1. 引言
Finemet合金 [1] ,因其磁导率高、矫顽力低、电导率高、损耗低等优异的软磁性能,被誉为人类人工合成的最佳材料。理论预测,Finemet合金相比硅钢等传统软磁材料具有显著优势,将使变压器、互感器、开关电源、电机等电力电子领域的软磁器件性能大幅提升 [2] 。但是,在实际应用中,采用非晶合金薄带制备的变压器、互感器和电机铁芯等非晶软磁器件的性能并未达到理论预计的优异性能 [3] 。除了因高电阻率导致的涡流损耗降低得以较充分体现外,非晶合金高磁导率的优势并未得到充分的体现。尤其是采用非晶合金薄带制备的非晶电机铁芯和大功率非晶变压器,除了明显降低涡流损耗外,综合效率的提升并未得到体现。按理论预测,采用非晶合金薄带制备铁芯替代硅钢铁芯的非晶电机应有10%~25%的效能提升 [4] ,但是,迄今,世界最高水平的非晶电机最高只能提升3% [5] ,远远没有达到理论预计。
由于现有的非晶软磁器件制备工艺普遍采用将非晶合金薄带进行盘绕的方法制备铁芯,为了实现较高的填充系数,通常都在较大的应力作用下才能使薄带紧密盘绕,这就不可避免地在非晶磁芯盘绕过程中引入很大的应力作用。李文忠等人研究表明非晶纳米晶材料的磁性能对应力敏感,存在巨应力效应(GSI) [6] 。为了消除应力的影响,现有工艺,普遍采用退火的方法试图消除应力的作用。但是,Herzer [7] 和Ohnuma [8] 等人研究表明,非晶软磁材料在应力作用下退火会感生显著的磁各向异性,严重影响非晶软磁器件的性能。退火是否是消除应力影响提升非晶软磁器件性能的好方法,是本文将要回答的科学问题。