1. 引言
汽车副车架是悬挂与车架之间的一个过渡构件,悬挂系统作为一个整体安装在副车架上,然后与车身相连,形成一个完整的系统。副车架的存在可以消除来自车轮和发动机的振动和噪声,使得只有少部分的振动和噪声能够传入车厢,提升了车辆的舒适性与操控性。
近些年来各个国家对于汽车安全性的要求日益严格,为了满足相关的法规要求,必须对副车架的相关性能特别是疲劳及可靠性进行研究 [1] 。通过副车架CAE技术与台架试验,对副车架研发具有重要的现实意义及应用前景 [2] [3] 。
本文搭建了疲劳试验台架,针对某款汽车前副车架进行了疲劳破坏试验,得到了局部结构不足之处,通过前后对比分析及试验验证,优化方案提高了结构刚度,能更好满足汽车悬架性能的要求。
2. 汽车前副车架疲劳台架及试验
2.1. 副车架疲劳台架
疲劳试验机由激振装置(液压泵站、液压系统及测试机架)、计算机控制系统和电气控制系统等部分组成。激振装置采用电液伺服控制驱动的液压缸,试件安装固定的试验台上,横梁式的机架安装固定激振装置,激振油缸通过其它连接装置固定在横梁上来给实践施加激振力。
疲劳试验机主要工作参数范围:激振力大小为1~35 KN,而且连续可调;最大振幅 ± 100 mm;频率范围0.1~20 Hz;如图1所示为汽车副车架的疲劳试验台架布置图。
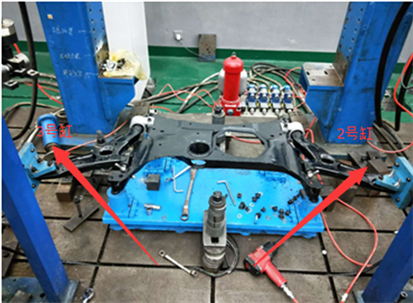
Figure 1. Layout drawing of fatigue test bench for sub frame
图1. 副车架的疲劳试验台架布置图
2.2. 副车架疲劳试验
根据图1所示疲劳试验台架布置,对2号、3号油缸进行加载试验,2号油缸的加载力是3.8 KN,频率1 Hz;3号油缸的加载力是3.9 KN,频率1 Hz。如图2所示为加载试验位移–时间曲线。
通过给定的加载,70万次约195 h时间后,副车架无明显变形以及疲劳裂纹、断裂等现象。
3. 副车架成型优化及验证
3.1. 副车架下板原结构及疲劳验证
疲劳台架实验验证,该副车架结构强度以及刚度上满足标准,达到了设计要求。但疲劳试验后,发现悬置套管一侧的平面位置有翘曲、轻微变形现象,如图3所示为优化前副车架下板结构图,如图4所示为优化前副车板下板原实物检测图。主要在于副车架下板存在面积较薄的平面区域,使得刚度下降,产生了轻微翘曲现象,有必要进行结构的优化。
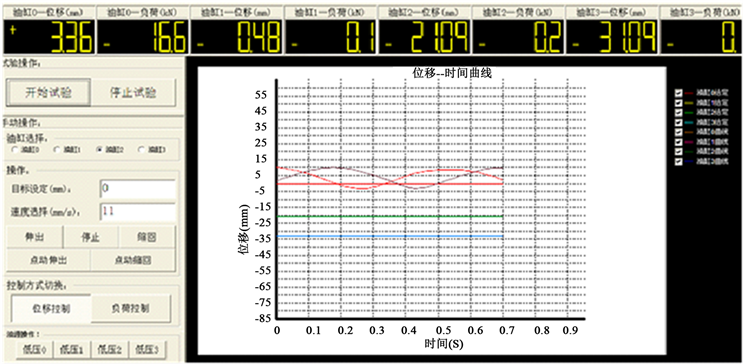
Figure 2. Displacement-time curve of loading test
图2. 加载试验位移-时间曲线
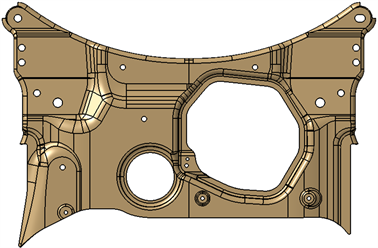
