1. 引言
21世纪是科技飞速发展的世纪,具体到每一个科技领域诸如交通、军事、能源等基础设施,均迫切需要能够在高温、高压及高辐射等极端环境下高效率工作的电子器件。然而据目前所研究和了解的情况看,传统硅器件由于其自身限制,很难满足这些条件[1] 。碳化硅(Silicon Carbide,简称SiC)材料是第三代宽禁带半导体材料。4H-SiC材料在室温情况下的禁带宽度为3.28 eV,近似于硅(Si)的三倍,极大地提高了器件的工作电压。4H-SiC材料的热导率为4.5 W∙cm−1∙K−1,同样也是硅(Si)的三倍,降低了对冷却系统的需求。另外,SiC材料的临界雪崩击穿电场强度是Si材料的10倍以上,使得SiC MOSFET相比于Si MOSFET导通电阻更小。开关电压更高、温度性能更好,特别适用于功率开关应用 [2] 。SiC材料正是在这样的背景下以其优良的物理和电学性能进入了国内外研究者们的视野里。
良好的欧姆接触是高压、大功率半导体器件领域应用的关键工艺技术之一。欧姆接触质量的好坏和接触电阻的大小直接影响着半导体器件的开关速度以及半导体器件的功率损耗。如图1所示,SiC LDMOSFET器件结构上的源极和漏极均需要形成良好的p型欧姆接触。和Si材料相比,由于在SiC材
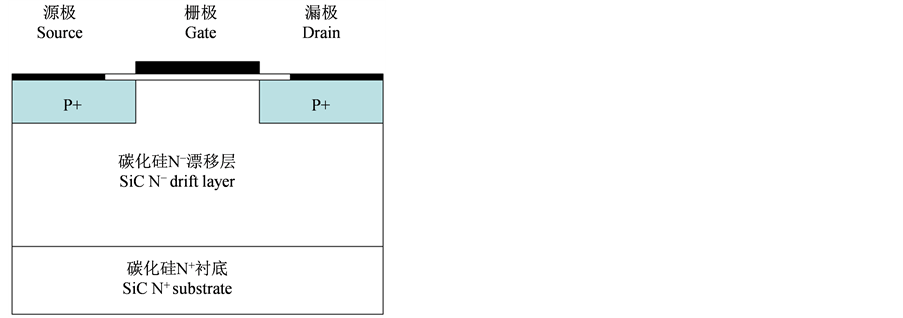
Figure 1. The schematic view of the SiC LDMOSFET
图1. SiC LDMOSFET器件结构示意图
料中p型杂质的离化能比n型杂质的离化能高,掺杂浓度又难于做到n型SiC的掺杂水平 [3] ,因此,p型SiC材料的良好欧姆接触获得难度大,制约了SiC LDMOSFET的器件性能。
截至目前,对于p型SiC的欧姆接触的文献报道主要是选用不同的金属材料在不同的工艺条件下进行合金退火(退火温度和退火气氛等),比较实验结果 [4] 。为了达到最优的p型SiC的欧姆接触,Mysliwiec M 等人使用Ti(10 nm)/Al(100 nm)/Ti(16 nm)在p型4H-SiC上的欧姆接触退火条件为1000℃,2 min,所得比接触电阻优值为3.1 × 10−3 Ω·cm2 [5] ;Tsukimoto S将Ti(50 nm)/Al(190 nm)电极制作在SiC上后的退火条件为1000℃,2 min,所得比接触电阻优值为2.0 × 10−5 Ω·cm2 [3] ;Crofton J采用Ti(100nm)/Al(300nm)后的欧姆退火温度选择950℃,1 min,所得比接触电阻的最佳值为1.45 × 10−4 Ω·cm2 [6] ;Tamaso H等人使用Ti(20 nm)/Al(30 nm)/Si(30 nm)在p型4H-SiC上的欧姆接触退火条件为1020℃,2.5 min,最后所得最佳比接触电阻值为1.7 × 10−4 Ω·cm2 [7] 。Ti/Al比率决定着p型SiC欧姆接触的形成和最佳化的Al浓度范围从70%~80% [3] [8] [9] 。许多研究已经报道的Ti/Al欧姆接触的Al厚度都超过100 nm [9] - [11] 。例如,Tanimoto等人已经报道 [9] Ti(80 nm)/Al(375 nm)有非常低的p型比接触电阻率ρp,已经得到的p型SiC比接触电阻值范围在10−3~10−5 Ω·cm2之间 [12] [13] 。较厚的Ti/Al合金会增加工艺的时间和成本。