该科学问题的回答,对于寻求提升非晶软磁器件性能的新工艺具有重要意义。遗憾的是,迄今未见有报道明确回答该问题,业界普遍存在一个认识误区——适当温度退火可以消除制备过程引入的应力作用,导致现实非晶软磁器件生产过程中普遍采用退火工艺试图消除应力作用,忽略了应力存在条件下会感生不可消除的磁各向异性而严重影响器件性能。众所周知,电机、变压器的耗能占人类总耗能的70%以上,其效能每提高1个百分点所能节省的用电量,就相当于一个长江三峡的总发电量 [9] 。可见本文所研究科学问题,对于非晶软磁器件性能提升,和节能减排环境友好型新技术研发,具有重要意义。
2. 实验
本文使用单辊快淬法制备的Fe73.5Cu1Nb3Si13.5B9非晶薄带,宽1 mm,厚40 um,截取长14 cm的薄带。退火装置如图1所示,调整夹具之间的距离,使在夹具两端之间非晶薄带的长度为10 cm。在两端夹具之间的非晶薄带通以直流电,利用电流产生的焦耳热对样品实现退火,同在退火过程在两端的夹具上施加张应力实现电流应力退火。
电流应力退火感生的磁各向异性的定义根据杨燮龙等人 [10] 定义:横向磁各向异性场(HK)等于纵向驱动巨磁阻抗(LDGMI)曲线下降沿斜率变化最大处的外加磁场。定义LDGMI比如下:
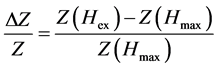
式中Z(Hex)和Z(Hmax)分别是在任意外磁场和最大外磁场下测得的阻抗值。
图2是经应力退火样品典型的LDGMI曲线,定义磁各向异性场Hk。
