1. 引言
传统生物柴油生产过程中会产生大量副产物甘油,甘油自身价格低廉,且其分离和精制技术目前仍存在成本高、工艺复杂和耗能大等问题 [1] [2] ,因此将甘油转化为高附加值的化学品 [3] ,可有效提高其经济效益,同时对生物柴油产业的发展具有重要意义。
碳酸甘油酯作为甘油的一种衍生物,由于无毒、低蒸发率、低可燃性和保湿能力强等优越性能 [4] ,使得它在涂料、胶黏剂、润滑剂及其个人护理和医药等领域有着广泛应用 [5] [6] 。目前从甘油出发合成碳酸甘油酯主要有四类方法:光气法、羰化法、氨酯法和酯交换法 [7] 。光气法具有温度低、转化率高、选择性好等优点,但以剧毒的光气为原料合成碳酸甘油酯,一方面对环境污染严重,另一方面危害人体健康;羰化法可以分为一氧化碳氧化羰化法和二氧化碳羰化法,其中一氧化碳活性较高,但一氧化碳有毒且操作存在一定的安全隐患,二氧化碳羰化法是环境友好的反应,但受热力学限制存在产率低、催化活性差的问题,即使以超临界二氧化碳作为反应物,最高产率仅能达到32% [8] ;氨酯法产率高、产物易分离,但对反应装置和设备要求高;酯交换法包括直链碳酸酯法和环状碳酸酯法,直链碳酸酯法中最典型的是碳酸二甲酯法,该法原料环保易得,反应条件温和,对设备要求低,副产物易分离,现阶段以酯交换法合成碳酸甘油酯的研究最为广泛,是当前最为绿色环保、经济的方法之一 [9] 。
碱催化酯交换法制备碳酸甘油酯国内外已有许多报道 [10] [11] 。非均相固体碱催化与均相碱催化酯交换反应相比,能够较好地解决催化剂与产物分离的问题,工艺流程相对简单且对环境污染较少,催化剂可以重复利用,具有较好的工业化前景。其中,碱土金属的氧化物是一类有工业应用价值的固体碱催化剂。最近以CaO固体碱催化酯交换反应的研究相当活跃 [12] [13] ,因具有较高碱性、无毒性、廉价易得、在有机物中溶解度低等优点,成为酯交换反应催化剂的研究热点。
本文以CaO为催化剂,将其用于非均相体系制备碳酸甘油酯,考察了催化剂制备条件和碳酸甘油酯合成条件对CaO催化性能的影响。
2. 实验部分
2.1. 原料与仪器
碳酸二甲酯(DMC),分析纯,成都市科龙化工试剂厂;丙三醇,分析纯,天津市科密欧化学试剂有限公司;无水乙醇,分析纯,天津市河东区红岩试剂厂;氧化钙,分析纯,国药集团化学试剂有限公司;碳酸甘油酯,纯度90%,临沂中通科技有限公司。
GC-2000气相色谱仪,聚光科技杭州股份有限公司;DF-101S恒温加热磁力搅拌器,郑州科丰仪器设备有限公司;SC-03低速离心机,安徽中科中佳科学仪器有限公司。
2.2. CaO固体碱催化剂的制备
将100~200目市售氧化钙在高温下于马弗炉中焙烧6 h,放入干燥皿中备用。
2.3. 碳酸甘油酯的制备
