1. 引言
SiCp/Al复合材料是铝合金为基体、SiC颗粒构成的颗粒增强形复合材料,同时具备两者优点,如比强度大、耐磨性好、耐高温等优点,被广泛应用于汽车、军事、光学精密仪器等领域 [1] [2] 。然而,由于Al基体和SiC颗粒的物理力学特性相差较大,在机械加工中容易带来切削力不稳定、加工表面完整性差等问题,从而限制该类材料的广泛应用 [3] [4] 。
为获取高质量的SiCp/Al复合材料加工表面,大量研究人员通过实验和仿真结合的方式对SiCp/Al复合材料展开研究 [5] 。Teng [6] 等比较了不同尺寸级别下的SiC颗粒对材料表面质量的影响,发现纳米级别的SiC颗粒可以显著改善表面质量。Gao [7] 等研究了高体积分数SiCp/Al复合材料的变形机制和工艺参数对表面粗糙度的影响。Zhang [8] 等通过ABAQUS模拟不同颗粒尺寸下的切削行为,分析切削过程中最大等效应力出现位置和颗粒粒度对切屑形态的影响。Duan [9] 等考虑了基体粘附、二体磨损和三体滚动摩擦等因素,指出SiC颗粒主要以脱粘、破碎和挤压的方式在剪切区与刀–屑接触部分被去除。Xu [10] 等研究发现SiC颗粒在小于0.01 μm的划痕深度下以延性方式去除,随着划痕深度的增加,SiC颗粒的脆性断裂变的明显。房玉鑫等 [11] 研究了高速铣削条件下的成屑机理和表面完整性,结果表明提高切削速度能够显著提高加工表面质量。在此基础上,对SiCp/Al复合材料表面和亚表面损伤也有相关研究,Wang [12] 等通过仿真和车削实验指出切削深度接近颗粒高度一半时,颗粒完全脱粘,形成空洞,导致表面质量恶化,减小切削深度可提高表面质量。Wang [13] 等仿真分析了表面缺陷的形成机制,发现其与SiC颗粒几何尺寸有关;而Wu [14] 等则通过仿真与实验相结合的方式研究了切削深度对亚表面损伤深度程度的影响。王俊磊 [15] 、Xiang [16] 和Yan [17] 等利用有限元模型探究了超声振动对SiCp/Al复合材料加工表面形貌以及表面损伤的影响,研究表明,超声振动振幅在一定范围内增大,可有效改善颗粒破碎效果,减少亚表面损伤,抑制表面裂纹扩展等。
SiC颗粒断裂机制与其形态尺寸有关,并且其断裂形式对材料表面损伤程度起到关键性作用,尽管在上述研究中分析了颗粒尺寸与表面缺陷、表面粗糙度的关系,但是未充分研究不同切割深度下的颗粒断裂形式,除此之外,两相界面层属性对复合材料整体性能 [18] ,如整体刚度、强度和韧性等有着密切联系,在建立有限元模型时应充分考虑这些因素,因此本研究在针对上述研究中存在的不足,建立考虑SiC颗粒以及两相界面影响的有限元仿真模型,对SiC颗粒在不同磨削路径的去除形式,引起的表面缺陷、表面损伤展开仿真分析,并进行了试验验证。
2. SiCp/Al有限元模型建立
2.1. 有限元几何模型
材料与磨粒的几何特征是建立有限元模型的基础,也是影响分析结果的关键。因此本研究使用PYTHON语言对ABAQUS进行二次开发,建立SiCp/Al复合材料几何模型,实现SiC颗粒的随机分布,图1显示为磨粒切削几何模型,图中磨粒设置为刚体,其中Referencepoint为刀具的刚体参考点。工件为长200 μm,宽40 μm的矩形,SiC颗粒直径为5~20 μm,并依据本文所用材料中增强相含量,Al基体2A14、SiC颗粒和金刚石磨粒物理力学性能参数如表1所示 [19] [20] 。基于SiCp/Al复合材料主要成分(见表2),将SiC颗粒体积分数设置为20% [21] [22] 。
