1. 引言
喷砂是采用压缩空气为动力,以形成高速喷射束将喷料(钢砂、钢丸、玻璃砂、玻璃珠等)高速喷射到需处理的工件表面进行冲击研磨,使工件外表面的外表或形状发生变化,把表面的杂质、杂色及氧化层清除掉,同时使介质表面粗化,达到消除基材表面残余应力和提高基材表面硬度的作用 [1] [2] 。
喷砂机主要原理是在密闭的喷砂箱内,利用管道内压缩空气将粉状颗粒物料从进砂管输送到喷砂管内,砂粒在管路内被压缩空气推动向前运动,在由动能转化为势能的过程中,使高速运动的粉状颗粒物料快速流向加工件的表面,从而达到改善物体表面质量的作用 [3] [4] 。压缩空气以一定流速和压力从喷枪喷嘴射出的同时,连同研磨砂一起喷出,作用于工件表面,起到去毛刺和强化工件的作用。喷砂处理后的混合研磨砂,从喷砂箱的下部落下,通过回收管和风管吸入上方的回收箱 [5] [6] [7] 。
喷砂设备可用作对金属的锈蚀层、热处理件表面的残盐和氧化层、轧制件表面的氧化层、锻造件表面的氧化层、焊接件表面的氧化层、铸件表面的型砂及氧化层、机加件表面的残留污物和微小毛刺、旧机件表面等进行处理,以去除表面附着层,显露基体本色 [8] - [13] 。
喷砂机通过电气控制系统实现全自动喷砂,可以自动调节喷砂角度、喷砂时间、喷砂距离、喷枪的运动、工作台的转速等 [14] [15] [16] 。电气控制系统主要由横移组件、纵移组件、喷砂组件、吹净组件、除尘组件等几个部分组成,所有的组件都是由PLC事先设定的参数统一协调控制 [17] [18] [19] [20] [21] 。
国内外许多学者针对玻璃喷砂的冲蚀现象做了大量研究,Belloy等 [22] 提出了一种结合金属硬掩膜的玻璃喷砂工艺,并制备了用于微流体器件的通孔和沟槽结构,得到了良好的喷砂刻蚀效果。Wensink等 [23] 采用光刻胶掩膜电镀的铜微结构进行喷砂刻蚀,获得了高精度、易加工冲沙刻蚀效果。Ciprian Iliescu等 [24] 人应用非晶硅与碳化硅的复合结构作为掩膜结构与传统的铬金结构和非晶硅结构作对比,改善了刻蚀结构的形貌、成功刻穿了1 mm的耐热玻璃并制备了微流体器件。以上研究主要关注点在喷砂过程的材料制备和选择角度,并未针对喷射喷嘴不同的排列、形状、角度等结构参数进行分析。
本文通过构建喷砂设备模型,分析设备的内流域结构,得出设计的不合理之处,对不合理之处提出解决方案并进行分析比较,以达到最好的对玻璃冲刷的效果。本文着重于从设备的喷嘴来进行分析其对设备冲刷效果的影响。通过比较喷嘴的排列、形态和角度的不同,分析设备压力分布、流线分布以及砂粒轨迹和粒度来讨论确定哪种设备模型对玻璃冲刷的效果最好。
2. 内流域分析及模型构建
2.1. 喷砂内流域模型抽离
喷砂颗粒喷射入玻璃表面有偏离原本流动方向的趋势,具有随着水流表面流动的倾向,并具有持续研磨的能力,原模型如下图1所示。
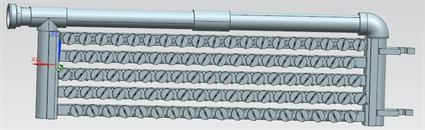
Figure 1. Original model of sandblasting equipment
图1. 喷砂设备原模型
对所给模型部分内流域进行抽取分析,去除喷嘴后如下图2所示。
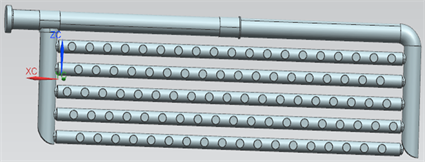
Figure 2. Watershed inside sandblasting equipment
图2. 喷砂设备内流域
2.2. 颗粒轨道力学模型的构建
为更优的实现颗粒流动轨迹的追踪,更精确的实现康达效应目标下喷嘴的工作性能优化,采用颗粒轨道力学模型作为气固两相动力学模型,用连续性介质描述气体,用离散性介质表达固体颗粒。采用Euler方法求解,气相流动的质量控制方程微分守恒形式如下式所示:
(1)
其中,