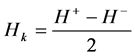
与
的取值如图2所示,取半高宽对应的磁场为下降沿斜率变化最大处。
伸长量:
其中
为样品退火后的实际观测值,
是样品退火前的原长。
Fe73.5Cu1Nb3Si13.5B9非晶薄带在电流密度为30 A/mm2,应力为198 MPa条件下保温30 min,测量其LDGMI曲线。再将该样品通以密度为30 A/mm2的电流持续30 min进行回火处理,然后测量其LDGMI曲线。随后再用相同条件对同一样品重复回火13次,并在每次回火后测量样品的LDGMI曲线。
3. 实验结果与讨论
图3是Fe基合金薄带经应力退火及回火样品的典型LDGMI曲线,a曲线是经应力退火样品的LDGMI曲线,b曲线是经第1次回火样品的LDGMI曲线,c曲线是经第3次回火样品的LDGMI曲线,d曲线是经第10次回火样品的LDGMI曲线,e曲线是经14次回火样品的LDGMI曲线。由图3可见,经应力退火的样品的LDGMI曲线经前几次回火有明显变化,表现为回火使LDGMI曲线往中心收缩和升高的行为,即样品的磁各向异性场明显减少和最大巨磁阻抗比增加,但是,随着回火次数的增加,这种变化迅速减缓。回火10次和回火14次样品的GMI曲线基本重叠在一起,表明10次以上回火样品的磁各向异性场和巨磁阻抗基本不变。
根据杨燮龙等人给出的磁各向异性场的计算公式,得出样品的磁各向异性场HK随回火次数的关系曲线如图4所示,图中N为零时是样品应力退火的磁各向异性场,回火1次磁各向异性场减小了60%。图5即回火一次到十四次的磁各向异性场的变化曲线,从图中可以看出,磁各向异性场的变化大致分为两个阶段,回火四到六次磁各向异性场平均减小了2.2%,回火六到十三次磁各向异性场平均减小了0.9%,
