1. 引言
随着制造业转型升级的推进,对数控机床的精度要求越来越高。机床的准静态误差和动态误差共同影响了数控机床的加工精度 [1] 。数控机床准静态误差的测量和辨识方法可分为直接测量和间接测量两种。
为了减少测量时间和成本,并快速有效地获取平动轴和旋转轴的几何误差,学者们更倾向于使用间接测量法。Ibaraki [2] 系统回顾了数控机床平动轴和旋转轴误差测量的主要方法。用于平动轴误差间接测量的方法为基于激光干涉仪的多线法和体对角线法等;而用于旋转轴误差的测量与辨识主要设备有:球杆仪 [3] 、R-test [4] 和测头 [5] 等。激光追踪干涉仪和激光跟踪仪是常用于测量机床空间精度的设备。它们使用激光干涉原理进行距离测量,具有高精度。然而,用于角度测量的角度编码器由于电气误差等因素,测量不确定度较大,直接影响测量精度。因此,仅基于单一定位的“单站法”测量精度受到限制。上述误差测量方法都是在机床空载情况下完成的,未考虑机床在实际加工过程中的动态误差。
数控机床典型试件切削和检验是机床验收的重要依据之一,可真实、全面反映机床实际应用问题。现行国内外用于数控机床切削性能测试的典型试件可分为三大类:用于评价机床工作精度的试件、用于检验机床切削性能的试件和用于机床性能评价(如热态和插补性能)的试件。常见的典型测试工件,如ISO10791-7试件,四角锥台和圆锥台试件,此外还有NCG2004和NAS979标准件等经典试件。
上述典型试件用于反映机床整体加工性能,而针对机床运动轴几何误差的辨识,学者们设计了不同的特征试件。这些试件在不同加工模式下切削,特定加工模式下的几何特征对少数误差项敏感,可通过比较实际加工尺寸与理论尺寸来辨识几何误差。常见的试件特征包括一维特征(孔 [6] 、槽 [7] )、二维特征(阶梯 [8] 、平面和圆弧 [9] )和三维特征(圆锥台和球面),也有将这些特征集成于一体的特征试件 [10] ,并可分析误差的可补偿性。然而,上述方法无法辨识出机床在真实切削条件下的动态误差,虽然考虑了机床的动态误差和准静态误差。
为从根本上提高机床加工精度,本文以实际切削工件为本源,考虑机床准静态误差和实际切削过程中的动态误差,提出了基于切削特征工件辨识与分离影响机床加工精度的动态误差和准静态误差的方法,旨在精确高效测量机床误差。
2. 特征工件设计
本文在一台三轴VMC850E数控立式加工中心上开展实验,该数控机床工作台尺寸1000 × 500 mm、X/Y/Z最大行程850/500/540 mm。
特征工件的设计思路:设计的工件能尽可能多的映射出三轴机床平动轴的定位误差、直线度误差、垂直度误差的特征。特征工件要尽可能全部映射出三轴数控机床的21项几何误差,且特征工件的尺寸应足够覆盖机床实际加工过程中常用加工区间。根据三轴数控加工中心的具体结构,本文设计的阶梯槽特征工件如图1所示,工件150.000 mm,宽100.000 mm,高70.000 mm。每个阶梯槽高度为4.000 mm,X轴方向阶梯间距为10.000 mm,Y轴方向阶梯间距为6.500 mm。本文基于该特征工件可分离并辨识出7项几何误差,包括X轴定位误差、X轴定位误差、Y轴定位误差、Z轴定位误差、X轴在Y方向上的直线度误差、X轴在Z方向上的直线度误差、Y轴在X方向上的直线度误差、Y轴在Z方向上的直线度误差,如图2和表1所示,同时本文亦基于该特征工件分离出动态误差。如图3所示,在辨识准静态误差的同时,也能辨识出动态误差。
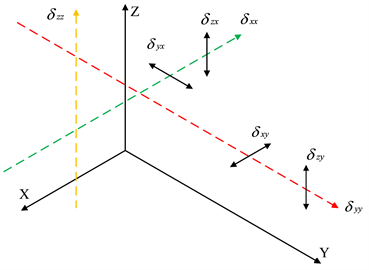
