1. 引言
燃煤电厂是水资源消耗和废水排放大户。随着日趋增大的水资源和水环境容量压力,以及越来越严格的环保要求,实现水资源优化利用和减少废水排放量,对水环境保护和发电企业自身可持续发展都具有重要意义。
根据美国电力研究中心(EPRI)对于废水“零排放”的定义:电厂不向地面水域排放任何形式的水(排出或渗出),所有离开电厂的水都是以湿气的形式或是固化在灰及渣中。这意味着,真正的废水零排放应做到将所有需要排放的液体以水蒸汽或固体的形式进行排放,而没有任何液体形式的排放。国内很多电厂做过许多相关研究和尝试,但实际上仅仅实现部分废水的减排,或仅仅实现了部分种类废水处理后的回用,而其他废水如循环冷却系统排水、脱硫废水、非经常性废水等处理后则直接排放或部分用于干灰加湿,没有真正实现废水零排放 [1] 。同时,目前电厂灰渣大多数立足于综合利用,需要调湿的灰渣量较少甚至没有,造成脱硫废水回用于灰渣调湿的可靠性较差。
河南某2 × 660 MW燃煤供热机组工程的水资源论证和环境影响评价批复均要求,工程应实现废水零排放,不设置入河排污口。本文通过分析该工程的水源、废水种类和水量、各系统耗水情况等,介绍了实现全厂废水零排放所采取的系统方案和关键技术,重点是循环冷却排水旁流石灰处理系统和脱硫废水“预处理 + 正渗透 + 蒸发结晶”处理系统。研究结果对采取循环冷却方式和石灰石–石膏湿法脱硫技术的燃煤电厂废水零排放方案设计具有一定的参考价值。
2. 项目水源、废水种类和废水量
河南某电厂设计建设2台660 MW超超临界燃煤机组,采用石灰石–石膏湿法脱硫系统、SCR脱硝系统、电袋复合除尘和湿式电除尘器,以及干除灰、干排渣系统等。该工程以城市污水处理厂中水为生产水源,主要水质指标见表1所示,满足《城市污水再生利用工业用水水质》(GB/T 19923-2005)相关控制指标。
该工程设有二次循环冷却系统,废水包括经常性废水和非经常性废水两大类。其中,经常性废水包括净水站废水、循环冷却排水、锅炉补给水处理系统浓水、脱硫废水、含油废水、含煤废水、生活污水;非经常性废水包括机组酸洗废水、空预器冲洗废水等,具体如表2所示。
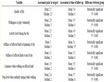
Table 1. Water quality of the recycled municipal wastewater
表1. 中水水源的水质分析
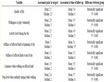
Table 2. Overview on wastewater emission
表2. 废水产生情况
*括号外数据为夏季非采暖期水量,括号内数据为冬季采暖期水量。
3. 零排放系统与关键技术
3.1. 系统难点
实现该工程废水零排放的难点和关键有两处:
1) 循环冷却排水。由表2可知,循环冷却排水为全厂产生量最大的经常性废水,夏季可达733 m3/h,除回用于化学水处理系统、脱硫系统和直接用于冲洗、抑尘等环节外,尚余近400 m3/h。由于其水量大且盐分含量较高,难以在厂内全部直接回用消耗,因此必须增加旁路处理系统对其进行除盐处理,出水可回用于循环冷却水,而浓水则送至对工艺水质要求较低的生产环节,如脱硫工艺用水。这样有利于提高浓缩倍率,降低循环冷却排水量和减少补充水的取水量。
