1. 引言
γ-TiAl金属间化合物以其高的比强度,比模量,优异的抗疲劳性能以及耐腐蚀等优点,在航空发动机、火箭发动机和燃气轮机等领域具有广阔的应用前景 [1] [2] 。TiAl金属间化合物的弹性模量、抗蠕变性能等远远优于钛合金,与Ni基高温合金相当,但密度还不到Ni基合金的二分之一,被认为是最有工程应用潜力的新一代轻质耐高温结构材料之一 [2] [3] [4] 。2006年Ti-48Al-2Nb-2Cr合金作为一种新的轻质低压涡轮机叶片材料已经被成功地应用到了美国通用公司的商业飞机引擎上面 [5] 。另外TiAl基合金还被成功应用到了工业燃气涡轮机 [6] 和汽车发动机上面 [7] [8] 。但是常规的TiAl合金室温塑性和断裂韧性不佳,高温抗蠕变和抗氧化性能较差。为此,近年来,国内外TiAl基合金的研究中开始出现新型高熔点TiAl合金。在TiAl中添加高含量、高熔点的过渡族元素(Nb、Zr、Hf、Ta等)之后高温性能均得到了一定的提高。其中,加入高含量的Nb元素对TiAl基合金室温塑性及其他室温力学性能的提高尤为明显 [9] 。
随着TiAl基合金在航空和汽车领域应用的不断推广,TiAl基合金的耐磨性也受到了广泛的关注。近年来,人们针对微观结构 [10] ,涂层,温度 [11] ,载荷 [12] 和环境 [13] [14] 等因素对TiAl基合金的摩擦磨损性能的影响开展了广泛的研究。Rastkar [12] 等人研究了不同摩擦载荷对Ti-48Al-2Nb-2Mn和Ti-45Al-2Nb-2Mn-1B在摩擦过程中表面剥落和变形机制的影响。Qiu [14] 等人发现Ti-47Al-2Cr-2Nb-0.2W合金的磨损率对环境气氛中的氧气非常敏感,在空气中耐磨性不佳。多项研究 [12] [13] [14] [15] [16] 发现未经表面处理的TiAl基合金的耐磨性能不佳。而且TiAl基合金作为结构材料在高温下采用液体润滑进行减摩和抗磨也不易实现。目前国内外科研工作者分别采用了等离子渗碳,气体渗氮,激光处理和阳极氧化等方法来提高TiAl合金的耐磨性。但是以上工艺也存在制备成本较高 [17] ,处理强化层与基体结合强度不佳等问题。另外渗氮和渗碳常用含氢气体也容易引起TiAl合金氢脆。表面纳米化技术是近几年备受人们关注的新技术。它可以显著提高材料的力学性能和物理化学性能。其实质是在材料表面制备一层纳米层,利用纳米晶体结构的优异性能来改善材料的性能,从而达到提高材料服役行为的目的。目前实现表面自纳米化最常用方法是表面机械研磨(Surface Mechanical Attrition Treatment, SMAT) [18] 。
因此本文采用球磨工艺对Ti-47Al-2Cr-0.2Mo (at.%)和高Nb含量的Ti-45Al-7Nb-0.3W (at.%)两种合金进行表面机械研磨强化处理,对比研究了表面纳米强化层的微观组织结构与显微硬度分布。同时,本文将两种TiAl合金原始样品和表面机械研磨强化后的样品在室温空气条件下进行了往复式滑动摩擦试验,对比研究了两种TiAl合金表面机械研磨强化前后的摩擦行为和磨损机制。