Figure 2. Schematic diagram of 7 geometrical errors based on separation and identification of feature parts
图2. 基于特征工件分离与辨识的7项几何误差示意图
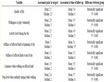
Table 1. Seven geometrical errors based on feature part separation and identification
表1. 基于特征工件分离与辨识的7项几何误差
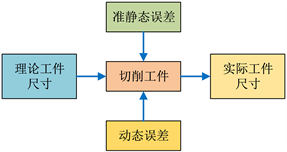
Figure 3. The dynamic and static errors that affect the machining accuracy of machine tools
图3. 影响机床加工精度的动静态误差
3. 误差辨识与分离原理
3.1. 误差辨识原理
图4为基于特征工件的准静态误差辨识原理图。首先将特征工件分解成多个子特征,不同子特征可辨识不同的误差。然后利用测头测量图4所示测点,得到对应子特征的实际坐标值。最后分析实际坐标值与理论坐标值之间的偏差,从中辨识机床平动轴的准静态误差。
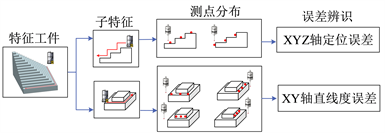
Figure 4. Principle diagram of quasi-static error identification based on feature workpiece
图4. 基于特征工件的准静态误差辨识原理图
在此对数控机床平动轴定位误差、直线度误差的辨识过程作详细说明:
① 定位误差辨识:分别选取阶梯槽在对应X、Y和Z方向分段端面上的点云数据(图5显示了X向测点),与理论尺寸值相比较,从而辨识出X、Y和Z轴的定位误差。
② 直线度误差辨识:以X轴为例,选取如图5所示点云数据,分析在Y和Z方向上的误差值,即可得到X轴在Y和Z向上的直线度误差;类似地,可以得到Y轴在X和Z方向上的直线度误差。

Figure 5. Identification principle diagram of positioning error and straightness error
图5. 定位误差、直线度误差的辨识原理图
3.2. 误差分离原理
基于特征工件的动静态误差分离流程如图6所示。首先切削特征工件,工件在机测量和三坐标测量机标定;然后处理两组数据,三坐标测量机标定值与特征工件理论尺寸值之差即为机床总误差;三坐标测量机标定值与特征工件在机测量值之差即为准静态误差。最后机床动态误差为总误差与准静态误差之差。
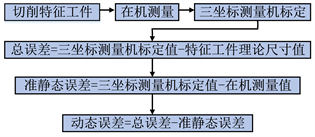
Figure 6. Dynamic and static error separation flow chart based on feature workpiece features
图6. 基于特征工件特征的动静态误差分离流程图
分离三轴机床平动轴的7项几何误差,需设置X、Y和Z轴定位误差测量起始点和X、Y轴直线度误差测量起始点、终止点、间距,如表2所示。
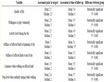
Table 2. Measure the start and end coordinate positions based on errors