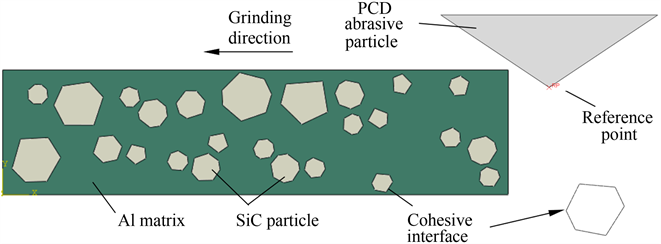
Figure 1. SiCp/Al composites grinding geometric model
图1. SiCp/复合材料磨削几何模型
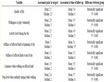
Table 1. Physical property parameters of Al matrix, SiC particles and diamond abrasive particles
表1. Al基体和SiC颗粒以及金刚石磨粒物理性能参数
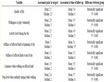
Table 2. Proportion of main components of materials (volume fraction)
表2. 材料主要成分占比(体积分数)
2.2. 有限元仿真模型
2.2.1. 铝基体本构模型
在仿真模拟前处理过程中,基于Al基体、SiC颗粒物理力学性能不同,分别对其进行材料属性的赋予,铝基体以Johnson-Cook本构模型 [23] ,如式(1)所示:
(1)
式中
分别为材料屈服强度、应变硬化数、应变率数;是等效塑性应变率、参考应变率、等效塑性应变;熔点、室温应变敏感数、热软化数;如表3所示:
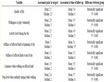
Table 3. Parameters of Johnson-Cook constitutive model for Al matrix
表3. Al基体Johnson-Cook本构模型参数
Al合金基体的切屑分离过程由Johnson-Cook断裂准则来描述 [14] ,D的表达式如式(2):D = 0表示损伤演化起始,当D = 1表示材料完全失效,表达形式:
(2)
式中:
分别为损伤起始的等效塑性应变等效塑性应变增量。
(3)
式中:断裂失效参数
的数值如表4所示。
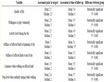
Table 4. Failure parameters of Johnson-Cook fracture in Al matrix
表4. Al基体Johnson-Cook断裂失效参数
2.2.2. SiC颗粒断裂准则
SiC作为一种硬脆材料,在切削过程中会直接发生脆性失效,因此材料断裂准则设置为脆性断裂准则。SiC颗粒的失效用正应力准则描述 [24] [25] ,其定义为
(4)
式中:
为应力主分量,
为脆性材料的抗拉强度。
SiC颗粒达到失效阈值后,其损伤演化判定准则为断裂能准则。为损伤裂纹的开裂位移,被计算为:
(5)
剪应力保留模型是剪应力对SiC颗粒裂纹应变的函数,可以通过式(6)计算:
(6)
式中:
为材料未失效时剪切模量,
为
的剪切保持函数:
(7)
式中:
、
为材料相关参数,
为开裂张开应变。
在有限元建模中,描述SiC脆性断裂参数如表5所示。
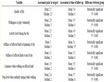
Table 5. Parameters of SiC particle brittle fracture model
表5. SiC颗粒脆性断裂模型参数