2. 实验
本文采用等离子旋转电极法制备的Ti-47Al-2Cr-0.2Mo (at.%)和Ti-45Al-7Nb-0.3W (at.%)预合金粉,在1250℃、170 MPa条件下,热等静压保压5小时,制备得到两种γ-TiAl合金。采用电火花线切割方法制得尺寸为20 × 30 × 6 mm的两种γ-TiAl合金样品,经过清洗和打磨除去样品表面氧化物和其他污染物后放入立式行星球磨机对两种γ-TiAl合金进行球磨。为避免球磨过程中样品表面氧化,球磨罐放样品后抽真空并充入氩气保护。球料质量比为5:1,转速为500转/分钟,球磨30分钟后冷却10分钟,然后反向转动,循环往复,球磨总时间为24小时,以此实现对TiAl合金的表面机械碾磨强化。
本文采用Rigaku D/Max 2550 VB+型转靶式X射线衍射仪对表面机械强化处理后的TiAl样品表面进行检测,阳极靶为Cu,扫描步长0.02˚,电压40 kV。本文还采用BUEHLERMicroMet5104型显微硬度测试仪测量从样品强化表面到基体的显微硬度分布,每25 μm深度测量一组显微硬度值,每个深度重复测量三次取平均值。徕卡DM2700M-RL型金相显微镜和FEI FEG 250型场发射扫描电子显微镜被用来表征分析了表面机械强化后两种TiAl显微组织以及摩擦磨损试验后的样品表面磨痕和磨屑。
滑动摩擦试验采用美国UMT-3型号往复滑动摩擦试验机,摩擦对偶件为直径9.5 mm的铬钢球,硬度为HRC62。对偶件由摩擦试验机上端夹持,室温空气环境下以5 N的稳定载荷和0.2 m/s的速度在样品上往复滑动20分钟,摩擦系数由计算机控制程序自动采集并记录。同种试验参数下摩擦试验重复三次以减少测量误差。TiAl样品表面的摩擦槽由Keyence(日本)VHX5000超景深三维显微镜进行了表征。摩擦试验结束后,采用高精度电子天平测量摩擦前后TiAl样品的摩擦质量损失。表1为两种TiAl合金的物理性质,密度由排水法测得。
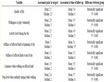
Table 1. Material properties of TiAl alloys
表1. TiAl合金的材料性质
3. 结果与讨论
3.1. 表面机械研磨后TiAl合金微观组织
图1为Ti-47Al-2Cr-0.2Mo和Ti-45Al-7Nb-0.3W合金经表面机械研磨后的横截面显微组织。两种TiAl合金表面经剧烈塑性变形后组织细化效果显著,表面机械研磨处理后表面均生成了明显的细晶层。从样品表层至心部基体,晶粒细化的效果逐渐减弱,两种TiAl合金内部组织仍保持较原始的热等静压烧结状态。在相同的表面机械研磨条件下,Ti-47Al-2Cr-0.2Mo样品表面细晶层的厚度在70 μm左右,而Ti-45Al-7Nb-0.3W合金表面细晶层的厚度在110 μm左右,大于Ti-47Al-2Cr-0.2Mo合金。
