摘要: 现代工业生产对危化液体的混合搅拌有着越来越高的需求,但危化液体搅拌安全性与准确性的质量取决于设计、制造和检测各个环节,其中液位的高低是影响液体质量的关键因素。基于此,设计一个基于S7-1200PLC控制的液体混合搅拌系统,该系统能检测液位的高低,并控制液体的排放。该系统用SIMATIC HMI精简系列面板控制液体混合装置,该触摸屏上可实现对PLC的启动,进料阀、出料阀和搅拌机的动作示意控制,并显示当前液位及高、中、低3个液位。
Abstract:
Modern industrial production has an increasing demand for the mixing of hazardous liquids. How-ever, the safety and accuracy of hazardous liquid mixing depend on all aspects of design, manu-facturing and testing. The level of the liquid level is the most important factor affecting the mixing of hazardous liquids. Based on this, a liquid mixing and stirring system based on S7-1200PLC con-trol is designed. This system can detect the level of the liquid and control the discharge of the liquid. The system uses a SIMATIC HMI streamlined series panel to control the liquid mixing device. The touch screen can realize the start of the PLC, the action control of the feed valve, the discharge valve and the mixer, and display the current liquid level and high, medium and low liquid level.
1. 引言
随着现代工业的发展,液体混合自动控制系统在许多方面都是不可缺少的,常用在化工、制药、石油等领域,并且他们在生产过程中至关重要有越来越多的实体企业在制造产品中需要用到高危型腐蚀性液体作为原材料。在工艺加工的初期,这些原材料多是在人为的操作下把原料按住工程师的要求在一定的条件下按顺序进行加工,但这些行业中的液体混合的大多为易燃易爆品,甚至是有毒有腐蚀性的液体,工业上常用方式往往为用钢瓶包装原材料后再运往车间现场,但随着需求量的扩大,用这种方式会导致企业生产效率低,大大限制企业的发展。此外,由于罐装区域离车间往往还有一段距离,并且管道阀门多,需要多名员工同时远程操作,若出现操作失误的情况,后果十分危险。随着继电器的发展与广泛应用,很多企业实现了半自动化的控制流程,但是也难以保证实现生产过程中的混合精确、可靠等要求。因此,本论文引用现代新技术与设备西门子PLC,实现了更高自动化程度危化液体的混合搅拌自动化控制,提高了生产效率的同时,降低了人工成本以及意外风险。
2. 控制系统运行要求
设计的物料混合系统主要是针对传统人力物料混合精度低、生产效率低的问题而采用现代流行的PLC和HMI触摸屏实现高效率、高保证的物料混合系统设计方案 [1] 。本次设计的工作流程大概分为以下几个阶段:
第一阶段:启动阶段,按下启动按钮,PLC与HMI面板启动,控制系统预备运行阶段。
第二阶段:液体A进料阶段:通过低液位传感器检测当前液位,当前液位处于低液位状态,传感器S1接收到信号,控制阀X1打开,加注液体A至物料罐中。
第三阶段:液体B进料阶段:通过中液位传感器检测当前液位,当前液位处于中液位状态,传感器S2接收到信号,控制阀X1闭合,同时控制阀X2打开,加注液体B至物料罐中。
第四阶段:混合液体搅拌出料阶段:通过高液位传感器检测当前液位,当前液位处于高液位状态,传感器S3接收到信号,控制阀2闭合,同时电机M开始搅拌30 s后控制阀X3打开,混合液体C全部放出,当物料罐内液面降至S1时,关闭控制阀X3停止放出。
