1. 引言
变压器的总损耗是由空载损耗与负载损耗两部分组成,其中空载损耗不随负载大小而变化,只要变压器投入运行它就存在,其大小仅随电压波动而略有变化,在运行中可认为是一个不变的值。虽然空载损耗仅占总损耗的15%~25%左右,但由于电网中变压器的数量和总容量很大,且存在大量的低负载率的变压器,使空载损耗的影响显得尤为突出。因此,我国从20世纪80年代起,就开展了降低变压器损耗的研究,从推广采用S7系列的变压器,到性能更先进的S9系列产品,到比S9系列的损耗标准更低的S10、S11等系列产品,不断进行改进发展。现在,又有损耗更低的“非晶合金铁芯”变压器投入运行。要降低变压器的空载损耗,就要研究其降损原理,下面就从变压器制造理论和根据负荷情况改变变压器运行方式两个方面来论述变压器空载降损措施。
2. 从变压器制造理论上分析空载降损措施
变压器的铁芯结构采用铁芯柱和铁轭净截面相等(At = Ae)时,其空载损耗P。为:
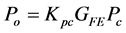
式中:Kpc——空载损耗附加系数,Kpc值与具体工艺、工装或结构等有关,目前在一些技术先进的工厂Kpc的值已有较大的降低。叠片式铁芯Kpc的取值范围为1.2~1.4,卷铁芯结构,单相Kpc = 1.02~1.04,三相Kpc = 1.1~1.25。)。GFE——铁芯(硅钢片)总质量(kg)。Pc——硅钢片单位质量损耗(w/kg),按设计磁通密度和选用的硅钢片型号可查设计手册获得 [1] 。
从上式可以看出,要降低变压器空载损耗应从降低铁芯的质量、单位损耗以及附加损耗系数这三个方面着手,具体分析如下。
2.1. 降低铁芯的总质量
首先,从变压器原理的分析可知(
),在保持铁芯磁密(B)一定的条件下,铁芯直径的减小(S减小)将使得绕组匝数增加,即铁芯材料消耗的减少将使得导线材料的消耗增加并使得短路阻抗、负载损耗值增加。而短路阻抗是变压器的一个很重要的性能参数,对变压器的制造成本,短路电流的大小,电压质量的高低及系统运行性能都有显著影响,在设计时要求严格地控制在一定范围之内。根据计算短路阻抗公式可知。短路阻抗的电抗分量:

式中:f——频率,IN——额定电流,UN——额定电压,W——主分接头总匝数(IN、W为同一侧数据),HK——两绕组平均电抗高度(即两绕组实际平均高度),∑D——常称为漏磁的等效面积(
:其中a1、a2:内外绕组径向厚度。r1、r2:内外绕组平均半径。a12:漏磁空道厚度、即高低压绕组间间隙宽。r12:漏磁空道平均半径)。ρ——洛氏系数(
,其中
,R2;外绕组外半径,R1内绕组内半径)。K——考虑横向漏磁通的影响的附加电抗系数 [2] 。
由上式可知,当增加铁芯直径而使绕组匝数W减少时,若要维持短路阻抗为一定值,则需要使绕组电抗高度HK减少,并使纵向漏磁等效面积∑D增大,即增加辐向尺寸而减少绕组高度,以使绕组和整个变压器的尺寸向宽而低的方向发展。反之,如减少铁芯直径而使绕组匝数增加时,为保持短路阻抗不变,则整个变压器的尺寸将向窄而高的方向发展。由于铁芯直径的选取将关系到整个变压器的制造成本,应视铁芯材料的增减及导线材料的减增之中哪一个量变化对制造成本影响更大来决定,确定最优的铜铁比,综合考虑各方因素,才能作出结论。这也是变压器实现优化设计的关键。
