2. 物理数学模型
2.1. 物理模型
本文以我国某炼铜企业的闪速熔炼炉为原型,建立数值仿真物理结构模型。由于研究中着重关注砷元素在悬浮熔炼条件下的反应与分配行为特点,因此计算区域仅包含闪速熔炼炉反应塔、沉淀池部分气相空间以及反应塔顶部的精矿喷嘴、天然气烧嘴等,如图1所示。
2.2. 数学模型
用于描述闪速熔炼过程的数学模型有 [8] [9] :1) 通用模型:即连续性方程、动量方程、能量方程和组分传输方程;2) 湍流模型:Realizable κ-ε模型;3) 辐射模型:P1模型;4) 化学反应模型:根据对进出闪速熔炼炉的含砷炉料——铜精矿、渣精矿、吹炼渣、冰铜、熔炼炉渣等——进行了砷化学物相分析与扫描电镜分析,以及参考文献 [10] [11] 中所涉及的化学反应,主要包括颗粒表面反应和体积反应两个部分。
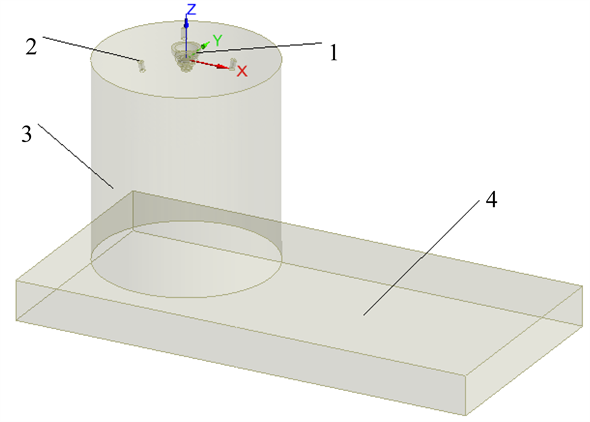
Figure 1. Schematic diagram of copper flash furnace physical model. 1-Concentrate nozzle; 2-Gas burner; 3-React shaft; 4-Gas space of settler
图1. 铜闪速炉物理模型示意图。1-精矿喷嘴;2-塔顶天然气烧嘴;3-反应塔;4-沉淀池气相空间
颗粒表面反应:
(1)
(2)
(3)
(4)
(5)
(6)
(7)
(8)
(9)
体积反应:
(10)
(11)
2.3. 定解条件
三种边界条件:1) 各气流入口均设置为质量流量入口,以某炼铜企业实际操作参数为依据,各股气流的参数如表1所示;2) 对于动量方程,计算区域内各壁面均设置为无滑移壁面,对于能量方程,壁面温度根据闪速熔炼炉炉内温度分布特点及与其接触的烟气温度进行设置;3) 烟气出口设置为压力出口,根据在线监测数据,出口处的压力设置为−42 Pa。
闪速熔炼炉投料量为60.56 kg/s,通过取样并进行相关实验分析,其配料、特征粒径、颗粒物相组成分别如表2~表4所示。
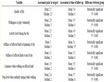
Table 1. Distribution parameters in flash furnace
表1. 闪速炉配风参数
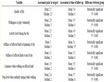
Table 2. Batching parameters and characteristic particle size in flash furnace
表2. 闪速炉配料参数及特征粒径
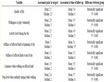
Table 3. Phase composition of concentrates and soot
表3. 精矿、烟灰的物相组成
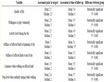
Table 4. Phase composition of slag concentrate
表4. 渣精矿的物相组成
3. 仿真结果与分析
闪速熔炼过程中,含砷物质Cu3AsS4、As2O3的反应过程及中间产物As4O6的转化过程决定着砷的分配行为,控制着砷的流向。下面将根据仿真结果对此进行逐一分析。
3.1. 气相含砷物质的反应过程
气相中As4O6和AsO的浓度分布可以清楚地反映出砷在气相空间内的转化过程,闪速炉中心对称面上As4O6和AsO的气相浓度分布如图2所示。