表示气相密度的变化率,简简化为非压缩性气相时,该数值为0;
表示气相质量流密
度的分散程度。
气相的动量控制方程如下式所示:
(2)
其中,
表示气相的动量源项;
表示与应力变化率相关的应力张量,如下式所示。
(3)
固相颗粒的流动求解采用Lagrange方法,在Lagrange坐标系中计算,可由牛顿第二定律得到颗粒的动量微分方程,求解该方程得到颗粒相在流场中的具体运动轨迹。如下式所示:
(4)
其中,
表示颗粒相的总受力;g表示重力加速度;其中颗粒相重力受力如下式所示:
(5)
其中,M表示颗粒质量,kg;V表示颗粒体积,m3;d表示颗粒粒径,m;其中颗粒相浮力受力如下式所示:
(6)
其中,M1表示颗粒排开体积空气质量,kg;
表示空气密度,kg/m3;其中颗粒相曳力受力如下式所示:
(7)
(8)
其中,Cd表示拖曳系数;v1表示气流速度,m/s;v表示颗相粒速度,m/s;其中颗粒相Magnus力受力如下式所示:
(9)
其中,CL表示升力系数;Ω表示颗粒相对旋转速度;其中颗粒相Basset力受力如下式所示:
(10)
其中,t0表示初始加速的时间;其中颗粒相压力梯度力受力如下式所示:
(11)
其中,
表示颗粒周边压强梯度。简化颗粒相动量方程可得:
(12)
3. 喷嘴的设计方式比较分析
喷砂设备对玻璃的冲刷效果与许多因素有关,例如砂粒的大小、流速、喷嘴的设计等。由于砂粒和流速等外部影响,我们可以通过外部调节来选择合适的喷嘴模型,所以本文不对外部因素做分析,着重于分析喷嘴的设计对玻璃冲刷效果的影响。下面我们将从喷嘴的排列方式、喷嘴的形态、喷嘴的排列、喷嘴的角度和固相颗粒的粒度尺寸五个方面来分析其对玻璃冲刷效果的影响。
3.1. 固相颗粒的粒度尺寸分析
喷嘴前端气固流体物理参数对续压和喷射阶段两相流情况影响巨大,同时砂型颗粒的粒度分布范围对射流喷砂下的玻璃表面质量产生影响。在仿真过程中,以数值模拟物性需求作为测试基准,开展砂型颗粒物性数据的分析测定。采用粉体综合性能检测仪检测颗粒的粘度和密度情况,激光粒度仪检测颗粒的粒度分布情况,如图3所示。
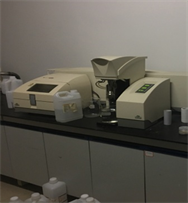
图3. 粉体综合性能检测仪(左)激光粒度分析仪(右)的物性检测
采用八组实验取平均值的形式降低测量误差,针对物性参数进行整理分析,结果如表1所示。
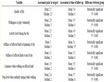
Table 1. Physical parameter test results of particles
表1. 颗粒参数检测结果
3.2. 排列方式分析
对排列方式进行分析可分为两类,一类是喷嘴交错排列,另一类是喷嘴对齐排列。图4、图5和图6为两种不同排列方式的玻璃壁面所受的压力分布,流线轨迹与砂粒轨迹图。
(a) 对齐 (align) (b) 交错 (interlace)
Figure 4. Pressure distribution in different arrangements
图4. 不同排列方式压力分布
(a) 对齐 (align)
(b) 交错 (interlace)
Figure 5. Streamlined distribution of different arrangements
图5. 不同排列方式流线分布
(a) 对齐 (align)
(b) 交错 (interlace)
Figure 6. Sand grain trajectories with different arrangements
图6. 不同排列方式砂粒轨迹
从上图可以看出不同排列方式对玻璃板压力大小与压力分布影响并不明显,对比砂粒与流线轨迹,可以看出相同状态下,交错排布流线与砂粒分布更为均匀,因此交错排列冲刷效果较好。
3.3. 喷嘴形态分析