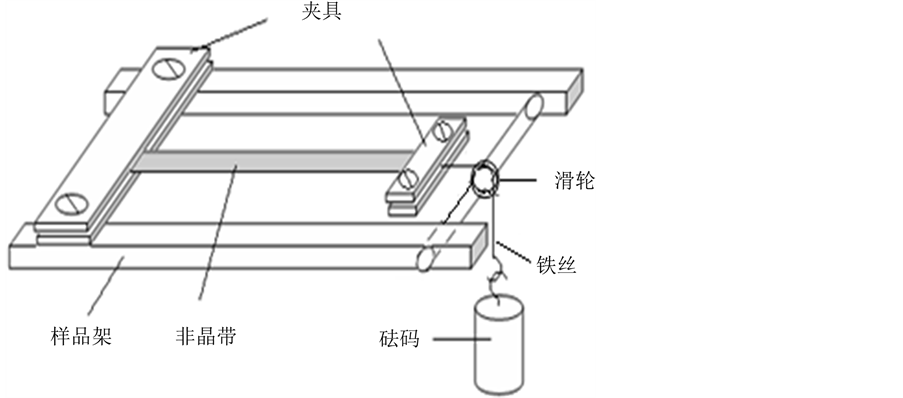
Figure 1. Curve: device of stress annealing
图1. 应力退火装置示意图
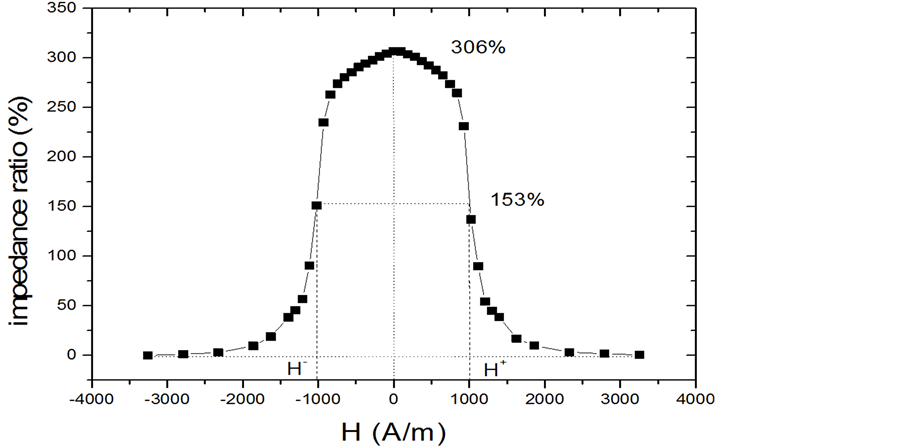
Figure 2. Curve: after annealing of Fe73.5Cu1Nb3Si13.5B9GMI curve and theory of the magnetic anisotropy
图2. Fe73.5Cu1Nb3Si13.5B9退火后GMI曲线图及各向异性场计算原理
可以看出多次回火后磁各向异性场趋于稳定。图6是回火四到六次的磁各向异性场的变化曲线,其变化规律经过线性拟合后符合
;图7是回火六到十三次的磁各向异性场的变化曲线,其变化规律经过线性拟合后符合
,从以上两个变化规律发现前六次回火磁各向异性场减小呈现一个规律,后几次回火磁各向异性场变化很缓慢。样品14次回火后磁各向异性场剩余27%。
图8是样品的宏观伸长量随回火次数的变化曲线,其中N为零的点是样品经过退火后的伸长量,样品经过退火后伸长了5.4%。图9是样品回火的收缩量随回火次数的变化曲线,回火第一次后样品的回缩了0.1%,回火第两次后回缩了0.02%,回火第三次后样品回缩了0.015%,回火第四次后样品回缩了0.01%,回火第五次后样品不再回缩。
