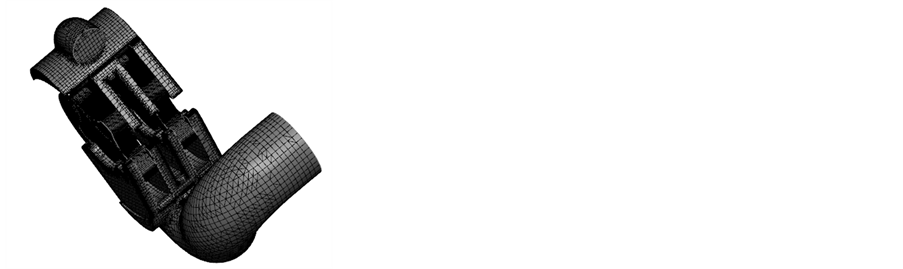
Figure 12. Prototype two-stage pan-cycloid pump
图12. 原型两级泛摆线泵
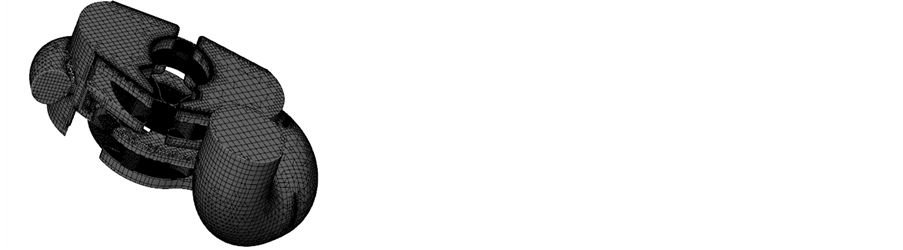
Figure 13. Dislocated two-stage pan-cycloid pump
图13. 错相位法两级泛摆线泵
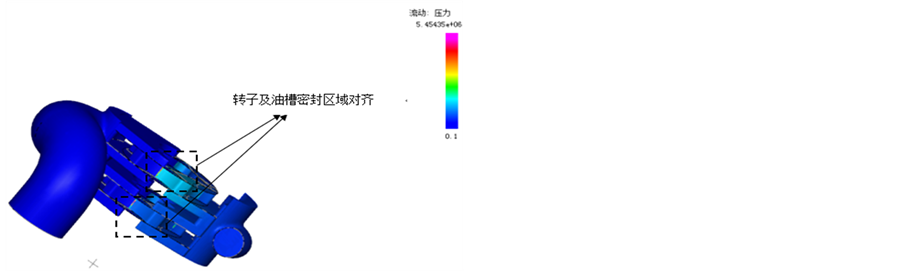
Figure 14. Pressure cloud: Prototype two-stage pan-cycloid pump
图14. 原型两级泛摆线泵压力云图

Figure 15. Pulsating flow diagram: Prototype two-stage pan-cycloid pump
图15. 原型两级泛摆线泵流量脉动图
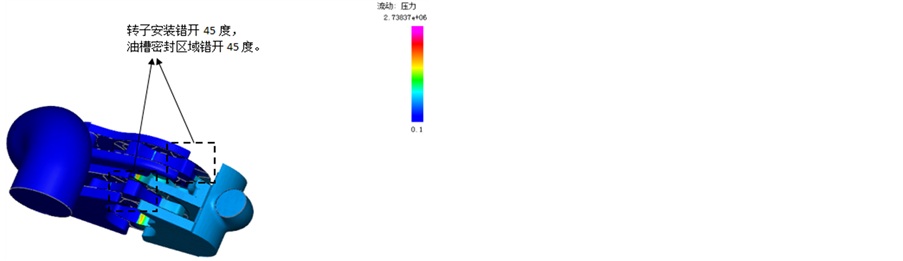
Figure 16. Pressure cloud: Dislocated two-stage pan-cycloid pump
图16. 错相位法两级泛摆线泵压力云图

Figure 17. Pulsating flow diagram: Dislocated two-stage pan-cycloid pump
图17. 错相位法两级泛摆线泵流量脉动图
对转子错开45度,能降低约40%的流量脉动。证明错相位法确实可行。
基金项目
国家自然科学基金号:No.51266012。