图2为Ti-47Al-2Cr-0.2Mo和Ti-45Al-7Nb-0.3W合金表面机械碾磨处理前后的X射线衍射谱。可以发现表面机械强化处理前后的两种材料并未发生明显的相变,X射线衍射结果显示材料均以四方TiAl相为主。两种TiAl合金表面机械强化后X射线衍射峰与原始样品相比,均有明显宽化。主要原因可能有两种:一是TiAl合金的表层晶粒在表面机械研磨过程中发生了晶粒的破碎和细化,这与图1中两种TiAl合金横截面的显微组织相吻合;二是在机械研磨后表层的组织中存在大量的残余应力。
(a)
(b)
Figure 1. Cross-sectional microstructures of as-SMATed TiAl alloy: (a) Ti-47Al-2Cr-0.2Mo alloy, (b) Ti-45Al-7Nb-0.3W alloy
图1. TiAl合金表面机械研磨处理后横截面显微组织:(a) Ti-47Al-2Cr-0.2Mo合金,(b) Ti-45Al-7Nb-0.3W合金
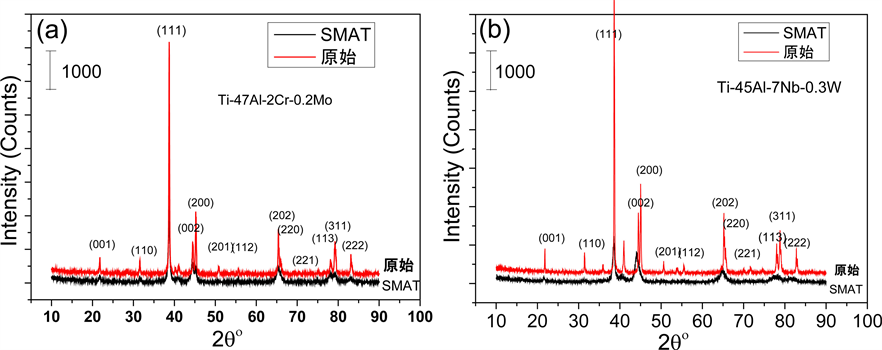
Figure 2. XRD patterns of original TiAl alloys and as-SMATed TiAl alloys: (a) Ti-47Al-2Cr-0.2Mo alloy, (b) Ti-45Al-7Nb-0.3W alloy
图2. TiAl合金表面机械研磨前后X射线衍射谱图:(a) Ti-47Al-2Cr-0.2Mo合金,(b) Ti-45Al-7Nb-0.3W合金
3.2. 显微硬度
图3为两种TiAl样品表面机械强化后沿强化表面的垂直方向由表层向基体过渡的显微硬度分布曲线。从图3可以看出,两种样品的显微硬度由外向内呈现出逐步降低的梯度分布。基体的Ti-47Al-2Cr-0.2Mo样品显微硬度在270 MPa左右,基体Ti-45Al-7Nb-0.3W样品的显微硬度稍高,在370 MPa左右。经表面机械强化处理后,两种样品表面硬度均显著提升,Ti-47Al-2Cr-0.2Mo样品的表面硬度提升到600 MPa左右,提升幅度超过100%;而Ti-45Al-7Nb-0.3W样品表面硬度提升到700 MPa左右,硬度提升幅度在90%以上。从硬度分布曲线来看,距样品表面75 μm深度范围内的硬度远高于基体,其硬度在基体硬度的1.5倍以上,而在100 μm深度以后的组织硬度则维持在稳定的水平,表明表面机械研磨强化处理的有效强化深度达到75 μm。这与Zhao [19] 等人的研究结果基本一致。
3.3. 滑动摩擦试验
3.3.1. 摩擦系数