表2. 基于误差测量起止坐标位置
3.2.1. 定位误差分离
如图7所示,本节以X轴定位误差为例进行阐述。工件切削完成后,在主轴上固定千分表。
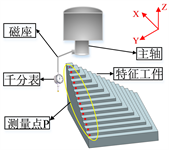
Figure 7. Positioning error is measured on the machine
图7. 定位误差在机测量

Figure 8. Positioning error CMM calibration
图8. 定位误差三坐标测量机标定
特征工件在机测量过程中,读取各测点在机床坐标系中的X轴坐标值αi。测量时,千分表依次碰触测点,且同时保证其读数为固定值,因此各阶梯槽之间的距离可表示为X轴运动量。
(1)
特征工件从机床移至三坐标测量机上,保证三坐标测量机参考系与在机测量时的参考系一致,三坐标测量机测量的测点记为H点,与P点保持一致。如图8所示,其测量的X轴方向的坐标值为
,两测点之差即为每一段阶梯槽之间的距离。
(2)
由于三坐标测量机的测试精度高于三轴数控机床加工精度一个数量级,测得的尺寸可以认为是特征工件的实际尺寸,其与阶梯槽理论相对尺寸I之差,即为工件的总误差E。
(3)
特征工件总误差E是由机床准静态误差E1与动态误差E2综合构成,如式(4)所示:
(4)
三轴数控机床平动轴的准静态误差E1可分离,即为:
(5)
由式(4) (5),切削过程中的动态误差E2可分离,即为:
(6)
3.2.2. 直线度误差分离
如图9所示,本节以Y轴在Z方向上直线度误差为例讲解直线度误差分离的方法。工件切削完成后,在主轴上固定千分表,利用千分表测量Y轴在Z方向上直线度误差测量分布点Q。
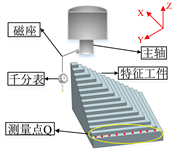
Figure 9. Straightness error is measured on machine
图9. 直线度误差在机测量
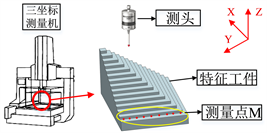
Figure 10. Straightness error calibration of CMM
图10. 直线度误差三坐标测量机标定
特征工件在机测量过程中,在Y轴方向起始测点,千分表设置一个易于观察的初始值
。通过操作机床手轮和观察机床坐标系Y轴坐标值,保证千分表等间距移动,读取千分表在每个测点上的读数
。以起始点为基准点,计算后续每个测点读数与基准点读数的差值。
(7)
三坐标测量机测量的M点,与Q点保持一致,如图10所示,读取Z轴方向的坐标值为
。类似地,以Y轴方向起始测点为基准点,计算后续每个测点坐标值与基准点坐标值之差。
(8)
理想情况下,直线度误差为0,则加工的工件表面光滑平整。但实际中,工件尺寸起伏不平,则三坐标测量机测量的偏差量为工件的总误差E。
(9)
三轴数控机床平动轴的准静态误差E1,即为:
(10)
因此,切削过程中的动态误差E2,即为:
(11)
4. 实验内容
4.1. 特征工件加工
特征工件的原材料为150 × 100 × 70 mm铝合金经去毛刺、清洗后装夹到机床工作平台夹具上。在UG中完成三维建模后,通过CAM软件生成用于加工的NC代码并完成切削加工。实际切削过程中的工艺参数如下,进给速率:120 mm/min、切深:4 mm、主轴转速:1200 rpm。
4.2. 在机测量
4.2.1. 定位误差在机测量