As4O6和AsO在炉内的总体反应过程如图3所示。根据反应速率相对大小的不同,As4O6的生成与消耗过程可以分为以下三个阶段。
1) 生成速率大于消耗速率阶段:这一过程发生在距离塔顶0.75 m的区域内,此时精矿和配风刚入炉,温度较低,主要以As4O6的生成为主,在离塔顶0.75 m处时As4O6的量到达最大值。此时,虽然精矿还未着火,但在中央天然气燃烧产生的高温区域的作用下,部分As4O6开始分解,从图3(b)可以看出,在离塔顶0.75 m处时,炉内已经生成了一定的AsO。
2) 消耗速率大于生成速率阶段:这一过程发生在距离塔顶0.75~2.5 m的区域内,伴随着精矿的着火和中央天然气的燃烧,气相的温度急剧升高,在达到分解温度后,As4O6的生成速率便将大大低于其消耗的速率。图3(a)表明在距离塔顶2.5 m时,炉内原来积累的As4O6已消耗殆尽。
3) 生成速率等于消耗速率阶段:这一过程发生在距离塔顶2.5~3.25 m的区域,此时由于精矿已经完全着火并开始燃烧,气相的温度远超过As4O6的分解温度,致使As4O6在生成的一瞬间即被分解和消耗。
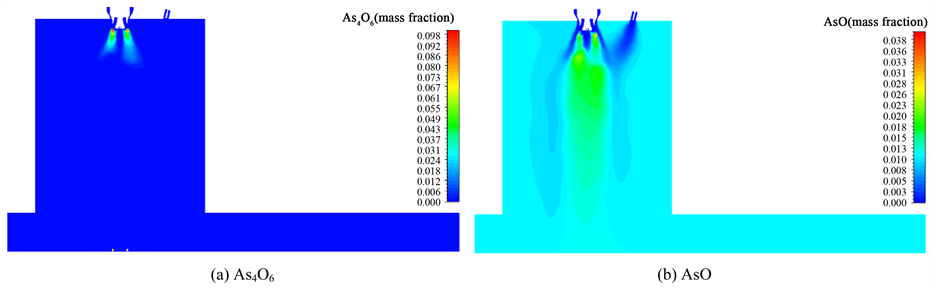
Figure 2. Distribution of gas concentration field on the symmetry plane of flash smelting
图2. 闪速熔炼炉对称面上的气相浓度场分布云图
(a)
(b)
(c)
Figure 3. The trend of As4O6 and AsO in the furnace: (a) Generation and consumption trends of As4O6 in the furnace; (b) Trend of generation of AsO in the furnace; (c) Net flow of AsO in the furnace
图3. 炉内As4O6和AsO的变化趋势:(a) 炉内As4O6的生成与消耗趋势;(b) 炉内AsO的生成趋势;(c) 炉内AsO的净流量
由图3(c)可以看出,在这一阶段由As4O6转化而来的AsO变化很小,可以认为As4O6的生成与转化过程在距离塔顶2.5 m的区域内已基本完成。
从图3(c)中可以看出,在距离塔顶2 m以内的区域,生成了超过95%的AsO,其中,距离塔顶1 m以内区域生成的AsO约占40%,距离塔顶1~2 m之间的区域生成的AsO约占60%,在距离塔顶3 m以下的区域,不再有AsO生成。据此可以推论:距离塔顶1~2 m之间的区域是生成AsO的主要区域,含砷物质的反应过程在距离塔顶3 m的位置处已基本完成。
3.2. 颗粒相含砷物质的反应过程
混合精矿中Cu3AsS4在闪速熔炼过程中化学反应如式(9)所示,其反应过程如图4(a)、图4(b)所示。从图中可以看出,精矿中的Cu3AsS4入炉后立即发生化学反应,砷以As4O6的形式进入气相,铜以Cu2S
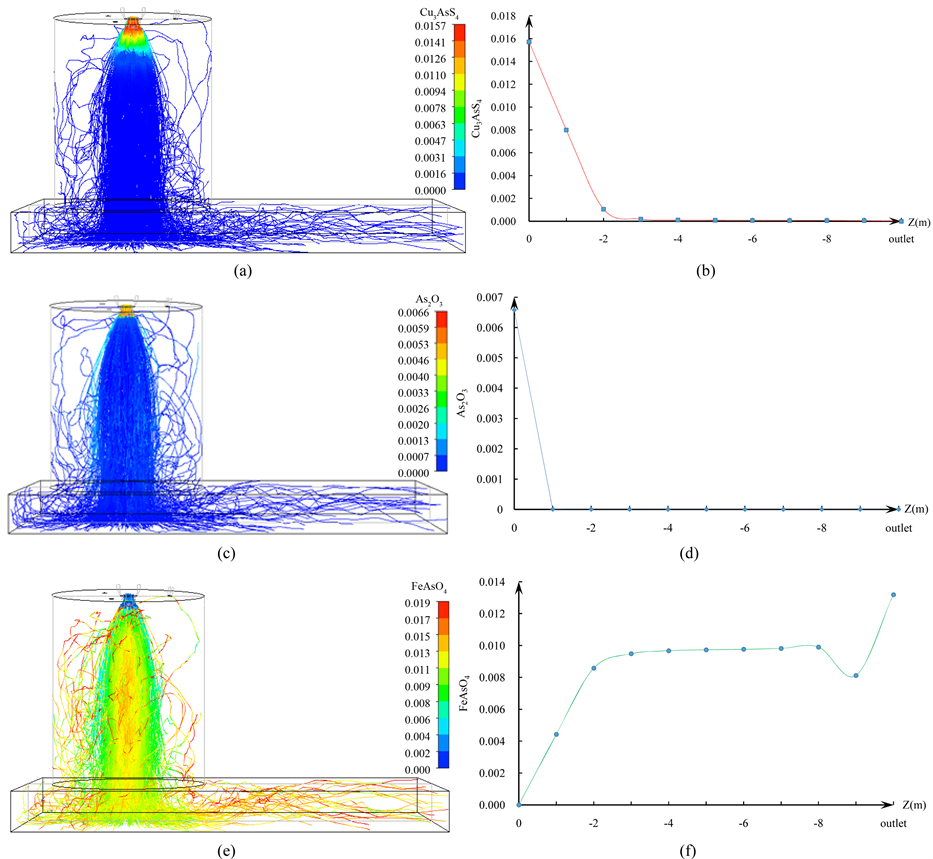