本文共分析圆柱、圆锥、扁嘴形3种不同类型的喷嘴的压力分布情况、流线分布情形和砂粒轨迹,结果如下图7所示。
(a) 圆柱喷嘴 (Cylindrical nozzle) (b) 圆锥喷嘴 (Cone nozzle)
(c) 扁嘴型喷嘴 (Flat nozzle nozzle)
Figure 7. Pressure distribution of different nozzle shapes on the glass surface
图7. 不同喷嘴形状于玻璃面压力分布
对比三种不同类型的喷嘴,圆柱与圆锥喷嘴对玻璃面冲刷效果较差,并且流体与砂粒的分散效果较差。而扁嘴型喷嘴的喷嘴流体速度较低,这意味着扁嘴型喷口处受到的压力更小,并且扁嘴型喷嘴的分散效果更好,有着更大的冲刷压力。
3.4. 喷嘴角度分析
由研究可知,随着冲蚀角度的增加,玻璃冲蚀率逐渐增大,冲蚀损伤区域深度和宽度也逐渐增大,损伤区域形状由椭圆向圆形转变,冲蚀剖面轮廓由抛物线形向圆锥形转变。
粗糙度是指表面具有的较小间距和微小峰谷的不平度,粗糙度值越大表面越不平整。玻璃在冲蚀角度为45˚时的粗糙度均大于15˚时的粗糙度,45˚的轮廓微观不平度平均间距小于15˚时的,轮廓谷深和峰高大于后者,表面高低起伏严重。冲蚀角度为90˚时,轮廓微观不平度的平均间距较大,冲蚀表面极不规则。
将原模型喷嘴角度调整,分为三个角度,90˚、60˚和45˚,所取得的分析结果如下图8。
(a) 90˚喷嘴角度 (90˚ nozzle angle) (b) 60˚喷嘴角度 (60˚ nozzle angle)
(c) 45˚喷嘴角度 (45˚ nozzle angle)
Figure 8. Pressure distribution at different nozzle angles
图8. 不同喷嘴角度压力分布
由上图可看出在3种不同角度下,45˚压力分布较为均匀,较少出现压力分布集中的现象。但随着偏转角度的减小,射流距离会逐渐增大,并且玻璃壁面法相冲击也会减弱。
(a) 15 m/s喷射速度 (15 m/s injection speed)
(b) 20 m/s喷射速度 (20 m/s injection speed)
Figure 9. Changes of sandblasting speed at different spraying speeds and sizes
图9. 不同喷射速度各粒径喷砂速度变化
通过对比图9不同气流喷射速度下四种粒径的颗粒喷砂速度变化趋势进行对比,可以得出:海泡石大粒径颗粒的速度始终不受气流速度的影响,且一直维持自己的速度水平,而小粒径的喷砂颗粒随入射气流的不断增大,速度的最大值也不断提升,且速度值更容易出现波动,而出现速度波动的原因是小粒径颗粒更容易受到气流旋涡的影响而出现能量损失,因此为保证玻璃喷砂的质量,应当保证适当提升砂型颗粒的尺寸精度,也可提升喷砂作业的效果。
4. 总结与分析
在本文中,通过对玻璃喷砂设备的技术改造,优化了一套半自动玻璃喷砂管道系统;并对比分析了喷嘴的不同排列方式,喷嘴外形与喷嘴角度对玻璃板冲刷效果的影响,发现:喷嘴数量为18时,发现交错排布效果较好;冲刷均匀性和冲刷颗粒散度较好;扁嘴型喷嘴的冲刷压力达到冲蚀力要求并且喷口处更不容易磨损,具备更高的经济性和工作稳定性;随着喷嘴偏转角的不断减小,玻璃面的压力分布也变化更加均匀,但随之射流距离也会持续增大,使得玻璃表面冲击压力不断降低,在实际喷沙工况下,应当根据玻璃类型和冲蚀颗粒类型进行综合考虑,另发现更小的颗粒具有更强的喷砂冲击能力,应当不断细化冲蚀颗粒粒度来增强玻璃喷砂的工作效果。
基金项目
湘潭大学教学科研仪器设备改造研制项目:三坐标点阵式快速柔性夹具研制(6801006)。
NOTES
*通讯作者。