如图11所示,特征工件切削完成后,利用磁座将千分表固定在主轴上。通过机床手轮控制机床平动轴移动,确保在机测量特征工件X、Y和Z轴上的每个测点时,千分表读数均保持一致。记录机床坐标系中X、Y和Z轴机床坐标值。
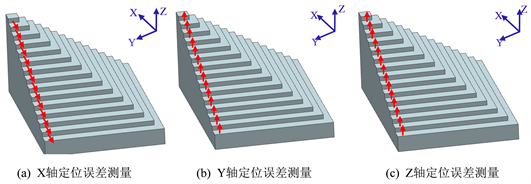
Figure 11. X, Y and Z positioning error measurement
图11. X、Y和Z定位误差测量
4.2.2. 直线度误差在机测量
如图12所示,特征工件切削完成后,利用磁座将千分表固定在主轴上。通过机床手轮控制机床平动轴移动,使千分表在X、Y轴起始测点的读数易于观察。如表2所示,测量X轴方向直线度误差时,两测点间距为20.000 mm;测量Y轴方向直线度误差时,两测点间距为13.00 mm。记录千分表的读数。
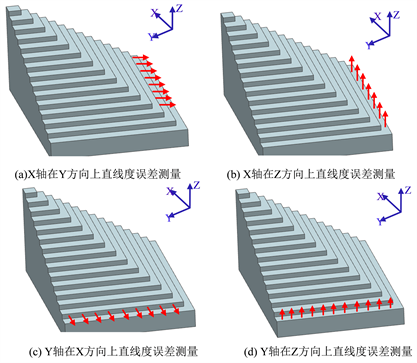
Figure 12. X, Y axis straightness error measurement
图12. X、Y轴直线度误差测量
4.3. 三坐标测量机标定
本文在ZEISS三坐标测量机上进行标定。三坐标测量机测量过程与结果如图13所示,特征工件放置三坐标测量机工作台上,保证三坐标测量机参考系、测点与在机测量一致。
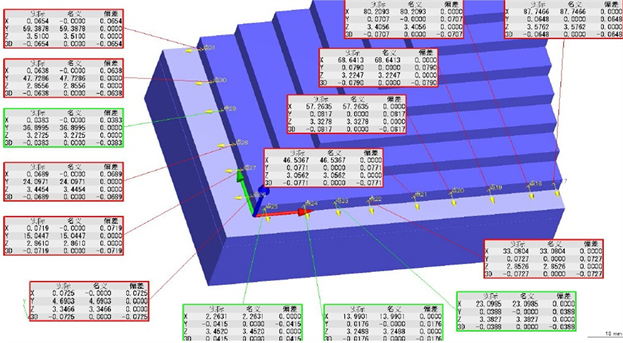
Figure 13. The workpiece is measured on a coordinate measuring machine
图13. 工件在三坐标测量机上测量
5. 实验结果与验证
5.1. 误差分离结果
如图14所示,由上述误差分离与辨识原理,将在机测量与三坐标测量机标定的两组数据代入公式(1)~(6),分离得到X、Y和Z轴定位误差方向的总误差、准静态误差、动态误差。
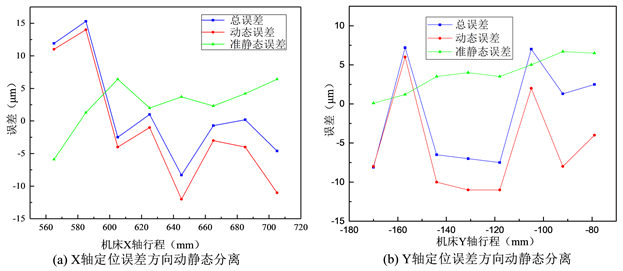
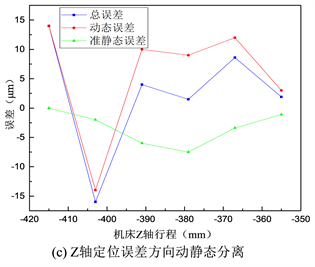
Figure 14. X, Y and Z axis positioning error direction dynamic and static separation
图14. X、Y和Z轴定位误差方向动静态分离
如图15所示,根据本文中误差辨识与分离原理,通过代入在机测量与三坐标测量机标定的两组数据到公式(7)~(11),计算出X、Y轴直线度误差方向总误差和动静态误差。
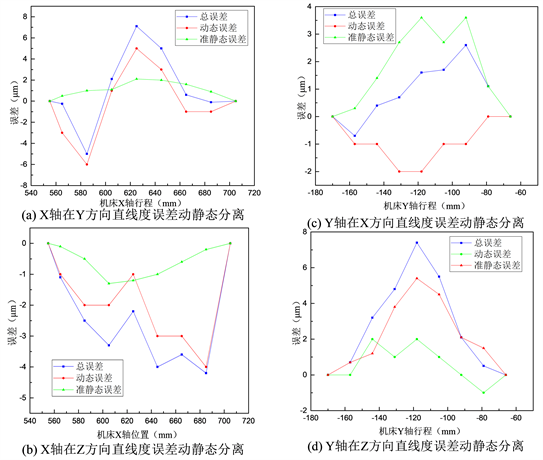
Figure 15. X, Y axis straightness error direction dynamic and static separation
图15. X、Y轴直线度误差方向动静态分离
由图14、图15可以看出:
(1) 动态误差与总误差走势基本一致,由此可见,动态误差是影响该机床加工精度的主要因素。
(2) X、Y和Z轴定位误差,随着切削行程的增加,误差逐渐增大。X、Y轴方向上直线度误差,随着行程的增加,误差先增大后减小,行程开始与结束时的误差为零。
(3) 动态误差的大小与刀具和工件相对位置变化有关,进刀和退刀过程中,刀具受到非均匀切削力,动态误差变化较大;稳定切削过程中,刀具受到均匀切削力,动态误差变化较小。
(4) 相对于X、Y轴方向,Z轴动态误差变化更大。
5.2. 结果验证