按一定摩尔比将甘油、碳酸二甲酯和无水乙醇加入带有回流装置的100 mL三口烧瓶,充分搅拌后水浴恒温反应,在相应时间间隔取样,将样品离心除去催化剂,并通过气相色谱仪对样品进行分析。以正丁醇为内标物、无水乙醇作为溶剂,采用内标法对产物碳酸甘油酯进行定量分析。色谱分析条件为:DB-WAX型毛细管柱(30 m × 0.32 mm × 0.25 mm);载气为N2,流量20 mL/min;分流比30:1;气相色谱进样口温度为250℃,FID检测器温度为300℃,进样量1 μL。
2.4. 反应原理
甘油与碳酸二甲酯酯交换反应制备碳酸甘油酯的反应方程式如下:

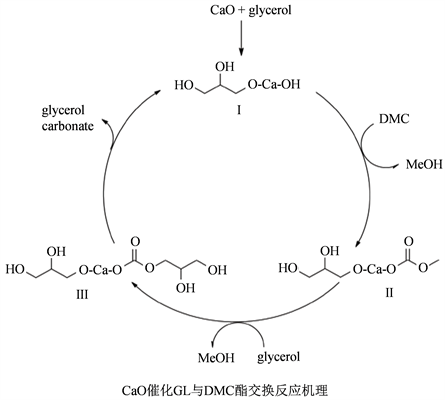
3. 结果与讨论
3.1. 反应温度对碳酸甘油酯产率的影响
由于该反应为吸热反应,因此反应温度的高低直接影响反应速率 [14] 。本文以900℃焙烧6 h的CaO为催化剂,乙醇为助溶剂,在n(甘油):n(DMC)为1:1,催化剂用量为5% (基于甘油质量)的反应条件下,考察反应温度对碳酸甘油酯产率的影响,结果如图1所示。
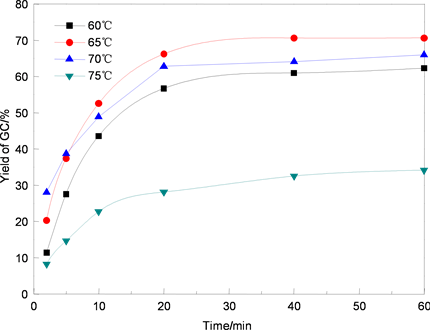
Figure 1. Effect of temperature on the yield of glycerol carbonate
图1. 反应温度对碳酸甘油酯产率的影响
由图1可知,当反应温度从60℃升高至65℃,碳酸甘油酯产率明显从62.64%提高到70.61%;继续升高反应温度,碳酸甘油酯产率反而下降,造成上述变化现象的原因主要是由于反应温度过高会加剧DMC汽化,减小了DMC在反应体系中的浓度,不利于反应正向进行。因此,实验确定最佳反应温度为65℃。
3.2. 催化剂用量对碳酸甘油酯产率的影响
在酯交换反应中,活性中心位数量很大程度上取决于催化剂用量 [15] 。若增大催化剂用量,不仅为反应物提供较大的接触面积和更多的活性中心,同时也使反应原料扩散到催化剂表面的距离减小,传质阻力相应减小,反应达到平衡需要的时间缩短,产率提高。在n(甘油):n(DMC)为1:1,反应温度为65℃条件下,以900℃焙烧6 h的CaO为催化剂,乙醇为助溶剂,考察催化剂用量对碳酸甘油酯产率的影响,结果如图2所示。
由图2可知,碳酸甘油酯的产率随催化剂用量增加呈先增大后降低的趋势,催化剂用量为5%时碳酸甘油酯的产率达到70.61%。由此说明,催化剂用量过低时,不足以提供足够的活性位点 [16] ,导致碳酸甘油酯产率较低;当催化剂用量过大时,催化剂的活性组分CaO会和甘油生成甘油钙 [17] ,同时催化剂浓度过大会增加传质传热阻力,从而使催化剂的活性显著降低。此外催化剂用量过大,也会导致反应体系黏度增加甚至最终形成凝胶而不利于产物的分离 [18] 。因此,选择催化剂的最佳用量为5%。
3.3. 甘油与DMC摩尔比对碳酸甘油酯产率的影响
甘油与DMC摩尔比是影响酯交换法制备碳酸甘油酯的重要因素之一。对于该酯交换反应,甘油与DMC摩尔比理论计量为1:1,因酯交换反应为可逆反应,过量的DMC可以促进反应向正方向进行,有利于产率的提高。因此,通常通过在反应过程中加入过量DMC来提高碳酸甘油酯产率。