Figure 3. The structure of sub-frame lower plate before optimization
图3. 优化前副车架下板结构图
3.2. 副车架下板优化结构后及疲劳验证
如图5所示为优化后副车架下板结构图,主要结构改进在于小圆孔左上侧增加了一条冲压槽,由此增加构件刚度,减小变形。改进后的副车架,再次在疲劳试验机上进行疲劳试验,如图6所示为优化后副车板下板实物检测图,检测结果表明,构件没有发生较大翘曲变形,平面度满足了工程要求,由此提高了副车架的成型质量。
3.3. 副车架下板优化结构前后有限元应变对比分析
通过对副车架下板优化结构前后有限元应变对比分析,如图7所示为优化前副车架下板应变图,图中表明,优化前副车架下板存在回弹过大,导致尺寸不可控等现象;如图8所示为优化后副车架下板应变图,图中表明,下板尖角位置一侧的回弹有所下降,最大应变量由近4 mm减少到3 mm左右,提高了副车架整体结构刚度。
4. 结论
通过汽车前副车架进行了疲劳破坏试验,得到了局部结构不足之处,前后对比分析及试验验证,优
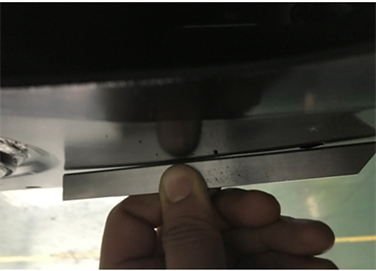
Figure 4. Physical examination of sub-frame lower plate before optimization
图4. 优化前副车架下板原实物检测图
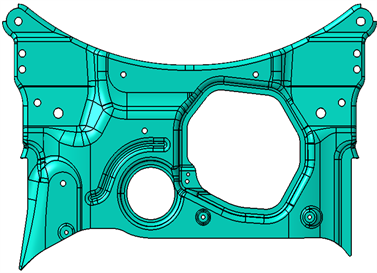
Figure 5. The structure of sub-frame lower plate optimized
图5. 优化后副车架下板结构图
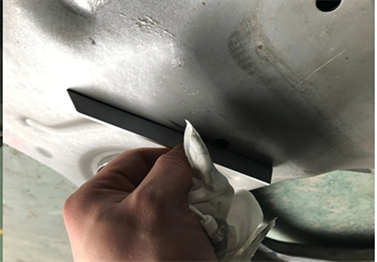
Figure 6. Physical examination of sub-frame lower plate optimized
图6. 优化后副车板下板实物检测图
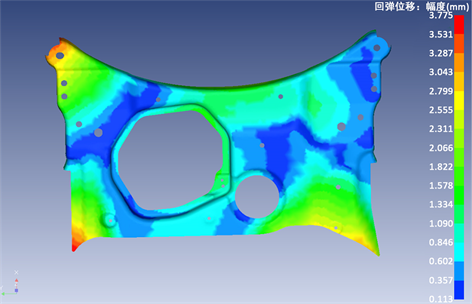
Figure 7. Strain diagram of sub-frame lower plate before optimization
图7. 优化前副车架下板应变图
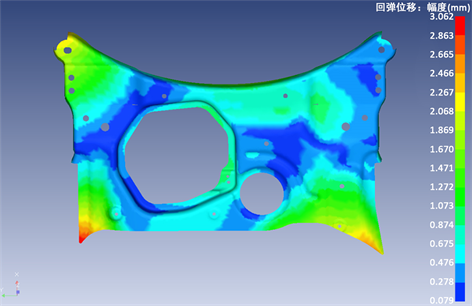
Figure 8. Strain diagram of sub-frame lower plate optimized
图8. 优化后副车架下板应变图
化方案提高了结构刚度,能更好满足汽车悬架性能的要求。
结构改进及优化后,副车架下板的回弹有所下降,结构安全性以及工艺满足要求,疲劳实验表明,经过相同条件的加载疲劳试验,没有发生疲劳破坏。