所以为了提高软磁器件的性能,应采用叠片式非晶磁环。图10是非晶态叠片式磁环和盘绕式磁环的
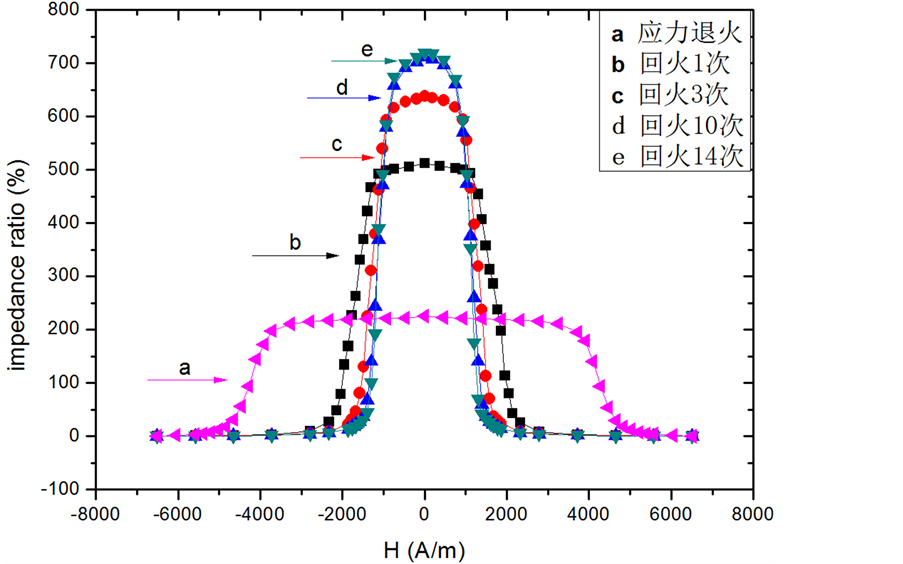
Figure 3. Curve: Fe73.5Cu1Nb3Si13.5B9 annealing and several typical tempering GMI curve
图3. Fe73.5Cu1Nb3Si13.5B9退火以及几种典型回火过程的GMI曲线
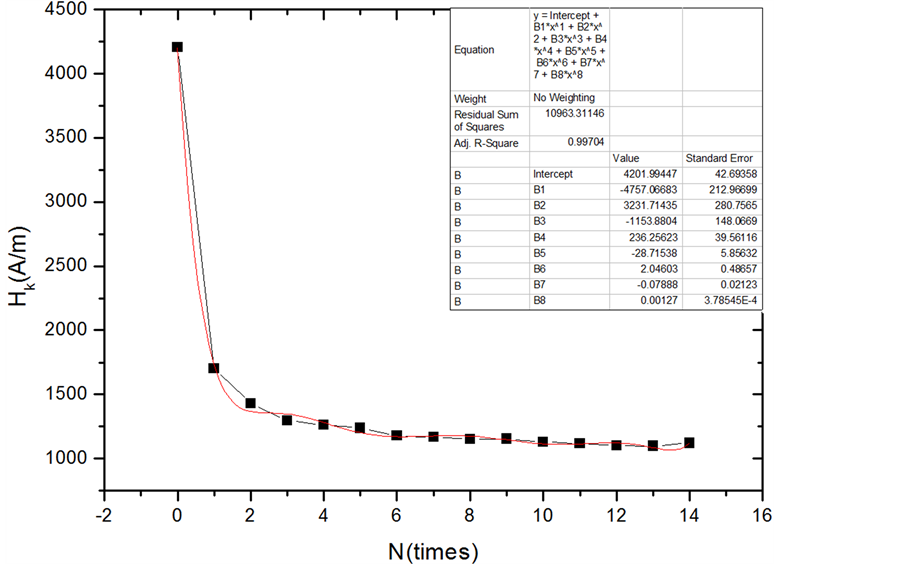
Figure 4. Curve: the magnetic anisotropy field and times of tempering
图4. 回火次数与磁各向异性场的关系曲线
磁导率随频率的变化曲线,l是叠片式磁环的磁导率随频率的变化曲线,c是盘绕式磁环的磁导率随频率
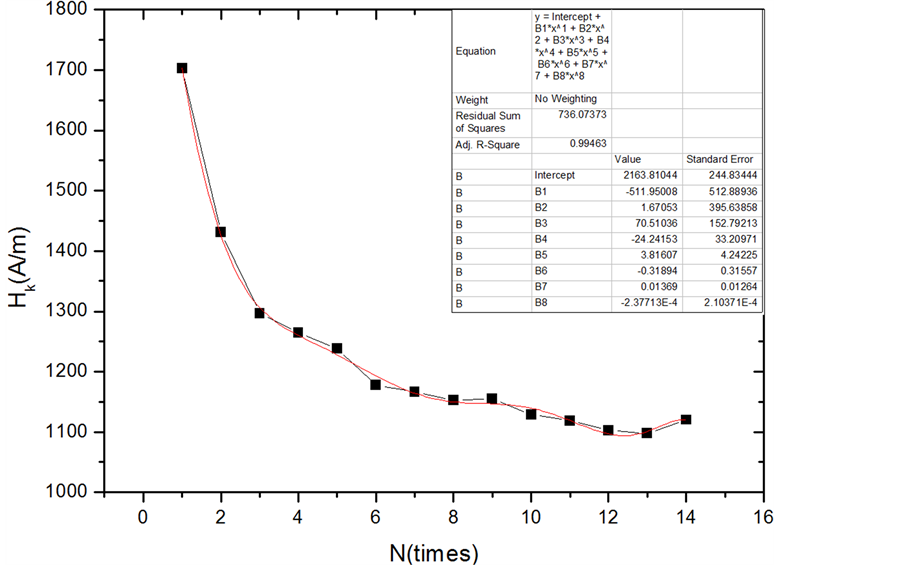
Figure 5. Curve: the magnetic anisotropy field and times of tempering
图5. 回火次数与磁各向异性场的关系曲线
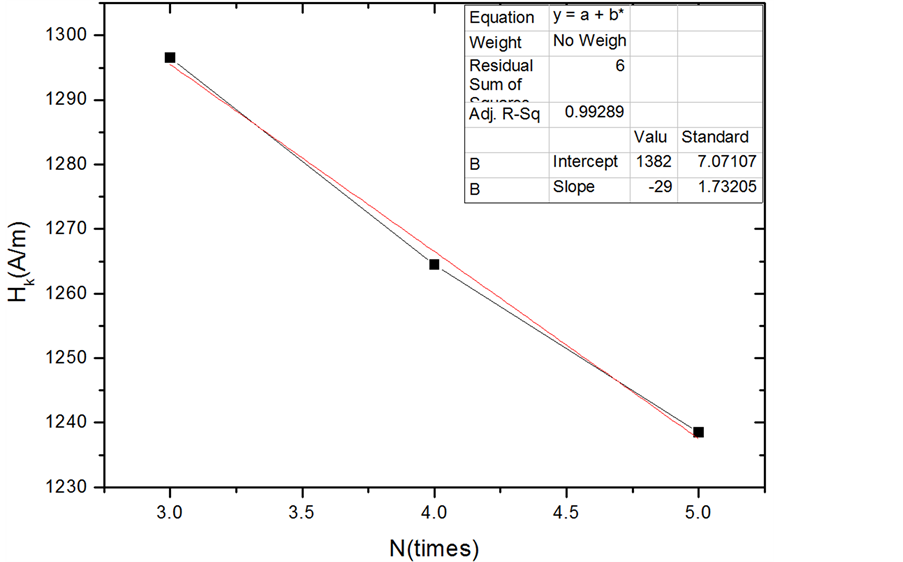
Figure 6. Curve: the magnetic anisotropy field and times (three to five) of tempering