反应物摩尔比对碳酸甘油酯的产率影响如图3所示。在反应温度65℃、催化剂用量5%、煅烧温度900℃的条件下,随着甘油与碳酸二甲酯摩尔比的增大,碳酸甘油酯产率先增大后减小,当n(甘油):n(DMC)为1:3时产率达到最大。因为加大DMC用量能够提升反应物的浓度和传质速度,有助于甘油的转化,但反应物摩尔比增加到一定程度后对正反应的推动作用越来越小 [19] 。此外,DMC的用量过大还会增加成本,且过量的DMC会导致其他副反应的发生。因此,实验选择最佳甘油与DMC摩尔比为1:3。
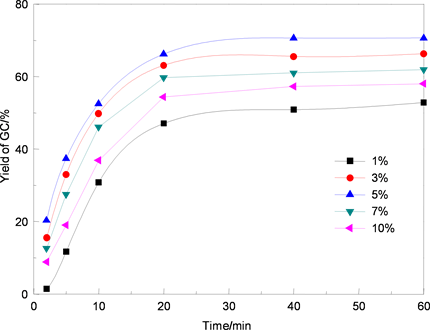
Figure 2. Influence of catalyst dosage on the yield of glycerol carbonate
图2. 催化剂用量对碳酸甘油酯产率的影响
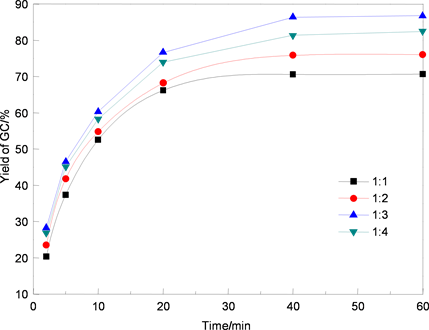
Figure 3. Influence of n(glycerol):n(DMC) on the yield of glycerol carbonate
图3. 甘油与DMC摩尔比对碳酸甘油酯产率的影响
3.4. 焙烧温度对碳酸甘油酯产率的影响
钙基固体碱催化剂在存放过程中易碳酸盐化和吸潮水解在其表面生成CaCO3和Ca(OH)2,减小了CaO表面碱性位点,使其催化活性降低,另一方面,生成的碳酸钙和氢氧化钙还会阻碍CaO活性组分与反应物的接触使其催化活性下降 [20] 。在CaO催化剂的制备过程中,高温焙烧有利于使其表面更多的活性位点重新暴露出来,提高其催化剂酯交换活性。
由图4可以看出,随着焙烧温度由500℃升高到900℃,CaO的催化活性先升高后降低,当焙烧温度为800℃时,碳酸甘油酯产率达到最大值87.02%造成上述变化规律的主要原因是由于高温作用下,CaO表面的Ca2+-O2−形成了良好的协同作用 [21] ,焙烧温度过低不足以使其表层的碳酸盐和氢氧化物分解;而
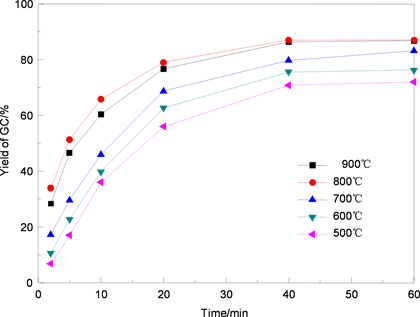
Figure 4. Effect of the calcination temperature on the yield of glycerol carbonate
图4. 焙烧温度对碳酸甘油酯产率的影响
过高的焙烧温度将造成催化剂表面烧结、比表面积下降,使参与反应的活性点数量减少,从而导致催化剂活性降低。因此,800℃为制备CaO催化剂的适宜焙烧温度。
4. 结论
CaO 催化剂能很好地催化甘油和碳酸二甲酯非均相体系制备碳酸甘油酯。在焙烧温度为800℃时,该固体碱催化剂在反应温度65℃、n(甘油):n(DMC)为1:3、催化剂用量5%的条件下,催化反应1 h碳酸甘油酯产率可达87.02%。
基金项目
2016年陕西省大学生创新创业训练计划项目“复合固体碱催化制备碳酸甘油酯”。