1. 引言
设计六西格玛(DFSS)是在低成本的情况下,满足客户对产品质量和性能的期望,致力于设计质量的一种工程开发过程 [1] 。目前,我国已经是汽车产销大国,汽车产品创新不仅仅是当今汽车市场竞争的核心,更是我国从汽车大国走向汽车强国的保证。顾客的需求和国家法规的要求是汽车设计创新的原动力,而DFSS正是以顾客需求为中心,是汽车产品设计过程及稳健性开发的方法论 [2] 。
质量管理专家ASI的乔杜里先生提出的IDDOV流程 [3] ,即识别机会(Identify Opportunity)、界定需求(Define Requirements)、概念设计(Develop Concepts)、优化设计(Optimize Design)、验证设计(Verify Performance),是大家公认的适用于制造业的六西格玛设计流程。IDDOV流程中兼顾各种工具的运用,比如质量屋(QFD) [4] [5] ,创造思维和发明工程方法(TRIZ) [6] [7] ,田口方法 [8] 等。
本文运用IDDOV六西格玛设计流程开发出一款车载电子设备管理机构,从收集客户声音开始,运用质量屋识别客户需求,头脑风暴产品概念并用Pugh工具对概念进行选择,优化设计、最终设计出满足顾客需求且性能稳健的车载电子设备管理机构。
2. 车载电子设备管理机构开发过程
2.1. 识别机会
识别机会是DFSS的第一阶段,主要任务是寻找项目机会、确定项目目标及范围、组建项目团队,制定项目计划等。近年来,触屏、通讯和处理技术的发展,手持电子设备日新月异,但在乘用车上,没有合适的装置来存储和管理电子设备,驾驶员和乘客需要在车内合适的位置设计开发出车载电子设备管理机构,实现对电子产品的使用、存储和充电功能,更好的实现人机交互,所以创建了车载电子设备管理机构开发项目,项目团队包括创新、工业设计、产品开发、人机工程及DFSS主黑带。
2.2. 定义需求
定义需求是DFSS的第二阶段,此阶段的主要任务是了解客户声音(VOC)、确定客户需求。收集VOC,主要用于开发产品概念,确定噪音因子,不仅需要关注客户对产品本身的评价及需求,也要关注客户使用产品所处的环境。项目成员在某大型停车场搜集了50个样本,其中38名驾驶员或乘客认为有必要在车内增加车载电子设备管理机构,占76%。对其产品功能和使用位置等需求进行了调查,结果表明:客户期望车载电子设备管理机构的功能是管理不同尺寸的电子产品、可视性好、拿取方便,而最受欢迎的位置为仪表板中控及副板区域(图1)。
(a)
(b)
Figure 1. Market research (a) Product functions; (b) Product position
图1. 市场调查(a) 产品功能;(b)产品位置
此阶段的第二个主要任务是将VOC转化成工程语言,通过QFD将VOC逐层展开为设计和顾客关键需求,准确的识别、量化顾客需求并针对需求进行产品设计,最终制定出产品的设计方案和工艺要求 [7] 。对于车载电子设备管理机构开发项目,将收集的VOC进行归类和处理,利用QFD提炼客户需求并将需求转化为具体可量化的工程要求。由QFD分析过程(表1),客户对车载电子设备管理机构的最基本的功能需求为,能够管理不同型号的电子产品,并且在驾驶员或乘客使用的过程中,保持良好的视角和人机交互性。
2.3. 概念开发
DFSS的第三阶段是概念开发,此阶段的主要任务是找到最佳概念,满足客户需要的潜在产品功能,主要包括三部分:a) 定义产品需要实现的功能;b) 创建数量众多的想法或模型实现产品功能;c) 选择最佳的想法或概念,在下一阶段进行优化。对产品进行概念收集,可以采用头脑风暴、TRIZ、6-3-5 brain writing、矩阵法等等,重要的原则是:想法越多越好且好坏兼容。概念收集后,用普氏概念分析法(Pugh)进行概念选择、创新与改进。根据上一阶段定义的产品需求目标,第二次Pugh的选择结果如表2。其中“+”代表功能优于对标件,记为5分,“-”代表功能劣于对标件,记为1分,“S”与对标件功能相似,记为3分。