2.2.3. 基体–颗粒内聚力界面模型
在SiCp/Al数值模拟处理过程中,粘聚力单元被广泛应用于描述基体–颗粒界面上力与裂纹位移的作用关系上。在外力作用下,基体–颗粒界面承受载荷,Al基体与SiC颗粒在两相界面处开始分离,依据界面断裂破坏准则,在裂纹位移达到预设值时,粘聚力单元失效,裂纹沿粘聚力边界拓展,进一步导致两相界面失效,从而使Al基体与SiC颗粒分离脱粘 [26] 。研究使用内聚力单元建立界面模型为:
(8)
(9)
在本研究中,
,完全失效值:
,粘聚力在载荷作用过程中的变化可由式(10)描述
(10)
两相界面的损伤破坏基于二次名义应力准则,即当切向名义应力比和法向名义应力比的平方等于1,Al基体-SiC颗粒界面开始损伤,描述公式如式(11),取值如表6所示。
(11)
3. 加工试验条件与方法
在本研究中,工件材料使用20%Vol SiCp/Al复合材料,经线切割加工材料至尺寸为:长*宽*高 = 20 mm*20 mm*5 mm的式样,磨削实验在Carver S600A机床上进行,式样经PCD精铣后进行平面磨削试验。在磨削条件上,湿式磨削时,磨削液能加快磨屑的排出,减小磨屑对已加工表面质量划擦,但磨削液难以进入磨削区,加工时磨削区温度高,在砂轮磨削过后,磨削液会使工件表层温度急剧下降,以至工件表层产生较大的应力,可能导致表面坑洞、裂纹等缺陷。采用干式磨削时,磨削区高温使铝基体软化,使其硬度降低,从而材料表面整体的硬度会相应降低,表层塑性流动加强,弥合加工表面微观裂纹,减少应力集中。在磨削方式上,当采用顺磨时,由于工件和砂轮在磨削区运动方向相同,SiC颗粒的损伤比较单一,尽管表面粗糙度较好,但同时也无法准确分析SiC颗粒的各类损伤形式,当采用逆磨时,SiC颗粒的损伤形态较多,因而也能够更加直观地分析SiC颗粒的损伤情况,因此本研究选用干式逆磨方式进行加工,如图2所示。磨削刀具采用上海蓝领数控科技的金刚石树脂结合剂铣磨刀具,磨削加工现场如图3所示,磨削后的工件采用通过超声清洗机去除表面磨屑及杂质。磨削试验参数如表7所示。
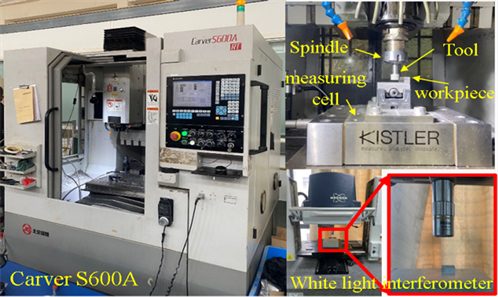
Figure 3. Test equipment and site settings
图3. 试验设备及现场设置
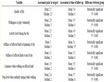
Table 7. Grinding process parameters table
表7. 磨削工艺参数表
磨削表面观测试验是通过白光干涉仪与ZEISS Gemini 300 SEM扫描电镜相结合的方式,并以此分析表面的主要缺陷形式,展开对磨削表面形貌和粗糙度的分析与研究,观测试验中的粗糙度采集方式是通过随机选取磨削表面上三个位置,取粗糙度数值的平均值,作为其表面粗糙度,利用单因素试验分析磨削速度、进给速度、磨削深度对表面粗糙度粗糙度的影响。
4. 结果分析与讨论
4.1. SiC颗粒断裂机理分析
SiCp/Al复合材料微观去除过程受到SiC颗粒与磨粒的相对位置的影响,为解释SiCp/Al复合材料在加工过程中的去除机理,进行了不同切割深度下的材料去除仿真分析,细微观中磨粒与的SiC颗粒接触方式如图4所示,图5中显示了本此模拟中形态各异的SiC颗粒位于磨粒不同切割路径下的相互作用位置,由于颗粒SiC颗粒属于高硬脆性材料,相较于Al基体在加工中与磨粒在不同的接触位置会产生不同的应力状态,从而产生不同的去除形式,这对工件表面完整性起重要作用。
