1. 再生铜制杆行业发展现状
再生铜制杆行业是一个较为传统的行业,近十年来发展迅速,产能规模由2002年50万吨发展到2020年470万吨,增长约10倍;由于政策导向产能相对集中在江西、湖北等地区 [1]。
2020年11月1日,国家恢复了再生铜原料进口,给国内再生铜杆深加工产业带发展契机。又相应出台和实施再生铜原料标准GB/T 38471-2019,拓宽了原料进口渠道,解决了国内原料供应不足的问题。
由于政策导向和逐利资本注入,行业进入了快速发展期,但生产技术、管理水平相对滞后,大多数企业仍停留在以“师傅经验”为主导的简单操作生产模式,导致产品质量稳定性差,产品性能指标参差不齐,附加值低,行业处于低水平竞争阶段(价格战);亟待规范和完善技术工艺、管理体系,应用新工艺、新装备 [2] [3]。
可预测:未来3~5年,再生铜制杆行业将迎来产业迭代升级的发展期 [4]。
2. 再生铜精炼工艺原理
再生铜精炼原理就是利用铜的氧化——还原可逆性,其活泼性低于大多数金属杂质元素,精炼过程中金属杂质元素先被氧化,其氧化物密度低于铜液的密度,浮于铜液表面。采用氧化、造渣、扒渣、还原过程,去除大部分杂质元素 [2]。
氧化:在熔融状态下通入压缩空气,使金属元素和氧发生反应,生成金属氧化物。
氧化的目的:主要是去除锌、铅、锡、铁、镍等杂质,通过蒸锌、酸性造渣、碱性造渣的方式除去杂质,提高铜的纯度。主要反应方程式如下:
锌的去除 ZnO + SiO2 = ZnSiO3
铅的去除 PbO + SiO2 = PbSiO3
锡的去除 SnO + SiO2 = SnSiO3
SnO2 + Na2CO3 = Na2SnO3 + CO2
SnO2 + CaO = CaSnO3
铁的去除 FeO + SiO2 = FeSiO2
Fe2O3 + 3SiO2 = Fe2SiO3
镍的去除 ① 溶剂造渣法
NiO + SiO2 = NiO∙SiO2
NiO+Fe2O3 = NiO∙Fe2O3
② 俄罗斯熔析法除镍
还原的目的:将氧化阶段产生的氧化亚铜还原为单质铜。传统还原工艺为“插木还原”,此法是将青木插入铜液中,由于青木在铜液中的干馏(C + H2O → H2 + CO + CH4)作用,产生氢、一氧化碳及碳氢化合物起到还原作用;新工艺采用天然气还原,是利用天然气裂解产生还原性气体(CH4 = 2H2 + CO)起到还原作用。
反应方程式为:
① Cu2O + C = CO + 2Cu,
② Cu2O + H2 = 2Cu + H2O↑,
③ Cu2O + CO = 2Cu + CO2↑,
④ 4Cu 2O + CH4 = CO 2 + 2H2O + 8Cu。
3. 铜杆连铸连轧工艺控制
连铸工艺流程如下:精炼后的铜液经流槽流入浇包,铜液通过浇包的浇嘴进入铸机的结晶轮冷却结晶形成铸坯,铸坯经过轧机连续轧制、清洗还原成光亮铜杆 [5]。
主要控制点:铜液温度、冷却水流量、铸机速度、脱模剂厚度、结晶轮温度、钢带温度、铸坯温度、入轧温度、乳化液温度和流量、出轧温度、清洗剂温度和流量、产品温度。具体控制参数见表1、表2 [2]。
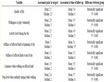
Table 1. Cooling water flow of each zone
表1. 各区冷却水流量
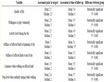
Table 2. Process node control parameters
表2. 工艺节点控制参数
异物控制:铜液杂质、结晶轮/钢带清洁度、铸坯毛刺、轧制颗粒物、乳化液、清洗液的理化指标。
4. 再生铜制杆的质量分析及优劣判断
1、再生铜杆产品质量现状
因原料不同、生产工艺、设备相对落后、关键技术人才缺乏导致产品质量参差不齐。
主要表现为电性能(体积电阻率)、化学性能(成份)、加工性能(拉丝、退火、损耗)波动大或不达标。优质企业生产的再生铜杆质量接近精铜杆水平(如江钨的再生铜杆),多数企业的产品与行业标准或国家标准要求差距较大。
2、再生铜杆产品质量分析
1) 化学性能(成份)——波动大或不达标
主要表现在Zn、Pb、Sn、Fe、Ni含量超标或波动大,进而导致Cu含量波动。由于精炼技术落后,选用造渣剂不当,温度控制不合理,在氧化除杂阶段未能有效去除Zn、Sn元素;在还原阶段造成Zn、Sn元素回熔现象。
部分企业技术不成熟,为了生产顺畅性,在生产过程中添加了Pb,从而导致杂质元素超标。
行业中氧化–还原都使用包覆耐火材料的钢(铁)管为工具,自耗溶入Fe,可能导致铁元素超标;在精炼过程中当Ni ≥ 100 ppm,需加入Fe2O3除镍,因工艺处理不当,也可能导致铁元素超标。