Ti-47Al-2Cr-0.2Mo和Ti-45Al-7Nb-0.3W合金表面机械强化处理前后样品均在室温、空气环境下以5N的稳定载荷和0.2 m/s的速度进行了20分钟滑动摩擦磨损试验。每个样品在相同试验条件下重复三次,以减少误差。图4为两种TiAl样品表面机械强化处理前后摩擦系数随时间变化的曲线。如图4(a)和图4(c)所示,原始的热等静压态Ti-47Al-2Cr-0.2Mo合金和Ti-45Al-7Nb-0.3W合金的摩擦系数均在0.45~0.6之间,两者相差不大。图4(b)和图4(d)为两种TiAl样品经表面机械强化后的摩擦系数。与原始样品相比,在摩擦试验初始阶段经表面强化的两种TiAl合金样品的摩擦系数出现了明显下降,并分别维持了不同的时间。强化后Ti-47Al-2Cr-0.2Mo合金低摩擦系数(0.12左右)维持了约450 s,强化后Ti-45Al-7Nb-0.3W合金低摩擦系数(0.15左右)维持了约800 s。表面机械强化处理后两种TiAl合金在摩擦初始阶段低的摩擦系数主要原因是其表面产生的细晶层具有较高的硬度。通常在摩擦载荷一定的情况下,材料表面硬度越高,摩擦表面发生的弹塑性变形越小,其摩擦系数也会越低。强化后Ti-45Al-7Nb-0.3W合金比强化后Ti-47Al-2Cr-0.2Mo合金的低摩擦系数维持的时间长,主要原因可能是,如图1和图3所示,Ti-45Al-7Nb-0.3W合金产生的细晶层较厚且硬度也较高,因此耐磨损的时间较长。当摩擦对偶钢球把TiAl表面的细晶强化层完全磨损后,摩擦系数迅速恢复到原始TiAl样品的摩擦系数。对比图4(b)和图4(d),很明显,强化后Ti-45Al-7Nb-0.3W合金的细晶层耐磨性能更佳。结合图1和图3,这可以很好地解释了表面机械强化后Ti-45Al-7Nb-0.3W合金的细晶层耐磨性能更佳的原因。
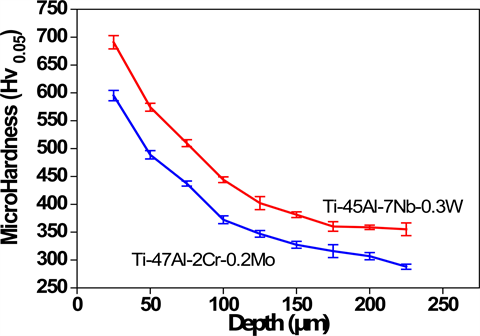
Figure 3. Microhardness vs. depth from the surface of as-SMATed TiAl alloys
图3. 表面机械强化处理后TiAl硬度沿深度变化曲线
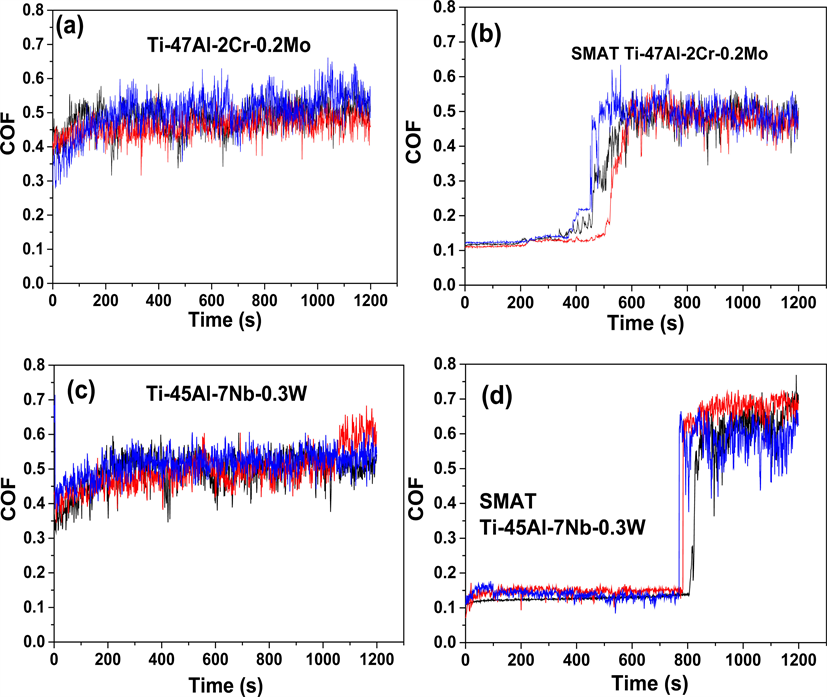
Figure 4. Coefficient of friction vs. time of original TiAl alloys and as-SMATed TiAl alloys from three repeated tests: ((a), (b)) Ti-47Al-2Cr-0.2Mo; ((c), (d)) Ti-45Al-7Nb-0.3W
图4. 表面机械强化处理前后TiAl摩擦系数与时间关系(三次重复试验)曲线:((a), (b)) Ti-47Al-2Cr-0.2Mo; ((c), (d)) Ti-45Al-7Nb-0.3W
3.3.2. 磨损量
从图5中可以看出,原始热等静压烧结态的Ti-45Al-7Nb-0.3W合金的磨损量略低于Ti-47Al-2Cr-0.2Mo合金的。根据表1中两种合金的显微硬度,可以发现Ti-45Al-7Nb-0.3W合金硬度更高一些,这可能是导致原始Ti-45Al-7Nb-0.3W的耐磨性更好的主要原因。