2) 脱硫废水。采用石灰石–石膏湿法工艺进行烟气脱硫时,用真空皮带机将脱硫石膏浆液变成固态以供综合利用,将产生脱硫废水。由于其成分复杂,难以实现重复利用,属于末端废水。该废水水量不大,但氯根含量很高,且含有重金属等多种难处理的成分,主要超标项目包括悬浮物、pH值、汞、铜、砷、铅、镍、铬等,其中汞、砷、铅、镍、铬等属于第一类污染物,根据GB8978-1996的要求,脱硫废水应单独处理 [2] 。
脱硫废水的常规处理工艺一般包括中和、沉淀、絮凝、澄清等环节,出水中绝大部分污染物得以去除,但氯离子浓度仍然很高,通常可用于冲灰冲渣、干灰调湿、灰场喷洒等。然而,采取干除灰、干排渣工艺和立足灰渣综合利用后,出水回用于上述环节的可靠性较差。实现脱硫废水复用的关键是要将废水中的氯离子和硬度去除以避免复用设备发生腐蚀与结垢 [1] ,因此,需要对常规工艺的出水进行进一步的深度除盐处理,使其绝大部分能够回用于其它环节,提高废水重复利用率,尽可能减少需要末端处理的浓水量,降低末端处理设施的运行压力,实现脱硫废水零排放。
3.2. 方案设计
实现电厂废水零排放,应按照“一水多用、梯级使用、循环利用”的基本原则,在满足各环节用水品质的前提下,优化废水处理方式和回用途径,尽可能提高水的重复利用率,从而减少新鲜取水量和降低废水产生量。在对系统难点和关键分析的基础上,据此原则,构建该工程的废水零排放系统如图1所示。
图1中,深度处理后的中水作为循环冷却系统补充水;循环冷却系统排水中的一部分经旁流石灰系统处理后作为锅炉补给水、脱硫工艺水和回用于循环冷却系统,一部分直接回用于脱硫工艺用水,另有少量直接用于各类冲洗用水;脱硫废水经正渗透处理后,浓水作为末端废水进入蒸发结晶系统实现盐分分离,清液与浓水脱盐后的清水共同回用于锅炉补给水;生活及消防用水取自城市自来水,主要回用于绿化喷洒,冬季植被需水较少时亦可用于输煤系统冲洗。
3.3. 循环冷却排水旁流石灰处理系统
采用旁流处理选择性地除去水中悬浮物、溶解固体和微生物等有害成分,是实现冷却水系统即时在线清洁和冷却水水质改善的积极措施[3] ,是近阶段容易实现、也是成本较低的节水方式[4] 。高华生等[5] 认为大型工业循环冷却水系统可采用“化学混凝过滤、弱酸离子交换树脂和反渗透技术”相结合的三级旁流处理工艺,且该工艺的三大单元可根据用户实际需要进行组合。本工程的旁流石灰处理系统即采用“化学混凝–纤维过滤–弱酸树脂软化”工艺,并结合实际生产流程,将反渗透单元结合锅炉补给水处理系统设置,进一步软化和净化水质后作为锅炉补给水使用。
1) 化学混凝和纤维过滤单元
循环冷却排水加入沉淀剂和混凝剂后,在管道中混合均匀并进入纤维过滤器,在滤床上方的反应区发生软化反应和微絮凝反应,生成的CaCO3、Mg(OH)2等颗粒与水中的悬浮物、磷酸盐等一起被纤维滤料截留去除。