2) 电性能(体积电阻率)波动大或不达标
影响电性能的主要因素:
化学成份波动大或不达标、产品组织结构;如晶粒、铜粉量、氧化膜厚度都会影响电性能;检测方法、测试环境对检测结果影响也较大;因为铜杆电阻值(0.3~0.4毫欧)较小。影响质量的铸坯组织见图1 [5]。
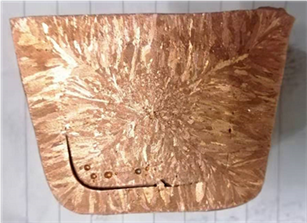
铸坯低倍组织casting and rolling 铸坯低倍组织casting and rolling
Figure 1. Billet diagram
图1. 铸坯组织图
3) 加工性能(拉丝、退火、损耗)波动大或不达标
主要表现:拉丝过程的断线率和损耗率高,成品铜线的退火性不均匀。
导致拉丝易断线主要因素:铜杆夹杂、气孔、开裂、含氧或氢过高、杂质微合金化偏析;
导致损耗率高主要因素:铜杆表面毛剌飞皮多、有氧化、不光滑、有棱角(圆整度差)、氧化膜过厚;
导致退火性能差主要因素:铜液中氧含量与杂质元素不稳定、不均匀,杂质微合金化偏析,浇铸时产生偏析。
4) 机械性能波动大或不达标
主要表现:抗拉强度和伸长率低,扭转数不达标;扭转断头后残样可能表层、深层开裂,会影响到后续的拉丝断线率。
影响抗拉强度和伸长率、扭转数:氧含量、晶粒结构、冷却梯度、铸造及轧制温度、检测方法(行业中加10 kg配重;样件标距250 mm、扭转速度30 rpm ± 10%)。
5) 外观质量差、尺寸不达标
外观质量差、尺寸不达标主要表现:毛剌飞皮多、表面粗糙、有棱角;
影响外观质量差、尺寸不达标因素:晶粒结构、冷却梯度、铸造及轧制温度、轧辊表面粗糙度、氧化膜厚度、铜粉量。
3、 再生铜杆质量优劣判断
参照国标GB/T 3952-2016《电工用铜线坯》、再生铜行业标准YST 793-2012《电工用火法精炼再生铜线坯》及其他相关标准。再生铜杆质量优劣判断相关标准见表3 [6]。
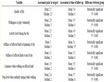
Table 3. Relevant standards for judging the quality of regenerated copper rod
表3. 再生铜杆质量优劣判断相关标准
5. 解决问题的方法
1、精炼工序:应遵循精炼工艺“九字方针”——深氧化、准还原、扒渣净。通过有效的检测手段,定量分析杂质元素的种类及含量,正确使用造渣剂,精确控制精炼温度和氧含量,有效去除有害杂质元素。
我们的总结为:
- 温度控制是贯穿精炼过程的核心;
- 氧含量控制是精炼过程的基础;
- 酸性造渣、碱性造渣是精炼过程的方法;
- 氧化–还原是精炼过程的可灵活运用的原理。
2、浇铸工序:严格控制浇铸温度,纯铜熔点1083℃,一般采用30℃~60℃的过热度作为浇铸温度。采用“一缓、二强、三精”的冷却梯度方法,精准控制结晶温度曲线,解决了铸坯夹杂、夹气和裂纹问题。
3、轧制工序:严格控制入轧温度和出轧温度,通过控制乳化液浓度、流量和温度,让轧件维持在合理的轧制温度,正确控制轧件压缩比,保证轧制过程中不裂、不堵、不拉;通过控制清洗液浓度、流量和温度(流量控制原则“前缓、中强、后弱”),解决产品温度和氧化膜厚度问题。
引进先进工艺技术,多维度集成创新,持续提高产品质量。
6. 再生铜制杆新工艺分享
(一)、天然气还原工艺
1. 天然气还原机理
天然气还原是利用CH4的还原性与氧化亚铜反应得到单质铜的机理 [6] [7];主要有如下几个方面的优势:
(1)、符合环保理念
传统工艺采用“青木还原”,改用天然气还原工艺后,不需要砍伐森林,明显减少了颗粒物排,践行了“绿水青山就是金山银山”的环保理念。
(2)、节能效果显著
天然气热值高、燃烧效率高。在还原阶段,通入铜液的天然气与Cu2O反应的过程会释放大量的热,能保持炉内铜液温度,不需要燃烧装置持续加热,节约了燃料的消耗;相对于传统工艺,具有明显的节能的效果。
2. 天然气还原的前置条件
当天然气供气压力 ≤ 0.2 MPa,不适合采用天然气还原;如果采用天然气还原工艺,需要增加天然气增压设备。
(二) 添加稀土铜杆新工艺
稀土作为工业上的“维生素”,在铜及铜合金中有着显著的作用;一是稀土在铜及合金中显现出明显的微合金化作用,这主要是指,稀土金属与铜及其内部的其它杂质形成第二相,并且细化铜及其合金的晶粒组织 [7]。
二是稀土能够明显地增加合金的再结晶温度及并提高其软化温度。
三是稀土能够去除铜及合金中的杂质元素,稀土微合金化工艺可以显著减少异类杂质元素的引入,实现合金净化,提高合金强度及耐蚀性,保证铜材优良的导热导电性。
再生铜杆生产过程中加入适量的多元稀土合金,能有效平衡氢、氧元素、去除“部分”杂质元素,从而提高产品的导电性、可塑性。