经表面机械强化处理后的TiAl合金的体积磨损量均比原始样品少。Ti-47Al-2Cr-0.2Mo原始样品摩擦过程中磨损量在160 × 10−6 cm3左右,经表面机械强化处理后的Ti-47Al-2Cr-0.2Mo样品磨损量在110 × 10−6 cm3左右,相比原始样品减少不到三分之一;而Ti-45Al-7Nb-0.3W原始样品的磨损量150 × 10−6 cm3以上,经表面机械强化处理后磨损量减小到50 × 10−6 cm3以下,减小幅度在三分之二以上。Ti-45Al-7Nb-0.3W样品经表面机械强化处理后耐磨性能提升明显优于Ti-47Al-2Cr-0.2Mo样品。很明显,在相同的表面机械研磨强化条件下,Ti-45Al-7Nb-0.3W合金的表面强化耐磨效果更好。这也与图1和图3中Ti-47Al-2Cr-0.2Mo和Ti-45Al-7Nb-0.3W合金表面机械强化后的细晶层组织的厚度和显微硬度分布具有较好的一致性。Nb元素的加入能细化TiAl合金晶粒,是提高其室温塑性最有效的手段之一。对比图1(a)和图1(b),能发现Ti-45Al-7Nb-0.3W合金基体的组织更加细小。一般来说,金属的晶粒越细小,其塑性也会越好。这将有利于Ti-45Al-7Nb-0.3W合金在表面机械强化过程中变形更加均匀,同时也减少了表面机械强化过程中加工硬化导致的裂纹和破碎。因此,Ti-45Al-7Nb-0.3W合金表面机械强化后细晶层
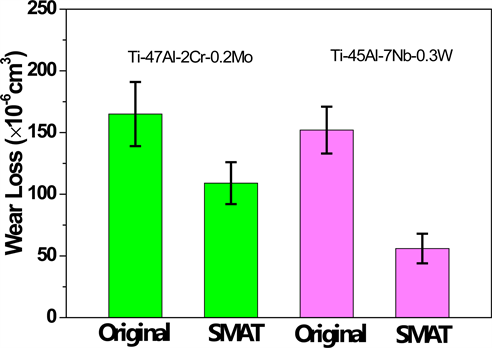
Figure 5. Wear loss of original TiAl alloys and as-SMATed TiAl alloys
图5. TiAl合金表面机械研磨处理前后磨损量
保留得更好,厚度更大。由此可以看出,高含量的Nb元素的引入提高了TiAl基金属间化合物对表面机械研磨强化的效果,有助于提高TiAl基金属间化合物的耐磨性能。
3.3.3. 磨屑形貌及成分分析
图6为表面机械强化处理前后两种TiAl合金在摩擦试验产生的磨屑的扫面电子显微镜照片及元素能谱分析,图6(a)为Ti-47Al-2Cr-0.2Mo原始样品磨屑形貌,从图6(a)中可以看出原始样品磨屑中含有较多大尺寸片状磨屑,考虑为摩擦过程中基体材料的塑形而引起的摩擦对偶球与样品表面在摩擦过程中粘着和基体材料推移堆叠,在长时间的摩擦后粘着堆叠区脱落,呈现为尺寸较大的片状磨屑。其中一些薄而且平的磨屑主要可能来自于粘着磨损。图6(c)为Ti-47Al-2Cr-0.2Mo样品经表面机械强化后的磨屑形貌。与图6(a)对比可见,Ti-47Al-2Cr-0.2Mo经表面机械强化处理后的样品产生的磨屑尺寸相对较小,且未见较大尺寸片状磨屑。图6(e),图6(g)分别为Ti-45Al-7Nb-0.3W样品经表面机械强化处理前后的摩擦试验产生的磨屑形貌。从图中可看出,经表面机械强化处理后的Ti-45Al-7Nb-0.3W合金摩擦过程中产生的磨屑也较原始的Ti-45Al-7Nb-0.3W合金的磨屑偏小。主要原因可能是Ti-47Al-2Cr-0.2Mo样品经表面机械强化处理后其表面产生一定程度的加工硬化,硬度提高,塑性降低,因而在摩擦过程中粘着和堆叠现象较少,容易破裂成尺寸细小磨屑。