2) 弱酸树脂软化单元
该单元采用弱酸阳离子交换树脂同时降低水中的硬度和碱度。高华生等[5] 研究表明,该单元出水水
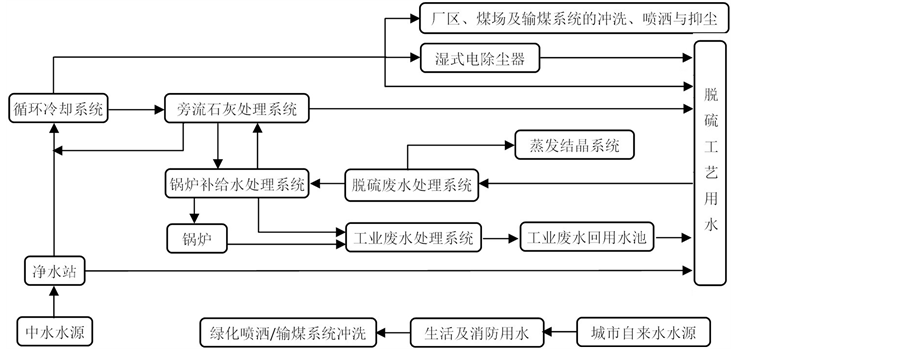
Figure 1. Schematic diagram of zero discharge system and wastewater flows
图1. 全厂零排放系统及废水流向示意图
质中此两项指标均为50 mg/L左右,pH值约3~6,基本满足补充水水质要求,且出水偏酸性有利于减少结垢倾向。如图1,单元出水回用于循环冷却系统,水量约315 m3/h,单元浓水回用于脱硫工艺用水,浓水量约3 m3/h。
3) 反渗透单元
该单元用于系统对补充水中有害成分有更严格要求时的进一步软化和净化。本工程将其结合锅炉补给水处理系统布置,亦可视旁流石灰处理系统为锅炉补给水的预处理环节,如图1,浓水进入工业废水处理系统,软化水用作锅炉补给水。
通过采用“化学混凝–纤维过滤–弱酸树脂软化”的旁流石灰处理系统对循环冷却排水进行处理后,出水水质基本满足循环冷却系统水质需求,与中水深度处理后的补充水混合后,共同作为循环冷却水使用。该处理系统有利于提高浓缩倍率,减轻结垢倾向,利于循环冷却系统的稳定运行。
3.4. 脱硫废水正渗透和蒸发结晶处理系统
目前常用的电厂脱硫废水深度处理方法主要包括膜浓缩法、蒸发浓缩法和结晶技术。马越[6] 等通过对国内外脱硫废水零排放典型案例的分析认为,其深度处理技术基本均采用蒸发结晶工艺,相对于膜浓缩法而言,该技术路线虽然运行成本和设备投资较高,但预处理要求较低,且系统简单、流程短、运行稳定,其可靠性和对原水水质波动的适应性都远远高于膜浓缩法。
该工程采用“常规工艺预处理 + 正渗透 + 蒸发结晶”的脱硫废水处理工艺,对盐分进行充分分离,处理后的出水为除盐水,回用于锅炉补给水处理系统。其主要工艺流程如图2所示。
1) 预处理
预处理采用国内外火电厂中应用最广泛的脱硫废水混凝–沉淀法,其关键工艺是三联箱技术[7] 。脱硫废水进入预沉池,通过重力沉降降低悬浮物浓度,同时起到废水缓冲的作用,随后废水被提升至三联箱。首先,向中和箱投加石灰乳,F−转化成不溶的CaF2沉淀,Cu2+、Ni+、Cr3+等重金属离子以难溶的氢氧化物形式析出沉淀;然后,废水流入沉降箱,加入FeClSO4和有机硫(TMT15),使水中的Ca2+和Hg2+、Pb2+等重金属形成难溶的硫化物等微细絮凝体;微细絮凝体随废水流入絮凝箱后加入助凝剂,助凝剂与微细絮凝体逐渐形成更大的絮凝体;废水进入澄清分离器后,絮凝体与水分离,絮凝体浓缩形成污泥,清水流入出水箱内加酸调节pH值至6~9;最后,清水储存中间水池内,等待送至脱硫废水深度处理车间处理,浓缩污泥则由污泥输送泵送至污泥脱水装置,经板框压滤机脱水后制成泥饼外运处理,滤液返回预沉池收集处理。
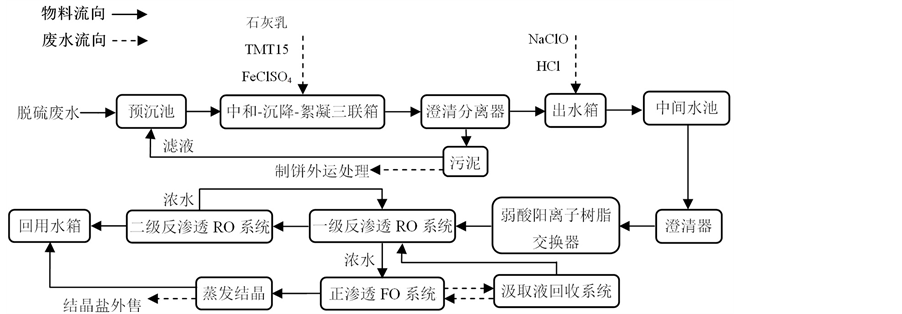