图6. 回火次数(3~5)与磁各向异性场的关系曲线
的变化曲线,从图中看出,非晶态叠片式磁环的磁导率高于非晶态盘绕式磁环的磁导率 [11] ;图11是叠
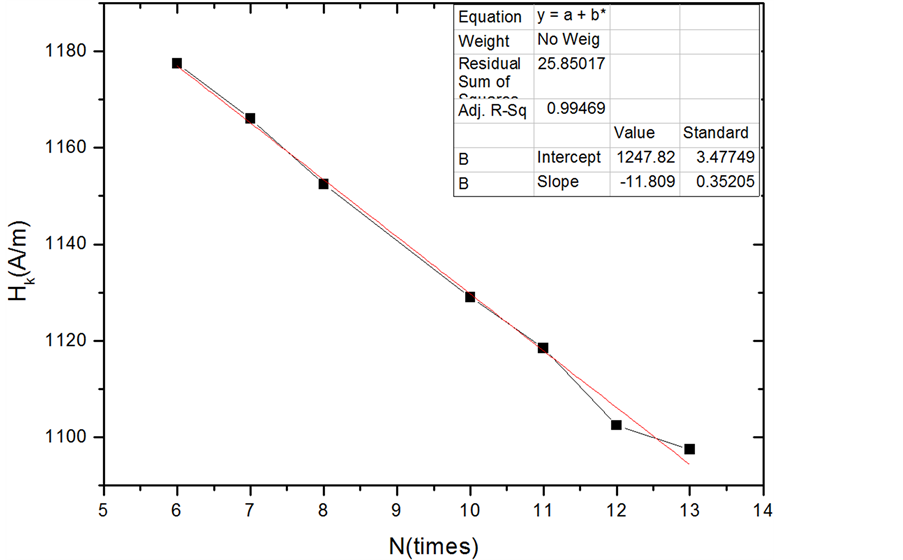
Figure 7. Curve: the magnetic anisotropy field and times (six to thirteen) of tempering
图7. 回火次数(6~13)与磁各向异性场的关系曲线
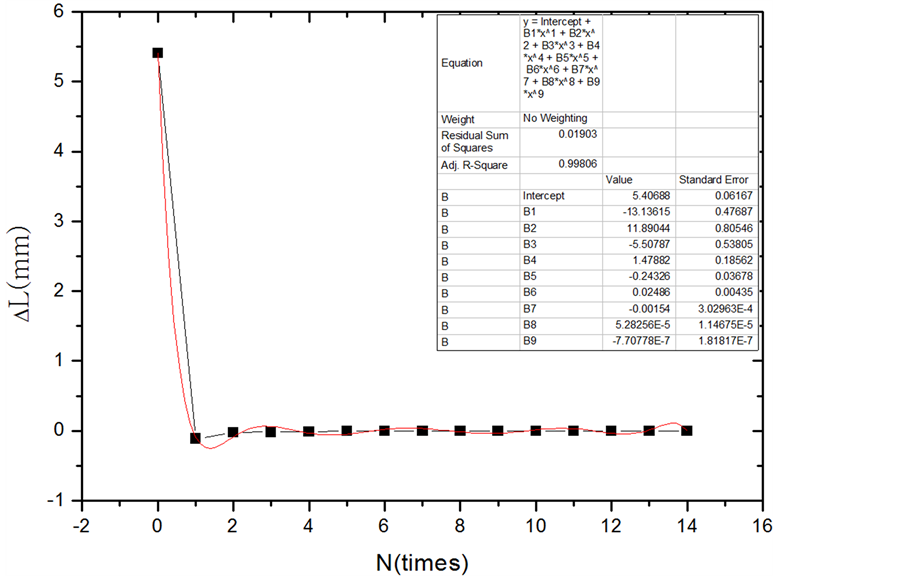
Figure 8. Curve: the elongation and times (three to five) of tempering
图8. 应力退火及回火次数与伸长量的关系曲线
片式和盘绕式磁环经过热处理后的磁导率随频率的变化曲线,l是经过热处理后叠片式磁环的磁导率随频
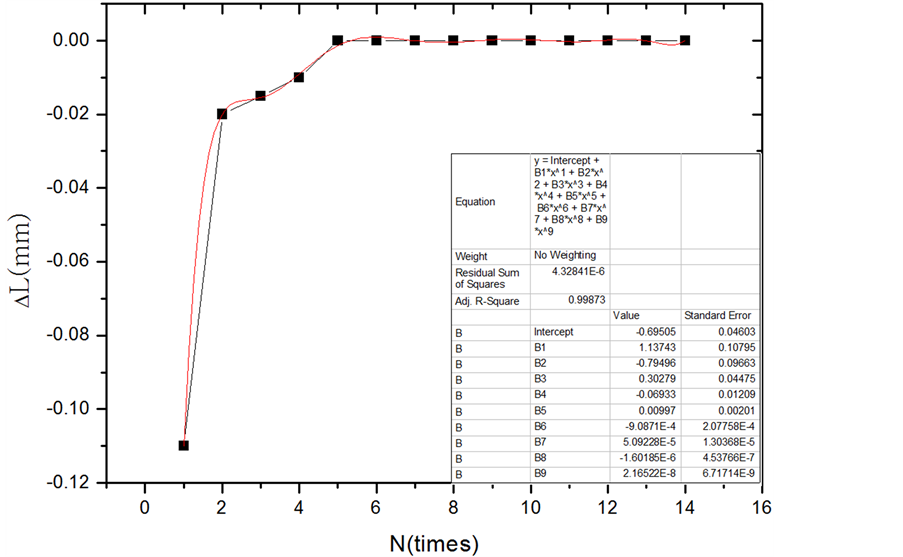
Figure 9. Curve: the elongation and times (three to five) of tempering
图9. 回火次数(3~5)与伸长量的关系曲线
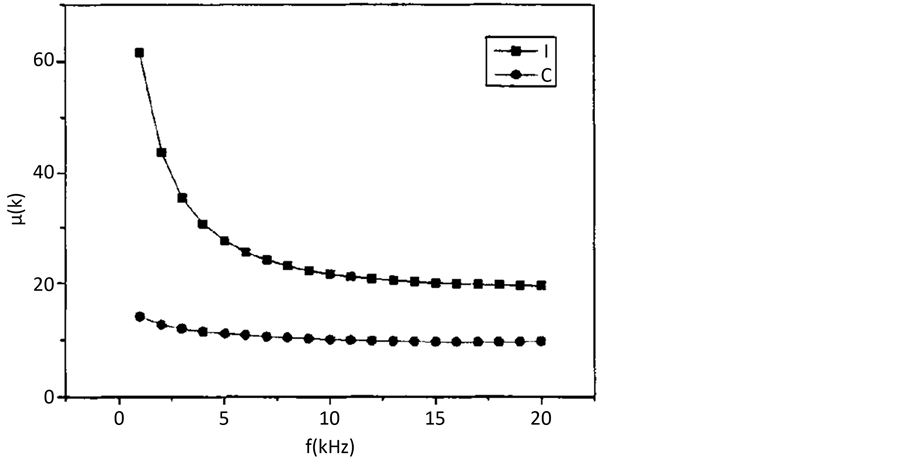
Figure 10. Curve: change of magnetic permeability of the two cores with frequency variation