图6(b)、图6(d)、图6(f)和图6(h)为两种TiAl合金表面机械强化处理前后摩擦试验所得磨屑的元素能谱分析。可以看出原始TiAl样品产生的磨屑氧含量要低于表面机械强化处理后TiAl合金产生的磨屑。这可能是因为表面机械研磨后的TiAl合金表面晶粒更加细小,破碎后的磨屑也相对细小,从而导致其磨屑的比表面积更大,在摩擦过程中更容易氧化。这些硬质的氧化物磨屑,如氧化铝等磨屑,将会为整个摩擦过程引入二体或者三体的磨粒磨损。通常三体磨损的磨粒与金属表面产生极高的接触应力,往往超过磨粒的压溃强度。这种压应力使韧性金属的摩擦表面产生塑性变形或疲劳,而脆性金属表面则发生脆裂或剥落。
值得注意的是,不论在表面机械强化处理前后,Ti-47Al-2Cr-0.2Mo样品磨屑中的氧含量总是高于Ti-45Al-7Nb-0.3W样品,这表明Nb元素的引入能有效提高TiAl基金属间化合物的抗氧化能力,这与Chen [20] 等人的研究结果一致。Jung [21] 等人的研究结果也表明:在γ-TiAl基合金中,随着Nb含量的提高材料的抗氧化能力得到了显著提高。
3.3.4. 磨痕形貌
图7为表面机械强化前后两种TiAl合金的表面磨痕形貌的背散射电子显微镜照片及对应区域元素能
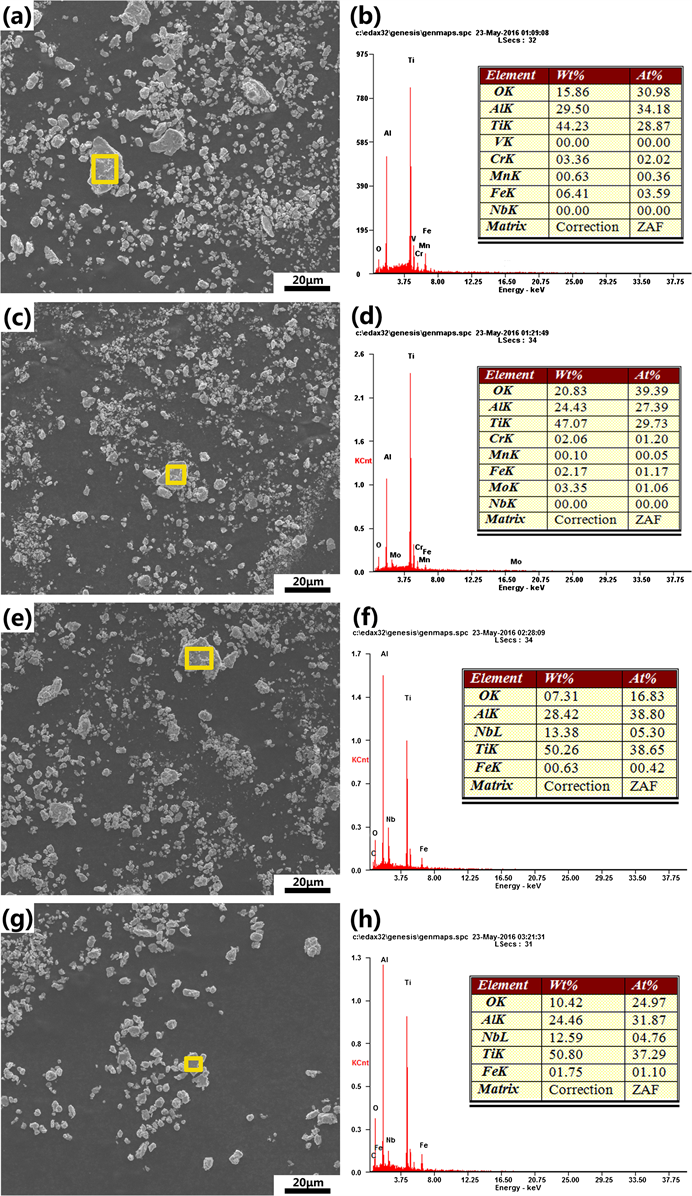
Figure 6. Wear debris from the sliding tests of original TiAl alloys and as-SMATed TiAl alloys and EDS: ((a), (b)) original Ti-47Al-2Cr-0.2Mo; ((c), (d)) As-SMATed Ti-47Al-2Cr-0.2Mo; ((e), (f)) original Ti-45Al-7Nb-0.3W; ((g), (h)) As-SMATedTi-45Al-7Nb-0.3W
图6. TiAl合金表面强化处理前后滑动摩擦后磨屑形貌及元素能谱分析:((a), (b))原始的Ti-47Al-2Cr-0.2Mo;((c), (d)) SMAT强化的Ti-47Al-2Cr-0.2Mo;((e), (f))原始的Ti-45Al-7Nb-0.3W;((g), (h)) SMAT强化的Ti-45Al-7Nb-0.3W
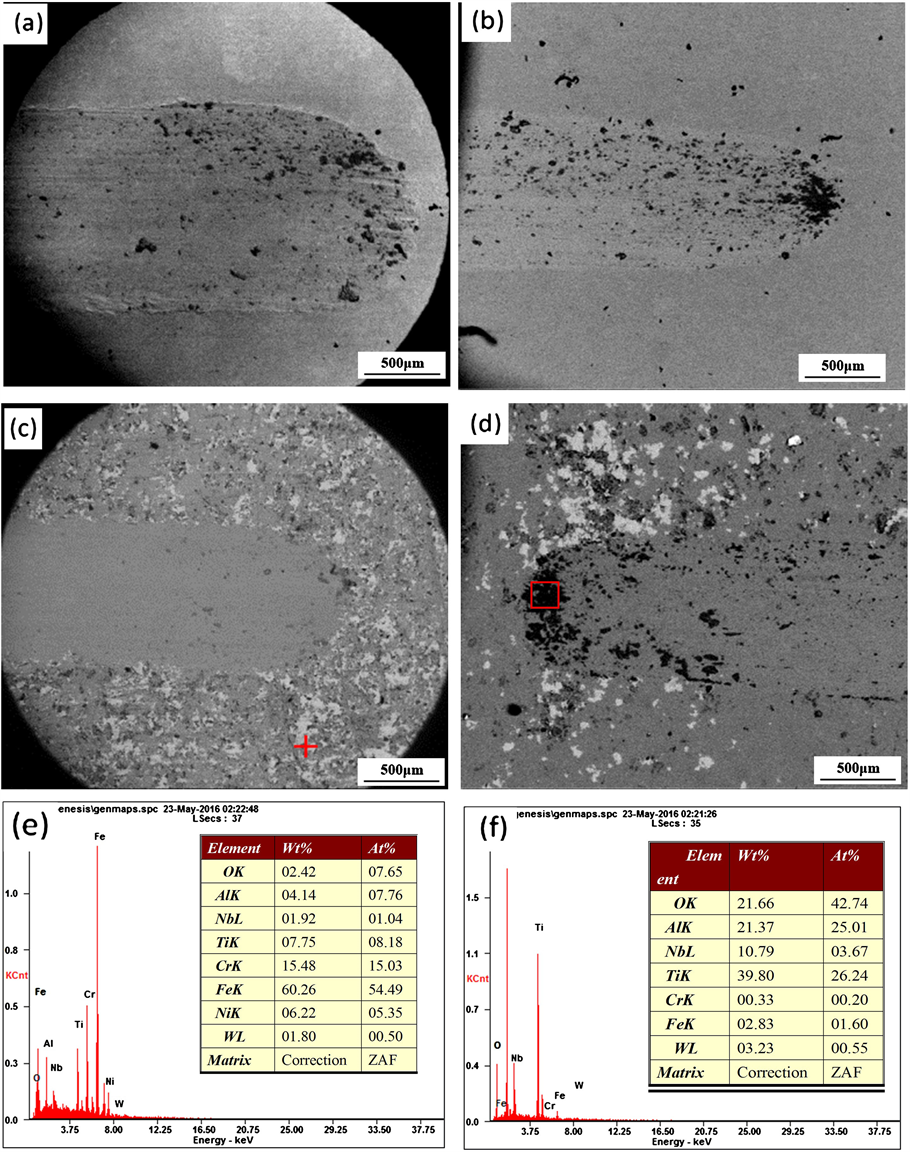