Figure 2. Technical flow Chart of desulfurization wastewater treatment
图2. 脱硫废水处理工艺流程图
2) 正渗透
来自中间水池的废水进入澄清器投加碱液进一步调节pH值稳定在7.5~8.5,同时可促使水中Ca2+、Mg2+形成CaCO3沉淀和Mg(OH)2沉淀以污泥的形式除去;清液进入弱酸阳离子树脂交换器,再次降低水中Ca2+、Mg2+的含量,使水软化,其反洗水和再生液均返回中间水池循环处理。
离子交换产水进入一级反渗透RO系统脱除盐分,一级RO产水进入二级反渗透RO系统进行精制,浓水则进入正渗透FO系统。二级RO产水进入回用水箱后供用户使用,浓水回流到一级RO 装置进一步回收利用。
一级RO浓水进入正渗透FO系统进一步浓缩至含盐量200 g/L左右作为蒸发结晶系统的原料,产水则回流至一级RO装置,与来水混合后经一级RO、二级RO装置进一步回收利用。
2014年12月投运的华能长兴2 × 660 MW机组是国内首个运用正渗透技术的废水零排放项目[8] 。该厂脱硫废水产生量约18 m3/h,采用将传统混凝沉淀技术与正渗透技术相结合的方案,经浓缩后进入蒸发结晶系统的浓水仅3~4 t,大大减小了结晶器规模,有效降低了运行过程中电能、药品等消耗量,可减少企业约20%的资金投入和30%的运行成本[9] 。
3) 蒸发结晶
采用机械蒸汽再压缩蒸发系统和立式强制循环结晶器,浓水在蒸发结晶过程中产生的蒸汽经冷凝后进入回用水箱与二级反渗透RO装置产水混合后一起外供回用,而结晶析出的固体颗粒则经离心机脱水干燥,最终生成含水率小于5%的结晶盐,送至包装车间处理后外售。强制循环结晶工艺还有利于实现不同盐类的分别结晶分离,使结晶盐纯度得到提高,有利于提高副产品的附加值[10] 。
4. 结束语
1) 废水零排放是火电行业可持续发展的必经之路,对于采取二次循环冷却方式和石灰石–石膏湿法脱硫技术的燃煤电厂而言,实现全厂废水零排放的关键和难点在于提高循环冷却系统的浓缩倍率、减少循环冷却排水量,以及末端脱硫废水的综合利用。
2) 增设旁流石灰处理设备对循环冷却排水进行处理,出水中的一部分可回用于循环冷却系统,有利于提高浓缩倍率和减少循环水新鲜补水量,一部分可作为锅炉补给水水源,同时将处理废水用于脱硫工艺用水,一水多用、循环利用,是实现循环冷却排水全面综合利用的有效途径。
3) 脱硫废水经常规工艺预处理后,进入正渗透系统进一步浓缩,大大降低了进入蒸发结晶器的水量,有效降低了蒸发结晶器的设备投入及运行成本;再经蒸发结晶工艺处理,结晶盐品质明显提高,相对于常规处理产出的结晶盐需作为危险废物专门处置而言,既实现了脱硫废水的真正零排放,又节约了危废处理成本并实现了工业盐销售收益。
4) 脱硫工艺用水作为厂内用水品质要求较低的环节,是废水回用的最大受水点,接受的回用水源种类多、水质差异大。因此,实际运行中应加强全厂水务管理,尤其是各废水排放点、水处理系统与脱硫工艺部门的协调运行,以保证各路回用水源都能按照设计要求在脱硫系统中得到重复使用,这是零排放设计方案能够真正落实的重要保障。