本文研究了一个新组分的Ti/Al基p型欧姆接触,所采用的Ti/Al金属厚度仅为20 nm和30 nm。随后,对其欧姆接触特性进行了系统地研究。
2. 实验
本实验通过在n型4H-SiC衬底片上生长1 um厚的p型高掺杂的外延,掺入的杂质是Al,浓度为1 × 1020 cm−3。在化学方法清洗表面后,溅射AlSi作为隔离刻蚀的掩膜,刻蚀隔离后淀积金属,金属Ti和Al均是通过溅射台溅射的。溅射金属后,通过光刻和刻蚀制作TLM接触电极,电极示意图如图2(a)所示。经退火后形成欧姆接触,然后采用传输线方法(transmission-line method, TLM)测试比接触电阻率。退火温度是1000℃,退火时间是2.5 min。实验中使用Ti(20 nm)/Al(30 nm)在p型4H-SiC上形成的金属电极TLM测试结构图形如图2(b)所示,其长度和宽度均为200 um,接触块两两之间的间距从小到大分别为10,20,30,40,50,60,70,80,90,100 um。
本研究在总结前人退火温度的前提下,结合现有工艺条件,选择主退火温度和时间分别为1000℃,2.5 min。图3展示的是实验中RTA退火的示意图,图3中上边的曲线代表退火过程中的温度变化,下边的曲线代表退火过程中的功率变化。由图3可知,先进行500℃,60 s的预退火,然后以10℃/sec的速率升温至1000℃,在1000℃保持150 sec,然后自然降温。
(a) (b)
Figure 2. (a) The schematic diagram of TLM test structure; (b) The TLM test patterns
图2. (a) TLM测试结构截面示意图;(b) TLM测试结构图形
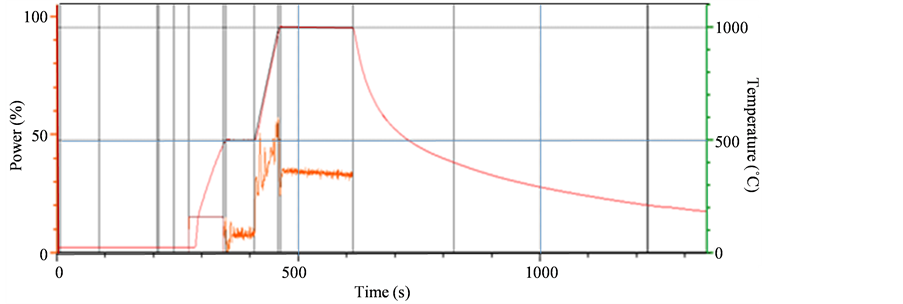
Figure 3. Temperature versus time curve during RTA process
图3. RTA退火工艺中的退火温度–时间曲线
3. 结果和讨论
3.1. Ti(20 nm)/Al(30 nm)/p型4H-SiC欧姆接触的机理
虽然使用Ti/Al基合金在p型SiC上形成欧姆接触的理论提出很多,然而对于Ti/Al基合金通过合适的工艺条件能够在SiC上形成欧姆接触的机理目前仍无定论。Ohyanagi认为接触界面存在的碳元素在降低肖特基势垒方面很可能扮演着重要的角色 [14] 。然而,Nakatsuka等人总结说,TiAl合金中Al成分在接触过程中才是占主要地位的 [9] 。John和Capano使用湿法刻蚀和离子研磨技术,排除了这些可能性,然后声称:欧姆特性的形成是因为在金属半导体接触之间形成了碳化物、Ti3SiC2和Al4C3 [13] 。