通过Pugh对收集的概念进行选择,综合考虑产品的功能、成本和制造等因素,团队成员对各概念进行对比和评分,概念4因产品结构简单,可操控性强,成本低,能够实现手机等电子设备的可视、存储、充电等功能,与仪表板及副板能较好的集成,评分最高,最终确定为车载电子设备管理机构的开发方案。概念4由电子设备夹持机构、双滑轨机构、阻尼器/齿条、缓冲器等辅助部件组成。其中最核心的结构为双滑轨机构,它能够利用最小的滑道空间,完美的实现预先给定的轨迹(图2);夹持机构由支架系统,动力系统组成;滑轨连杆机构由滑道、连杆和销轴等组成。
2.4. 优化设计
完成概念设计后,进入IDDOV的第四步:优化设计。优化设计就是稳健性设计,是六西格玛设计的精髓。此阶段对产品和过程设计参数进行优化,其目标是在质量、成本和交付时间允许的基础上达到企业利益的最大化,同时使系统本身具有抵抗各种干扰的能力,即使用环境恶劣或者操作不当,系统仍能满足客户需求。优化设计阶段依次为定义目标、建立理想函数、噪声因子策略、控制因子策略、水平&正交矩阵、实验&数据收集、数据分析、预测&验证。
表1. 质量屋分析
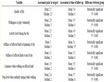
Table 2. The second turn Pugh analysis
表2. 二次Pugh选择分析
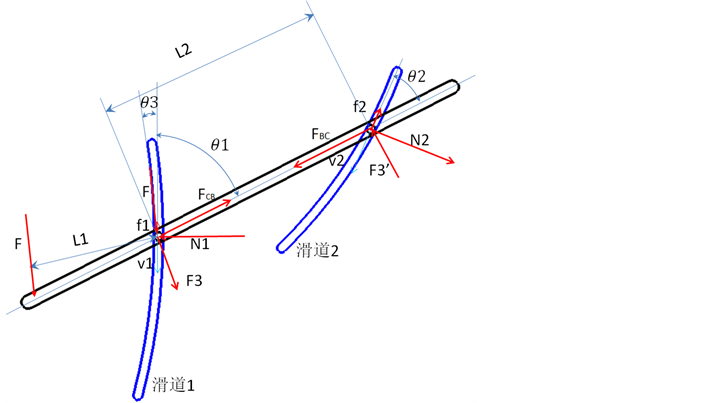
Figure 2. Double slide rail mechanism schematic diagram
图2. 双滑轨机构示意图
2.4.1. 定义目标&范围(Scope & Objective)
优化设计第一步为确定产品研究范围。与DFSS第一阶段任务确认研究范围不同,此阶段的产品研究范围限定于所优化产品。定义研究范围的准则为:a) 基于输入信号,能量转换和输出相应结果;b) 系列设计参数(建议8个以上)。结合产品设计目标和设计方案,从结构和功能两方面来定义产品研究的范围。如图3所示,把系统拆分为三个层次:系统、子系统和部件(图3(a)),对应的功能域也对应分为三个层次:系统功能、子系统功能和部件功能(图3(b))。把与设计目标相关的部件定义在研究范围内,与设计目标无关的部件定义为非研究范围。通过分析,支撑机构为非研究范围,其余为研究范围。
2.4.2. 建立理想函数(Ideal Function & Signal Strategy)
所谓理想函数是基于设计目的,建立系统输入和输出之间的需求关系。理想方程代表着理想状态的系统,一般来说是不能实现的。本研究定义的理想方程输入为功,输出是位移,如图4。
2.4.3. 噪声因子策略(Noise Strategy)
所谓噪声因子是在设计过程中,工程师无法控制或者需花费很大代价控制的,但又必须考虑的因素。常见的噪声因子有温度变化、产品老化,人的操作习惯等。信噪比(S/N)是用来描述产品抵抗内/外干扰因素所引起的质量波动的能力,信噪比越大表示产品越稳健。公式中方差σ2越小,S/N越大;特性值y越大,S/N越大 [9] 。
(1)
对于车载电子设备管理机构,共头脑风暴出8种噪音,最终选择影响较大的3种噪音因子作为研究对象,见表3。其中N1为在噪音因子最差参数时最低输出;N2为噪音因子最佳参数时最佳输出。
2.4.4. 可控因子策略
控制因子是可能影响操作力的因素,并且是在设计过程中可以控制的,将可控因子归纳到表4中。
(a)
(b)
Figure 3. Product scope (a) Physical domain; (b) Functional domain
图3. 产品范围,(a)结构域;(b)功能域
表3. 噪音因素表
表4. 可控因子表
2.4.5. 实验设计(Run Experiments/Collect Data)
根据已经定义的噪音因子和控制因子,将可控因子表作为内表,噪声因子表作为外表,建立L18(2^1 3^5)正交矩阵表(表5)。对每一组数据创建CNC模型进行力和位移的测试,从位移与力的关系曲线,提取数据。