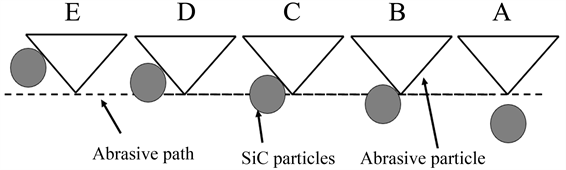
Figure 4. Location diagram of abrasive particles and particles
图4. 磨粒与颗粒位置示意图
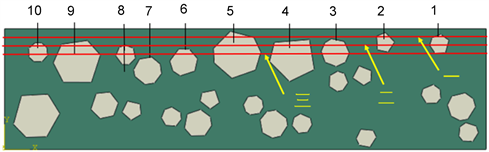
Figure 5. Trajectory of abrasive particles
图5. 磨粒轨迹图
图5中标记为“一”的直线表示为磨粒作用深度在3 μm的磨粒轨迹图,此时,颗粒1、颗粒2、颗粒5在磨粒运动路径上,图6(a)为磨粒切削后的表面形貌图,从图中能明显看出,只有SiC处发生了较大的脆性去除,在磨粒切削过程中,SiC颗粒是承受载荷的作用主要,在此相对位置下,SiC颗粒发生顶部局部断裂,造成表面小凹坑。图6(b)左图显示的是在此切割深度下的切向力与法向力的变化趋势,右图显示颗粒去除过程的Von mises应力分布,当磨粒分别与Al基体和SiC颗粒作用时,切削Al基体时的作用力都明显小于SiC的作用力,经计算,SiC颗粒的磨削力是Al基体的5~7倍,在磨粒接近SiC颗粒时,由于SiC颗粒形态以及力学性质明显区别于Al基体,在SiC颗粒与Al基体界面发生应力集中现象,因此切削力也迅速增大,当磨粒与SiC发生接触时,切削力达到峰值,此时SiC颗粒内部应力达到其强度,导致发生SiC颗粒断裂破坏,当SiC发生断裂或者磨粒切出SiC颗粒时,切削力急剧下降。颗粒断裂过程的磨粒切削力及内部应力变化对应如图6(b)中A、B、C、D所示。
(a) ap = 3 μm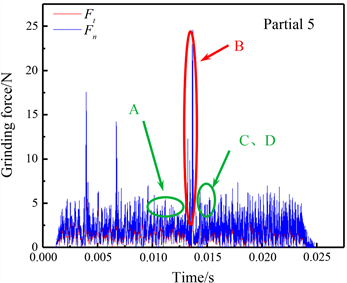
(b) 颗粒5去除过程
Figure 6. Surface morphology and removal phenomenon
图6. 表面形貌与去除现象
实际磨削过程中,由于SiC颗粒分布随机性以及在磨粒的反复切削下,稳定磨削阶段,磨削力的变化时会在一定范围内波动,但是无论是切削Al基体还是SiC颗粒其切向力都小于法向力,如图7所示,图中因测力仪安装方向及设置原因,Fx为实际磨削中的法向力,Fy为实际磨削中的切向力。
图5中标记为“二”的直线表示为磨粒切割深度在6 μm的磨粒切削轨迹图,此时,在SiC颗粒1~10中,只有颗粒7未参与切削,随着磨粒切削深度增加到9 μm时,颗粒7也参与了切削,随着磨粒切深由3 μm增加到6 μm时,SiC颗粒发生断裂的现象增多,并且小尺寸颗粒发生了解离去除,大尺寸颗粒的损伤深度增大,磨粒切削表面形貌图如图8(a)所示。图5中标记为“三”的直线表示为磨粒切割深度在9 μm的磨粒切削轨迹图,图8(b)显示了在磨粒切削深度为9 μm下的表面形貌,相较于切削深度3 μm和6 μm的表面形貌,在9 μm下的磨削表面存在更多缺陷,小尺寸颗粒被拔出形成凹坑,大尺寸颗粒产生的裂纹也随着增大。
(a) ap = 6 μm
(b) ap = 9 μm
Figure 8. Surface topography of abrasive cutting
图8. 磨粒切削表面形貌