更进一步的研究对接触区揭示了另一种允许电子穿过半导体的新理论,即在SiC/Ti3SiC2界面上会形成阶梯 [15] 。Ti/Al基金属电极与p型4H-SiC经退火后形成欧姆接触的原因还有很多,目前较为公认的解释是在快速高温热退火后,金属半导体之间形成了中间物Ti3SiC2 [3] ,Ti3SiC2属于窄禁带半导体,禁带宽度仅为0.12 eV。这样可以有效的降低势垒高度,利于载流子的热场发射,从而形成欧姆接触 [16] 。退火前后能带变化模型如图4所示。
3.2. 传输线方法(Transmission-Line Method, TLM)和模型计算
TLM测试法是测量比接触电阻的一种常用的方法。TLM测量的测试装置包含一系列长度和宽度均相等的相同的金属压焊点,它们做在半导体表面上,并且间距d不相等。传输线模型法最早由Schockley引入,后来Berger作了进一步改进。按照此模型的测试图形,如图5所示,在一宽为Z的长条形半导体上做上一系列长方形欧姆接触,为避免电流横向在两个宽为Z、长为L的欧姆接触之间,此长方形半导
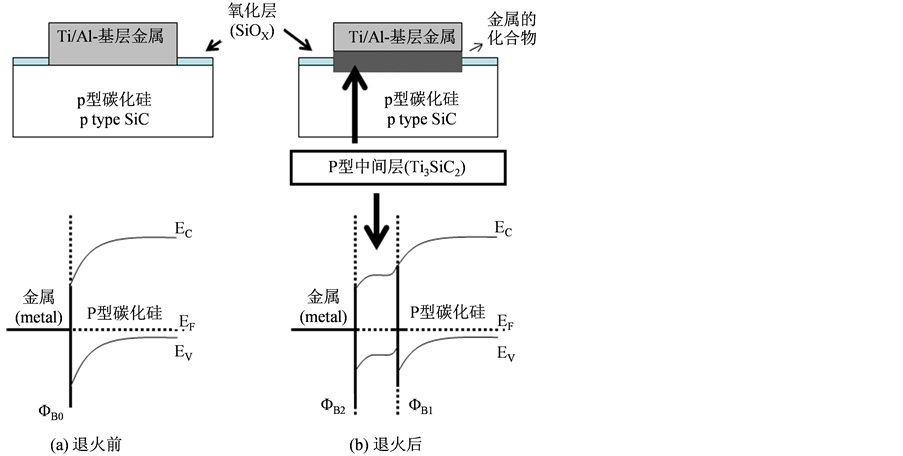
Figure 4. The energy band gap model of Ti/Al/p type 4H-SiC before and after annealing
图4. Ti(20 nm)/Al(30 nm)/p型4H-SiC退火前后能带模型
体需要和环境隔离。这个可以通过做腐蚀台面,或者做p-n结在周围做高阻隔离,在SiC工艺中,由于SiC的材料特性难于进行刻蚀,因此在工艺中常用的就是做p-n结做高阻隔离。在光刻工艺允许的条件下,Z与W的值应该尽量接近,即间隙应尽可能小,以降低寄生电阻。
比接触电阻ρc是评价欧姆接触质量的重要参数,是指金属与半导体之间形成的电阻Rc与金属与半导体接触横截面积A的乘积。采用TLM传输线方法,比接触电阻(ρc)可以通过金属半导体接触的I-V特性计算得到,即
(1)
式(1)假设金属与半导体接触的整个面积都参与了导电过程,实际的情况并不是这样。比接触电阻ρc与半导体的掺杂浓度和金属与半导体接触的势垒高度有关,可以表示为
(2)
其中,N代表半导体掺杂浓度,ΦB是金属与半导体接触的势垒高度,式(2)给出了比接触电阻ρc与两者的变化规律,其意义是如果通过实验得到某一掺杂浓度的金属和半导体形成的欧姆接触的比接触电阻ρc,可以通过式(2)得到其他掺杂浓度N的比接触电阻ρc。
然后,通过TLM测试模型压焊点上的I-V测量,可以获得间隔为d的不同压焊点上的总接触电阻RT,如下式(3)所示:
(3)
将总接触电阻RT作为间距d的函数,可以得到图6。通过图6中的两个截距和斜率,利用式(4)和(5)最终计算出比接触电阻。
(4)
(5)
其中,Rsh为材料的己知方块电阻。Rc是合金化后金属与半导体的接触电阻。LT称为传输长度,定义为电压曲线下降到1/e时的金属块长度;Slope为所做曲线的斜率;当RT = 0时,直线在d轴上的交点为2LT。而直线的斜率为
[17] 。TLM测试法的关键在于作图。用
表示所测各组总的电阻值,