2.4.6. 数据分析(Analyze Data (S/N, β))
根据测试结果,可以计算出信噪比(S/N)和理想斜率函数(β),根据公式2进行计算:
(2)
其中,r为输入平方和,
为最佳拟合线上各点的平方和,
为噪音的方差,
根据公式,计算结果如表6。
2.4.7. 预测和确认(Predict & Confirm)
根据表6的数据,分别计算可控因子A-F在不同水平下的理想斜率函数(β)和信噪比(
),以A为例进行计算,可控因子A在水平1时的理想斜率函数:
表5. 正交矩阵表
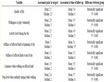
Table 6. Characteristic value and S/N
表6. 特性值和信噪比
(3)
可控因子A在水平1时的信噪比:
(4)
同理求解可控因素B-F在不同水平下的理想斜率函数(β)和信噪比(SN),总结于表7和表8。
将表7和表8的数据生成响应图,如图5。
从理想斜率函数(β)方面进行判断,结合表7的排序和图5各因子不同水平点的分散情况,可以看出因素D、E影响最大,从信噪比(SN)方面进行判断,结合表8的排序和图5各因子不同水平点的分散情况,可以看出因素A、B、C、F影响最大,综合考虑信噪比和理想斜率函数,最终确定的优化组合为A1,B3,C3,D1,E1,F1。根据表7和表8中信噪比的平均值,预测优化组合的理想斜率函数值(
)和信噪比(
),计算结果如下:
(5)
(6)
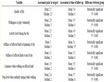
Table 7. Different Control factors β
表7. 可控因子不同理想斜率函数
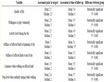
Table 8. Different control factors S/N
表8. 可控因子不同水平信噪比
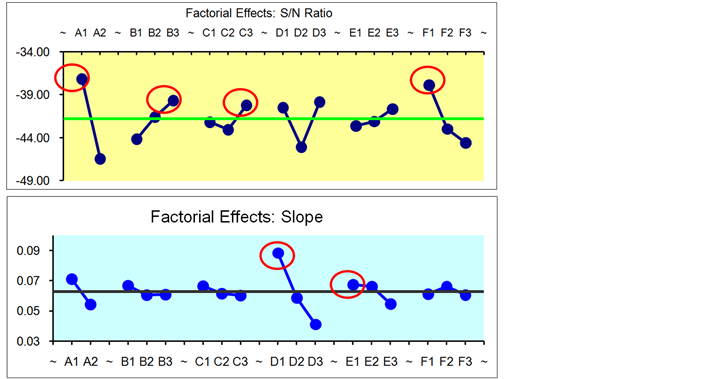
Figure 5. Response plot of control factors S/N and β value
图5. 可控因子信噪比和理想斜率函数 + 响应图
2.5. 结果验证
根据优化的组合,重新设计车载电子设备管理机构,并进行验证试验,将模拟值与预测值作对比,以确认预测值的准确性。将预测和验证结果总结于表9,可以看到,优化设计后理想斜率函数β验证值和预测值相差0.024,信噪比相差4.78,两者接近,预测结果可信。优化设计后,S/N比原设计提高了8.84 dB,将其带入公式7,计算出车载电子设备管理机构的系统稳健性提高了64%。按照优化后的数据重新制作产品模型(图6),并对其力和位移的测试,由图7可以直观的看到优化前后产品稳健性的提高。
表9. 确认表
图6. 优化后产品模型
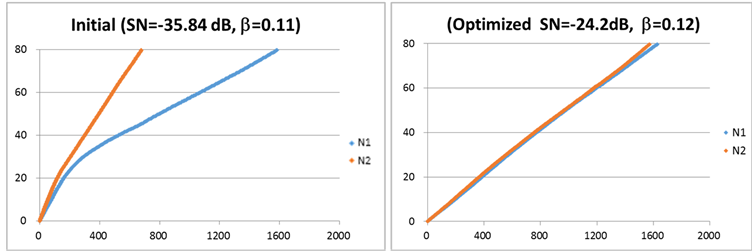
Figure 7. Test and calculate result comparison between initial and optimized design
图7. 产品优化前后测试与计算结果对比
(7)
3. 结论
本文通过市场调查,建立车载电子设备管理机构开发项目和团队,定义项目目标及研究范围。运用客户声音、质量屋工具识别客户需求。基于客户需求,头脑风暴产品概念并用Pugh工具对概念进行选择,最后选择布置于仪表板和副板过渡区域的概念4为研发目标。在优化设计阶段,进一步定义产品研究目标和范围,建立理想方程,查找噪音及可控因子,进行田口实验及大量数据分析,最后找到最优化的产品参数组合,优化后产品的系统稳健性提高了64%。
本文运用设计六西格玛IDDOV流程开发了满足客户需求的车载电子设备管理机构,实现了产品的正向开发和稳健性设计。实践证明DFSS是一整套强大的设计质量控制工具和宝贵的思维方式,企业想拥有自己的核心产品,提升市场竞争力和影响力,就应该鼓励广大研发人员学习和掌握DFSS工具,在日常的开发中灵活应用。