Figure 7. Back-scattering images of worn surface of original TiAl alloys and as-SMATed TiAl alloys and EDS: samples (a) original Ti-47Al-2Cr-0.2Mo; (b) original Ti-45Al-7Nb-0.3W; (c) As-SMATed Ti-47Al-2Cr-0.2Mo; (d) As-SMATed Ti-45Al-7Nb-0.3W; EDS results from (e) the point marked by cross in Figure 7(c) and Figure 7(f) the area marked by square in Figure 7(d)
图7. 摩擦试验后TiAl合金表面磨痕背散射电子显微镜照片及元素能谱分析:原始态(a) Ti-47Al-2Cr-0.2Mo;(b) Ti-45Al-7Nb-0.3W;表面机械研磨强化态(c) Ti-47Al-2Cr-0.2Mo;(d) Ti-45Al-7Nb-0.3W;(e)对应图7(c)十字标记区域元素能谱分析和(f)对应图7(d)方形标记区域元素能谱分析
谱分析。对比可见,Ti-45Al-7Nb-0.3W样品在表面机械强化处理后磨痕的宽度最小,这与前文中图5的磨损量数据表现一致。另外,两种TiAl合金的磨痕里面均有平行的细小犁沟,部分摩擦表面还有残留黑色的磨屑在磨痕内,这都是磨粒磨损的典型特征。
由图7(c)和图7(d)可以看出,两种TiAl合金表面机械强化表面的磨痕旁边有部分的白色物质附着,如图7(e)元素能谱分析表明该白色区域为球磨过程中粘附在TiAl合金表面的铬钢球成分。对比图7(a)和图7(c),发现经表面机械强化后的Ti-47Al-2Cr-0.2Mo样品磨痕宽度要小于图7(a)中的,这意味着强化后Ti-47Al-2Cr-0.2Mo合金更加耐磨。此结果也与图5中的磨损量相吻合。
除图7(c)以外,其他样品的磨痕的端部都堆积附着了一些深色的磨屑,结合图7(f)的能谱分析,这些磨屑大部分由TiAl合金的氧化物组成,还含有少量的Fe元素,其来自于摩擦对偶的铬钢球。证明TiAl合金在摩擦过程中氧化反应比较严重,与Qiu [14] 的研究结果吻合。另外,氧化反应在摩擦生热的帮助下增强,因此摩擦过程中的机械力能够非常容易地破碎氧化层,随后氧化层将开裂和剥离摩擦表面,并留下的凹坑。如图7(c)所示,表面机械研磨强化的Ti-47Al-2Cr-0.2Mo产生的磨屑只有很少量附着在磨痕上的,这可能是因为其摩擦过程中产生的磨屑硬且脆,导致在摩擦过程中无法进行塑性变形进而粘附在TiAl合金样品的磨痕上。
图8为两种TiAl合金表面机械强化处理前后的摩擦试验后磨痕3D形貌和截面轮廓。由图可得,原始Ti-47Al-2Cr-0.2Mo样品磨痕深度在41 μm左右,经强化后减小到36 μm左右;原始Ti-45Al-7Nb-0.3W样品磨痕深度在30 μm左右,经强化后减小到21 μm左右。结合图7的磨痕宽度分析可知摩擦过程中样品的体积损失为Ti-45Al-7Nb-0.3W样品强化前后的减少幅度远大于Ti-47Al-2Cr-0.2Mo样品,与前文摩