伴随着SiC颗粒相对于路径的上移,颗粒的损伤形式发生了转变,如图9,颗粒1在9 μm下发生整体颗粒破碎,并有残留的破碎颗粒,当磨粒切削至颗粒1下部时,发生了脱粘拔出,并且颗粒底部的基体发生了撕裂,图10中显示颗粒5随着磨粒切削深度的增加的应力变化,仿真显示去除方式也由局部破碎转为解离破碎,并伴有微裂纹的产生。值得注意的是,内部应力的大小与其在路径的不同位置有关,且应力集中均从Al基体与SiC接触界面发生,随着SiC被切削深度的增大,其承受的载荷也随之增大。在参与磨粒切削的SiC颗粒中,SiC颗粒去除方式也并非完全相同,如颗粒3,在磨粒切深6 μm下发生断裂破碎,在磨粒切深9 μm下发生塑性去除,而随着磨粒切削深度的增大,与之类似形态尺寸的颗粒10却由整体断裂破碎转变为脱粘拔出。以上分析表明,尺寸较小的SiC颗粒去除方式随着被切削深度的增大易发生脱粘去除,但也受到SiC颗粒在Al基体中位置状态的影响,发生塑性去除。较大尺寸的SiC颗粒去除方式以断裂破碎为主,随着被切削深度的增大会伴有裂纹产生。
4.2. 磨削加工表面完整性分析
为了更加直观地分析SiCp/Al复合材料磨削后的表面形貌,利用白光干涉仪对加工表面进行三维采集,如图11所示。图11分别显示在四组磨削深度下的工件的表面形貌,可以清晰的看出,随着磨削深度的增加,磨削沟槽呈现高低交替周期性的变换,磨削加工表面的高低起伏特征相较于小磨削深度下也更为明显,因而加工表面的粗糙度也更大。
图12(a)显示磨削深度对沿磨削方向粗糙度的影响规律,根据图中曲线变化规律可知,磨削深度由3 μm增加到12 μm时,加工表面粗糙度明显增大,主要归因于过大的磨削深度会造成磨削加工过程不平稳,磨削力和磨削温度增大,磨粒磨损加剧,此外,细微观上磨粒未变形厚度也因此增大,相应造成Al基体塑性变形程度增大,从而造成SiCp/Al复合材料中的SiC颗粒脆性去除率增大,SiC颗粒以脱粘拔出、断裂破碎的形式去除的比例大幅增加,使得表面粗糙度值在一定范围内大幅度增加,由图12(b)可以看出,磨削速度由4.7 m/s增大到9.4 m/s时,磨削表面粗糙度显著降低,这归因于实际参与进行磨削过程的磨粒数量增多,一方面,砂轮单位时间内转速提高,提高使得单颗磨粒去除材料量减少,提高了表面质量。另一方面,单颗磨粒作用于工件的时间变短,导致磨削区内产生的热量在砂轮磨削瞬间内无法散出,材料软化,因而更易于加工,在磨粒的反复作用下,加工表面趋于平整,进而会降低表面粗糙度,由图12(c)可以看出,当工件速度增大,SiCp/Al复合材料的加工表面粗糙度随之增大,这是由于SiC颗粒的去除形式发生变化,SiC颗粒解离破碎、脱粘情况增多,加工振动变化大,表面粗糙度也因此而增大。
(a) ap = 3 μm
(b) ap = 6 μm
(c) ap = 9 μm
(d) ap = 12 μm
Figure 11. Surface topography of grinding
图11. 磨削表面形貌图
(a)
(b)
(c)
Figure 12. Variation trend of surface roughness parallel to grinding direction
图12. 平行磨削方向表面粗糙度变化趋势
图13(a)~(c)表示为各工艺参数对垂直磨削方向的表面粗糙度的影响,整体上其值的大小显著大于沿磨削
(a)
(b)
(c)
Figure 13. Variation trend of surface roughness in vertical grinding direction
图13. 垂直磨削方向表面粗糙度变化趋势