表示金属块的各间距,ρc表示比接触电阻,具体测试计算步骤如下:
1) 测出一组实验数据RTi。
2) 将实验数据RTi和金属块间距di描点在直角坐标系上,并做直线(如果欧姆接触良好,同时各个间距设置正确的话,所描的点应近似在一条直线上)。
3) 计算出直角坐标系上直线的斜率和截距,利用上述公式进行计算,最后求出比接触电阻ρc。
3.3. 基于TLM的I-V测试和拟合结果
图7展示的是在一系列不同间距的TLM模型上测试得到的I-V曲线。从图7中可以看出,电流和电压成线性关系,表明p型4H-SiC开始表现出良好的欧姆特性。
以临近的Ti/Al金属电极所测的接触电阻值作纵轴,以他们之间的间距做横轴,这就是典型的TLM测试表征模型。此特征曲线有线性特征,表明p型4H-SiC上已形成良好的欧姆接触,比接触电阻能够通过对I-V特性曲线的拟合准确地计算出来,如图8所示。拟合的结果显示使用厚度比较薄的Ti(20 nm)/Al(30 nm)合金金属通过常规退火工艺能够在p型4H-SiC上形成比接触电阻率相对较低的欧姆接触,其比接触电阻率ρc为5.71 × 10−4 Ω∙cm2。理想情况下,比接触电阻值越小越好,但因实际工艺或技
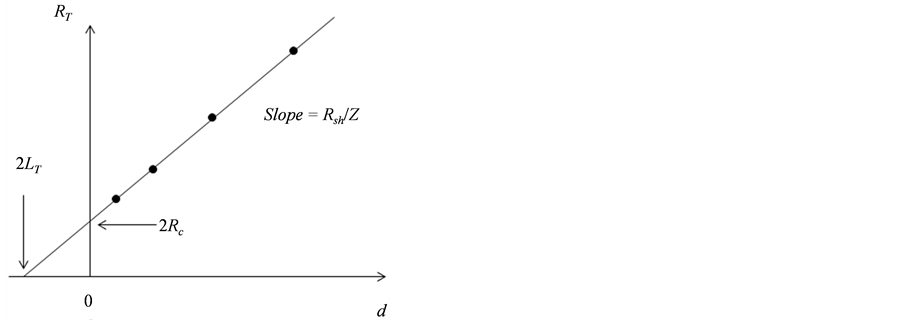
Figure 6. The function chart of total resistance versus the gap width between patterns
图6. 电阻做间距的函数
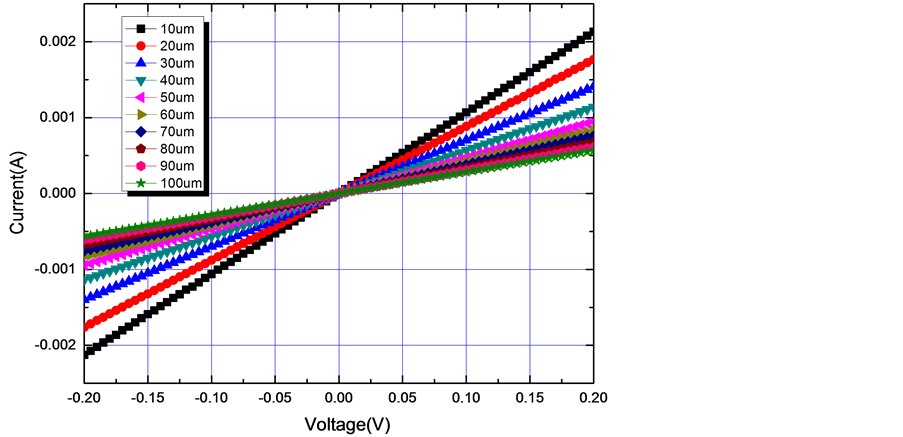
Figure 7. I-V curves in terms of different distances between patterns using the TLM model
图7. TLM模型中不同间距的I-V特征曲线
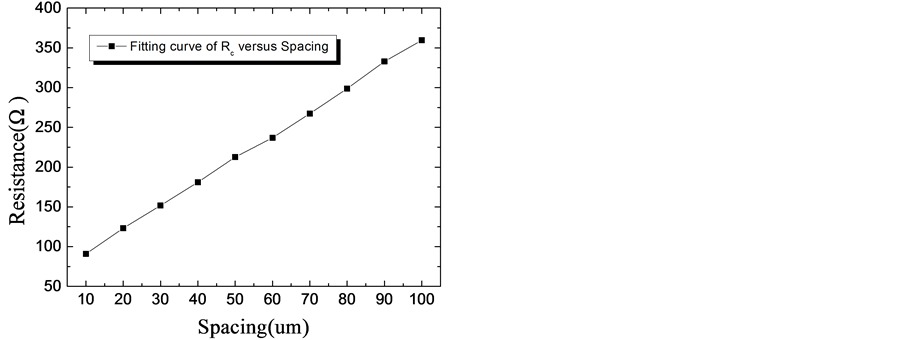
Figure 8. Fitting curve of Rs versus spacing based on I-V curve
图8. TLM测试拟合表征曲线
术条件的限制,本实验预期获得p型4H-SiC LDMOSFET欧姆接触的比接触电阻值只要在10−3量级即可接受。而本次实验获得的欧姆接触的比接触电阻率为5.71 × 10−4 Ω∙cm2,比预期结果的比接触电阻值降低了一个量级。本次实验获得较低的接触电阻率可能是由于采用了掺杂浓度较高的p型SiC材料(1020 cm−3量级),以及选择优化了退火条件,采用了在1000℃下退火2.5 min得到了较低的欧姆接触电阻率。满足了p型4H-SiC的LDMOSFET器件的电极欧姆接触的要求。
4. 总结
本文首先简要地介绍了p型SiC欧姆接触的开发背景、现状以及技术难点,然后描述了本实验过程及成果,并详细介绍了TLM测试法的理论及实际操作,验证并确认了使用厚度比较薄的Ti/Al(20/30 nm)合金通过常规工艺过程能够在p型4H-SiC上形成比接触电阻率相对较低的欧姆接触,其比接触电阻率为5.71 × 10−4 Ω·cm2。