为了验证分离得到的定位误差和直线度误差的准确性,本文采用MCV-500激光多普勒干涉仪对本机床进行验证实验。
MCV-500激光多普勒干涉仪的主要技术参数:激光稳定性:0.1 ppm,定位精度:1.0 ppm (1 μm/m),分辨率:0.01 μm,测量范围:15 m。
根据特征工件实际加工区间,设置激光干涉仪测量的起始点、间距、测试次数、温度和压力补偿等参数。
如图16、图17所示,激光干涉仪在机床空载情况下测量的误差与基于特征工件分离出的准静态静态误差进行对比分析。
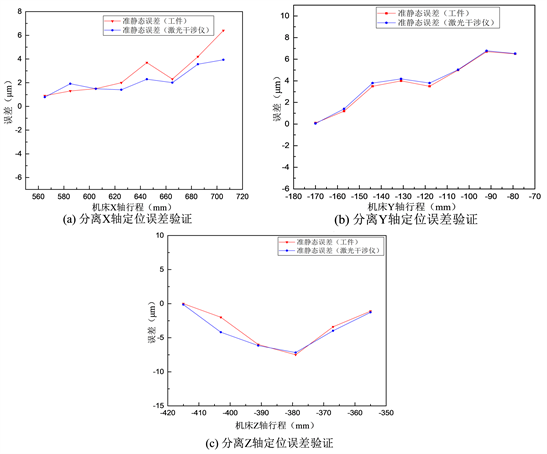
Figure 16. Separate X, Y and Z axis positioning error verification
图16. 分离X、Y和Z轴定位误差验证
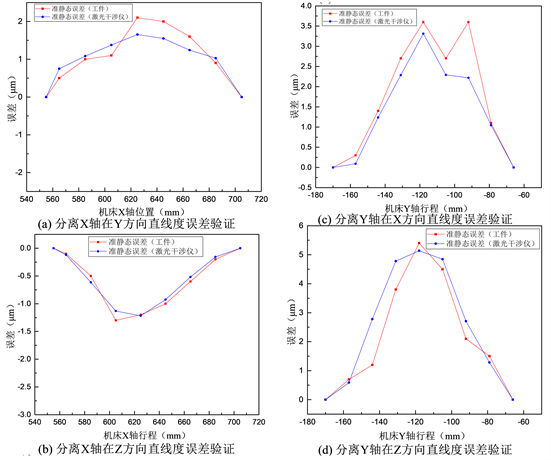
Figure 17. Separate X and Y axis straightness error verification
图17. 分离X、Y轴直线度误差验证
由于激光干涉仪进行单项直接测量获得的误差测量值准确度高,将单项测量值作为标准。由图15、图16可以看出,基于特征工件分离的准静态误差与激光干涉仪测量的误差,图形曲线走势一致。由精度公式(12):
(12)
计算出基于特征工件分离得到的X轴定位误差值精度为0.6921;Y轴定位误差值精度为0.8521;Z轴定位误差值精度为0.6866;X轴在Y方向直线度误差值精度为0.7734;X轴在Z方向直线度误差值精度为0.8532;Y轴在X方向直线度误差值精度为0.4935;Y轴在Z方向直线度误差值精度为0.7888。
通过验证实验进行的时间来看,平动轴误差单项直接测量的实验时间与基于特征工件测量的实验时间基本一致。但在辨识与分离准静态误差的同时,也得到能真实反映机床实际切削情况的动态误差,大大提高误差测量效率,保证了本方法测量的高效性。
6. 结论
本文针对现有机床误差测量方法无法准确反映加工精度的问题,提出了一种基于设计和加工特征工件的误差辨识和分离方法。该方法通过在机测量和三坐标测量机标定特征工件,实现了对机床加工精度的动静态误差的辨识和分离,并通过使用MCV-500激光多普勒干涉仪验证该方法的准确性。实验结果表明,该误差测量方法能够精确辨识平动轴的几何误差,并且相比传统方法,使误差测量效率进一步提升,为机床误差测量提供了新参考。
7. 展望
(1) 从特征工件设计的角度出发,设计的特征工件能全部反映出数控机床的21项几何误差和数控机床的加工区间,这将是本文研究方法继续拓展的重要方向。
(2) 到目前为止,关于动态误差的特征研究、动态误差产生的机理研究,还处于定性分析和描述的阶段。因此,在未来时间内,关于动态误差统一的数学化表达出典型特征,将会是该领域学者们重点突破方向。
(3) 动态误差的大小随着切削力变化而变化。造成切削力变化的因素:切削时工艺参数(切削主轴转速,切削进给速度,切削进给量等)、切削的进给方向(横向和纵向)、切削所用的材料等。研究上述因素对动态误差大小及方向的影响,是动态误差产生机理研究关键性的一步。
(4) 动态误差误差的大小与机床伺服系统的延迟有关。研究机床伺服系统是研究动态误差机理的重要方面。
(5) 验证动态误差是否存在减小总误差这一特征是研究动态误差产生机理的重要环节。
(6) 研究和分析动态误差的典型特征,是准确定义动态误差的基础,也是解释动态误差产生的机理,进一步实现数控机床系统补偿的前提。