该项目在调试期间使用软件编程的方式,采用梯形图中的模拟数据代替传感器输入信息,通过比较指令,将低、中、高3个传感器的信息用数据块中的变量替代 [2] ,系统调试过程中,用程序模拟实现液位增长和下降的过程,用输出线圈的触点状态模拟传感器信号。
液体混合搅拌系统的生产过程模拟如图1所示:
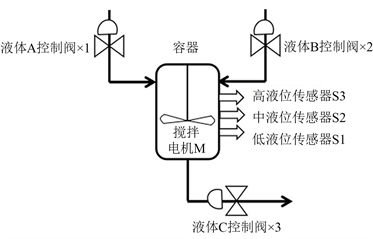
Figure 1. Production process simulation diagram of liquid mixing and stirring system
图1. 液体混合搅拌系统的生产过程模拟图
3. 控制系统硬件设计
3.1. PLC选型
在此自动控制系统中,充分考虑系统的可扩展性和维护的便利性,然后选择控制模块化PLC。因为此系统软件的运行是顺序控制,所以将西门子S7-1200 PLC作为控制模块来控制系统。因为它能够满足我们在液体混合控制要求中模块结构要求,且功能更加便于扩展,兼容性强等特点 [3] 。
3.2. HMI选型
可视化已经成为自动化系统的标准配置,为了实现这个配置,西门子出品了由各种面板和WinCC软件两大部分组成的人机界面(HMI)产品。国内的项目一般使用的是面板产品,其中微型面板、触摸面板、操作员面板、移动面板和多功能面板是主要的面板产品类型。最终我们选择了MCGS TPC7062TI幸好的HMI面板来实现人机交互界面 [4] 。包括实现系统的启停功能,采集物料罐中液位的实时数据等。该人机交互面板成本低,速度快,精准度高,兼容性强以及稳定性高等多方面特点,能够满足实时控制的要求,并且能够提供报警等功能。
3.3. PLC I/O点分配
对该物料混合系统工艺过程进行需求分析,确定该系统的I/O及其他元件地址分配如表1所示。
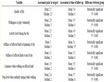
Table 1. System I/O and other internal components allocation table
表1. 系统I/O及其他内部原件分配表
4. PLC程序设计
整个控制系统的设计是采用PLCSIM进行仿真,采用LAD进行编写 [5] ,主要包括主程序[OB1]与函数功能块[FC1]以及数据块[DB1]构成。主要由三个控制阀,三个液位传感器,以及混合搅拌电机M等组成。以及数十个PLC变量组成全部的控制系统,如图2所示。
在功能块F1中,利用数据块中的变量来控制液体A与液体B的加液、搅拌以及搅拌后的混合液体C的出料功能的实现。由于条件限制,拟采用加减计数器来模拟液位的升降 [6] ,利用时钟存贮器提供的脉冲信号进行实现 [7] 。具体过程如下:
若当前液位值 ≤ 1,则表示低液位传感器S1产生电信号,此时低液位传感器S1有信号。
若当前液位值 = 20,则表示中液位传感器S2产生电信号,此时中液位传感器S2有信号。
若当前液位值 ≥ 40,则表示高液位传感器S3产生电信号,此时高液位传感器S3有信号。
部分梯形图如图3所示:
5. 系统调试
在S7-PLCSIM V18组态软件开发平台上,创建工作区后添加S7-1200仿真,再通过西门子TIA Portal V18项目进行编译后,下载到PLC中,通过以太网将PLC与触摸屏连接起来,下载到设备,下载成功后,在PLCSIM仿真软件中的库选项添加SIM表格 [8] ,并在属性栏勾选输入、输出、存储器后加载所选变量。如图4所示,打开监控画面,即可对触摸屏进行操作并分析输出状态。
6. 结论
按下启动按钮后,系统可按照相应控制要求完成各个阀门的自动开启与关闭的功能,并且因为S7-1200PLC具有较高的可靠性以及拥有较高的准确性的优势,可以实现对控制系统中各个变量以及各个设备输出的状态进行及时且精准的更改 [9] ,降低了由人工操作不准确性的风险。在另一方面也可以进行更加全面的对整个生产工艺进行全面的监控。
本文通过对液体搅拌机控制要求的分析,借助于西门子PLC配套的TIA Portal V18编程软件,实现了对液体搅拌机的自动控制,并解决了在控制过程中遇到的液位波动问题。利用西门子PLC设计出的控制系统具有可靠性高、抗干扰能力强,设备占用空间小、使用和维护简便等特点,解决了人工控制过程中存在的问题 [10] 。在实际应用过程中,可以通过配套软件很方便地随时修改系统的控制程序,以改变液体混合装置的工作时间和工作状况,满足不同液体混合的需要。此系统可对多种危化液体自动混合系统实现高精度的控制,能够有效降低事故率,且对工人的人身安全有了更加强劲的保障,具有较大的实际工程使用价值。
NOTES
*通讯作者。