方向粗糙度数值,一方面受到磨粒出刃高度不同的影响,在磨削过程中造成加工表面沟槽多,导致垂直磨削方向时粗糙度增大。另一方面,SiC颗粒的去除形式同样对垂直磨削方向的粗糙度造成显著影响。图13(a)中相较于磨削深度由3 μm增大到9 μm时粗糙度的变化,磨削深度由9 μm增大到12 μm时,变化较快,这是受到磨粒出刃高度不同的影响较大,同时较大的磨削深度,SiC颗粒脱粘、断裂形式比例增大。图13(b)显示随磨削速度的增大,垂直磨削方向的粗糙度呈下降趋势,产生这种现象的原因与图12(b)相同,主要是参与切削的磨粒数增多,同时单位时间内产生的热量增大,造成Al基体的涂覆现象平整了表面,表面粗糙度降低。图13(c)为进给速度对垂直磨削方向粗糙度的影响,增大工件进给速度,SiC颗粒受到磨粒的冲击作用加强,SiC颗粒的去除方式发生转变,同时逆磨的方式加强了这种作用,使其增大。
图14(a)~(d) SEM显示的是SiCp/Al复合材料经过磨削后的细微观表面形貌,根据图中观察,SiCp/Al复合材料加工表面质量较差,表面缺陷以SiC颗粒断裂残存在表面、SiC颗粒脱离基体造成的大空洞、SiC颗粒解离破碎以及Al基体涂敷于凹坑之上等。在磨削过程中,随着砂轮切削运动,当磨粒与塑性Al基体接触即在加工表面留下沟槽,当磨粒与脆性SiC颗粒接触时,在磨粒的冲击作用下,造成SiC破碎,部分脆性断裂的SiC颗粒被砂轮以磨屑形式带走,而留下凹坑并残留在SiC颗粒破碎形成的小凹坑上,如图14(a),图14(c),与周围Al基体表面形成鲜明对比,甚至在磨粒的冲击下,SiC颗粒会脱粘拔出使表面形成大空洞,使得加工表面质量更差,如图14(b)同时,在磨粒切削过程中,被去除的塑性Al基体在高温下部分被粘附在加工表面上或者涂敷于SiC颗粒脱粘形成的小凹坑上,这主要是由于在干式
(a)
(b)
(c)
(d)
Figure 14. SEM topography of grinding surface
图14. 磨削加工表面SEM形貌图
磨削条件下,磨削热聚集在磨削区造成温升较大,当达到Al基体熔点时,在砂轮与材料的相互挤压下,Al基体被涂覆在加工表面沟槽上或者SiC脱粘形成的凹坑之上,如图14(d)。通过具体分析SiCp/Al复合材料典型磨削表面形貌特征及其形成机制,验证了仿真结果,仿真分析对实际加工有一定的指导意义。
5. 结论
本文对SiCp/Al复合材料细微观磨削去除过程展开了材料去除仿真研究,揭示了SiCp/Al复合材料去除机理,揭示了SiCp/Al复合材料在磨削加工过程中SiC颗粒的断裂机制与被切削深度的大小有关,得出主要结论如下:
1) 通过磨粒切削模拟仿真可知,在磨粒切削过程中,磨粒切削SiC颗粒时的磨削力远大与磨削Al基体,SiC颗粒是主要的载荷承受者,当磨粒接近SiC颗粒时,会在SiC颗粒与基体界面处发生应力集中,颗粒内部应力大小与分布受到SiC颗粒尺寸、形状的影响。
2) 在磨削加工过程中SiC颗粒的断裂形式发生转变,增大被切削深度,较大尺寸颗粒易发生断裂破碎伴有裂纹的产生,小尺寸颗粒由断裂破碎转为脱粘去除,并撕裂SiC颗粒周围Al基体。表面缺陷主要为Al基体涂覆、断裂破坏破碎、解离破碎等。
3) 分析了沿磨削方向和垂直磨削方向粗糙度的变化机制,砂轮速度增大,SiC颗粒去除发生局部破碎,表面粗糙度值显著减小,表面缺陷减少,增大工件速度或者增大磨削深度,SiC颗粒脱粘形成大空洞,表面粗糙度值在一定范围内会显著增大,表面缺陷增多。