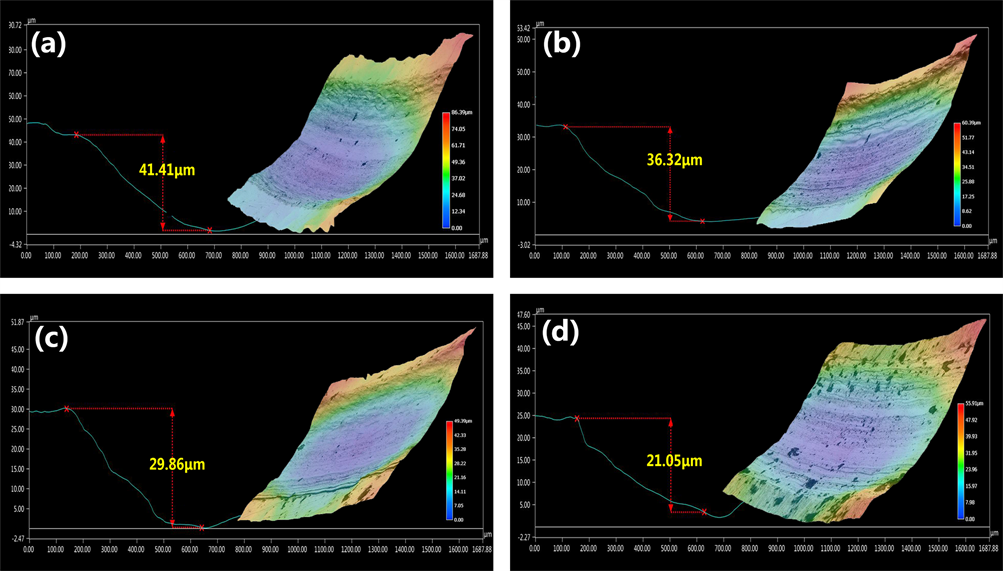
Figure 8. 3Dwear tracks on the worn surface from the original TiAl alloys and as-SMATed TiAl alloys and cross sectional profile: ((a), (b)) original Ti-47Al-2Cr-0.2Mo; ((c), (d)) As-SMATed Ti-47Al-2Cr-0.2Mo; ((e), (f)) original Ti-45Al-7Nb-0.3W; ((g), (h)) As-SMATed Ti-45Al-7Nb-0.3W
图8. TiAl合金表面强化处理前后磨痕3D形貌与横截面轮廓:(a)原始态Ti-47Al-2Cr-0.2Mo;(b) as-SMATed Ti-47Al-2Cr-0.2Mo;(c)原始态Ti-45Al-7Nb-0.3W;(d) as-SMATedTi-45Al-7Nb-0.3W
擦试验中体积磨损量一致。
由图8(c)可以发现,根据深度的标尺,表面研磨强化后的Ti-47Al-2Cr-0.2Mo的磨痕表面还存在较多的深色斑点,即表面点蚀和剥落,这是表面疲劳磨损的形态。另外,除图8(d)以外,其他三种情况下磨痕中都存在很大量平行的犁沟。而表面机械研磨后的Ti-45Al-7Nb-0.3W合金表面磨痕相对平整。通常平行的犁沟是由硬质的第三相颗粒在摩擦中产生。这也间接的表明Ti-45Al-7Nb-0.3W样品表面机械研磨强化后表面生成了较厚的耐磨细晶层。
4. 结论
1) 表面机械研磨强化处理可在Ti-47Al-2Cr-0.2Mo和Ti-45Al-7Nb-0.3W合金表面形成有效的细晶强化层,外表面细晶层硬度约为基体的2倍。
2) 经表面机械研磨强化处理后Ti-47Al-2Cr-0.2Mo和Ti-45Al-7Nb-0.3W合金表面细晶强化层的摩擦系数约为基体的1/4,耐磨性能均有明显提高。高Nb含量的Ti-45Al-7Nb-0.3W合金相比与Ti-47Al-2Cr-0.2Mo合金在表面机械研磨强化后耐磨性能提高更加明显,其体积磨损量减少为原始态的1/3。
3) 原始态的Ti-47Al-2Cr-0.2Mo和Ti-45Al-7Nb-0.3W合金的磨损机制为二体或者三体的磨粒磨损,还有一部分的塑性变形和疲劳磨损。经过表面机械研磨强化后的两种TiAl合金的磨损机制则以磨粒磨损为主。
基金项目
国家自然科学基金(项目号:51604112),湖南省自然科学基金(项目号:2017JJ3089),湘潭市企业科技特派员项目和湖南科技大学大学生研究性学习和创新性实验计划项目(项目号:201710534013)的资助。
NOTES
*通讯作者。