图10. 两种磁环的磁导率随频率的变化曲线
率的变化曲线,c是经过热处理后盘绕式磁环的磁导率随频率的变化曲线,由图可以看出经过热处理后的叠片式非晶磁环的磁导率明显高于盘绕式磁环的磁导率。叠片式的饱和磁感应强度、磁导率均高于盘绕式磁环,叠片式磁环的矫顽力、损耗均低于盘绕式磁环。所以非晶态和退火态的叠片式非晶磁环性能优于盘绕式磁环。
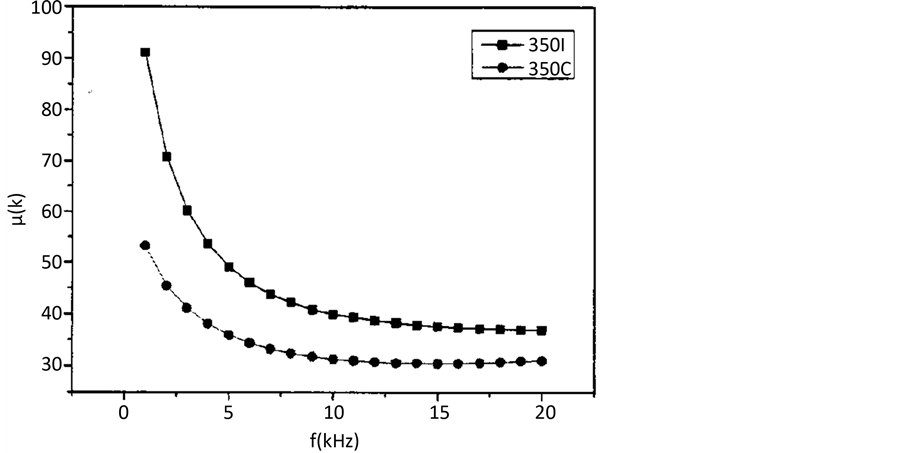
Figure 11. Curve: the magnetic permeability of laminated and coiled core annealed
图11. 经退火后的叠片式与盘绕式磁环的磁导率两种磁环的磁导率随频率的变化曲线
4. 结论
Fe基合金薄带经电流应力退火后感生显著的磁各向异性场,采用相同的退火电流对经电流应力退火的样品进行回火只能消除部分感生的磁各向异性场,难以完全消除,经10次以上回火样品的感生磁各向异性场趋于稳定,不再随回火次数的增加而下降,仍残余27%。这是导致盘绕式磁环的性能不如叠片式磁环的性能的主要原因,是导致非晶软磁器件性能提升难以达到理论预期的重要原因。本研究结果表明,现行采用退火手段消除非晶软磁器件制造过程中引入应力的做法,不够科学。本研究结论对于非晶软磁器件的性能提升具有重要指导意义。
基金项目
国家重点基础研究发展计划(973计划) 2012CB825705;浙江省重点科技创新团队2011R50012;浙江省自然科学基金项目LY14A040003。