另外,在绝缘设计或铁芯结构方面采用一些先进技术,也可缩短铁芯磁路的尺寸,达到降低铁芯的总质量的目的。例如:在相同铁心截面、窗高、心柱距的情况下,采用三维立体卷铁心结构比起传统铁心结构来说可减少铁轭用量25%。且三维立体卷铁心截面填充系数高于传统铁心,在相同净截面积时可减小铁心直径,使三维立体卷铁心可降低空载损耗15%~20% [3] 。
2.2. 降低铁芯材料的单位质量损耗
降低铁芯材料的单位质量损耗主要取决于导磁材料的性能,就目前使用的材料来看,优质取向硅钢片与非晶合金材料的竞争十分激烈。取向硅钢片的厚度可降到0.15 mm,当其电阻率为50 μΩ·cm时,在Bm = l.7 T时的涡流损耗为0.11 W/Kg、磁滞损耗最低为0.2 W/Kg,整个材料的单位损耗在0.3 W/kg左右 [4] ,而其W1.0/50 = 0.16 W/kg左右,已接近非晶合金材料的损耗水平。近年来,我国在三维立体非晶合金变压器的研制与生产方面已取得了一定的发展,三维立体非晶合金变压器的磁路结构采用三个几何尺寸完全相同的单框半圆形截面铁芯,互成60度组合而成。其每框铁心均由整根硅钢片连续卷绕而成,磁路中不存在任何接缝。且其铁心采用真空退火,进一步细化硅钢片磁畴,使硅钢片具有二次再结晶能力。空载损耗比S9型传统变压器降低75%左右 [5] 。
另外,考虑到非晶合金的饱和磁通密度较低,单相变压器一般取1.3~1.4 T,三相变压器一般取1.25~1.35 T,产品设计会受到一些限制。对于大型变压器,由于它的设计磁密不能取得太低,所以需采用优质高导磁硅钢片或激光处理硅钢片,对于负荷率较高的变压器,因铜损占比较大,也应采用高导磁取向硅钢片或激光处理硅钢片。
2.3. 降低铁芯附加损耗系数
铁损不仅与材料的单位损耗有关,还与铁芯的结构形式、制造工艺等密切相关。采用先进的铁芯结构和工艺,能更有效地降低铁损并使优质材料的性能得以充分利用。对于叠片式铁芯结构而言,减小铁芯附加损耗系数可采取下列措施:
1) 采用45˚斜接缝来代替直接缝。选用直接缝方式时,其磁通方向与轧制方向不相一致那部位的面积大大超过了45˚斜接缝方式,使转角部位的局部损耗比45˚斜接缝方式要大。因此,目前的叠片式铁芯,均采用了45˚斜接缝方式。
2) 改传统的交错接缝为阶梯接缝。因交错接缝会使接缝处的磁通改变方向进入相邻的硅钢片中绕过间隙,造成局部磁密增大或磁饱和从而增大了局部损耗。而采用阶梯接缝铁芯,使接缝朝着同一方向错位形成阶梯分布,由于其绕过间隙的磁通位置错开,局部磁密增大小于交错接缝方式。阶梯接缝级数愈多铁芯接缝处磁性能改善愈充分。但随着级数的增加,磁性能改善的幅度也愈来愈小,在6级以后就不显著了。实践证明,当采用5阶梯时,一般硅钢片可降低空载损耗6%~8%,空载电流40%以上,噪声可降低2~7 dB。如采用27 ZH110硅钢片,则可降低空载损耗3.8%,空载电流47%左右。总的来说,硅钢片愈薄,效果愈明显,用激光处理的硅钢片(ZDKH牌号),其降低效果更明显 [6] 。
3) 卷铁芯结构因没有接缝或接缝很少,接缝部位的磁密不均匀所引起的损耗可不予考虑。因高次谐波磁通(主要是三次谐波)可以在传统的卷铁芯结构的各框内顺利流通,其产生的附加损耗将是卷铁芯铁耗增大的主要原因。三次谐波可使磁通波形畸变为一个顶部下陷的波形,引起导磁材料在磁化过程中出现局部磁滞回线,导致磁滞损耗增大,其增大的倍数设为Kh,在卷铁芯的一个框中可以认为磁通是均匀分布的,且只考虑基波磁通和三次谐波,而一般叠片式三相心式铁芯中,可认为仅有基波磁通存在,计算出两种结构下涡流损耗的比值就是由于结构的原因而使经典涡流损耗增加的倍数Kw,若设磁滞损耗、经典涡流损耗、异常涡流损耗所占的比例系数分别为βh、βw、βn,则在三相卷铁芯中,结构特点引起铁芯总损耗增加的倍数为:

式中
:三相卷铁芯变压器的铁耗的附加损耗系数。
由于Kw的数值较Kh、及Kn大很多,所以使用经典涡流损耗较低的硅钢片,能明显降低卷铁芯的附加损耗系数
。当采用非晶合金材料制作卷铁芯时,由于非晶合金很薄只有0.03 mm,电阻率又较大达到130 μΩ·cm,所以它的涡流损耗很低。此时铁损的结构系数
的值基本取决于Kh的大小,其值可在1.05以下。因此,对于非晶合金中小型变压器,应优先考虑采用卷铁芯结构 [7] 。
4) 尽量减少机械加工对电磁性能的破坏。铁芯在叠片剪切、运输过程中受到撞击、夹紧时的应力作用以及冲片的毛刺等都会影响到硅钢片的电磁性能。为了降低这部分损耗,应采用先进的工艺装备 [3] ,改进铁芯的紧固方式,非晶合金铁心片对压力、撞击及弯折等有非常的敏感性。在受到压力、撞击及弯折后其空载损耗会增加,同时很容易出现断裂、掉渣等现象,从而可能引发变压器绝缘出现故障。因此,在操作及搬运过程中要做到轻拿、轻放,避免出现撞击、受压现象。并采取措施防止铁心片产生的粉未碎片等掉入线匝内。在装配下夹件及夹件绝缘之前,须先用吸尘器吸净金属碎片及灰尘,再对接缝部位的两侧面涂刷绝缘漆进行封闭化处理。由于卷绕过程中硅钢片所受到的应力较大,一般均需要增加退火工艺来恢复其磁性能 [8] 。
3. 根据负荷情况改变变压器运行方式来实现节能减损
考虑到电力系统要通过升压和降压来实现电能的传输与分配,由于标准电压等级较多,使电网中变压器的安装容量远超过发电机装机容量。所以,变压器降损对电网的经济运行影响很大,特别是从23:00到第二天的凌晨8:00这段时间,大部分小城镇及农村配变都处于轻载有的甚至是空载运行,变压器空载损耗显得很突出。此时,可根据负荷情况改变变压器运行方式来减小空载损耗,其原理如下:
如图所示,正常运行时,D1、D2、D3、D4在合闸位置、D5在分闸位置、负荷1、负荷2分别由B1、B2供电。当负荷1、负荷2很小时,可采用自动控制装置断开D2、D4,合上D5。这样,既可保证用户不间断供电,有可减少一台变压器的空载损耗,当总负荷达到单台变压器容量时再自动合上D2、D4,断开D5,恢复正常运行方式。此方法也可应用于变电站的大中型变压器,但要经过计算确定。例如2台SFSZ10-31500/110变压器,其单台额定空载损耗P0为30.6 KW,额定负载损耗PK为148.8 KW,设2台变压器负荷电流分别为I1、I2,且
,式中IN为变压器额定电流,则此时单台运行与2台运行铜耗之差为:
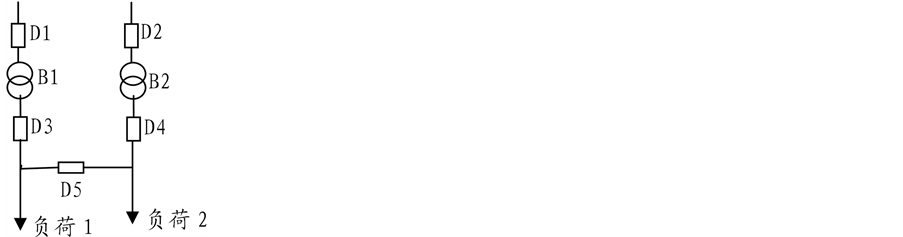

当
时上式取得极大值:

若
,则采用单台运行更节能,即
。
本例中
,所以,当总负荷只有单台变压器额定容量的0.64倍时,切换为单台运行较为节能。考虑到上面是以极值计算及变压器铜耗与电流成平方关系减小,其节能效果还是比较明显的。
4. 结论
通过采用新材料、新技术、新结构、新工艺不断提高变压器设计制造水平,可大幅降低变压器损耗,绿色环保节能的新型变压器将成为行业发展趋势,使其适应新时期节能减排的要求。同时,对于23:00到第二天的凌晨8:00这段时间,大部分小城镇及农村配变都处于轻载有的甚至是空载运行的情况,宜采用自动装置改变运行方式,停掉部分配变来实现节能。