Figure 4. Reaction of Cu3AsS4 and As2O3 (a) Cu3AsS4 mass distribution in mixed concentrates and soot; (b) Variation of Cu3AsS4 mass fraction along the height of the reactor; (c) As2O3 mass distribution in mixed concentrates and soot; (d) Variation of As2O3 mass fraction along the height of the reactor; (e) Mass distribution of FeAsO4 in mixed concentrates and fly ash;(f) Variation in the mass fraction of FeAsO4 along the height of the reactor
图4. Cu3AsS4、As2O3的反应过程。(a) 混合精矿、烟灰中Cu3AsS4质量分布;(b)Cu3AsS4的质量分数沿反应塔高度的变化;(c) 混合精矿、烟灰中As2O3质量分布;(d) As2O3的质量分数沿反应塔高度的变化;(e) 混合精矿、烟灰中FeAsO4质量分布;(f)FeAsO4的质量分数沿反应塔高度的变化
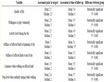
Table 5. Distribution ratio of arsenic in each phase simulated
表5. 仿真得到的砷在各相中的分配比
注e:熔体即为反应后落入沉淀池的颗粒相(精矿颗粒、烟灰、渣精矿、吹炼渣和石英)。
的形式继续存在于颗粒中;整个反应过程在精矿喷嘴附近的富氧环境下进行,在距离塔顶2 m的位置处已基本反应完全,转化过程迅速而稳定。
烟灰中的As2O3在塔内发生的化学反应如式(8)所示,转变过程如图4(c)、图4(d)所示。从图中可以看出,在炉内高温环境下,As2O3的挥发过程极为迅速,在距离塔顶1 m的位置处时已全部以As4O6的形式进入气相。
FeAsO4的生成反应如式(9)所示,生成过程如图4(e)、图4(f)所示。图4(e)表明,料柱中央的精矿颗粒FeAsO4的含量较高,而料柱外围的精矿颗粒FeAsO4的含量较低,这是因为位于塔中央的精矿颗粒更为集中,升温着火慢,粒径较小容易氧化造成的。从图4(f)可以看出:进入熔体的FeAsO4同进入气相的AsO一样,主要在距离塔顶3 m以上的区域内生成,而在3 m以下的区域,几乎不再有FeAsO4生成;精矿颗粒中FeAsO4含量的提高主要是由于精矿的进一步脱硫造成。
3.3. 砷在熔体与气相中的分布
闪速熔炼过程的数值仿真计算得到的砷在熔体及气相中的分配比例列于表5中。这里,由于烟尘随同烟气一起进入后续的工序,并不进入位于沉淀池的熔体中,因此将烟尘的带走的砷算在气相中。从中可知,在熔炼过程,最终有51.9%的砷进入熔体,48.4%的砷进入气相,而这和实际生产过程中收集的数据相符。
4. 结论
建立了描述铜闪速熔炼过程中砷分配行为数学模型,并对其进行了数值仿真,揭示了铜闪速熔炼过程中含砷物质的转化过程。主要结论如下:
1) Cu3AsS4的脱砷过程和As2O3的挥发过程都非常迅速,精矿中含砷物质Cu3AsS4的脱砷过程在距离反应塔顶3 m的区域内已基本完成,而烟灰中的含砷物质As2O3的挥发过程在距离反应塔顶1 m的区域内已基本完成;
2) 距离塔顶3 m以内的区域是调整砷进入熔体或气相比例的关键区域,闪速熔炼炉出口处砷在熔体中的分配比例为48.1%,在气相中的分配比例为51.9%。
研究尚未就砷在铜闪速熔炼过程中分配行为影响因素进行深入分析,后续将就此进行进一步研究。
基金项目
环保公益性行业科研专项经费项目(NO. 201509050)。
NOTES
*通讯作者。